That old adage of 90% done with 90% to go is now the state of affairs. As I write this, I have a flyable airplane. But with the need for a lot of little improvements, adjustments and corrections, Im firmly in the hangar.
So, in no particular order lets take a look at some of the modifications and the Boy, that was dumb corrections as I get near TBD. TBD? We have TBO, so why not The Big Day? It comes more trippingly off the tongue than FF for First Flight.
Forsaking Floppy Flaps
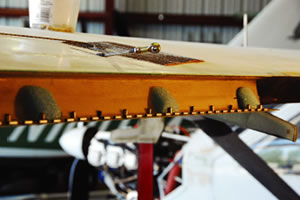
The trailing edge of the wing needed reinforcement. Those little green mounds are glass-covered foam and worked nicely to really stiffen the hinges.
First on the list, for no particular reason, is a reinforcement of the lower trailing edge of the wings. Early Jabiru models had this area reinforced with intermittent triangulation; mine, a later example, used a full-width component. While a good idea, the execution leaves a bit to be desired in that where the trailing edge was 2 inches of unsupported material, it is now inch. Even after adding a full-span hinge, a 5-pound vertical push with a thumb would deflect the material about a quarter inch.
Keeping in contact with other Jabiru builders is an essential part of building, and someone suggested that I add extra bracing and even described how to do it. By the way, this need not be done prior to the hinge installation. In fact, its easier to wait. Carve a piece of foam to make an arch about 3 inches wide and as high as will fit. Glue it into place and cover it with a couple of layers of glass. Repeat so as to create four or five trusses. Let the epoxy set, and you’ll be amazed at how much more stable that entire trailing edge has become. Wow, but how I love it when little changes create big improvements.
Truing Too Much Toe-In
This one is my fault. Youll remember that the gear legs were too bowed, leaving the axles pointing down at a 15 angle. I pulled the legs off, rigged up a heating box and, with the aid of 50 pounds hanging on a 5-foot extension, bent each leg to a less severe curve. Once they were installed, I had the axles pointing down at only 5 with no fuel, baggage or people. I picked that number by measuring a friends Jabiru in a similar condition; when it was loaded the axles were not quite level.
Success! As they used to say in the old westerns, Not so fast there, pardner. Id traded it being bow-legged for being pigeon-toed. It had been sufficiently bow-legged that fixing it increased the track width about 5 inches. But now the toe-in was such that track width would widen if I pulled the plane forward and narrow when going backward. Total variation? About 5 inches.
After much consideration I rejected the idea of rebuilding the heat box, not because it wouldn’t work, but because it would be hard to get the alignment I wanted. That left me to consider an in-place adjustment.
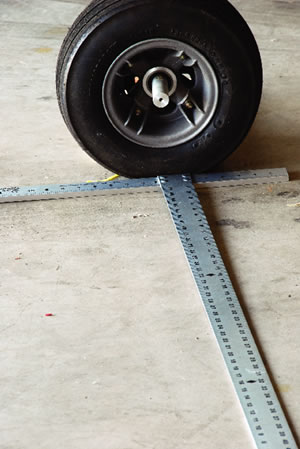
The T square is perpendicular to the length of the fuselage. Look closely at the axle extension pointing straight out, and you’ll see just how much toe-in needed fixing. This axle needed to be swung to the right to match the T square.
Option two was to pull the axles off, build up the inboard and outboard surfaces, and then sand it all flat and re-drill the four mounting bolt holes. Again, I didn’t like that option, as the small surface area would make it difficult to get the angle I needed.
Option three was to build tapered shims to slip between the axle plate and the gear leg. This was better, but still, how much taper would be needed?
Option four grew out of option three, that is, how about different heights of washers under the four axle bolts? That would, at the minimum, define the geometry of the shims considered in option three. Not only that, I wouldn’t have to consider the flatness of the surface; the stacked washers would ignore it. Better and better!
Heres a thought: What goes on in the space between the bolts, and what is the nature of a bolted joint? Lets consider the second half first: How does a bolt work? First, those bolts you’ve been using do not inhibit lateral relative motion of the bolted surfaces simply by filling the hole; the bolt-nut assembly is a clamp in exactly the same way as if wed put a C-clamp on the assembly.
I frequently get resistance to this idea, but the bottom line is this: A bolt or clamp is simply increasing the frictional load to the point that nothing moves. Don’t believe it? Try dragging carpeting around with the furniture still in place.
There are special bolts that actually will act as locating pins, but the run-of-the-mill bolt in use goes through a hole thats somewhat larger than the bolt. Clearance is clearance. If one plate/case must be accurately positioned, you’ll find dowel pins pressed into one of the two plates.
The other job of a bolt is to resist separation of the surfaces in the axial direction of the bolt. Think of cylinder heads being clamped down to keep the pressure of combustion in the cylinder.
Thats two functions, but this axle needs to resist lateral motion more than bolt-axial lifting. With that thought in mind, lets look at what happens in that unclamped area between the bolts. Start by going back to the carpet with furniture. More furniture equals more resistance to motion. But the areas between the furniture just don’t contribute much to the clamping action do they?
You probably feel this is right, but it still bothers you. OK, here comes some engineering. Assume we have a pair of perfectly rigid plates-neither will bend under load-and they have a total surface area of 25 square inches. Now clamp them together using a nut/bolt/washer system where the washers are only 1 square inch. Clamp down with 100 pounds of force, and you’ll get 100/25 = 4 pounds per square inch. Remember that the load on the washer is spread over the entire plate.
But now lets make those surfaces flexible like a carpet. Were not distributing the load over the entire 100 inches; its loaded only where the washers are, so now in that 1 square inch, we have a load of 100 psi, while the rest of the carpet is at zero.
The flexibility of the fiberglass is obviously somewhere between our perfectly rigid material and a carpet, but the point is this: Spread the load, and you’ll have to increase the clamping pressure to resist sliding. So it would seem reasonable that the size of the largest washer pretty well defines the area under most of the clamping load, right? There are other considerations, but Im willing to give this a try.
With that as my reasoning, I simply enlarged the holes just enough to clear the angular adjustment of the bolts, sanded the mating surfaces as flat as I could, added washers as needed and got the axles in the perfect alignment.
Doors Dangling Over the Daisies
This is not my goof. Jabiru wanted to avoid external hinges on the doors, as they apparently felt them unsightly, so the designers fabricated what seemed like a nice enough system. Two hinges and a door latch should make a three-point system for locating a door within the fuselage, right? Heres where, in the old Aussie movies someone says, Crikey, Mite. Because the hinges are so close together, and the bolt clearances are as they should be, the doors wobble around the longitudinal axis about an inch. With the wind over the fuselage, as in flying, the top of the door leans out into the airflow.
Again, get into the local community of Jabiru builders and you’ll see a panoply of solutions. A good one was to place a spring-loaded ball in the upper edge of the door; closing the door caused the ball to depress into its recess, and with the door fully closed, it snaps up into a small indentation in the doorframe.
My favorite, though, is to simply fab a little lever and mount it on the upper edge of the door. There’s no resistance when closing the door and, when engaged, the door itself is flexible enough that it can be opened from the outside.
Lighting the LED
Here is my favorite little tweak. You may remember that I had the panel laser-cut by Pega Precision of Santa Clara, California. I was able to have them cut the N number through the aluminum as well, so I thought it would be a nice touch to light it from the rear. I looked into various schemes including translucent strips, incandescent bulbs, fireflies in a jar and…nope, strike that last one. We don’t have fireflies in my neighborhood.
What I settled on was based on something I noticed in high school physics; light entering a sheet of translucent plastic is internally reflected, concentrating it to exit at the edges. Come forward a few years and use an LED for the light source. Now drill a hole in the plastic just large enough to press-fit a couple of LEDs and add a 1k-ohm resistor to keep the power under control. Presto, you have a tiny edge-lit pit of plastic. The next step was to wrap some packing tape around the whole thing to create a wall, and then bury the LEDs, resistor and wire in RTV. An aside: RTV, aka silicon seal, stands for room temperature vulcanizing, meaning it turns into a rubber-like compound at room temperature.
Now test it with a 9-volt battery to be sure you have the polarity right, and add a couple of spade terminals. Pull off the packing tape and glue it with contact cement to the back of the panel. I hooked this one up through the master switch so it would be a reminder that Id left it on, and then turned it on to the envious looks from other builders.
The nice thing about LEDs is that they have an MTBF of 10,000 hours. Thats mean time between failures, which means you can pretty much forget having to ever fix this little cutie.
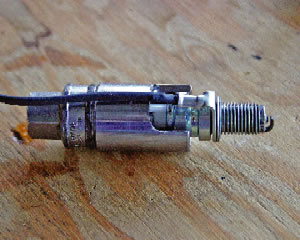
With little clearance between the spark plugs and the cylinder head fins, the ring lug for the CHT sensors required a modified spark plug wrench.
Socket Too, Me
The last item regarding the Jabiru 3300 powerplant. All that beautiful machine shop work means that the clearance between spark plug and cylinder head fin is nil. That, in turn, means that fitting the CHT rings under the plugs is nigh-on impossible.
First, and carefully, bend the lead for the CHT ring 90 so itll fit over the plug threads but clear the fins. Heres another Crikey! because the spark plug socket wont fit over the plug; the ring lead is in the way.
Solution? Use an abrasive wheel on a die grinder to create a large notch in the socket. Yes, it will still turn the spark plug. I have a specialized socket in the box for removing an oxygen sensor in the exhaust of my car, and in a couple of dozen cycles its never slipped or failed. It worked here.
Whats Next
Jim McCormick of Jabiru Pacific has offered to do the test flight, but Ill have to transport everything to a more suitable runway. My place has mountains on two sides, trees all around, and an 800-foot canyon to the south. Ill report how transport, reassembly and the flight go, but I suspect well be missing an episode next month.
Would I build another one? Ive groused and griped, complained and carped, so the obvious answer is…you betcha! Hey, if it was Lego snap-together easy thered be no Experi in the Experimental. I love the little challenges that make this my airplane, not just a newer Cessna 152. My wife says shes really looking forward to flying a client on a short trip in the plane and announcing that her hubby built it. I cautioned her to announce that after takeoff.
For more information on the Jabiru J250, call 559/431-1701 or visit www.jabirupacific.com.