
It might surprise you to find out that there is a 20% more fuel efficient aircraft piston engine sitting on the shelf that nobody is building. Its called a turbo-compound engine. Some 9000 were built in the late 1940s and early 1950s, and they have experienced more than 7.5 million flight hours. When jets came along, development on this engine stopped dead. Jets were simpler and expedient at the high power (thrust) levels required, so this made up for the fact that their brake specific fuel consumption (BSFC) was atrocious. People wanted to fly faster and higher, and fuel was cheap.
Back to the early days of WW-II. Allison aircraft engine designers were figuring out a way of cutting the fuel consumption so they could get more power out of a gallon of fuel. This is a difficult task at the best of times, but became a dire necessity during the war. Our B-17 bombers were being shot down in large numbers over Europe, and we needed a long-range fighter escort to protect them.
The engineers were aware that more than 50% of the energy in a gallon of fuel was going out the exhaust pipe in a hot blast of air. Some bright engineer thought up the idea of using a turbine fed from the high-energy exhaust gas to feed power back into the crankshaft. What wartime experience proved about this discovery is that recovering some of the wasted energy in the exhaust is the only practical way of reducing fuel consumption in double-digit percentages.

Theory, Practice, History
As far as I can tell, Allison was the builder of the first turbo-compound piston engine, though steam engines had been using the principle for years. The first non-turbo-compound Allison V-12 V 1710 produced 750 hp. By the beginning of WW-II it was producing 1050 hp, then 1125, then 1325, and late model P-38s used 1475-hp engines. The turbo-compound version was identified as the V1710-E22 by Allison, and as the V1710-127 by the government. It differs from a turbocharged engine, which uses exhaust gas energy only to drive a compressor and increase the pressure of incoming combustion air. Work on this turbo-compound engine began in 1944, funded by the government and continuing until 1946, when Allison asked that it be canceled because pure turbine engines had greater promise.
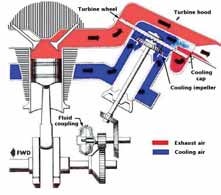
The V1710-E22 was the first successful turbo-compound engine, and probably one of only three types ever built. It was designed to power the Bell XP63H, which, as it turned out, never flew. The V1710-E22 had a military rating of 2320 hp, and a war emergency rating with water/alcohol injection of 3090 hp. The XP63H, had it gone into production, would have been one of the most powerful fighter planes of WW-II and probably with more range than the P-51 Mustang.
The Allison V-12 TC engine collected the exhaust gas from all 12 cylinders and routed it to the turbine at the rear of the engine through two exhaust tubes. The shaft from the turbine ran through the center of the first stage supercharger impeller, back to the engine and put its power directly into the crankshaft. The turbine could not be connected to the supercharger impeller directly because the supercharger was driven by a variable-speed transmission that did not run at a fixed speed ratio with respect to either the crankshaft or the turbine (See Figure 1). This engine represented quite an advancement over the original 750-hp Allison V-12 engine.
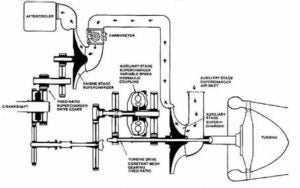
Curtiss-Wright R3350
While the Allison was the first of its type, the most successful turbo-compound engine was a version of the air-cooled, 18-cylinder, two-row radial Curtiss-Wright R3350 as used in the B-29 bomber and the Bearcat. The turbo-compound version had three turbines, each fed by six cylinders, geared to the crankshaft. The normal version produced 2700 hp and weighed 2850 pounds. The turbo-compounded version produced 3500 hp and weighed 3440 pounds. Think about that. Using 1940s technology and metallurgy-admittedly, disciplines that were progressing rapidly during the war-Curtiss engineers were able to break the mystical 1 pound per horsepower barrier. This engine was used on the Douglas DC-7C, some versions of the Lockheed Constellation and several other military airplanes.
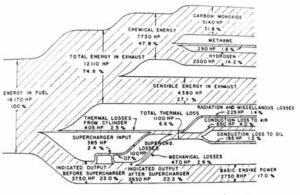
Powerful though it was, what makes the R3350 remarkable is its efficiency. Figure 2 shows the overall heat balance of the non-turbo-compound R3350 under takeoff conditions. A heat balance chart illustrates how individual percentages of fuel energy are allocated to different uses or non-uses in an engine. All of the various types of energy are converted to their heat equivalent in this chart. For example, horsepower can also be expressed as watts of heat. One horsepower is 746 watts. We will refer to it as horsepower rather than energy to keep it simple.
More than 74.9% of the horsepower implied in the fuel is exiting the exhaust without doing useful work during takeoff. It is common for all internal-combustion engines to waste over half the potential power in the fuel. In this case, the waste is much higher because the mixture is set very rich to cool the engine during takeoff-a common practice to this day on turbocharged aircraft engines. Subtracting all losses from the gross total horsepower in the fuel gives us 2750 net to the prop. This non-turbo-compound engine extracted only 2750 hp. Overall efficiency with a 10:1 air-fuel ratio for takeoff was a poor 16%. Not a good result.
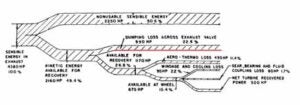
Power. More Power!
In the turbo-compound version of this engine, horsepower improvement is dramatic. Figure 3 shows only the R3350 turbo-compound engines exhaust part of the heat balance chart during takeoff. Total takeoff power is up to 3250 hp from 2750, an 18% improvement. Total recovered power from all three turbines is no less than 500 hp at sea level. (By the way, the label kinetic energy in this chart is merely the volume or weight of exhaust gas times its velocity squared. This is what is used for driving a turbine. It, too, is labeled in its horsepower equivalent.)
This takeoff power recovery heat balance chart was surprising. I had no idea that so much horsepower was wasted by the exhaust valves in a piston engine. The horsepower going to the turbines is minus the huge losses to the exhaust valves.
The remaining waste exhaust horsepower is not directly usable by simple means; however, if you allow the exhaust heat to dissipate to the air surrounding the engine before reaching the turbine, the recovered horsepower will be reduced. Looking at Figure 2 again, we see the potential horsepower in the fuel was 16,750 during takeoff. This is another way of stating fuel burn. Net power out at the prop is 3250 hp. Overall efficiency with a 10:1 air-fuel ratio for takeoff is improved to 20% with turbo-compound. This is still not good, but necessary to protect an air-cooled engine.
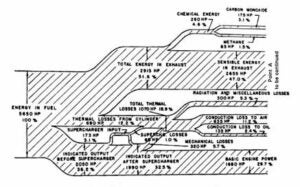
Figure 4 charts the heat balance for the non-turbo-compound engine during cruise, which is the most important part of the flight because its where the engine spends the most time operating. Due to a change in mixture ratio, the waste horsepower in the exhaust is down to 51.6% of the total fuel horsepower. This is typical of all internal-combustion engines. Figure 5 shows only the R3350 turbo-compound engines exhaust part of the heat balance chart during cruise. All three turbines generate a cruise horsepower increase of 160 hp. Total cruise power is up to 1840 hp from 1680, which is a 10% increase in power with no increase in fuel burn at sea level.
At altitude the gains are much higher. Looking at Figure 4, we see the potential horsepower in the fuel burned is 5650 during cruise. Net horsepower recovered at the prop is 1840. Therefore, overall turbo-compound engine efficiency during cruise is increased to a remarkable 32.3% at sea level. Turbo-compound engines work well at high altitude, because the back pressure on the power recovery turbines is reduced.
All of this was not easy to develop. Curtiss-Wright had a lot of problems with the exhaust valves, and most of the development money was spent on improving their lifespan. Radial engines in those days had a method of measuring the torque, or brake mean effective pressure, as it was called. The fuel-air mixture had to be set 10% below peak BMEP at a given rpm to lower the exhaust gas temperature by about 200 F. This temperature drop in EGT was critical to the life of the exhaust valves and the turbine.
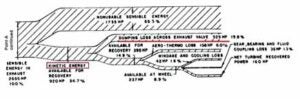
The same thing is true today in air-cooled aircraft engines. If you run the engine at peak EGT, the exhaust valves will be damaged. Most pilots run the engine at 50 F rich of peak EGT to prevent damage to the exhaust valves. The engine could also be run lean of peak with the same effect. That is what Curtiss-Wright recommended for the R3350 TC, which resulted in a better BSFC, meaning a lower fuel burn. The BSFC dropped from 0.45 pounds of fuel per horsepower per hour at peak EGT of 1650 F to 0.375 at 1450 F lean of peak. The R3350 TC commercial version had mechanical fuel injection that kept the mixture the same in all 18 cylinders-not an easy thing to do with a carburetor.
The fuel-injection system also has an auto-lean feature, a great labor-saving device for the flight engineers, and very advanced for its time. Occasionally the auto-lean feature would not work, and it was up to the flight engineer to manually set the mixture properly. All too often this was not done, and an exhaust valve would fail, taking out a turbine blade or two. At that point the engine had to be shut down to prevent further damage. It is easy to forget that this technology is almost 60 years old. With modern (higher temperature) materials, engine-control computers and aerodynamic improvements in turbines, the potential for increased fuel efficiency is mind boggling.
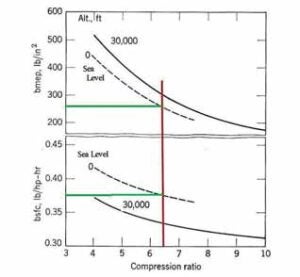
Figure 6 is a chart published by Curtiss-Wright, showing the BMEP and BSFC as a function of compression ratio and altitude. Brake mean effective pressure, or the mean pressure in the cylinders, is what creates torque. Curtiss-Wright chose a low 6.5:1 compression ratio for durability reasons. Note that the BSFC or fuel burn at sea level is in the 0.375 range. At 30,000 feet it is much better at about 0.325. These engines provided better aircraft performance with half the fuel burn in the 20,000 to 30,000 feet altitude region than turboprop engines do today.
The R3350 was used on the Lockheed Super Constellation, the Douglas DC-7C, the Lockheed P2V, the Fairchild C119 and the Martin P5M. Super G Connies with this engine were able to fly nonstop from San Francisco to London over the Arctic in the 1950s. That was not possible using jet engines until years later. (I highly recommend the book Lockheed Constellation, by Stringfellow and Bowers, Motorbooks. It describes the TWA 19-hour nonstop flights from San Francisco to London and 23-hour-plus flights London to San Francisco.) Some 9000 R3350 turbo-compound engines were built in the late 1940s and early 1950s, and TBO rose to 3000 hours.
There is no reason that the turbo-compound principle cannot be applied to our current turbocharged light-aircraft engines. In its simplest form, it would only be necessary to enlarge the turbocharger turbine and tap power out of the compressor end of the turbocharger to feed it back into the crankshaft.
The Wankel Rotary
Let’s take another look at the exhaust heat balance chart in Figure 5 without the offending exhaust valves. Total kinetic horsepower available from the fuel to the turbine now more than doubles from 14.9% to 34.7%. The losses to gears and bearings also fall to, say, 3%. Windage and cooling loss goes to 2.6% from 1.3%, and aero and thermal losses drop from 12% to 6%. Total loss for these factors alone is then 17.6%. Total kinetic horsepower available without exhaust valves is now 34.7% minus 17.6% or 17.1% of the total horsepower in the fuel!
Mazda Wankel engines do not have exhaust valves. In effect the engine is piston ported similarly to a two-stroke engine. In this case the rotor acts like a piston and opens and closes both the intake port and the exhaust port, doing away with troublesome exhaust valves. Most internal-combustion engines are lucky to retrieve 30% of the energy in the fuel. In theory what this means is that a Wankel rotary aircraft engine could be as much as 44% efficient, up from about 27% efficient. That is a huge improvement.
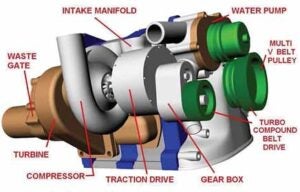
The power in the Mazda Wankel rotary engine exhaust has been talking to us for 40 years, saying, Hook me to a turbine, hook me to a turbine, hook me to a turbine! Anybody who has been around a Mazda rotary-powered race car without a muffler can understand the tremendous kinetic energy in the exhaust. There are no exhaust valves to slow down the speed of the exiting exhaust gases, which leave the wide open exhaust port at supersonic velocities. A race car driver friend, John Morton, claims he has permanent hearing damage from driving rotary race cars without mufflers. Current race rules demand mufflers, and turbochargers make great ones for the Wankel rotary engine.
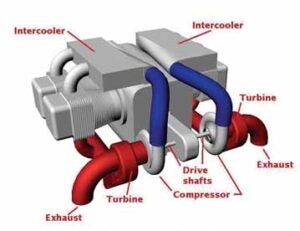
It was not until I read that SAE paper on the R3350 TC that I could put a number on the waste power in the rotary exhaust. Then it hit me. Yes, of course it has plenty of power in the exhaust. A normally aspirated 250-hp, 250-pound, mostly cast iron Mazda rotary engine with 27% overall efficiency has about 920 potential horsepower in the fuel. The turbo-compound R3350 achieved an 18% improvement in takeoff power. Because the fuel burn horsepower of the rotary is 920 hp, 18% of that is 160 hp. In theory, the turbo-compound rotary engine could increase the net horsepower out by more than 50%, to more than 410 hp, with no increase in fuel burn and little increase in weight or cost. This excellent power-to-weight ratio is almost in the realm of small turboprop engines with half the fuel burn. Amazing!
Now comes the time to harness all of those supersonic horses. Think of the Mazda Wankel rotary as an ideal gas generator for a turbine engine, a marriage made in heaven (See Figure 7). Maybe this will inspire the aircraft-engine industry to take another look at turbo-compound engines of all types, not just the rotary. I hope so.
The rotary loves high rpm and the turbos even more so . Gearboxes are heavy and hard to get right. A hybrid electric arrangement might not save weight and/or efficency but would allow the motor (or motors) to be placed in unusual configurations (think BD-5 and multi rotor). It is easier to run wires around corners than drive shafts. Maybe put a battery or capacitor in the mix for a takeoff boost.
Have you seen the inside out rotary? still early development.
How soon could the P-63H potentially have seen combat in WW2 with proper accelerated top priority by cancelling the P-39Q which was the most produced Cobra model although obsolete? A fast track equal to the P-51 program for this Kingcobra could compete for escort missions unlike any other P-63! That V-1710-127 engine was special!