Many of you have seen the work that professional avionics shops do when handling and bundling wires and harnesses. Some of you may also have thought, Wow, I wish my wiring looked like that! and then just figured there must be some secret that the professionals have to make it look that good, or it takes decades of experience to learn how to do it. The truth is that anyone can make wiring look good. However, it’s not something you should do just for looks, but also so that installation, maintenance and future upgrades will be easier. Later on, when you’re working under or behind the panel, you’ll be glad you took the time up front to make the installation clean and well organized.
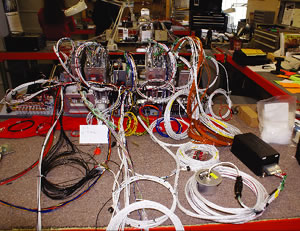
Planning
First, it’s important to have a plan. It doesn’t have to be fancy or complex, just some idea of what you’re going to do. Before you run a single wire in the airplane, sit back and think about it for awhile. Imagine where and how you’ll install certain items. Think about where you’ll put your antennas, where the strobe power packs will go, where the ELT will be, where and how the autopilot servos might be installed, along with flap motors and many other electrical items in the plane. Make a simple list of anything that will need wires run to it. Once you have the list of items, try to figure out how long the needed wires will be. Doing this accurately will help to make your wiring clean and your bundles easy to manage. Heres the first secret: Buy a roll of string. Not plastic twine or yarn from your wife’s craft basket, but a roll of colored, small, flexible nylon string. We’ve found the best string to be woven masons string. Many people use snap line/chalk line string, and it works OK, but it has a tendency to untwist when cut because it’s a twisted string. Woven string wont fray or unwind.
Instead of using an old 25-foot tape measure and roughly figuring 12 feet for Widget A (because it’s 12 feet from the panel to the location of the widget), take your roll of string and tie or tape it to the point where the widget is to be installed. Then run that string exactly how you think you’ll run the wiring for that unit. You’ll quickly find that the 12 feet you initially thought would work can easily be off by 20% to 30% or more. By the time you go up, down and sideways to route through ribs and bulkheads, you eat up a lot of length in wire. If you plan some of the more complicated wiring runs using lengths of string as your guide, you wont end up with wires stretched tight. (I occasionally see these on panels or in planes, and we refer to them as guitar strings. When plucked, they almost sing!) It’s always easier to cut wire off than to add to it. Needless splices in the middle of a bundle not only look unprofessional, but they can cause the bundles to be difficult to manage.
Now that you’re well along in your planning stage and figuring wire lengths you can start running wire, right? Wrong! We have more planning to do before we actually start pulling wires.
Besides wires being run all over the aircraft, there will typically be a number of other items that need to be routed. Sometimes these can share the same routing as the wires, but sometimes they absolutely should not. Before you start pulling wires, think ahead about other items such as pitot/static tubing, antenna coaxial cables, large battery cables, fuel lines, oil lines, trim/control cables, and anything else that may need to share routing with the electrical wires throughout the airplane.
There are certain combinations you want to avoid. High-voltage strobe cables, for example, probably shouldn’t be clamped to fuel lines. However, some items can easily share space as long as the materials of one wont cause chafing or wearing of the other. Pitot/static lines are typically a nylon tube and will not interfere with wiring. Control cables, on the other hand, should avoid everything else in the aircraft. Wires should never be close to or routed in such a way that they intersect control cables or other moving devices.
Try to form a plan where electrically noisy wires are not intermixed with electrically sensitive wires. Examples of electrically noisy wires would be P-leads, strobe wires, alternator leads and electric motors such as those for trim/flaps or gear. Electrically sensitive wires would be antenna coax, signal wires and audio wires. When correctly installed, all wires should be properly shielded to avoid problems, but keeping the runs separate will ensure a good, electrically quiet airplane.
Working Around Obstacles
Most of our homebuilt aircraft will have some sort of obstacle between where the wires start and where they end. This might be a firewall, bulkheads, wingroots, spars or even simple interior panels. This means you need to figure out how and where the wires will traverse these obstructions. It’s not as simple as drilling a hole and threading wires through it. Holes in such items should normally be protected with grommets, bushings or other hardware that keep the wire from chafing against it. Grommets are generally manufactured from a soft rubber, and therefore are best to use with either single wires or when the bundle of wires is known. They’re very good at protecting wires, but they can make the job of running multiple wires fairly difficult, because the soft rubber grabs onto wires as the diameter of the wire bundle reaches the diameter of the grommet.
Bushings are typically a harder nylon-type plastic material that allows wires and or tubing to be routed easily. Bushings are quicker and easier to install than grommets, and they do almost as good a job of protecting the wires. They do not seal like a grommet, but they take up less space then a grommet does and are more flexible when being installed in varying thicknesses of materials.
I realize that it’s often not possible to know each and every item that needs to be run throughout the aircraft prior to when you’re ready to do it. Im just trying to get you to anticipate things you’ll need to deal with later on. Try to keep these in mind when you start running wires or plumbing the plane. The more you can plan, the happier you’re likely to be in the end.
Another close view of the many wires in a complex panel. Note the color coding of certain wires. As an example, in this picture all shield ground pigtails are green, power wires are red, ground wires are black, EGT/CHT wires are brown, and GPS signal wires are blue.
Execution
Heres where we talk about the actual running and bundling of the wires. What do we mean by bundle? Technically, it’s any group of wires. Wire bundles can range from a simple grouping of two or three wires, to bundles of hundreds of wires that are many inches in diameter. On our typical homebuilt sport planes we will not have jumbo-jet-sized wire bundles, but you may be surprised at the number of wires you will have running through the aircraft. For a typical RV-sized sport plane, you will likely end up using 500 to 2500 feet of wire and nearly 100 feet of coaxial cable. More complex homebuilts will use even more. Much of this wire will be run alongside or be shared in bundles with like wires or other types of wires running in similar directions. Items such as autopilot servos typically require five to eight wires run to them from the instrument panel. You can either pay someone to build you a harness, or you can do it yourself. If you intend to do your own wiring in the aircraft, many times you can purchase wire that is pre-twisted or pre-bundled for its intended purpose.
Two ways to clean up bundles of wires that are running to a single unit is to either twist them together or enclose them in a sleeve. This material (called expandable tubing or snakeskin) is inexpensive and easy to procure from a number of sources, as it is used extensively by professional avionics shops and manufacturers. It’s easy to use, and because it’s flexible and expandable, it is one of the most effective ways to manage a bundle of wires.
If you need or intend to twist wires together, it can be difficult to do yourself with a large number of wires. However, twisting smaller sets of wires (two, three or four) is easily done. You simply cut the group of wires you’d like to twist (cut them about 15% longer than you need). Then secure one end of the wire group in a vise or other manner to hold them securely. Insert the other end of the wire group into an electric drill (preferably cordless) and start twisting them. Keep some tension on the group, and twist them slightly beyond what you desire (they will unwind a bit when you release them), but don’t twist them too tight. Examples of wires that are often twisted for both convenience and electrical reasons are push-to-talk (PTT), flap-motor and electric-trim-motor leads along with leads to some sensors. This makes the wires easier to run, and also acts as a kind of shielding.
Whatever method you choose, twisting or sleeving, you still need to work at keeping the bundles clean and combed. This means that you try hard to keep wires from crossing or weaving back and forth around each other. That not only looks horrible, it makes working on the wiring later extremely unpleasant. It may take a few extra minutes with each wire you run to keep it from looping or intersecting other wires in a bundle, and sometimes you might need to remove the bundle and rerun it, but it’s worth taking the time to do it. This is probably what gives professional jobs the most distinct appearance of being well done.
Security
Once you have a plan and have started running wires throughout your airframe and around the panel, you’ll quickly notice that without some help, the wires will run amok and start looking like the proverbial bowl of spaghetti. While this may be somewhat unavoidable throughout the build, it needn’t be that way once it’s finished. A number of tools and methods will help keep your bundles of wires from flopping around and getting tangled up.
The first order of business is the use of zip or cable ties. These cheap little devices (usually about a penny or two each) should be used religiously and prolifically while running wires in an airplane. Think of them as temporary (and easily disposable) holding devices. You should purchase a couple thousand and use them repeatedly. For example, if you’ve started to create a bundle of wires running fore and aft in the plane and you need to add wires, simply run the wire and zip-tie it as necessary to secure it. These temporary ties don’t need to be super tight; you’re just using them to keep the wires under control. Cut off older ties as you add to your bundle. Don’t worry about the cost, just use them judiciously. Be careful not to cut into your wire bundles as you clip off the old zip ties.
When you’re finished (or likely think you’re finished) with a bundle of wires, you can then install some zip ties permanently and tighten them up. Do not overtighten zip ties, or they may eat through the wire insulation (though this is not common).
In addition to or in place of zip ties, many professional shops still hand-lace their bundles of wires and avionics with lacing cord. This is a wax-impregnated nylon cord that when tied properly provides a nearly perfect way to secure bundles of wires. There are two or three different types of knots that can be used with the lacing cord, and most work well if done properly. However, if not done properly, they will simply fall off. Why use this method instead of zip ties? Well, first it’s a matter of pride in craftsmanship. Second, if you run your hand around many bundles of wire behind instrument panels, you may notice that zip ties that haven’t been properly trimmed tend to cut the heck out of your hands/arms/fingers. Furthermore, cord is probably a bit better on the wire bundle than zip ties, as it’s flexible and will conform to the shape of the bundle. The cord also doesn’t deteriorate like zip ties do, and doesn’t leave sharp ends when cut. Lacing/tying wires by hand is a time-consuming process, but it is not nearly as difficult as you might think. There are a number of places where you can see how to tie the knots (FAA AC43.13 Acceptable Methods, Techniques, and Practices illustrates it), and in the end you really will have a nicely finished bundle of wires.
Suppose you just finished hand-lacing an entire radio stack and then you realize you forgot one wire. Don’t despair, and certainly don’t start cutting off your zip ties or hand-laced knots. Everyone who is wiring his own airplane should have a wire spoon. This nifty little device is relatively unknown to general aviation, but anyone with a military or airline background will be familiar with it. It’s simply a small spoon-shaped device that will allow you to insert a wire into a previously secured bundle. The spoons can be purchased at a few online avionics suppliers and are now much easier to find since Ive started to push them, usually at about $10 to $12. If you don’t own one and you end up doing any wiring on your project, it’s well worth the money to purchase one.
You’ll also notice that most professional installations of wire in aircraft routinely use devices to physically secure wires and bundles of wires to the airframe. The best method is to use an Adel-style cushioned band clamp that is secured to the airframe, panel or radio rack. While these can be somewhat annoying to install, they really are the best method of securing bundles. However, many times it is not possible or easy to use a clamp to secure a bundle. Sometimes you just need to keep wires from flopping around (like under a control stick, or near a rudder/elevator trim servo), so something like a clamp is overkill. You can zip-tie things to the airframe, but be very careful to make sure wires or bundles of wires are never secured directly to any part of the airframe without some sort of anti-chafing or anti-rub tape/protection.
One easy way to do this is to use a small device that you can secure zip ties to that either adheres to the airframe or bolts to it. These are called zip-tie bases and are relatively inexpensive. You should still be a bit cautious when using the adhesive bases, however, because they are not designed to be used in high-temperature areas. If you stick them to the firewall, it’s likely they wont remain there. Adhesive zip-tie bases are more for keeping wires from flopping around than for holding lots of weight or affecting the routing of wires. If they are being installed for that purpose, consider installing them with a screw, rivet or better adhesive.
Last but not least is safety. How do we keep bundles of wires safe? Well, this depends on the relative location of a bundle of wires and its proximity to things that could cause it harm. For example, wires running firewall forward are subject to high heat, high vibration and overall a much more severe environment than at other places in the airframe. When passing large bundles of wires through a firewall or pressure bulkhead, ensure they are properly secured, sealed and are not chafing on the bulkhead. Some groups of wires may be run through connectors, while others should be run straight from the device to the engine. Wires such as EGT/CHT thermocouple wires generally should not be run through connectors. Therefore, it’s imperative that you keep them securely fastened both in front of and behind the firewall. If you intend to use zip ties firewall forward (it’s perfectly OK to do so), make sure they are either the high temp or Tefzel type. Caution: Never zip-tie wires directly to an engine mount without using some sort of anti-chafe material. Zip ties can and have eaten their way through steel engine mounts! Heavy wires should be properly secured and terminated as well. Main battery cables should always be fastened with appropriate clamps.
There. Thats a lot to digest, I know. But if you follow most of the advice, you’ll see there’s really is no magic to making your wiring attractive and easy to work on. Attention to detail and taking it one wire at a time is what it’s all about. Also, when creating bundles of wires behind the panel, keeping the lengths of wire in check and as exact as possible will go a long way toward avoiding extra loops in wires or those guitar strings we see once in a while. Spend the money on extra zip ties to use as temporary holding devices while running wires.
Bundling and routing of wires may not be as exciting as hanging your engine or installing the wings, nor will it be seen by most passers-by at the airport, but its probably one of the most important contributors to easy future maintenance of your aircraft, as well as to a reliable, quiet and safe electrical system.
Please have a look at LaceLok by DMC tools. We’d love to hear what you think about this new solution to wire bundling!