Build Your Skills: Composites In Part 6, enough theory! Lets build some wheel chocks. BY BOB FRITZ I recently sat in on Dave Saylors Fiberglass for RV10 Builders class (see the sidebar, Page 40) in which he had everyone build a set of wheel chocks. It was such a good experience I thought I would shamelessly pirate it for this article. I was also fascinated to see the different interpretations of seemingly straightforward instructions. More on that later. What well do here is a dandy little application of whats come before in this series. The nice part is that the result is not only useful, but you’ll be the envy of your neighbors and invited to give talks at the local Toastmasters. OK, thats a bit over the top, but you will have a useful set of wheel chocks that weigh about a tenth of what those old wood wedges you’re lugging around weigh. Id suggest you build at least two sets because your buddy will want one. Glass cloth: 24 x 7 inches. Don’t forget to cut this on the bias. Flox: 1 cup. Microballoons: 1 cup. Epoxy: 2 cups. Mix per the manufacturers instructions…but not all at once! Stir sticks: a dozen or so. Rubber gloves: at least six pairs. Cups: Paper, not plastic, and definitely not wax coated. A dozen or so will do. Foam for mold: 2-inch square by 24 inches long. It should be small cell; the type that flower arrangers like to use is perfect. Were going to split it into two triangles so if you can buy a triangular piece, all the better. Rope: 18 inches long and any diameter between 1/8 and 3/8 inch is fine. Any material is OK, but plastic is best. Clear plastic-wrap: One 24-inchwide roll will do. Heavy gauge is best. Kitchen wrap clings to itself too easily and tears apart instead of coming off the hardened glass. Roller: Should be 3 to 4 inches wide, any diameter. Even a piece of broom handle will work, but you like tools so heres an excuse. Circular razor, aka pizza cutter. 1-inch brushes: a dozen of the cheap disposable kind. 60-weight sandpaper: One sheet is enough, really rough grit. One old, large, flat-blade screwdriver or chisel for digging out foam. Peel-ply: One piece about 3 inches wide by 24 inches long. Needle or pushpin for piercing bubbles. Bandsaw or cut-off wheel to cut the hard fiberglass. Step drill for use on hard fiberglass. Drill motor for that step drill. Safety glasses. 36-inch straightedge. This project will take a couple of hours on day one, an hour on day two, 30 minutes on day three. Youll also need warm weather or a warm workshop. Below 65 F, and the epoxy wont harden. Use a small workbench with a plastic, or at least disposable, top. The epoxy will get stuck to it, ruining a wood surface. Split the foam square into two triangles about 24 inches long. Sand the three edges to about a 1/4-inch radius and vacuum off the dust. You are wearing the safety glasses, aren’t you? Mix epoxy and add micro until it has the consistency of mayonnaise; the brand is not critical. Paint this mixture onto foam and set foam aside. This fills the pores of the foam. Lay out 30 inches of clear wrap. Lay out fiberglass cloth onto wrap. Work out the distortions so that the piece is square and straight. Lay second fiberglass on first and straighten it. Mix about one cup of epoxy. Pour over cloth. Spread with brush or squeegee until completely wet. The cloth will be bright until soaked with epoxy. Lay the second sheet of plastic wrap over the wetted cloth. Use the roller to work out bubbles and excess epoxy. You need only a light pressure; don’t distort the glass. Use the straightedge and the circular razor to cut through the plastic and glass. You want to have a sandwich that will wrap around the foam, overlapping at least one face, and be about 1/2 inch longer than the foam. Use the handle of the brush to push/ lift the corner of the upper plastic. Gently pull away the upper plastic and dispose of it. Place foam stick on the cloth 21/2 inches from one edge of the cloth. (Read the next step to understand this positioning.) Lift plastic so that it wraps the cloth over one side of the foam mold and halfway down the second side. Brush the surface of the plastic at 45 to smooth out air bubbles. This angle minimizes distortions in the cloth. Use the pin/needle to pierce any bubbles and continue smoothing out the air. Use the handle of the brush to push and lift the corner of the plastic. Lay plastic back down to original position leaving the glass cloth in place. Lift the other plastic/glass over and around the foam. Roll the foam/epoxy over if needed to get all the cloth in contact with foam/ epoxy. Be careful to not roll the plastic wrap in between the layers of glass. Brush the surface of the plastic at 45 to smooth out air bubbles. Don’t forget to use the pin if needed. Unwrap the plastic back down to original position, leaving glass cloth exposed on two sides of the chock. Lay the strip of peel-ply onto one side of the foam mold. Use a brush to smooth out the peel-ply. Use the needle to pierce any bubbles and then continue smoothing. Rotate the part so that the peel-ply is down; remove the remaining plastic wrap and dispose of it. Place it on a flat sheet of new plastic wrap and let it dry 24 hours.Materials List
Other Requirements
Building Day 1
Building Day 2
Pull off peel-ply. It will be a firm pull. Note that this side is now the down side. Use the saw to cut off both ends of the stick so that they’re square. Draw a cutline at the midpoint of the length of the stick.
Place a mark on each side of the cut-line about 1/2 inch away from the cut-line. This is where you’ll drill holes for the rope.
Cut the stick in half. No, not lengthwise!
Use the screwdriver to dig out 1 inch of the foam from the end of both chocks where you marked the rope hole. Thats why I said it should be an old screwdriver. The foam is soft stuff, and well fill this in with epoxy later.
Dig out 1/4 inch of the foam from the other end of both chocks.
Drill one hole, barely large enough for the rope, where you made the mark on each chock.
Tape the chocks together, base to base, with the rope holes at the same end.
Cut about 18 inches of rope. If its plastic, use the soldering gun to melt through so that it wont fray. If its a fiber rope, wrap it with electrical tape and the cut at the midpoint of the tape to stop the fraying. Insert the rope through the holes.
If the rope is a snug fit through the hole, good. If not, tape the rope to the chocks. Don’t bother with a knot; the next step is the real anchor.
Mix about one cup of epoxy and paint it liberally into all four ends of the chocks, soaking the rope ends as well. This wetting out ensures that the epoxyflox used in the next step will adhere to the chock and the rope.
Add flox to the remaining epoxy to the consistency of cold peanut butter. You don’t want it to move when held on a stir stick. One of our guys left it rather thin and, though it made a nice, smooth end, it meant that he had to wait a day for it to set up before he could fill the other ends.
Pack the mixture into the ends of the chocks so that it stands up about 1/8 inch above the edges. Don’t worry about getting it smooth, just have it stick out.
Place the chocks on a couple of stir sticks for 24 hours so that the flox will fully set. Forget the stir sticks, and you risk gluing the chocks to the workbench. Nice set of work-stops you’ve got on the bench, Fred. But shouldn’t they be moveable?
Building Day 3
Untape the chocks and sand off all four ends to square and smooth. Heres your excuse to go buy that inch-wide belt sander.
Paint on or write your N number. If you dont, these are guaranteed to grow legs and walk away.
Be prepared to do it again for your buddy. See, I told you to make two sets.
I built at Dave Saylors AirCrafters and then put it in the airplane to take it to my shop about an hours flight away. Mistake. The air within the foam expanded as I went to altitude with the result being rather large bulges where the wet glass was pushed away from the foam. Lesson: Don’t move the piece until it hardens. The saving grace is that holes, separations and bubbles are of no consequence here because these are non-structural components. After all, Im just going to throw them on the ground and park an airplane on them! I went on to build a second set that came out perfect, though, so Ill be able to make that Toastmasters talk after all.
Even with bulges and voids, the upside is that you’ve learned a lot about how to work with composites. Arent you glad you did this before you started on that RV-10? The folks that came to the class were. After finishing, they all agreed that building this simple set of chocks left them rather proud of themselves and confident enough to tackle a more ambitious project…like glassing in an RV-10 windscreen.
Next month well take up vacuum-bagging. No, thats not a game played in Scotland by guys wearing skirts. �
For more information about AirCrafters builder assistance, call 831/722-9141, or visit www.aircraftersllc.com. A direct link can be found at www.kitplanes.com.
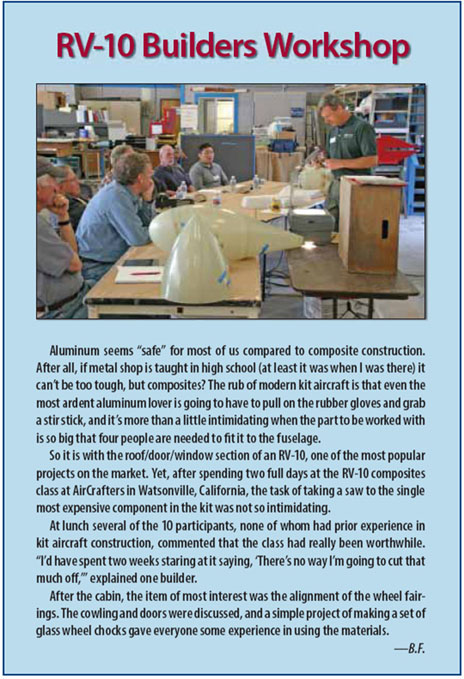