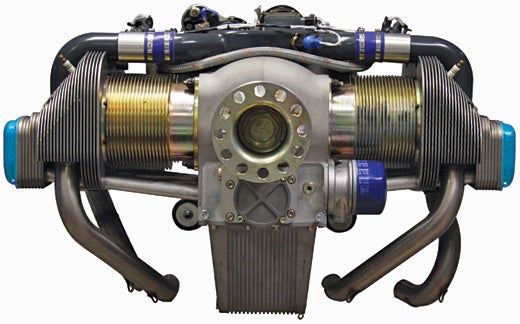
The UL Power four-cylinder engine looks every bit the traditional aircraft powerplant.
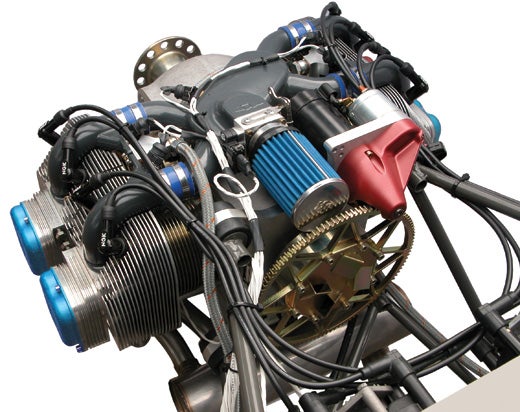
If you’ve been a KITPLANES® reader for more than 15 minutes, you have probably read about the UL Power engines. We mentioned them briefly in the April issue, but have been following the design for years. We first reported on it in the November 2007 issue, some months after the UL Power 260i was shown at the Sebring show that January. Back then, there was no U.S. distributor, and engines were just beginning to trickle in from Austria.
Since then, UL Power has drafted a new U.S. distributor in Robert Helms, who calls Lake Ozark, Missouri, home. UL Power North America is an important piece of the puzzle, helping kit manufacturers develop firewall-forward packages and providing customer support. Looking at the work Helms and UL Power North America has done in the background, I can say that the support apparatus, while nothing the size of, say, Rotax’s well-developed machine, has all the critical elements in place. More on this aspect at the end.
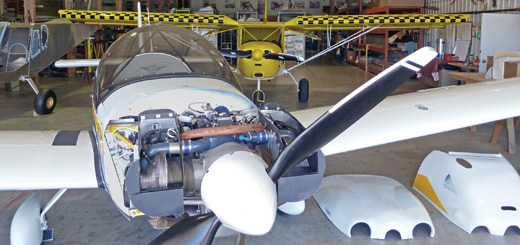
Firewall-forward packages are available from Zenith for the CH 650 and CH 750 aircraft.
Under the Covers
At its core, the UL Power series of powerplants is conventional in appearance but shares more with Porsche and Volkswagen flat engines. In general terms, all of the UL Power models are air cooled with straight, ungeared crankshafts terminating in a prop flange. The right-side cylinders are displaced forward and the left-right stagger is a bit more than we’re accustomed to seeing in opposed-piston engines for one simple reason: The crankshaft is supported by five bearings. The standard Continental/Lycoming arrangement has the crankshaft journals unsupported between opposed cylinder pairs. (Say, between cylinders 1 and 2; the crankpins are located 180° apart, but there’s no main bearing between them, only a thick web.) UL Power’s approach is more automotive/motorcycle than traditional airplane, which reflects the genesis of aero engines from large, lightweight, slow-turning powerplants and the contrasting needs of high-performance auto engines, where crankshaft stiffness permits high-rpm operation and the overall length of the engine is less of a concern. What’s more, the UL Power bottom end uses a “sixth bearing” that’s actually a set of ball bearings used to transfer thrust loads from the crank to the inside, forward face of the crankcase. Currently, the design does not accommodate hydraulic propeller governing, so builders will opt for fixed-pitch, ground-adjustable or electrically adjustable propellers only.
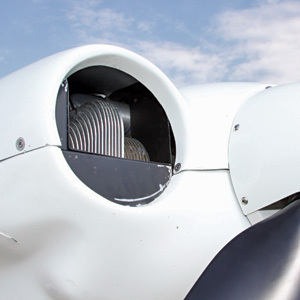
In the initial CH 650 installation, cooling air is admitted by round ducts and managed by simple sheet-metal baffles.
In other respects, the UL Power configuration is utterly conventional. A single camshaft lies below the crankshaft and opens the two valves in each cylinder through lightweight aluminum pushrods. The engines currently do not have hydraulic lifters or cam followers, so periodic valve adjustments are required, which are made through simple screw-and-locknut adjustments in the head. Each rocker-box cover is secured by three screws and is sealed with an O-ring in a groove cut into the head; leakage and access should not be a problem. According to the UL Power maintenance manual, available online, you must check valve clearances at 15, 50, 100 and 200 hours total time. (The chart does not continue past 200 hours, so it’s hard to know if the checks are meant to be at 100-hour intervals after 200 hours, but that’s the working assumption.)
Each aluminum head is pressed into steel liners that are in turn bolted to the cast-aluminum, vertically split crankcase. Again, very much like standard aircraft practice. The D-shaped combustion chambers feature prominent squish zones to help promote efficient combustion, which allows the company to place the valves parallel to one another for simpler machining operations and a more compact rocker box. The heads follow popular motorcycle design with side-by-side Bosch auto-style spark plugs—not the over/under scheme used on large-bore aero engines. The recommended plug is the Bosch FR 5 DTC, which has three non-adjustable electrodes. The manual warns that use of 100LL fuel will shorten spark-plug life and recommends shortening the replacement interval, which is currently 200 hours. The heads appear to have sufficient cooling-fin area—slightly more per combustion-chamber surface than a parallel-valve Lycoming or a Continental O-200, but less than an angle-valve Lycoming. UL Power has set modest cylinder-heat temperature limits; 375° F is the maximum with 320° F as maximum continuous. Consider that some Lycomings let you run to 500° F.
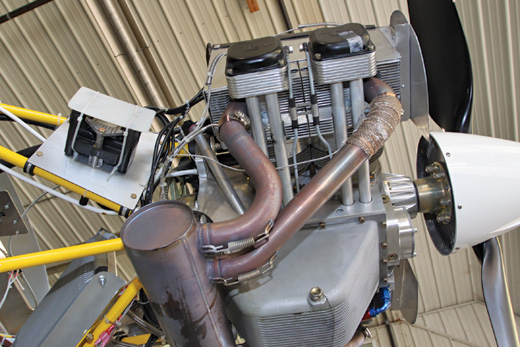
Engine packages will include a full exhaust system with muffler. Note the finned oil sump and the solid pushrod shrouds; that means replacing those seals will require removing a cylinder.
Pick Your Model
Today, UL Power makes six variants of two basic engines. The UL260 series is based on a 105.6mm bore and a 74mm stroke (or 4.157 inches by 2.913) for a bore/stroke ratio of 1.43. Traditional aircraft engines are in the 1.1 to 1.2 range, while the most radical motorcycle engines are highly oversquare (much more bore than stroke) with bore/stroke ratios nearing 1.8. What’s the point? Well, the comparatively short stroke explains how this relatively large four can spin safely to 3300 rpm.
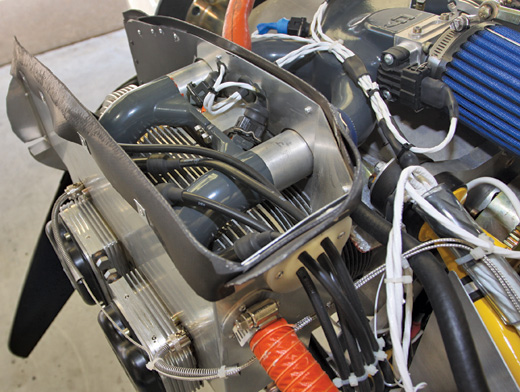
The electronic fuel injectors are visible just inboard of the dark-gray intake tubes. One injector per cylinder feeds the engine a supply of unleaded autogas or 100LL.
That smaller four-cylinder engine produces between 97 and 107 horsepower, depending upon compression ratio, which ranges from 8.16:1 to 9.1:1. Aerobatic and high-rpm helicopter versions are also available. Moving up a notch you get the 350 series, which adds stroke to the 260’s unchanged bore measurement; stroke increases to 100mm (3.937 inches), which brings the bore/stroke ratio closer to conventional aircraft engines. Yet the relatively short stroke—still 0.44 inches shorter than a Lycoming O-360’s—maintains reasonable piston speeds at the 350’s 3300-rpm redline. The bonus for more stroke? A wide, generous torque curve and improved peak power, now from 118 hp with low compression to 130 with a still-reasonable 8.7:1 compression. Thanks to that broad torque curve, the 350iS variant is capable of 75% of rated power (97.5 hp) at just 2200 rpm. The torque curve is so flat the engine makes 236 foot-pounds from a little more than 2100 rpm all the way to 2700. Rather than have the torque peak late to boost horsepower figures, the UL Power tuning puts the bulk of the work at engine speeds likely to be used day to day.
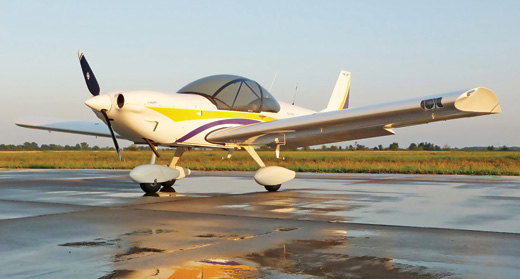
The current Zenith FWF setup for the UL Power engine places the oil cooler inlet beneath the propeller spinner.
Another strong suit for the UL Power is specific fuel consumption. According to documents published by the company, the specific fuel consumption of the 350iS ranges from a best of 0.396 pounds of fuel per horsepower-hour to 0.51 at 70 hp and above. The 350iS is actually quite fuel efficient at full power, with a claimed spec of 0.46 pph/hp-hr at 110 hp/3300 rpm. Most traditional aircraft engines are at 0.50 or higher at high power settings. The one thing a savvy pilot cannot do with the UL Power is intentionally run lean-of-peak EGT to truly maximize fuel efficiency; the computer won’t do it. Compared with the Rotax 912S, the UL Power has a couple of important advantages. First, it’s turning slower, so the amount of internal friction is less; plus, there’s no gearbox to rob a few percentage points of power. Second, the UL’s fuel injection is more accurate and consistent than the Rotax’s twin carbs. The same comparison could be made with the single-carb Jabiru 3300.
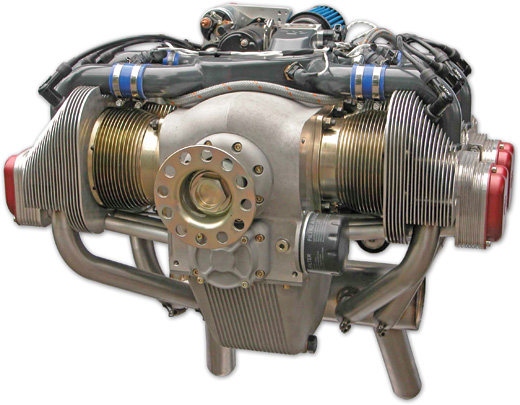
A solid-crank engine, the UL Power must be used with a fixed-pitch or electrically adjustable prop. That’s the oil pump just below the crank and to the left of the spin-on oil filter.
Wait, There’s More
So far the UL Power four-cylinder engines have been a modest success. According to the U.S. office, more than 300 engines have been sold worldwide, with 30 to 40 in the U.S. and approximately 15 flying. The factory produces one engine a day but could easily double that output should demand so dictate.
But the company has high hopes for its next project, a six-cylinder version based on the existing 260/350 architecture. A new cylinder-head assembly for the center cylinders was necessary, but otherwise the six is just a 3:2-scale four, including the two principal bore/stroke sets. With the shorter stroke, the new six is the 390i. But the one of interest to many pilots will be the 520i and the 520iS, which is currently putting out better than 200 hp in testing. Think about that: a 5355cc/320-cubic-inch engine capable of 200 hp at reasonable prop speeds and, according to initial testing, 220 hp at 3300 rpm. As we went to press, UL Power North America announced that the larger six had gone into early production. The 520i, rated at 180 hp, will sell for $33,000, while the 520iS, rated for 200 hp, runs $35,000.
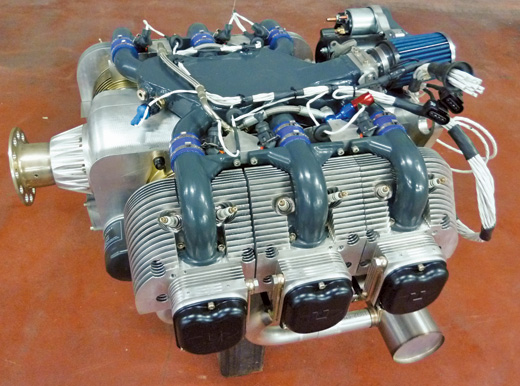
Here is the first production six-cylinder from UL Power. The 5.2-liter engine produces 180 to 200 hp.
Price Points
High technology doesn’t usually come cheap, but the UL Power series is competitively priced. Starting at $17,290 for the 260i (97 hp) and ranging up to $22,950 for the 130-hp 350iS, UL prices are absolutely in the ballpark. The current price for a 100-hp Rotax 912S from a kit manufacturer is just under $19,000. Jabiru will sell you an 85-hp 2200 for $15,500 or the 120-hp 3300 for $19,900.
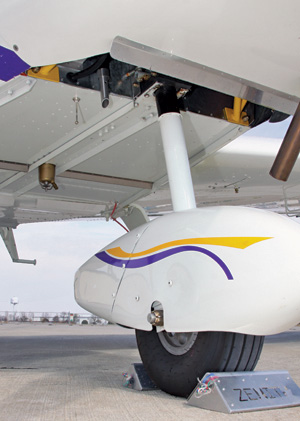
During development, Zenith fitted the CH 650/UL Power combo with a “trip strip” at the cowling outlet to improve cooling. A revised oil-cooler location may make this unnecessary.
Initial costs are one thing; ongoing development and support are something else. In the photos that accompany this story and the Zenith CH 650 B flight review in this issue (Page 8), you might note some oil on the sump and exhaust system of the 350iS that the Zenith has been running. Turns out one of the rocker-box oil supply lines had sprung a leak at the case fitting. It was possible to over-torque the fitting, which deformed the sealing nipple. Once deformed, no amount of further tightening would stop the leak. In just a few days, UL Power in Belgium, working with the North American office, came up with an improved fitting that was not only more robust but also field-repairable. It’s a small thing, sure, but consumer happiness is really the sum of many small things done right.
For more information, call UL Power North America, LLC at 573/434-0075, or visit www.ulpower.net.