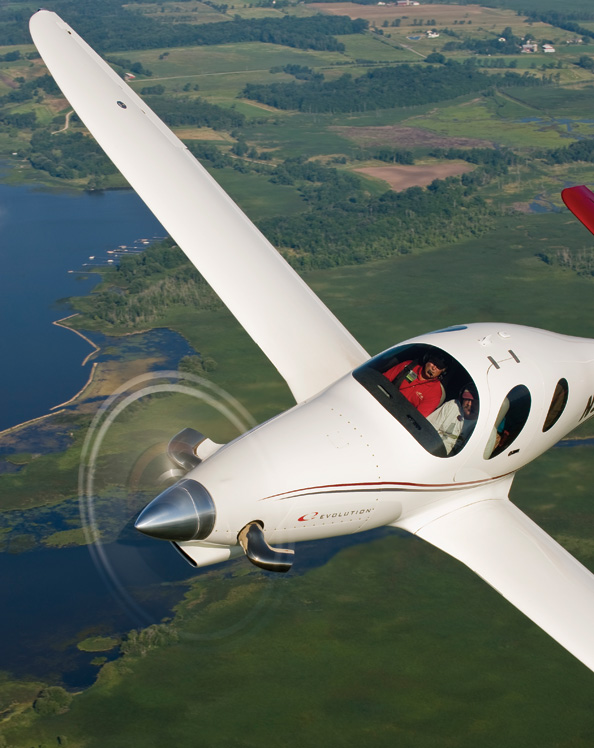
As we know from the first two installments in this series, Wendell and Martha Solesbee are building a Lancair Evolution, an honest-to-goodness 300-knot luxury kit aircraft that will someday whisk them across the country in a veritable eye blink. (These appeared in September and October, in case you want to get caught up.)
But for now there is still some assembly required, as they say. While the Solesbees’ project began life in the factory-authorized build center, better known as Brian Harris’s shop, they are now home on their own. The big structural parts were all done before transport from Oregon to California, but there are numerous systems to install, an engine to hang, interior and exterior finishes to worry about and, well, a lot of work to do between here and flying.
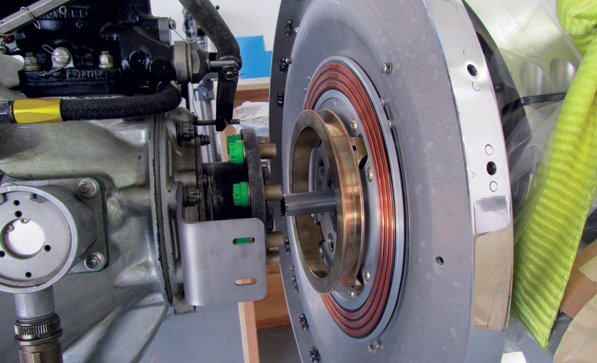
The contactor ring on the back of the prop allows for electrical power to be transferred to the propeller heating (deicing) elements. Access to the prop bolts becomes limited where the prop and engine come together. Wendell had to fabricate a special tool to tighten these bolts.
A Systematic Approach
So there are some systems to install. How bad can that be? The builders have instructions, right? Well, sort of.
The Solesbees were early kit buyers. When they first arrived back home in Chino with their new project, the instructions were what you might call a work in progress. When they unloaded the fuselage and wings at their hangar the instructions consisted of a few dozen sheets of notebook paper with sketches, notes and some dimensions. Because the Solesbees have previously built two other airplanes including a Lancair IV-P, they were undaunted by this considerable challenge and simply got to work.
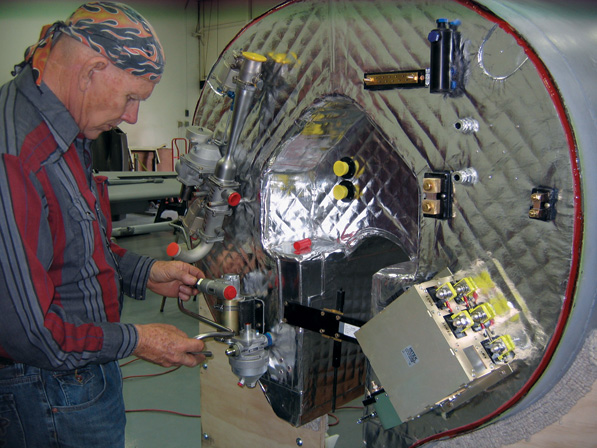
Builder Wendell Solesbee connects a fuel line to the gascolator on the firewall. The firewall blanket protects the composite structure from the heat of a potential engine fire. On Wendell’s right is the electrical control unit. In front of him and slightly to his left is the flow pack, which controls turbine bleed air used for cabin pressurization. Other items seen include the brake fluid reservoir, a ground bus bar, and two ammeter shunts.
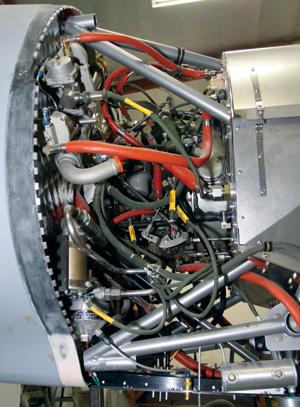
The space between the engine and the firewall is a busy place in the Evolution engine compartment. In this photo the flow pack and gascolator stand out. Beyond that it looks like a big bowl of spaghetti, but the Solesbees know where everything goes, or so we hope.
In fairness to Lancair, the instruction manual is now well-developed and available for anyone to see on the company’s web site. It is updated frequently and is apparently up to the considerable task of guiding a builder through the complex process of assembling a high-performance airplane, but it didn’t start that way. Few new kit manufacturers get the instructions right from the start.
We will look at each system, in no particular order, to see what the Solesbees had to do. Remember they are not dropping into a professional builder-assist center from time to time where every tool and part is laid out perfectly to make assembly as easy as possible. They are working the old-fashioned way, which is why we are so interested in following along as they learn. Which skills are to be tested? Builder-installed systems in the Lancair Evolution include powerplant, electrical, avionics, fuel storage and delivery, hydraulics, flight controls and rigging, cabin pressurization and air conditioning. Yes, just about all of them. (Interior and exterior finishes will be covered in a future installment, as will the first flight.)
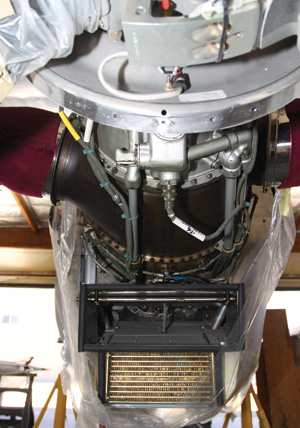
The engine air intake mates to the scoop on the cowl. Inside the cowl the air is split so that some of it goes to the oil cooler, seen below the engine air intake, with the rest going into the engine. The plastic is there to keep dust out of the engine while the Solesbees sand the fuselage.
Put Your Pratt Here
Let’s start with firewall-forward. Lancair helped the Solesbees secure a mid-time Pratt & Whitney PT6A, which saved them about $200,000 as compared to buying a new engine for about $450,000. The factory also provided the parts and fabrication necessary to set the engine up to install. This prep work and fabrication currently costs about $85,000 and is necessary to ensure that the engine will work well in this plane. If these numbers are leaving you a bit short of breath, you’re not the only one. It takes time to get used to turbine prices. As early builders, the Solesbees saved some money compared to current costs, but they also paid a price by being guinea pigs for a developing product. Still, the fact remains that if you’re going to fly on kerosene, you must be prepared for the overall economics of it.
The firewall-forward process begins with installing a protective blanket over the composite firewall structure, a step common to Lancairs and other all-composite aircraft. The blanket is there to ensure that the heat that could be present in the case of an engine fire will not ignite the composite structure, which will start burning on its own once it reaches about 700 to 800. The test is to be sure that a 2000 engine fire can be contained for 15 minutes before it becomes a whole-plane fire. Lancair makes this protective blanket for the builder, and all the builder has to do is secure it in place. Once the blanket is installed, items like the flow pack (pressurization), the gascolator, the auxiliary fuel pump and the electrical control unit attach to the firewall. Lancair provides a layout for these items, so it is fairly easy to place them before the engine goes in, which makes things much simpler.
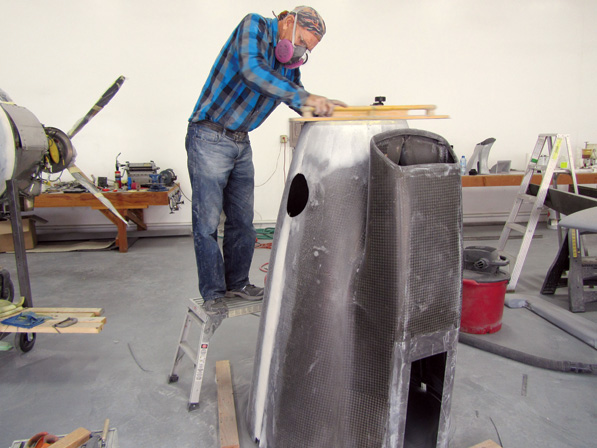
With the engine and propeller now in place, Wendell can bring his considerable expertise with composites to bear on fitting the cowl. This was the most difficult composite work to be performed on the Evolution. It is also one area where an inexperienced builder would need some serious help.
With the preparation now complete, the engine and mount slide into place. Lancair, as part of the firewall-forward package, has pre-installed the intake plenum, the oil cooler, the starter/generator and a host of other minor accessories, greatly reducing the need to work in the tight space between the engine and firewall. A massive Hartzell four-blade prop caps the engine installation, but the contactor ring to transfer power to the prop’s heating elements produced some tight working spaces for securing the prop bolts, forcing Wendell to make a special wrench just for the task.
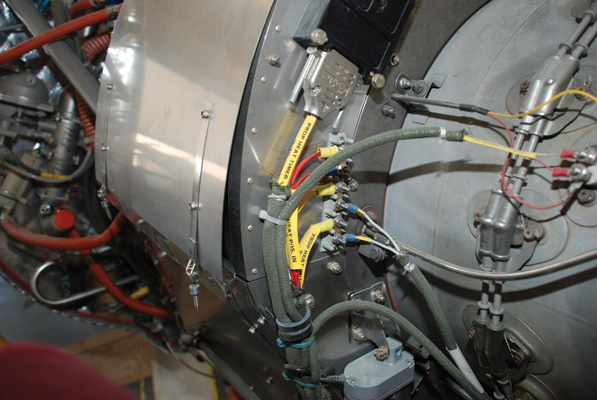
Pre-wired electrical harnesses make wiring easy for the Evolution builder. The clear labeling on these harnesses speeds up the work and ensures that wires go where they are supposed to.
Volts and Amps
The electrical system of the Evolution goes a step or two beyond what most amateur builders will ever tackle, but it encompasses items that individually are familiar. They are just bigger and more complex than what most of us are used to seeing. The system begins with a pair of Concorde RG24-20 batteries. They are only rated at 19 amp-hours each, but remember that at 24 volts a 19 amp-hour battery puts out power (watts) like a 38 amp-hour, 12-volt battery. They weigh 42 pounds each and together put out power equivalent to 900 cold-cranking amps at 12 volts. The Evolution power control system connects these in parallel for starting.
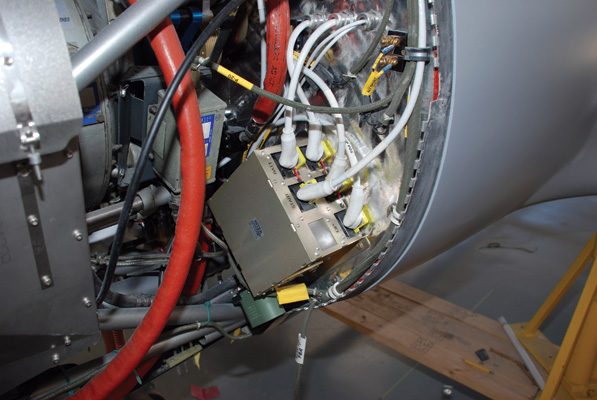
Big power needs big wires. Those king-sized wire crimpers come in handy when putting ends on the #1 and #2 AWG wires that run from the batteries and the starter/generator. The power control unit handles all the power switching, routing and regulating duties for the Evolution. In most homebuilt airplanes, each of these chores is handled by separate components.
We ordinary builders would expect to see things like master/starter relays and voltage regulators on the firewall, but in the Evolution all of these functions fall to the power control unit. This box manages the battery charging and electrical distribution chores, making sure power is always available when and where it is needed. To connect it, the Solesbees got good use out of their king-sized wire crimpers, where #2 and #1 AWG wires are common.
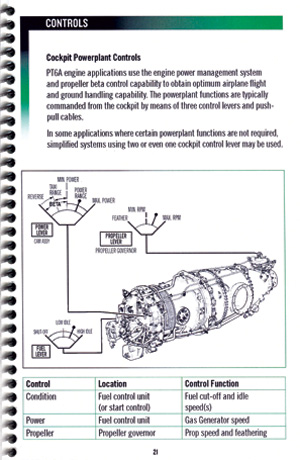
A page out of Pratt & Whitney’s turbine manual. Lancair helped the Solesbees secure a mid-time P&W PT6A engine for their Evolution.
From the power control unit the big wires head to the starter/generator. This engine-mounted unit combines both starting and charging tasks into one device. This is standard for turbine engines, but unseen with piston engines, at least the kinds of piston engines homebuilders are used to working with. It makes perfect sense to get double duty out of such a heavy piece of equipment, but managing it does add complexity to the electrical system. Luckily, Lancair provides its customers with a detailed wiring diagram and installation instructions for all of these items. It also provides builders with pre-wired harnesses for most major systems. Some ends need to be attached to connect to certain components, but the wiring harnesses greatly simplify electrical tasks.
The control of the electrical system, the engine sensors and the avionics all come together on the instrument panel, so it makes sense to talk about them at the same time. The instrument panel is another area where Lancair has gone a long way toward making Evolutions look like factory-manufactured airplanes. As we read before, the basic structure of every Evolution is assembled in the factory jigs to ensure a great deal of uniformity across the fleet. The instrument panel is similarly factory pre-wired with little offered to builders in the way of choices. The philosophy is that if they all fly the same and have the same systems, then training can be standardized for the fleet and pilot checkouts can be greatly simplified. This also makes the insurance companies happy.
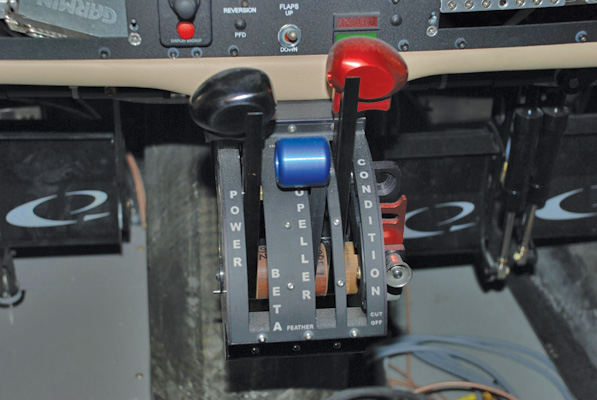
The engine controls look familiar, but on closer examination they are a bit different than what piston drivers are used to. The Power lever controls turbine rpm and thus engine power. It also provides for reverse thrust or beta, in which the pitch of the propeller is changed so that it produces drag or negative thrust to help slow the airplane after landing. The Propeller lever controls propeller rpm, plus feathering. The Condition lever controls fuel to the engine, but does not adjust mixture as it would in a piston airplane.
Big-Screen Glass
The instrument panel houses the Garmin G900X system with added controls to specifically address the needs of the Evolution. The Garmin 900X is the Experimental version of the widely used G1000 system found in so many new certificated airplanes. Autopilot choices are limited to the TruTrak Sorcerer or the Garmin system, which is quite a bit more expensive. The Solesbees chose to go with the TruTrak because of their past success with it in their Lancair IV-P. This is a two-axis unit with vertical and horizontal control including ILS approach capability. For about $8000 it is an impressive autopilot. The yaw damper adds another $2500 or so. The Solesbees also added an Avidyne TCAD traffic system to the basic G900X panel. This is a sophisticated traffic avoidance system that will give them near airline-quality traffic information. A keypad data entry system complements the G900X installation.
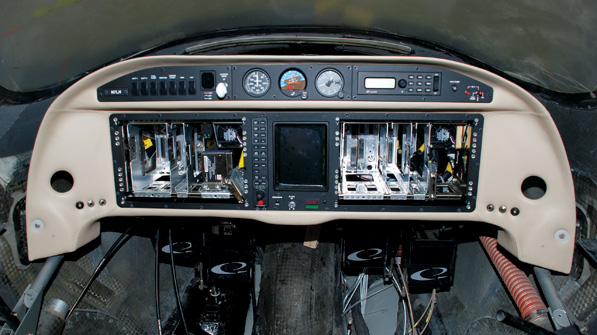
The beautiful Evolution instrument panel doesn’t look as nice stripped of its major components, but the weight savings makes handling much easier and prevents possible damage to the expensive Garmin boxes that will go in later. Cannon plugs that connect to pre-made wiring harnesses make panel installation easier than you might think.
Mercifully, all of this fancy stuff comes in a completely pre-wired instrument panel that simply bolts into place. Several cannon plugs connect the panel to wiring harnesses that make everything work. Wire sizes and routings have already been selected, and wire ends and cannon plugs are already installed in most cases. It is almost a matter of just dropping everything into place. With all that Lancair has provided you really don’t have to know too much about electronics to produce a truly impressive electrical/avionics system.
Antennas are almost an afterthought when avionics come up, but they need some special attention in the Evolution. Most "fast glass" builders are used to concealing antennas inside the fuselage, but with an electrically conductive carbon-fiber structure this is not an option. At 300 knots another thing that is not an option is inexpensive antennas. Nice, sturdy, high quality (expensive) antennas attached to the outside are the order of the day. Again, all of this is included in the kit price, so you hardly notice it.
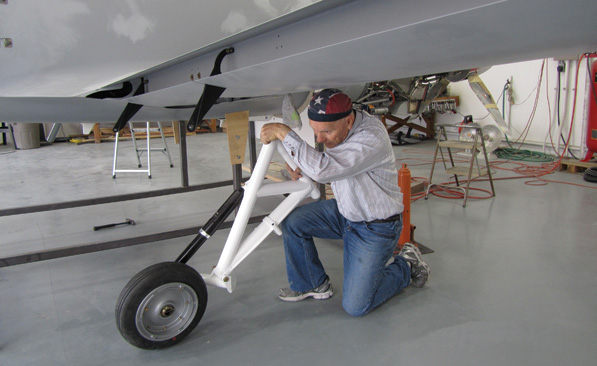
Wendell installs the new, beefed-up steel landing gear provided by Lancair after the original aluminum gear legs proved to be a bit too fragile. Lancair has been very good about providing these upgrades free to early kit builders.
Getting in Gear
The Evolution’s hydraulic gear system is typical of larger airplanes from the certified world. The gear switch activates a hydraulic pump that raises or lowers the substantial landing-gear legs. These legs were originally machined aluminum, but early ground testing proved them to be rather fragile, so they were replaced with heavy-duty welded steel legs that look like they could withstand just about any sort of landing short of a full-on crash. A hydraulic pump and accumulator sit beneath the floor of the baggage compartment where they can easily be accessed for servicing. If the hydraulic pump fails to respond when called, the accumulator may have enough pressure for one gear extension. Otherwise, gravity is the source of power for dropping the landing gear into place for the mains, and a gas pressure cylinder will extend the nose wheel. A little shake of the plane may be needed to lock the maingear into place when the gravity method is employed. There is no hand crank or manual hydraulic pump.
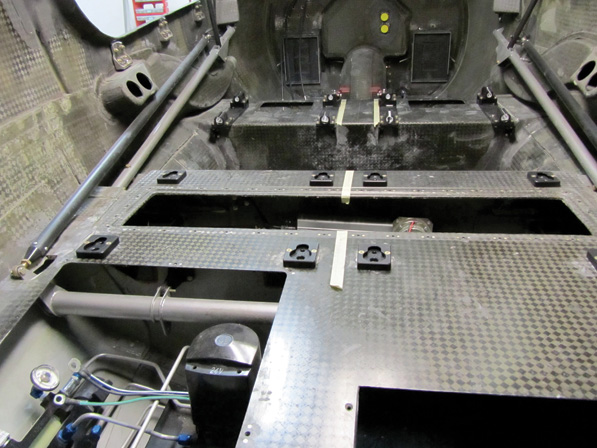
There is a lot happening under the cabin floor of the Evolution. Several access panels cover up the systems underneath. The hydraulic pump for the landing gear can be seen on the lower left.
Flight controls look conventional, and they are. Good old cables run from the stick and rudder pedals to the various surfaces. The autopilot removes the need for rudder and aileron trim, but otherwise everything is as you would expect. The sticks are similar to the side sticks found in other Lancairs and various Cirrus models. They are attached to each side of the fuselage with one for the pilot and one for the copilot. Some Cub drivers may object to the reversal of the throttle and stick hands, but it is really pretty easy to get used to left-hand stick and right-hand throttle. If not, you can just sit in the right seat.
The rudder pedals are fully adjustable, which brings a smile to Martha Solesbee’s face. Being a bit shorter than Wendell, she really appreciates how easy it is to set the pedals in a comfortable position for someone of her height. A convenient hand crank makes pedal adjustment a snap. It is features like this that set the Evolution apart as a first-class airplane.
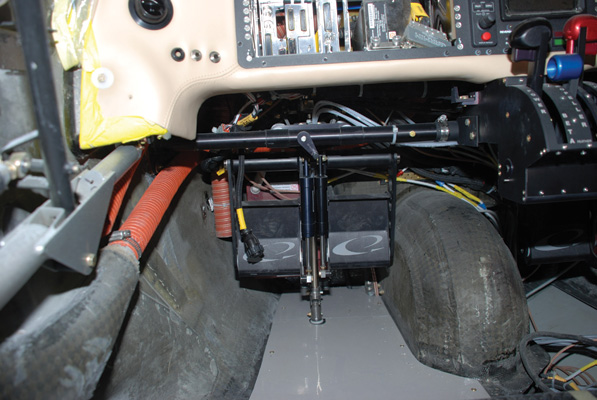
A small hand crank makes adjusting the position of the rudder pedals easy. In a matter of seconds, a taller or shorter pilot can be made comfortable with a few simple adjustments.
Gas and Go
The fuel system is simple except for the added complexity of a return system, which is also found in some piston-engine planes. The tanks are provided by wet wing sections on each side and provide a total of 168 gallons of Jet A to feed the thirsty Pratt. There are no auxiliary wing tanks or center tank to add complexity, so things are pretty straightforward-this is a massive improvement over the turbine-powered Lancair IVs. A duplex Andair fuel valve switches feed lines and return lines simultaneously, so the return line system is transparent to the pilot once the plane has been assembled.
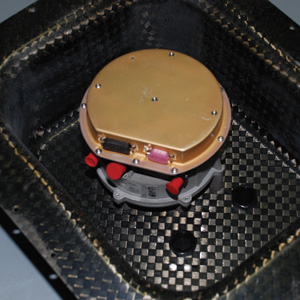
This valve, located in the aft cabin bulkhead, regulates the air pressure in the cabin by venting excess air overboard through the vents in the aft portion of the fuselage. If the pressure was allowed to get too high, it could blow out the windows and door seals; too low and occupants would not get the oxygen they need for high-altitude flight.
The engine controls are at once familiar and not quite so for piston pilots. There is a power lever that looks a lot like a throttle, and in fact acts much like a throttle. It controls engine turbine rpm and thus engine power. The power lever can also reverse the pitch of the propeller to help slow the plane after landing. Next is the propeller control, which also looks familiar, but has the added feature of feathering, something we see in twins but not in piston singles. The propeller control works through a governor on the engine to control propeller speed within a fairly narrow range of 1500 to 1900 rpm. Lastly, we see a lever marked "Condition." It looks like a mixture control, but it isn’t. The condition lever is more of an on/off switch for the engine fuel, with added settings for high idle and low idle for ground operations. The actual fuel metering is handled by an automatic fuel control that is not directly linked to the pilot. These control levers connect to the engine through cables that could come right out of any homebuilt airplane.
A major system that is well-known to Lancair IV-P builders is the cabin comfort and pressurization system. Most of us consider this unfamiliar territory, but to the Solesbees this is ground they have covered before, at least in general terms. The Evolution pressurization system starts at the flow pack, where turbine bleed air is metered and sent to an intercooler to lower its temperature enough so that it won’t melt the parts inside the air conditioning system. This is another component that Lancair foundwanting in its original form, so they sent the Solesbees a redesigned unit that works much better. Even though this caused a delay in the construction process, the free upgrade was most welcome, because it is such a critical component. Did I say free? Yes, Lancair has been good about making needed improvements during the building process at no cost to builders. The redesigned intercooler, just like the gear legs, were provided to kit builders at no extra cost. The company is to be commended.
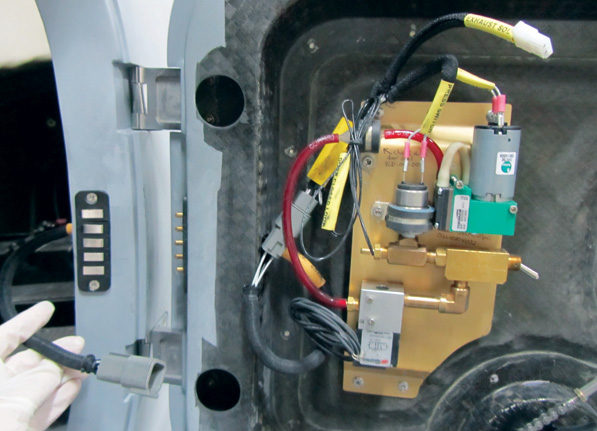
To properly seal each door to an airtight condition, a small pump provides pressurized air to inflate the seal around the door. Electrical contacts in the door jamb allow power to be connected to the pump and controlled from the instrument panel.
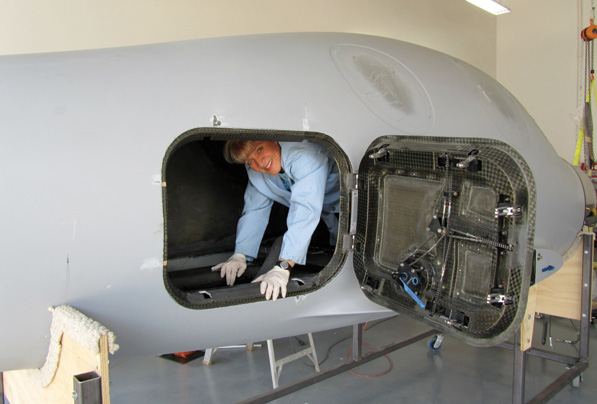
Martha Solesbee glasses in partitions in the cabin floor. These compartments will house various items such as the landing gear hydraulic system, the emergency oxygen system, and a number of electrical components. The complex latch hardware can be seen on the baggage door.
Once past the intercooler, cabin air is cooled by an automotive-style air conditioner with an engine-driven compressor. The condenser is located in the back behind the aft pressure bulkhead and vented outside through two ports in the fuselage. With the bleed air already warm, added heat is unnecessary. Some electrically heated seats round out the cabin comfort package. One thing that goes automatically with pressurization is emergency oxygen. A small bottle provides about 20 minutes of oxygen to four people through masks in case of emergency.
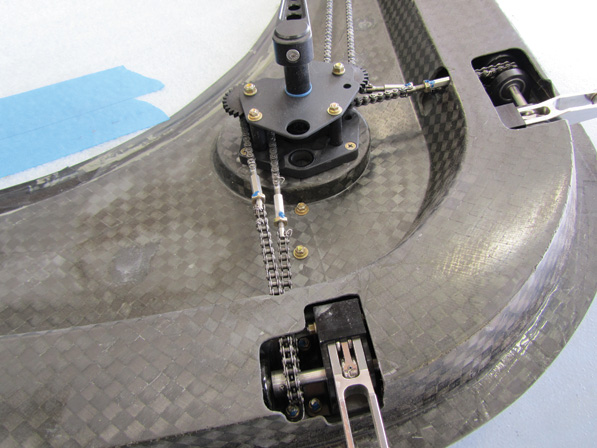
The complexity of the door latch mechanism is a thing to behold. In a pressurized airplane it is vital that each door latches positively and securely. At altitude there is an amazing amount of pressure on each door. Once the upholstery is in place no one will ever see all of this except at annual inspection time.
The Builders’ Perspective
While each system is fairly straightforward and furnished with clear instructions, an airplane with this level of performance has lots of items that need to be attended to, and the major differences between the Evolution and the IV-P have to do with support systems for the turbine engine. The Solesbees started out with little more than their previous experience and a handful of notes to go on-and let’s not mince words: Their experience and craftsmanship on previous homebuilts count for a lot. But by the end Lancair had come through with a large volume of detailed instructions and some important upgrades. There is little doubt that an inexperienced builder would have been lost in the Solesbees’ place, but now they would at least have a fighting chance of making it through to completion.
In all honesty, a fighting chance is not exactly what Lancair promises. Wendell and Martha brought a lot of building experience to this project, which made it possible for them to proceed where a novice builder surely would have been stuck without some serious professional help. What seems to be the case is that a large dose of professional help is needed to fulfill Lancair’s promise to first-time builders, particularly those with a low-serial-number aircraft. We’ll give Lancair its due and say that the manuals and guidance will continue to improve as more builders gain experience and the factory receives feedback from the field.
In the next installment, we will look at finishing the interior and exterior, a topic near and dear to the Solesbees’ hearts owing to their longtime involvement in repairing, painting and customizing cars. In addition, we will look at the little details that are involved in getting from 90% done and 90% to go, which is about where the Solesbees are now, to really ready to fly.
For more information, call 541/923-2244 or visit www.lancair.com.