Angle of attack indicators have been used by the military and airlines for years and have made their way into general aviation as well, especially in the Experimental world. We’ve all read and been taught that AoA should be trusted as the most accurate provider of available lift to the wing during all phases of flight. That means that once it is properly calibrated it doesn’t matter what the G-loading is on the wing. The AoA system will give you a warning prior to the stall, regardless of indicated airspeed.
But what really happens when AoA and airspeed disagree with each other? Can we really force ourselves to trust the AoA system when we’ve been flying via indicated airspeed for most of our flying career? I got to witness this firsthand this past week.
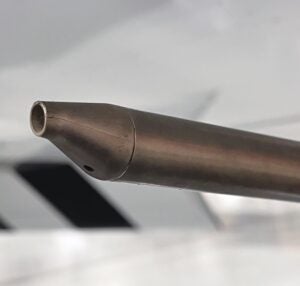
A customer was bringing in his RV-8 for a condition inspection, and he lives close enough that I agreed to fly him back in his RV-8. It’s a gorgeous airplane, very nicely equipped, so I suffered through it. Sure enough, at takeoff the AoA system started yelling at us right about liftoff. I was in the rear seat and tried to look over his shoulder to see the airspeed, and it looked a little high, but RVs accelerate so quickly it was really hard to come to any conclusion. However, he mentioned it had started yelling at him recently, and he did perform a stall at altitude and the airspeed seemed about 10 knots high. On final approach, the AoA system was again yelling, and the pilot was using normal indicated approach speeds. It was a little rough outside due to winds, and the approach felt mushy to me. The landing was not one of his best. (In his words, his worst one all year.) I was convinced it was due to low actual airspeed. I remarked to him that I think he had a static leak.
As I was taxiing out for the return trip, I came up with a plan. RVs accelerate so quickly at takeoff that I usually just make sure the airspeed is alive, and then I really don’t look at it again until I am in the climb attitude. In this case, with 5500 feet of runway ahead of me, I used much less power and slowly accelerated to liftoff speed. There was no doubt that liftoff speed was higher, and the AoA was yelling at me quite early.
Back at the shop I connected the pitot-static tester to the aircraft and it showed a massive leak on the static side, just as I had predicted. It took a while to find it, as it was hidden on the back side of the tee connector in the aft fuselage that went to the static ports. The Nylo-Seal tubing had split where it had been forced over the plastic tee. They should have used a Nylo-Seal tee instead of forcing the tubing, but another possibility is to heat the tubing prior to installing it on the tee. That will usually prevent the cracking.

So, let’s talk about the reason for the disparity between airspeed and AoA. AoA is a measurement between the relative wind and the angle of the wing chord. It can be done using a vane (you can usually see this type on commercial jets) or via a special pitot tube, as in this case. The pitot tube has the normal forward-facing hole and then has another hole below it at a different angle. Then, through fancy algorithms and math, calculations are performed to arrive at the AoA value presented to the pilot. With either method, when the critical angle of attack is approaching, which is usually around 17° for most normal aircraft, a warning is announced. The bottom line is that this measurement is not affected by external forces. By the way, I say “most normal” aircraft as there are military aircraft that due to sheer power are able to break some of the rules regarding angle of attack.
If you remember from your primary flight training, the airspeed indicator is the only instrument that receives both pitot pressure and static pressure. The primary purpose of the static connection is to correct the indicated airspeed for altitude. Simplistically, this means that at higher altitudes there are fewer air molecules striking the pitot tube, so without the correction, the indicated airspeed would be lower. The wing only cares about indicated airspeed. At 1 G, it takes a given amount of air molecules flowing over it at a specific airspeed to create the necessary lift. Add more G’s and it takes more air molecules, hence more airspeed.
So, what happens if we were to decrease the static pressure at a given airspeed? Well, decreasing the static pressure is the same as climbing, so the indicated airspeed would show an increase. This is exactly what was happening with this RV-8. The inside of the aircraft, and especially the aft tail cone area, is at a much lower pressure than the outside air, due to the lift created by the fuselage. The cracked tubing was allowing the static system to sense this lower pressure and correcting the airspeed indication, just as if it was at a higher altitude. So, the result was a higher indicated airspeed.
That brings us back to the first question: Which one should we trust—AoA or indicated airspeed? Personally, I am of the opinion that AoA has a better chance of being right than does the indicated airspeed. At least, that has been my experience across the amateur-built fleet. Most static systems are never checked for leaks unless they are certified for IFR flight. Almost every static system that we check for the first time does have leaks.
One last point here. I get a kick out of how many owners brag about their particular aircraft being so much faster than everyone else’s. Invariably, every single one of them that has come to our shop, especially during the prebuy, has had a static leak. So, if yours seems to be a whole lot faster than the average model, you might want to have the static system checked. I’ll even offer up a poor man’s quick check, with a word to be careful. Set your altimeter to zero, or the nearest thousand feet if you are at too high of an elevation to use zero. Take off and then make a low pass down the runway at 10 feet or so. Take someone with you, or use a GoPro in the cockpit, as you want to be focused outside the aircraft for the low pass. If your altimeter doesn’t read pretty close to your low pass level, then you have a static leak.
Sorry if I’ve busted your bubble on your speedy aircraft, but accurate altimeters are good for low approaches in IMC, and AoA will be your best friend for those short field trips.
I’ve never seen anyone discuss this topic before, and it’s much needed given how common AOA indicators are becoming.
While a vane-type AoA indicator would remain accurate with a static leak, most modern AoA systems rely on measuring static pressure. So a (new) static leak would also introduce errors to the AoA system. More specifically, the AoA is measured based on (L-S)/(P-S), where L,P, and S are the pressures measured at the Lift, Pitot, and Static port locations. P is greater than L, so decreasing S reduces that ratio, indicating a lower AoA than actual. You cannot trust the AoA to save you from from flying the wrong approach speed if the static source is in error.
The altimeter low-pass test is also important for detecting position error in static measurement. By rather than trying to fly fast near the ground, I would suggest flying at a fixed altitude at two different speeds. I use the roofline of my local airport’s tower. It’s a clear visual altitude reference, but 50 feet higher than the runway. If the altitude indicated varies between low-speed and high-speed passes, the S measurement has position errors. That could be from a static leak, or it could mean the static port is not on the ideal location.
Angle of attack tells margin above stall but DO NOT WARN about G load on engine mounts, batteries and fixed items. The wing stalls at 3.8 to 6 Vs at design gross weight. The G load the engine mount doesn’t get stronger at light weight. A Load meter or at least a table showing Va and Checked for lighter operating gross weight.