Every spring, Ronnie Smith of South Mississippi Light Aircraft, brings his wit and considerable Rotax experience to local hosts California Power Systems for a week of Rotax service and maintenance training. Chino Airport, east of Los Angeles, provides an aviation-rich environment for three two-day classes, including two-stroke service and maintenance, 912 service mainly geared towards owners, and a 912 maintenance course focused on mechanics.
The 914 turbocharged engine receives minimal attention, and the new 912 iS fuel-injected engine none at all. A course on the fuel-injected engine is under development and should be available next year. Smith’s approach is generally low-key, but it’s effective and includes a good mix of PowerPoint slides, lecture and hands-on work with the various engines.
Attendees were an eclectic mix from Australia, Trinidad, Mexico and the U.S., with some participants staying for the entire six days and others coming only for selected courses. Interestingly, I was the only Californian in the group, even though the course was held in Southern California. Rotax considers these to be required courses for anyone wishing to maintain a Rotax engine in compliance with LSA rules. After six days of studying and working on these engines, it’s easy to see why. The special tools and techniques required to do the job are well outside the equipment and experience of most A&P mechanics.
Initial certification requires this two-day session with one-day follow-up courses required every two years after that to maintain the certification. These courses are strongly recommended for those working on ELSA and Experimental/Amateur-Built (EAB) aircraft, but the regulations do not allow Rotax to require them. That said, there are plenty of good reasons why any Rotax owner should take at least the basic service course, owing mainly to the many differences between Rotax engines and traditional aircraft engines.

The Rotax 503 engine is an air-cooled two-stroke that can still be found on many ultralights and small Experimental aircraft. It is still supported by Rotax, but no longer available new.
Two-Stroke Engine Training
Classes began with the two-stroke engine course. Even though Rotax only has one model of two-stroke engine still in production, there are thousands of these engines in service around the world, powering a wide assortment of small aircraft of every description imaginable. The reliability of these little powerplants depends on them getting qualified service at regular intervals, and for that, training is a must. The sharpest A&P mechanic with years of experience working on Lycoming and Continental engines is ill-prepared to delve into the innards of these or any other two-stroke engines. They are simply different animals. This course focused in particular on the 503 air-cooled and the 582 liquid-cooled engines. Of these, only the 582 is available new from Rotax, but the 503 is still well-supported and commonly seen in the field.
Reliability dominates the discussion of any two-stroke aircraft engine. The only way to achieve that is with frequent and skilled maintenance. Rotax recommends a teardown and inspection every 150 hours and an overhaul every 300 hours for all their two-stroke engines. The overhaul process includes replacing the crankshaft, bearings, rods, pistons rings, and other parts as needed. Expect to spend about $1,900 on a 503 overhaul and about $2,500 on a 582 overhaul for parts. Mid-time teardown and inspection runs about half that amount. That is a fair bit of money to spend every 300 hours, but keeping your aircraft out of the weeds is pretty valuable, too.

The Rotax 582 is a liquid-cooled two-stroke that is still popular for ultralight and other light aircraft. It is the only two-stroke engine that Rotax still sells new.
The 503 engine is a basic two-stroke design whose concept will be familiar to older motorcycle riders. It is an air-cooled, two-cylinder, piston-port layout with a capacitor-discharge ignition (CDI) system and two spark plugs per cylinder. The single-carburetor version makes 46 horsepower and the dual-carburetor version makes 52 hp. It has a built-in fan to help with cooling, and a small alternator provides limited power for battery charging and accessories. Oil injection comes standard, but many owners prefer to pre-mix their fuel and oil. For those of you who have never experienced the joys of two-stroke ownership, the lubrication for internal engine parts comes from oil that is consumed during the combustion process. This oil can be injected by means of a small pump, or it can be manually mixed in with the fuel. Both ways work, but oil injection is easier to deal with. On the other hand, oil pump failure is a disaster for the engine and will not be obvious until something awful happens, whereas pre-mixed oil is pretty much foolproof.
The 582 engine, the only two-stroke Rotax still sells new, is a two-cylinder, liquid-cooled, rotary-valve design with dual carburetors and dual CDI ignition. The rotary valve adds cost and complexity, but it affords Rotax the opportunity to better control intake timing—something like cam duration in a four-stroke engine. This engine is also slated for termination somewhere in the future. Rotax has not announced a date, but with the pressure for reduced emissions and greater reliability, the days of two-stroke engines are definitely numbered. As of this writing, a new 582 engine sells for $5,382.

Piston problems account for most of the failures in Rotax 2-stroke engines. Most of these problems stem from poor maintenance or operator abuse.
Two-Stroke Troubles
Typical problems seen with two-stroke Rotax engines stem from a failure to comply with recommended maintenance, failure to operate the engine within its limits, and failures related to modifications. Corrosion can also present problems, because the open intake design of these engines easily exposes the crankcase to moisture from ambient air. This can lead to failure of the lower end rod and crankshaft bearings. Failures due to improper operation often take the form of piston failures, especially seizing. It is a good idea to remove the exhaust system and inspect the pistons every 50 hours to monitor any potential developing problems.
Experienced two-stroke operators know that religious adherence to maintenance and operating instructions makes for a reliable engine, and failure to do so will quickly put you in the weeds or worse. This course will teach you how to operate, maintain and repair these engines, which is information that it is going to be difficult to get anywhere else.
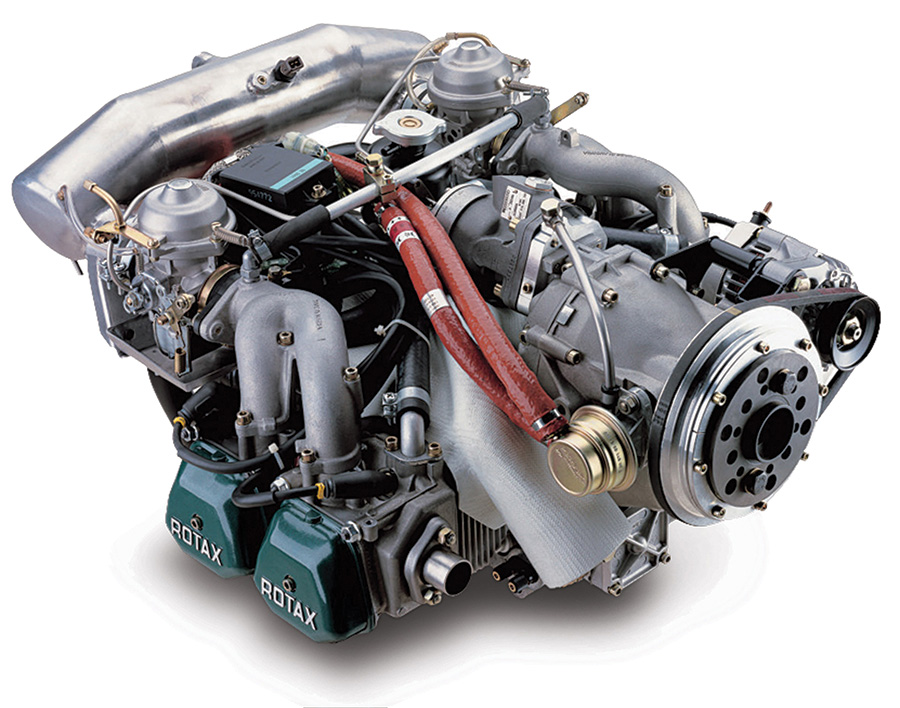
The 912 ULS is the most popular Rotax aircraft engine. It is a four-stroke engine that produces 100 hp and now boasts a 2000-hour TBO. With its light weight and solid reliability, it has come to dominate the LSA field.
Four-Stroke Engine Training
Rotax makes two basic models of their 912 series engines, the 80-hp 912 UL and the larger 100-hp 912 ULS engine, which has an 84 mm bore versus the 79.5 mm bore of the UL engine. A new 80-hp engine sells for $16,710, and the 100-hp engine goes for $18,578. These engines may have other designations depending on certification, but the engines themselves do not change.
The first 912 course focused on operating and servicing these engines, beginning with oil and gasoline. Rotax engines prefer auto gas and allow longer service intervals if auto gas is used at least 70% of the time. The 80-hp engine will run well on 87-octane regular gas, but the 100-hp 912 and the turbocharged 914 require 91-octane premium auto gas. Up to 10% ethanol content is allowed, but higher ethanol content should be avoided. The octane rating of 100LL avgas is more than sufficient, but the lead in avgas causes problems for the Rotax engine over time. Thus 100-hour oil change intervals are approved for engines using auto gas, but 50-hour intervals for avgas and semi-synthetic oil and 25 hours for avgas and synthetic oil are all that is allowed. The magic number is 70%. If you use auto gas at least 70% of the time and limit avgas to 30% or less, you can use the extended 100-hour oil change interval.
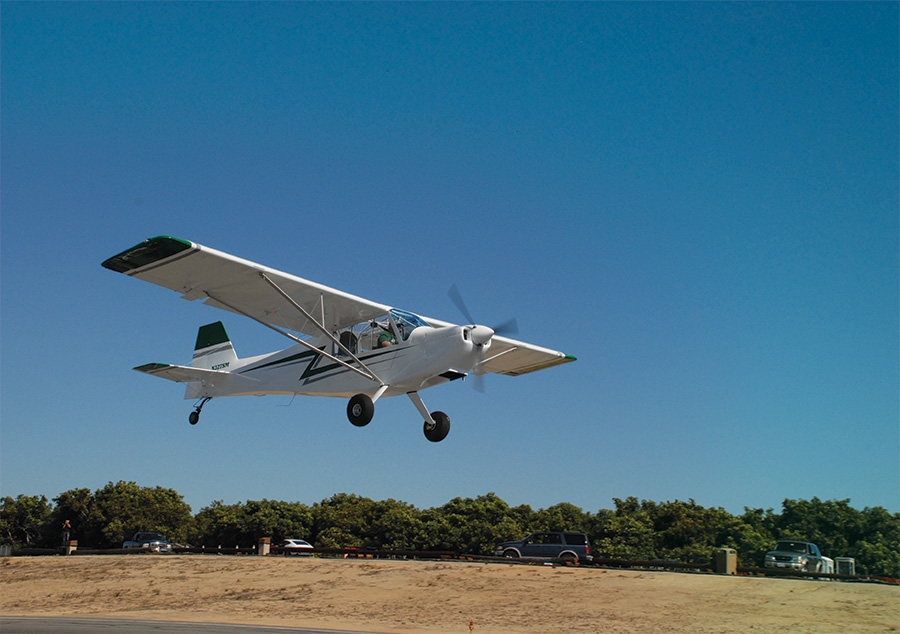
The Rotax 912 ULS engine powers this Experimental/Amateur-Built RANS S-7S and is the first choice of most other RANS builders.
This brings us to oils. Standard aviation oils such as AeroShell 100 are not approved for use in Rotax engines. Shell makes special oils just for Rotax engines—AeroShell Sport PLUS 2 for two-stroke engines and AeroShell Sport PLUS 4 for four-stroke engines. Consult Rotax maintenance publications for other approved oils. There are a number of auto and motorcycle oils that will work, but note the shortened oil change interval with avgas and full synthetic oil.
The 912 oil system has some unique features, the main one being that it is a dry-sump system with a remote oil tank. Crankcase pressure forces oil out of the engine and into the oil tank. The oil pump takes oil from the tank and sends it through the engine, but does not work to remove oil from the crankcase. This is very different from the inverted oil systems found on some aerobatic planes with Lycoming engines. Rotax oil systems are not well-suited for inverted flight or negative-G operations.

Instructor Ronnie Smith demonstrates the differential compression test to the class. Note that he does not attempt to restrain the prop but stands well clear of it.
At each oil change, the Rotax engine needs to be “burped” to be sure all the oil is out of the crankcase. To do so, you merely pull the prop through in its normal direction of rotation until you hear air being pumped into the oil tank, thus the “burp.” At this point, there will be no more oil remaining in the engine. Every 250 hours, the oil tank needs to be cleaned, which breaks the flow of oil to the oil pump. After this process or any other opening up of the oil system, the lifters must be checked to be sure they have not lost their oil and gone flat. The valve covers must be removed and each pushrod must be checked for proper clearance to do this. The clearance between the pushrod end and the rocker arm (valve lash) should not exceed .020 inches.
The gearbox on the 912 series engines needs to come off for inspection at 1000 hours, 600 if you use avgas more than 30% of the time. Gears and bearings get inspected at that time and the clutch breakaway force should be checked. This requires special tools and cannot be done on the airplane. The simpler friction torque test is routinely performed on the airplane using a simple fish scale.

If one Rotax 912 is good, two must be even better. This Air Cam seen at Sun ‘n Fun 2013 stands ready to take its new owner to scenic spots around the globe.
Differential compression testing is similar to the process used on Lycoming and Continental engines, but with a slight Rotax twist. Since there are no visible timing marks to indicate top dead center (TDC), it’s necessary to bring each cylinder up on its compression stroke and then use a straw or piece of wire placed in the spark plug hole to find TDC. Safety demands that you take some care to find the exact top of the compression stroke, because it is quite hazardous to try and hang onto the prop once you put air pressure into the cylinder. In other words, set the engine to TDC for that cylinder, insert the compression tester hose, clear the prop area, and then connect the tester and pressurize the cylinder. If you are not at TDC, the prop will move with a great deal of torque, more than most people can restrain due to the mechanical advantage of the gearbox. Be sure to be out of the way. The standard compression tester with a 0.040-inch orifice works well. Each cylinder should hold at least 75% of the input pressure—60/80 pounds, for example. Note that you will need an adapter with 12 mm threads, not the aviation standard 18 mm threads.

Rotax makes a number of very handy special tools such as this wrist pin extractor. Unfortunately, many of these tools are not just handy, but required to work on various Rotax engines, and they can be rather expensive.
Another maintenance item unfamiliar to most A&P mechanics is synchronizing the carburetors. The Rotax 912 engines (except the 912 iS) have two carburetors that must work together to get the best performance out of the engine. Two automotive vacuum gauges work well for this test, or an old twin-engine manifold pressure gauge would do the job if you can find a good one. The point is that at any particular throttle position, the vacuum reading at each carburetor should be the same. If they are not the throttle linkage needs to be adjusted until they are.
Most all electrical problems with Rotax engines can be tracked down with a high-quality ohmmeter. The maintenance manual lists resistance values between various points in the system. If the resistance is outside the listed range, the component needs to be replaced, or the connection needs to be restored, as the case may be. It is pretty simple, as long as you have a good meter.

Rotax crankshafts are built at the factory using rods that cannot be removed from the crankshaft. This crankshaft comes from a 912 engine.
Unique Features
As the class dug into the inner workings of the engines, some more unique features were uncovered. Rotax engines—including two-strokes—have built-up crankshafts. In other words, the crankshaft is assembled at the factory by pressing parts together using one-piece connecting rods that cannot be removed from the crankshaft. That means that there is no such thing as a field overhaul of a Rotax engine. Even factory-authorized repair stations do not overhaul the bottom end of the motors they rebuild. The entire lower part of the engine comes fully assembled with bearings and connecting rods installed by the factory. The authorized repair facility will then add pistons, cylinders, cylinder heads, and accessories to that factory-new bottom end. This is quite different than what mechanics are used to with Lycoming and Continental engines.

The Rotax 912 CDI ignition is activated by dual triggers for each of its two systems. A fifth trigger coil is used for a signal to the tachometer. The intake for the water pump can be seen at the bottom of the engine.
Before the mysteries of the Rotax crankshaft are even visible, it becomes obvious that the cylinder heads come apart from the cylinders as the engine is disassembled. With Lycoming and Continental engines, the cylinders screw into the heads when they are made and they stay that way forever, barring some catastrophic failure. The advantage of the Rotax construction is that if either part gets damaged or worn out, it can be replaced without replacing the other part. The downside is that there is now one more place for a leak to occur. Leaks between the cylinder and the head are not common, but they can lead to catastrophic failure if not corrected quickly.
More Power, More Dollars
There are limited options for those who wish to extract more power from their Rotax engines. The 100-hp 912 ULS is an obvious upgrade from the 80-hp 912 UL, and the 115-hp turbocharged 914 engine provides another boost, albeit at a fairly steep price of $31,679. The usual tack of increasing compression ratio is not really an option for the 100-hp engine, since compression is already at 11:1 in stock form. Modifications to the cam and heads almost always gain top-end power at the expense of power at lower rpms, yielding power bands that are ill-suited for the needs of most operators. Beyond that, there’s one more option. The 912 engine can be turbocharged with a kit made by Bully Dog. Using Rotax 914 parts with some modifications on the 912 ULS engine produces 130 hp in a pretty reliable and mostly-stock package. The upgrade cost for this modification is $16,500 if you already have a good 912 ULS engine, or $34,500 for a complete new engine. South Mississippi Light Aircraft performs this modification quite often, but only for Experimental owners.

The Rotax 914 UL engine is a turbocharged version of the 80-hp 912 UL engine. It produces 115 hp. Turbocharging is a great benefit to operators who work out of high-altitude airports, but it comes at a significant added cost.
Good Records Are a Part of Good Maintenance
One last point that Smith made was that it’s important to keep good maintenance records in an engine logbook. This will help you keep track of what you have done and will be invaluable when you go to sell your airplane. It will also help to keep your engine warranty in effect. In addition to any major engine work, you should log routine maintenance such as oil changes and oil type used, oil tank cleaning, compression tests, friction pull tests, and carburetor synchronization. A long and steady record of routine maintenance tells a prospective buyer that you took good care of your engine.
Get Trained to Get the Skills You Need
On a personal note, I have worked on Lycoming and Jabiru engines and taken factory training for both. Even though I have a fair bit of experience working on auto engines and motorcycle engines, I found the factory-approved training courses invaluable, teaching me things that I could immediately apply to the engines I was working on. The Rotax training courses I attended would be equally valuable, even indispensable, to anyone who owned or maintained a Rotax engine. If you own and maintain a two-stroke Rotax engine, you need to take the two-stroke course. If you own and only do simple things like oil changes on your four-stroke Rotax, you should at least take the service course. And, of course, if you do serious maintenance on 912 engines, you have no excuse for not taking the maintenance course the next time it is available.
Each course costs $500 for the two days. One-day renewal courses cost $250 each. In addition, there’s a heavy maintenance course that costs $650 and delves more deeply into gearbox maintenance and repairs, something only lightly covered in the regular maintenance course. Contact California Power Systems for their schedule of upcoming courses.

There was plenty of opportunity for hands-on work in these engine classes. This father/son team from Trinidad was there to learn everything they could about Rotax engines and stayed for the entire week.
Hello,
Are you able to hold a class and have any scheduled yet?