Last month I promised to talk about CNC at home, but I’m going to delay that a bit—not because CNC is too expensive. Truth is, there are so many affordable choices on the market that I’m still researching it. Some of the manufacturers went so far as to ask me to hold off until they finish testing their latest versions. Soon…I promise!
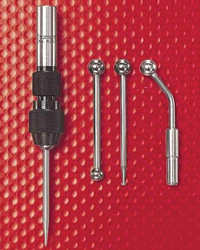
The wiggler set comes with four probes for different edge configurations. The spherical top of each probe fits within the housing.
For now, let’s take it to the edge. Where is the edge? If, up to now, all you’ve done is scribe a target and eyeball the position of the drill bit, this is for you. Now we’re going to get accurate—no more whittling. Don’t think this is overkill; it’s not. Starting from a precisely known point is step one on the road to more complex projects and to making your work a thing of real beauty.
Let’s start with the oldest way of finding the side of your material. It’s really simple: You take a cut and reset all the dials to zero. Duh! But that is not finding the side so much as creating it, and that’s fine for some projects. What if we have to do it without cutting the material? Or what if we are working on an existing part? You could just put a dial indicator in the spindle and…no, wait a minute. That won’t work. All that will tell you is that the dial indicator has touched the material.
It’s possible to find the surface of the material without buying a new tool (Darn!), and it’s accurate. Go get your micrometer and measure the cover of this magazine; it’s 0.0035 inch, right? Now measure the inside pages…0.002 inch. Bingo! You now have a supply of disposable [What?—Ed.] thickness gauges. Come to think of it, maybe you should use someone else’s magazine.
Anyway, you get the idea. Just insert a strip of any paper of any known thickness between the tool and the material without the machine running. Keep the paper moving as you gently crank the handwheel, and when you feel a drag that does not tear the paper, you’re that far away from the surface. Just set the dial to read that distance. Easy and cheap, no?
Remember, though, that the dials have to be cranked backward one full turn prior to approaching the material. This is to take all the slack out of the system. If you go too far and tear the paper, back out a full turn and try again.
Different papers have dramatically different thicknesses as well as tensile strengths, but the technique works beautifully to get you close. If you’re old enough to remember the Haight-Ashbury, make-love-not-war and psychedelically painted VW buses, you’ll also remember Zig-Zag papers. They’re still available, and they work nicely for this technique because they’re thin and pretty strong when wet. That’s the problem with the process; paper only works when the parts are dry. A minor variant on this is to use aluminum foil. It has a nicely consistent thickness, but it won’t tear as easily, so I put a notch in the edge to facilitate tearing if you get too close.
If you have a set of feeler gauges left over from the days when a tune-up on your car involved adjusting the valves—this is really making me feel ancient!— you’ll find that they work well, too. If you do remember those days, you’ll also remember wondering how hard a pull was needed; that is, the gauge was between the rocker arm and the end of the valve stem. You tightened a bit on the adjuster to reduce the gap and moved the feeler gauge. But these are well oiled, very smooth surfaces, so the gauge would move even though the adjuster was too tight.
I looked it up once within the texts of the American Society of Mechanical Engineers and found that they had established a standard value of 3 pounds of pull. That’s pretty light and relies upon your sense of force, but it does give you some idea and will certainly get you close even if you miss it by 100%.
Not Quite High Tech
Another way of finding the side wall of the material is to use an edge finder. There are several versions, but let’s start with the mechanical type that’s been around since Noah was taking wood shop. This is a totally non-intuitive gadget that’s slightly more complex than a brick but works amazingly well.
Take a precision-ground, hollow, 3-inch-long cylinder and part-off half an inch of it. Now put a spring inside the two pieces to hold them together. Put the long end in the spindle and turn on the rotation to about 1000 rpm. Position the Z axis so that the dividing line between the two pieces is above the surface of the material and advance it to the material. The short end is wobbling like crazy, because with only a spring to hold it, it’s anything but concentric to the long end. As you get closer, the short end contacts the material, and the wobble decreases as you would expect. What you don’t expect, however, is that the instant the short end passes being concentric to the upper end, it jumps sideways.
If the small end of the edge finder is 0.200 inch in diameter, then when it jumps sideways, you’re 0.100 from the centerline of the spindle to the edge of the material. Reset the dials to that value, put in your drill, and go to the spot. Remember that if you’re doing some milling, you’ll need to select the end mill and reset the dials appropriately with the diameter of the tool in mind. It’s a surprise the first time you see this, and it’s one of those tricks that’s fun to do when a non-machinist is watching. (To see this in action go to www.tormach.com/mfg_database.htm. You’ll also find several great videos on machining.)
There’s also a high-tech version of the edge finder that uses an LED inside the body of the upper cylinder. Instead of kicking the lower end sideways, it simply lights up the LED. It’s “trick” but not my favorite because it won’t work on non-conducting materials.
Another trick tool is the wiggler. If you thought the edge finder was something to send you back to your physics class, this will really give you a buzz. The wiggler consists of a cylindrical housing with a 2-inch needle protruding from the bottom. You put the housing into the collet or chuck and turn it on to about 1000 rpm.
The needle is being held within the housing by a spherical ball, so it wiggles like mad; your next job is to take a pencil and push the needle to center it. Now move the needle to the edge of the material, and with it still turning, touch the needle to the edge of the part; it will kick sideways just as the edge finder did.
But Where’s the Top?
Having found the side wall of the material, how do you know exactly where the top of it is? Again, you could simply cut the surface and set the dials. In fact, this is sometimes a preferred technique in that it ensures that the surface is normal to the axis of the spindle. Normal? The first time I heard that term in this context I thought, “You mean it was abnormal before?” What that means in geometry is that the surface or line being discussed is perpendicular to a designated axis.
Again, if cutting the material is not an option you can resort to the paper method. With just a little practice this can consistently get you within 0.001 inch of the surface. If you chew gum you might want to keep that foil wrapper, as it’s also a cheap and easy tool. Just don’t forget to remove the gum.
A more elegant technique is to roll a drill bit across the surface of the material as you bring the end mill down. Oh, and this is done with all power turned off. Forget to do this and that drill bit will take off across the shop with a decided verve and alacrity. Also, examine the drill bit carefully before doing this; if it’s been spun in the drill chuck, it probably has a burr, or it might be one whose shank is a different diameter than the size of hole it will drill. I’d also suggest you use something like a 0.250-inch bit if for no other reason than the arithmetic is easier than if you select a 29/64-inch bit. Of course, this assumes you have a flat surface large enough to allow the drill bit to be rolled around.
The paper technique will also work well for your lathe projects. Just put the paper between the material and the cutting tool, and crank in on the Y axis as you move the paper. This is more difficult in that you’re trapping the paper between the point of the tool bit and the line of the curved surface you’re machining, so it tends to go from clearing to tearing quickly.
Find a Drilling Position
If you tried the wiggler and, yes, that’s what it’s called in the parts books, you noticed it’s spot-on stable when it’s centered. That means it’s pointing straight down the axis of the spindle, so you can now reposition that punch mark on your material accurately. The drawback here is that if you touch it, it’s no longer on-axis. That’s not a big deal; just spin it up to speed and re-center it.
A far more techie technique is a laser-based device. Where the wiggler, edge finder, paper and chewing gum wrappers are all made by anyone who cares to, this is from a single manufacturer, SDA. It’s simple enough. A tightly collimated laser beam is mounted in a housing that can be held in a chuck or collet. It points straight down, and you turn a knob that rotates a polarizing lens until the beam is as tight as you like.
The first time you use it you should check the calibration by turning the spindle by hand; if the dot moves in a little circle, you use the included Allen wrench to zero it.
One thing SDA forgot to mention is that you should check this calibration at two heights. If your chuck is holding the device both off axis and parallel to the axis, you’ll get one circle at any height; this indicates that you need to calibrate the laser. But if your chuck is not parallel to the axis, your laser beam will be scribing a cone. You can determine this by adjusting the beam to a point and then moving the Z axis and checking to see if it’s still a point. If it’s now a circle, you have a problem with the chuck. You can find this laser at www.lasercenteredgefinder.com.
Get Dialed In
There’s something spooky about wigglers, though, and a laser won’t get you to the center of an existing hole. Now is when the dial indicator mounted in the spindle comes into play. Mount a finger-type indicator in the spindle and eyeball-center it over the hole. Move in the –Z direction to put the finger in the hole, and then move the finger (not the spindle) until it touches the hole. Now swing the spindle, and move the X axis until you get the same reading on opposite sides.
Repeat this for the Y axis until you can swing the spindle 360° with minimum deflection of the dial. You can ignore that small vibration of the needle as you rotate the spindle; just let it stop at the four cardinal points and fine-tune it until it’s good enough for your requirements.
I’ll make the point again here that you are the customer. If all you’re doing is making a clearance bore for a socket wrench, getting it within 0.005 inch is good enough. Back when James Watt built the first really good steam engine in 1769, they were working to 0.100 inch and calling it fine. We can easily move that over two decimal places now, and even three places is not unusual. But is it necessary? A brick made to 0.001 inch is just a more expensive brick. Keep that in mind as you build any project.
The Mold-Maker Method
My friend Bob Grosse showed me a cute technique he learned over 30 years of making molds. Instead of just finding the edge, he starts from the center of the material. His dial indicator is mounted on a device that clamps directly to the spindle; as such, he can swing the indicator in a large circle. With it extended to put it close to the surface, he then eyeballs the material to center under the spindle axis. He brings the indicator down to touch an edge, zeros it and then raises it. Rotate to the opposite side, take a reading, then move half of the offset. Bingo! He’s centered. Repeat that for the other axis, and the material is now dead center under the spindle.
The final step is move the material to a chosen zero-zero, X-Y position, which is simple enough. Just divide the longest dimensions by two and move it by that amount. I was looking over his shoulder when he did this and was initially intrigued. A couple of weeks later I was trying to figure out the advantage of this method and got nowhere, so I asked about it. “That’s the way I was taught as a mold maker,” Grosse explained. “I’m used to it, so it’s much quicker than using an edge finder.” Ah, well. I like to put my socks on first, and then my pants. The only disadvantage I could see is that the material size is limited to the size of the swing of the tool that holds the dial indicator.
Consider a Catalog
Some years ago I bought a right-angle extension for my air drill. It came with a half dozen drill bits, each sized for rivets. They’re a bit unusual (pun intended) in that one end is threaded; you use a wrench to install them. And then I broke one. Surprise…Home Depot does not carry them. But I found a source that does. You tool-and-die makers have been keeping this a secret, but I’m going to violate the code of omerta and inform readers about MSC tools, a mail-order company with the biggest catalog I’ve ever seen, at 4400 pages.
In looking for drill bits I found the usual jobber length such as sold at the corner hardware store, but I also found sizes down 0.035 inch, and 24-inch extensions for when you need to get way down there or don’t have clearance for the drill motor. In fact, there are 300 pages of drill bits! Check the web site at www.MSCdirect.com.
With some luck, next month I’ll be showing you how you can make parts for your own airplane that 30 years ago would have been impossible, even for the Skunk Works.
Editor’s note: If you have specific questions for author Bob Fritz, or if you have certain projects you’d like us to cover, email us at [email protected] with “Home Machinist” in the subject line.