For the first few years after completing my Van’s RV-10, hangar entry and egress at my municipal hangar was nice and flat and relatively easy to accomplish with just a manual tow bar. The only obstacle at the hangar was the sliding door tracks, which are just inverted angle iron mounted to the floor. They took a little grunt and momentum to traverse, especially with significant fuel aboard, but overall, it was a manageable situation.
When we built the airpark hangar, the terrain necessitated a slight slope from the taxiway to the hangar floor. My first attempt with the Bogert manual tow bar was (barely) successful. But that struggle and the nightmares of a runaway airplane careening down a wooded ravine were enough for me to realize that the time had come to mechanize the towing process.
A search of the forums and markets for ideas highlighted several attractive choices. I was particularly looking for lower cost and portability so those goals eventually landed me at the Minimax powered tow bar. From my observation, the Minimax team design philosophy has a distinctive tinkerer flavor that might be appreciated by a lot of Experimental/Amateur-Built types. In an attempt to fulfill a need, they’ve cleverly taken some off-the-shelf components—a small industrial gearbox and high-powered portable drill motors—and joined them with a custom driveshaft to make their base drivetrain. From there, they engineered a variety of attachment apparatuses to apply to myriad aircraft types and models. They’ll even sell you the core assembly and allow you to custom design your own connection rig to your aircraft.
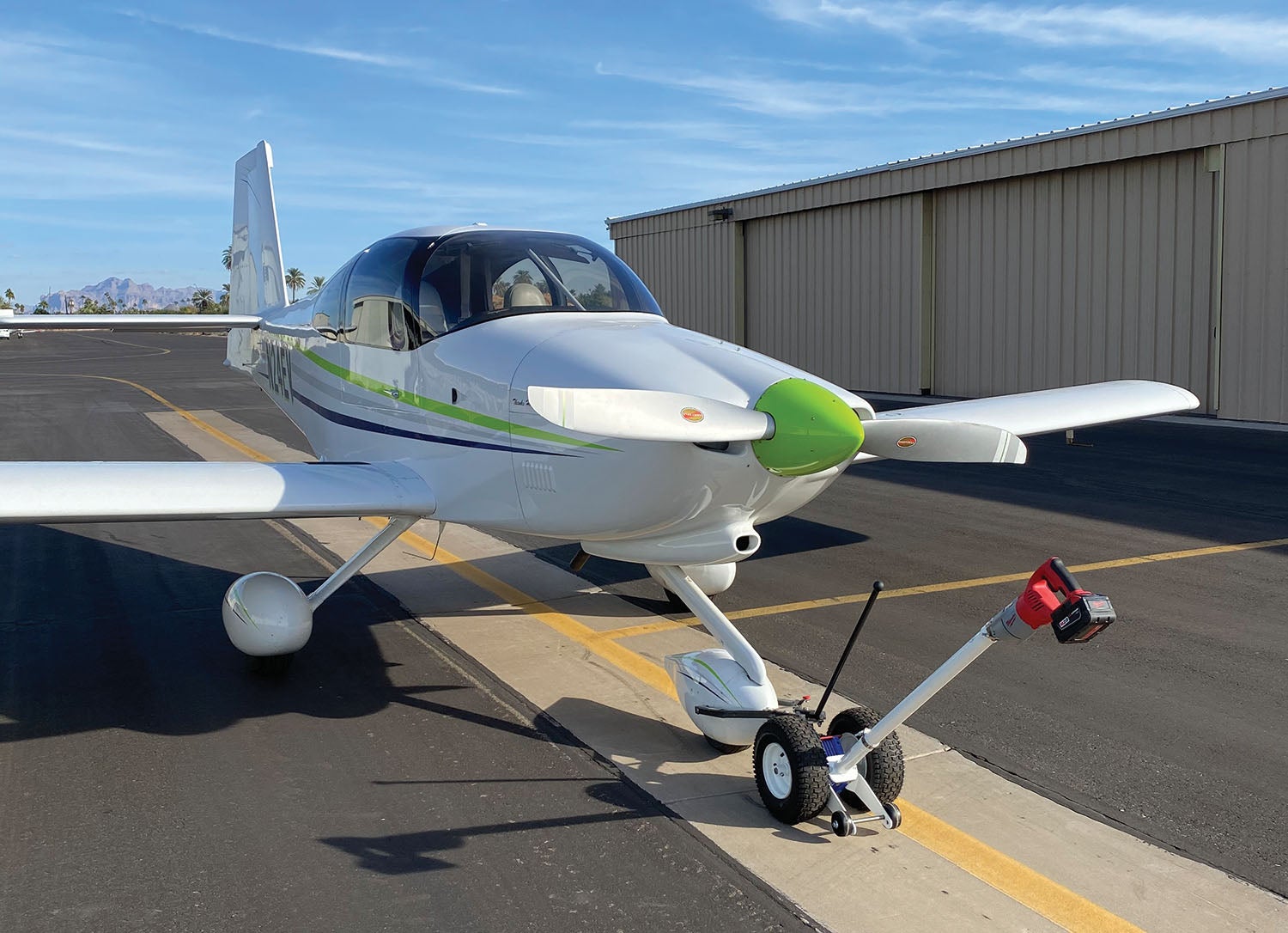
Give It a Try
I ordered their RV-10 version with the Milwaukee 28-volt drive motor. I will describe the drive motors in more detail further down. Once fully assembled, the entire assembly can be easily broken down into a couple of pieces that fit easily in my RV-10 baggage compartment. I still prefer the basic Bogert tow bar for carrying onboard, however.
Minimax lists the maximum aircraft weight limit at 4000 pounds. My airplane with average fuel is about half that, and the tug has had no trouble negotiating the slope at my airpark hangar either pulled in or pushed in (recommended).
My first use made me a satisfied customer but did highlight a couple of shortcomings. No doubt due to cost and simplicity constraints, the gearbox is a simple direct-drive design instead of limited-slip—the drive wheels are locked together in rotation. That means the
system doesn’t turn well beyond just a few degrees. What you do to turn is to either scuff the tires sideways a bit or raise the wheels off the ground and manually maneuver the nose (or tail) to the position you need and then lower the wheels to drive. It gets easier with practice.
This steering technique makes the Minimax more of a power-assisted tow bar than a full-on tug, which the company readily admits. It’s fine, as simplicity and lower costs are valuable in their own right.
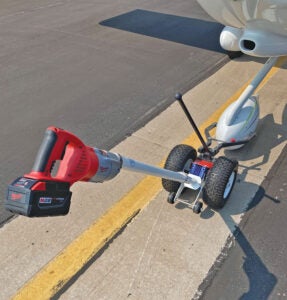
Park It
The simple gearbox has no neutral setting, which from a safety factor is probably a good thing. It only becomes an issue when the aircraft reposition is complete and you want to store the tug back in its spot. The comfortable speed at which it moves aircraft can seem painfully slow while you’re “driving” the tug back to its storage spot. The good news is that Minimax has developed an attachment they call the Speedy Mover, a set of supplementary wheels on the base that ride above the pavement in the towing mode. But lower the bar’s angle until the auxiliary wheels make contact, and you can raise the main wheels to pull or push the entire assembly easily. This is a must-have to complete the package.
Unfortunately, what I found with my RV-10 setup geometry was that the auxiliary wheels were too close to the ground so that the pressing action on the handle—needed for wheel traction—was limited by the mover wheels. Since the mover wheels’ legs bolt directly to existing threaded holes on the gearbox, there is no possibility of adjustment there. I drilled new holes for the mover wheel axle and moved its position slightly aft (toward the drive axle) and slightly higher. Now my assembly allows me full traction leverage on the main wheels, yet retains the function of the mover wheels.
After a year or so of using the Minimax at the airpark hangar, I came to appreciate it more and more, and came to miss its presence at the home hangar. In a weak moment, I may have cheekily mentioned to my wife a few weeks before my birthday how nice it would be to have one at each hangar. Always quick on the uptake, my dear wife took the hint and ordered one. When she did, she merely stated, “exactly as we had ordered before.” However, due to a shipment error, we actually received the DeWalt drive version when we had ordered the Milwaukee drive previously. From a journalistic standpoint, this gave me a chance to compare both drive types and declare a winner (for me). Call it a fortunate mistake.
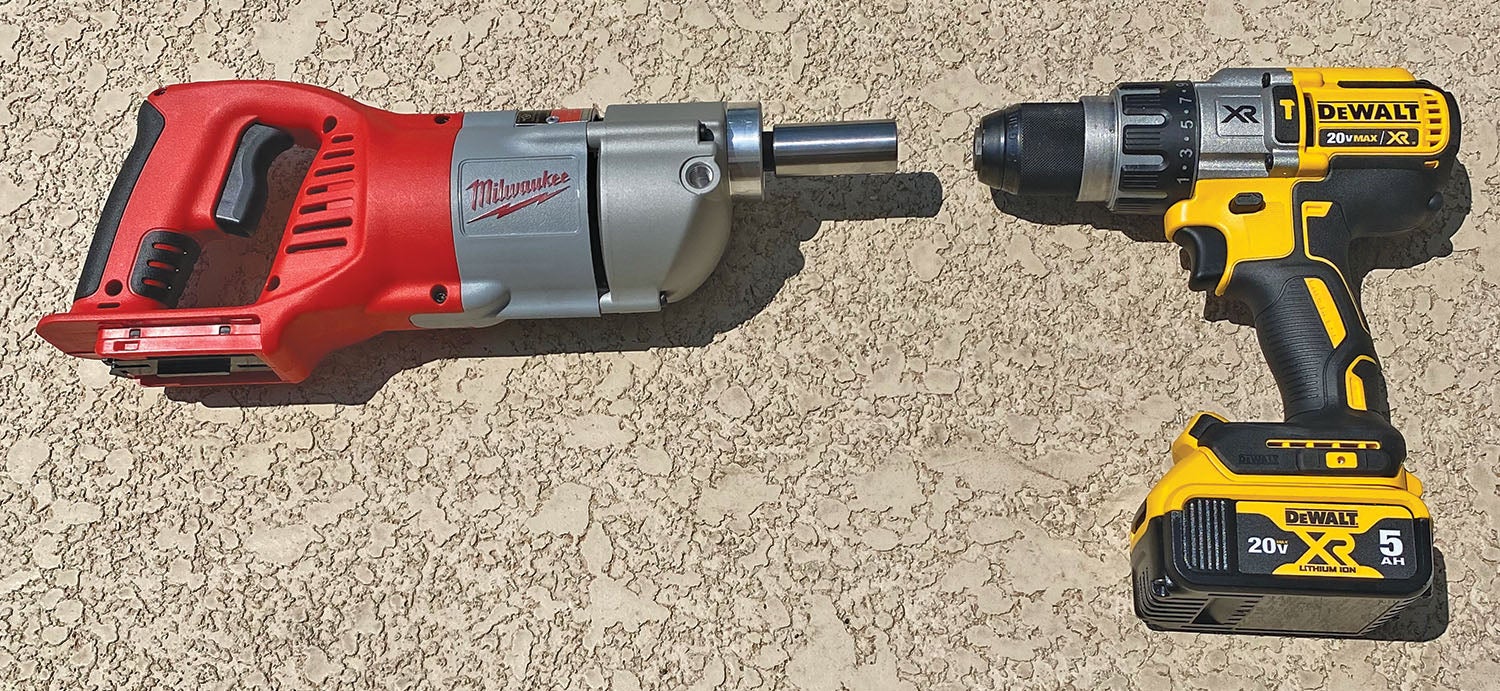
Who Wins, Then?
When I received the second unit, it didn’t have the optional Speedy Mover aux wheel assembly, so the first thing I did was call to order one. While I had the rep on the phone, I mentioned that I had to modify my original set because the legs were too long to work perfectly with my RV-10. The rep mentioned that this was a known problem in some applications and that they now had a second option with shorter legs available, so that was what I ordered.
The good news was that the wheels’ position was nice and high to allow pressure onto the main wheels for traction, but unfortunately they were now too high for everything else. Using the wheels to reposition the tow bar after use required an uncomfortable stoop to position the handle low enough to raise the main wheels off the surface. Also, when parked, the wheels were too high (legs now too short) to support the assembly upright, and it must be fully laid down onto the handle when idle. The solution for me will be to exchange the assembly for the longer-legged version and then drill new axle holes in the perfect position of my first set.
Back to the drive comparison. Both the DeWalt and the Milwaukee power units are top quality, but are also quite different. The DeWalt’s biggest advantage is that it comes with a keyless chuck used for its attachment to the Minimax. With the DeWalt, if you need or want to use the unit as a drill, you can do so by releasing the outer clamp on the handle tube, releasing the chuck and separating the drive motor from the Minimax.
The Milwaukee unit is different. It started life as a high-power angle drive, but its original angle-gear assembly and chuck have been removed. It connects to the Minimax handle tube driveshaft by set screws and Loctite. It would not be easy to separate, and even if one did, absent a chuck, would not be useful for much other than driving a Minimax. To its credit, however, the Milwaukee is decidedly more powerful than its stablemate. Its rear handle design also, in my opinion, makes it much more ergonomically friendly than the pistol-grip DeWalt. It even makes the entire “handle” of the Minimax longer, which is an advantage. It just seems more purpose-built for the Minimax aircraft maneuvering purpose than the “cobbled together” impression of the DeWalt.
Both the 28-volt Milwaukee and the 20-volt DeWalt are high-quality, high-power drive units. Both can move a 2000-pound aircraft with ease when combined with the rest of the Minimax setup. If I had an aircraft lighter than an RV-10 and no slope to negotiate, I’d order the DeWalt for its flexibility of use. However, after using both, for my needs, I’ll take the Milwaukee version—it’s the ideal solution.
My hangar also has a slope in front,, so it’s quite difficult for me to push my Cessna uphill, [ at 1770 lb], and then over the door tracks.
So, my solution cost me $160. I bought a $60 winch with remote control from Harbor Freight, a small battery and a charger.
I bolted the winch at the back floor of the hangar. I then pull the cable out and connect to the tail tie down hook.
Then with the remote in hand, I steer the aircraft with the tow bar…..easy, no sweat.! …and 1/10th the cost of a tugger.