“Don’t print this—the perfect fit of the luggage door was an accident. The RV-10 luggage door doesn’t fit well from the factory. Trace was applying pressure to it and it bent. When he put it in place, it fit perfectly.”
What compels some people to reveal their invisible errors while showing off their superb craftsmanship? Whatever it is, Eric Abraham has it. But then he and his building partner, Trace Blakely, also have the Kitbuilt Reserve Grand Champion (Silver) Lindy from AirVenture 2023 for their Van’s RV-10, the one whose minor imperfections Eric was pointing out. “We built it to get it done, not to win an award.” That said, the RV-10 was not their first trip to the AirVenture homebuilt awards stage. In 2021 Trace was presented an Outstanding Workmanship plaque for his RV-7, which Eric helped build. “When the RV-7 was inspected,” said Eric, “the DAR told us, ‘You should show this at Oshkosh.’ We were like, ‘Really?’ We didn’t know anything about that.” They do now.
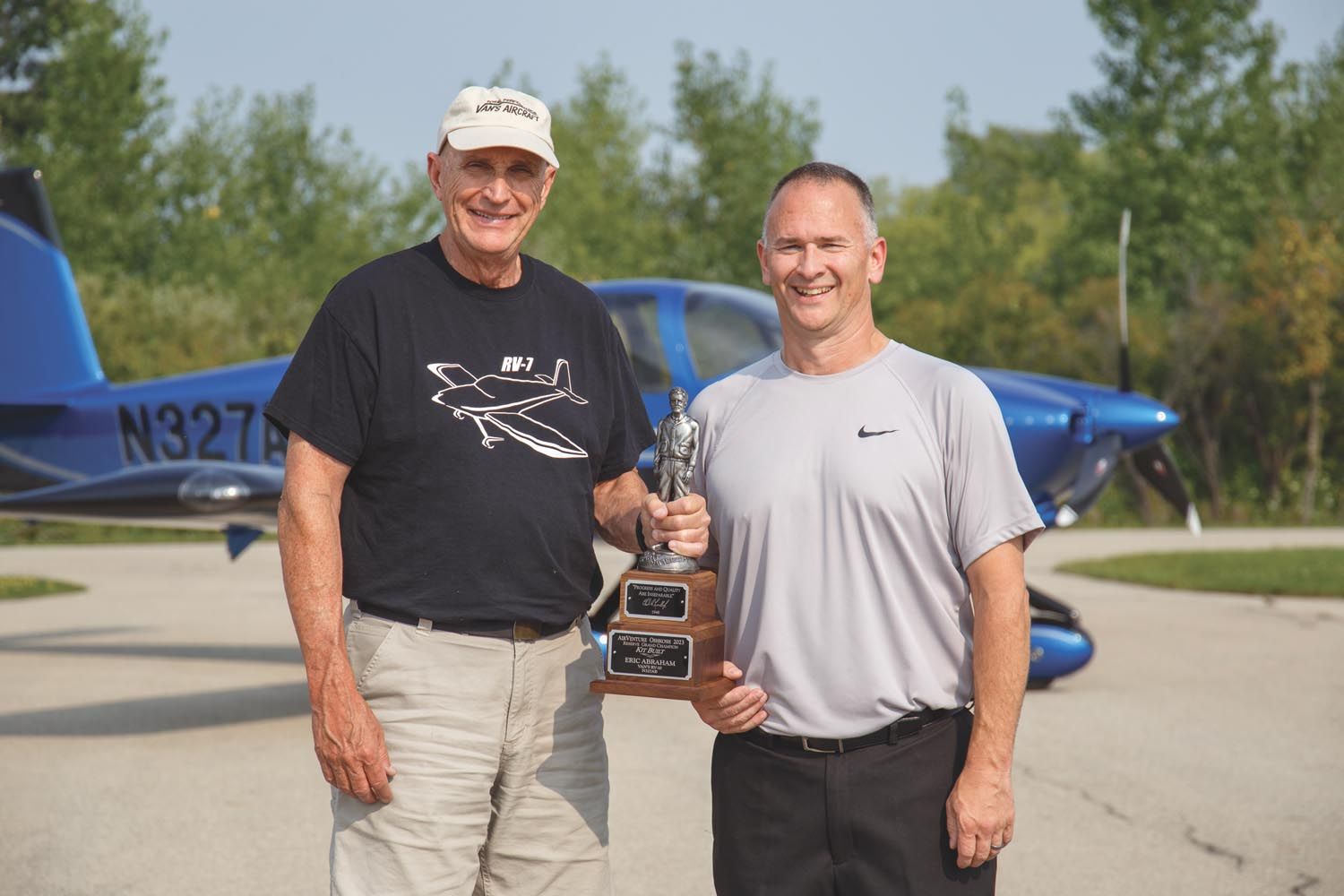
The Partners
The seeds of Trace Blakely’s aviation interest are rooted in homebuilding. His father owned a machine shop that built engines for air racing legend and aircraft designer Steve Wittman. Trace’s first airplane ride came at age eight, in 1964, in a Wittman Tailwind built by Arden Hjelle (pronounced “jell-e”). “When we received our Silver Lindy we were standing under a photo of Arden’s Tailwind, taken in 1970, when he was awarded EAA’s first Homebuilt Grand Champion.” (For details see KITPLANES July 2015 issue.)
Trace credits his father Don, Steve Wittman and Wittman associate Tom Meiklejohn for inspiring his aviation passion. A 3000-hour pilot with instrument, seaplane and mutli-engine ratings, Trace sold his Twin Comanche and now flies only Experimental aircraft. Prior to the Comanche, Trace restored a 1946 Ercoupe, which he sold to build the RV-7.
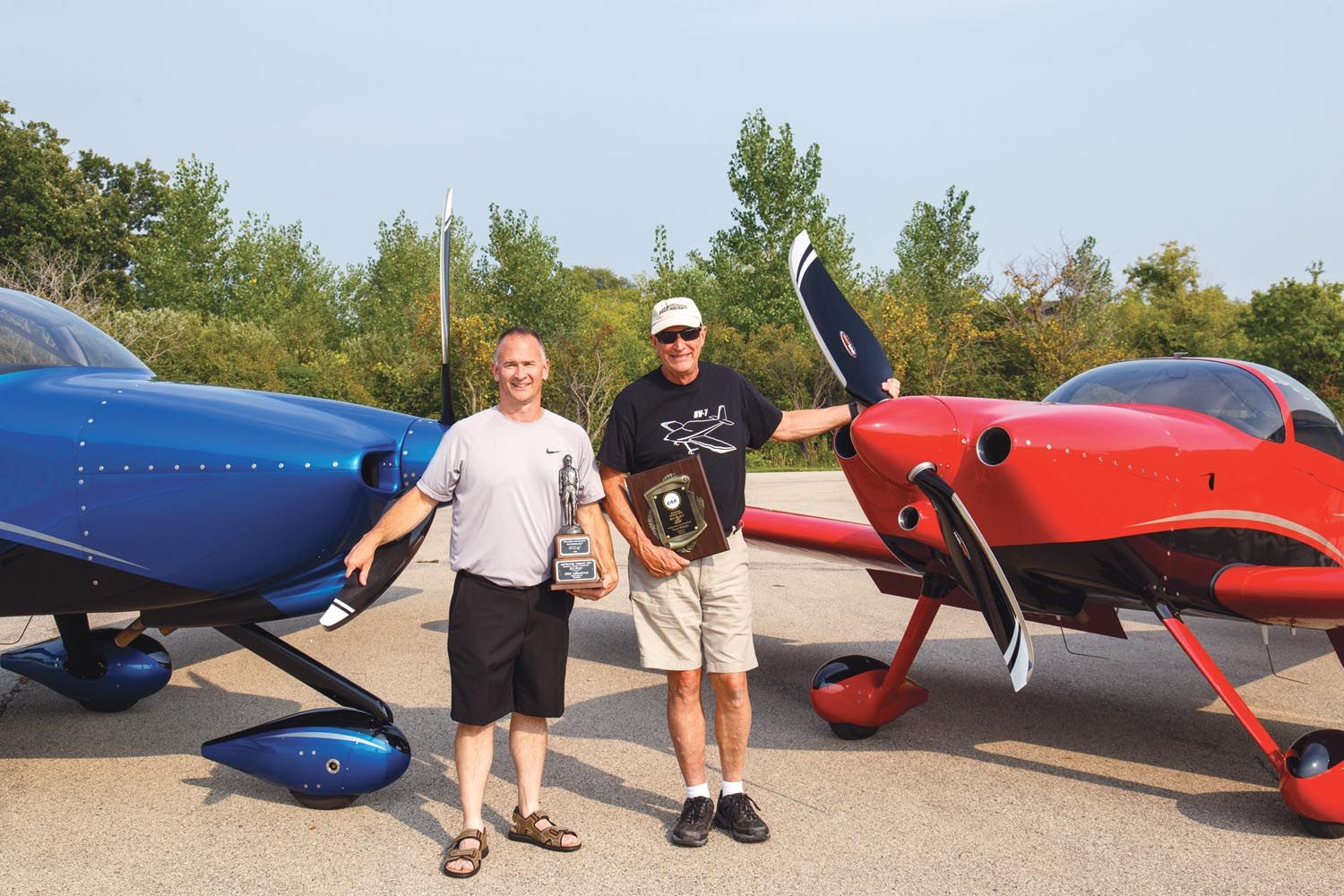
Eric Abraham was a private pilot when he poked his head in on an EAA Chapter 252 meeting in Oshkosh “to see what [homebuilding] was all about.” Clearly, he liked what he found. Eric, now a multi-engine-rated flight instructor, is also the lead volunteer for EAA Chapter 252’s Teen Build program, guiding teens through the construction of an RV-12. His first hands-on homebuilding experience was helping a coworker wire an RV-7A. He then jumped in on Trace’s RV-7 project and lent a hand with final assembly, wiring and painting. With that project done, and before their workmanship was judged exceptional at AirVenture 2021, Trace asked Eric, “What are we going to do now? We have all of these tools.”
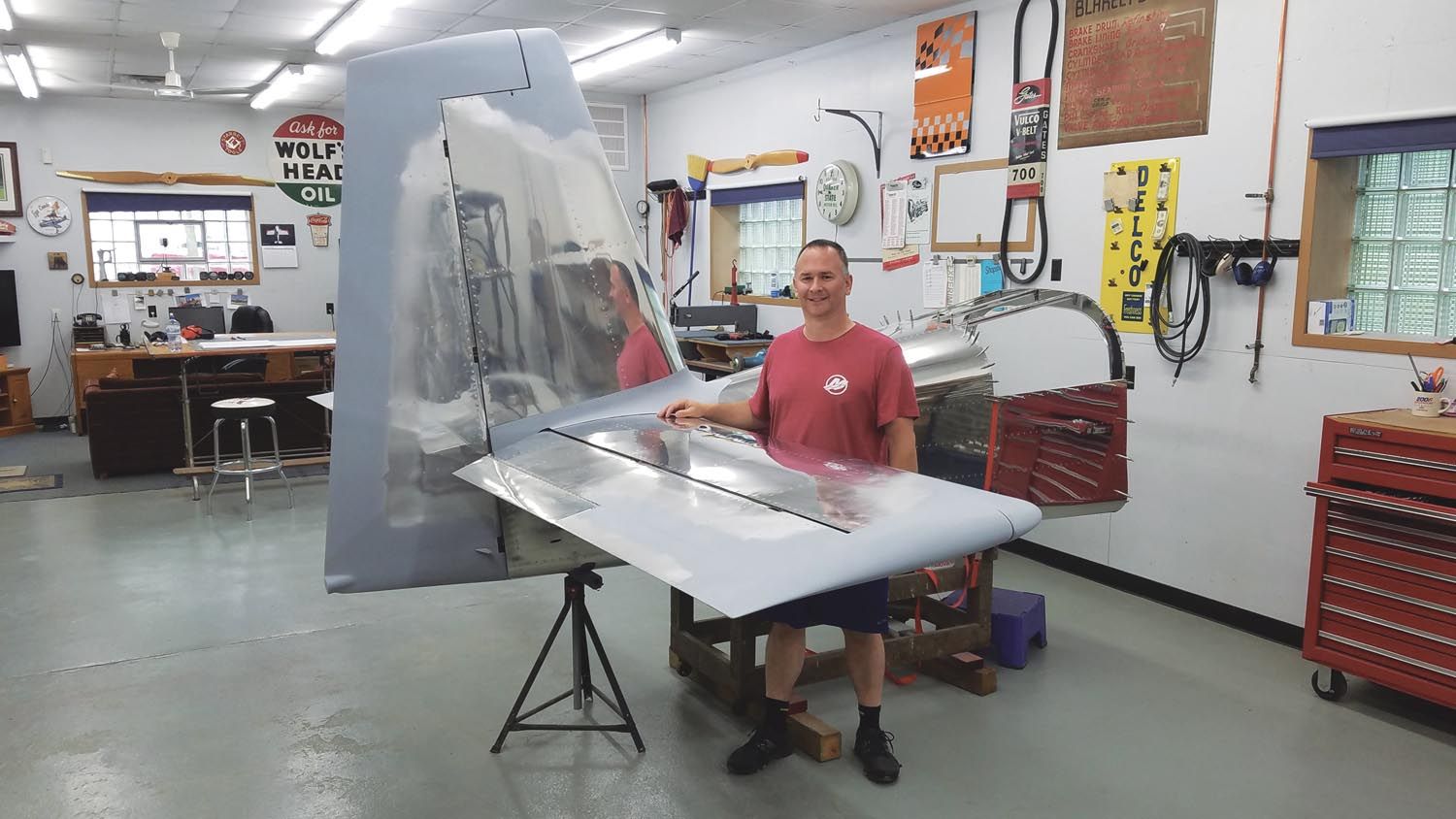
Project RV-10
It was a shared decision to build an RV-10, though the data plate, repairman’s certificate and Lindy bear only Eric’s name. “He’s 15 years younger than me,” said Trace, “so I figured the plane would be his someday. He pretty much called all the shots on it.” The project began in March 2020, just as the pandemic struck. Under the circumstances, Eric and Trace weren’t sure they should jump into a big project. They started with the empennage and got through the airframe in a year. Eric said, “We could see the supply chain problem developing so we ordered everything: the prop, the engine—everything. We didn’t have to wait for anything.”
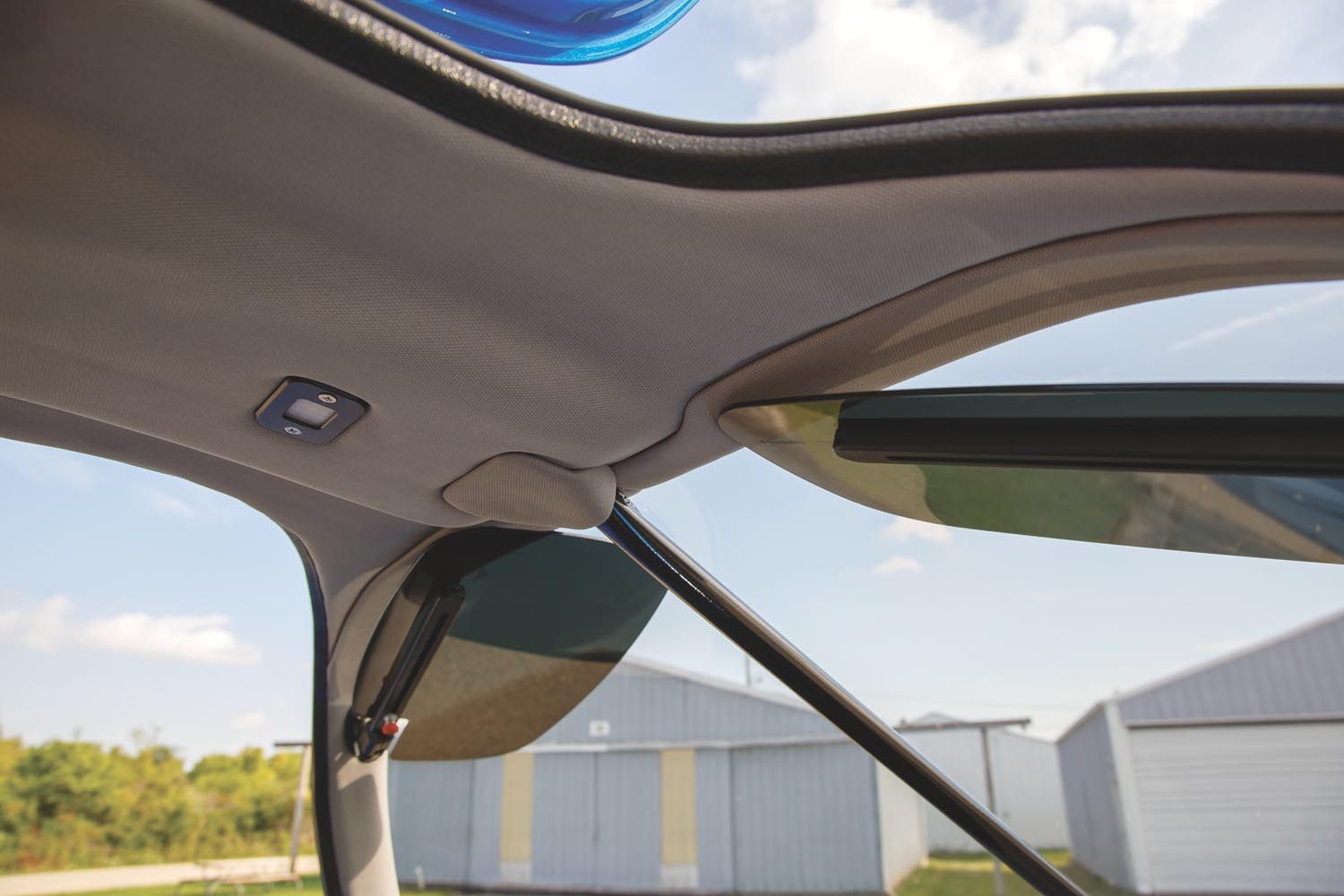
Working 20 to 25 hours per week each, the airplane was built at Trace’s home shop. Trace, being retired, would prepare parts during the day. “I’d do the drilling, deburring and dimpling. When Eric came in the evening we would assemble the parts. Most of the rivets were installed as a team.” Trace’s wife, Cindy, made them dinner and let them watch “Jeopardy” before kicking them to the shop. “Even after the airplane moved to the hangar,” said Trace, “she brought us dinner.” The project took three years and three months. “We liked what we did on my RV-7 so we just copied that, right down to the paint scheme,” said Trace, who was diagnosed with cancer in the middle of the project. “While recovering I had the desire to keep building but the ability wasn’t there. It took eight months to recover. Eric still came to my home shop three days a week. I did what I could, which wasn’t much.” Trace is now cancer free.
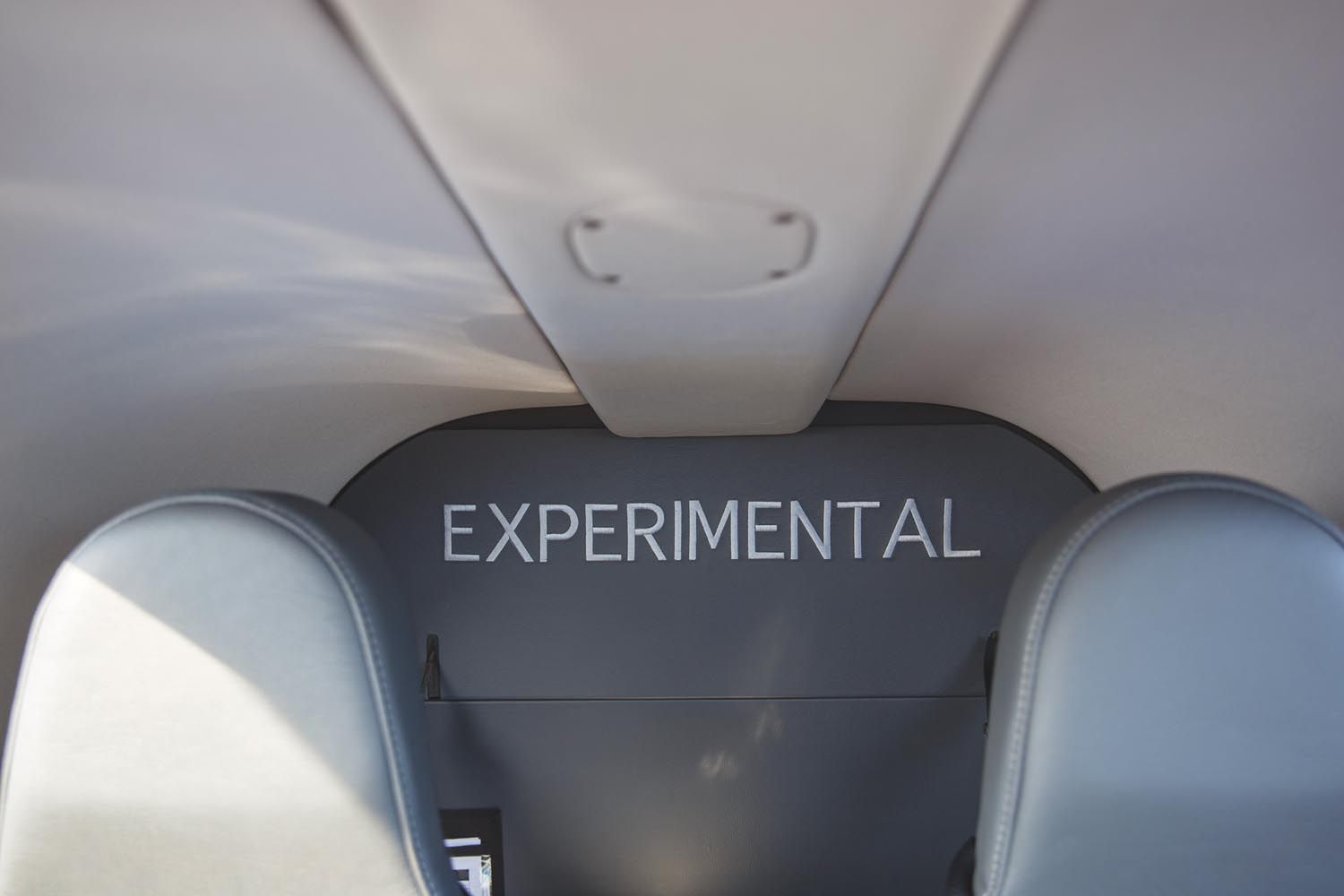
Clean. Simple. Elegant.
Those three words guided the execution of the RV-10’s interior. Eric looked at available upholstery for the RV-10 and concluded, “They’re all right, but they all look the same.” In true homebuilding fashion he bought a used industrial sewing machine and taught himself to sew by redoing a flying club’s Cessna seats for free. Eric began making the leather seats for the RV-10 by taking apart a Classic Aero Designs seat from Trace’s RV-7, to see how it was made. “I like Classic Aero’s products, but they don’t offer anything for the RV-10.” The color-matched trim panels are vinyl glued over custom-made fiberglass molds. “When you look at many RV-10s, the interior of the doors are often just painted, or material is glued on the door shell, leaving a raw edge. We didn’t want raw edges. We used the doors and pillars as molds and vacuum-bagged a thin layer of fiberglass over them, creating molded panels that we wrapped in vinyl. That gave us the finished edges we wanted.” The panels are held in place with Velcro. The overhead console was also custom-made. “We wanted a chase to run wires and to make it look nice, rather than having a flat ceiling.” Further underscoring that dedicated builders can tackle the entirety of an aircraft project without leaning on professional services, the Experimental placard on the aft luggage bulkhead was embroidered by Eric. “The machine could do three letters at a time. I just needed to take care lining up the letters.”
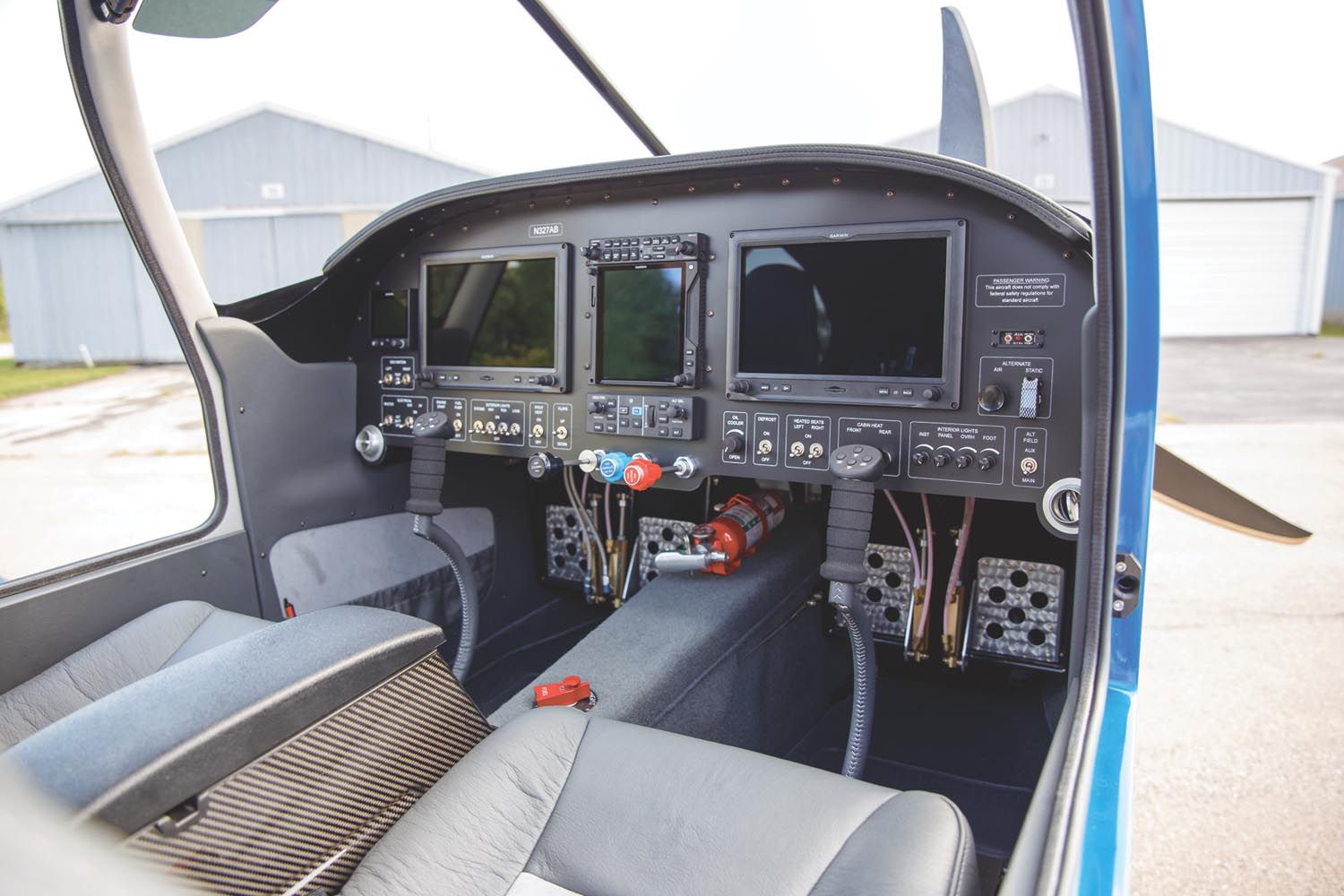
Eric designed the instrument panel in AutoCAD. Its structural layer, 0.063-inch-thick aluminum, and its top layer, black-on-white acrylic, were laser cut using the same program for a perfect match. To create the panel’s labels, Eric used a friend’s laser to remove the thin black layer from the acrylic panel overlay. This is where the panel shines, so to speak. Small electroluminescent panels, which glow to illuminate the laser-etched labeling, are sandwiched between the layers. The luminescent panels are tied to a rheostat. The effect is impressive. Eric credits that idea to another pair of RV-10 builders, Tim and Laura Huneycutt, who documented the design on their website, www.n1017h.com.
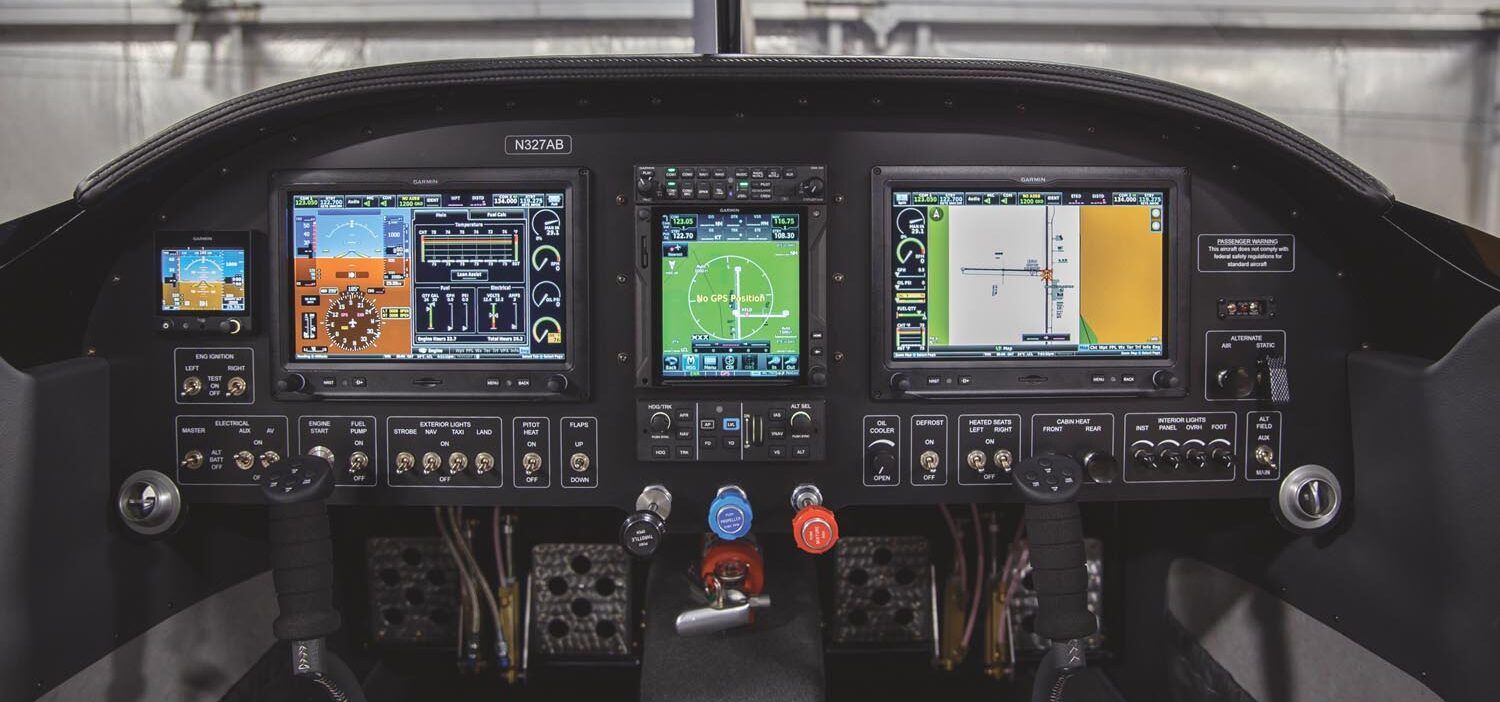
Fit and Finish
Considerable time was given to creating crisp cowling split lines and aligning the fiberglass wing and tail tips with their corresponding control surfaces. “We split the wingtips horizontally with a Sawzall, which allowed the top and bottom halves to slide over each other to achieve perfect alignment with the aileron trailing edges, then bonded them back together,” said Eric. The gear fairings and wheel pants also received considerable thought and attention to achieve a better-than-factory fit and provide improved long-term service. Eric explained, “We learned from the RV-7 that over time the gear leg will begin to chew into the wheel pant fairing. For the -10 we layered duct tape on the gear leg before molding the fairing. That left room for a layer of felt, in addition to anti-chafing tape. That way we won’t get wear in that location.” Eric, a self-taught painter, sprayed the aircraft with DuPont ChromaPremier. “We made our own paint booth out of 2x4s and plastic,” said Eric. Trace added, “We liked the paint scheme on my RV-7 so we duplicated it on the RV-10. That saved a lot of time.”
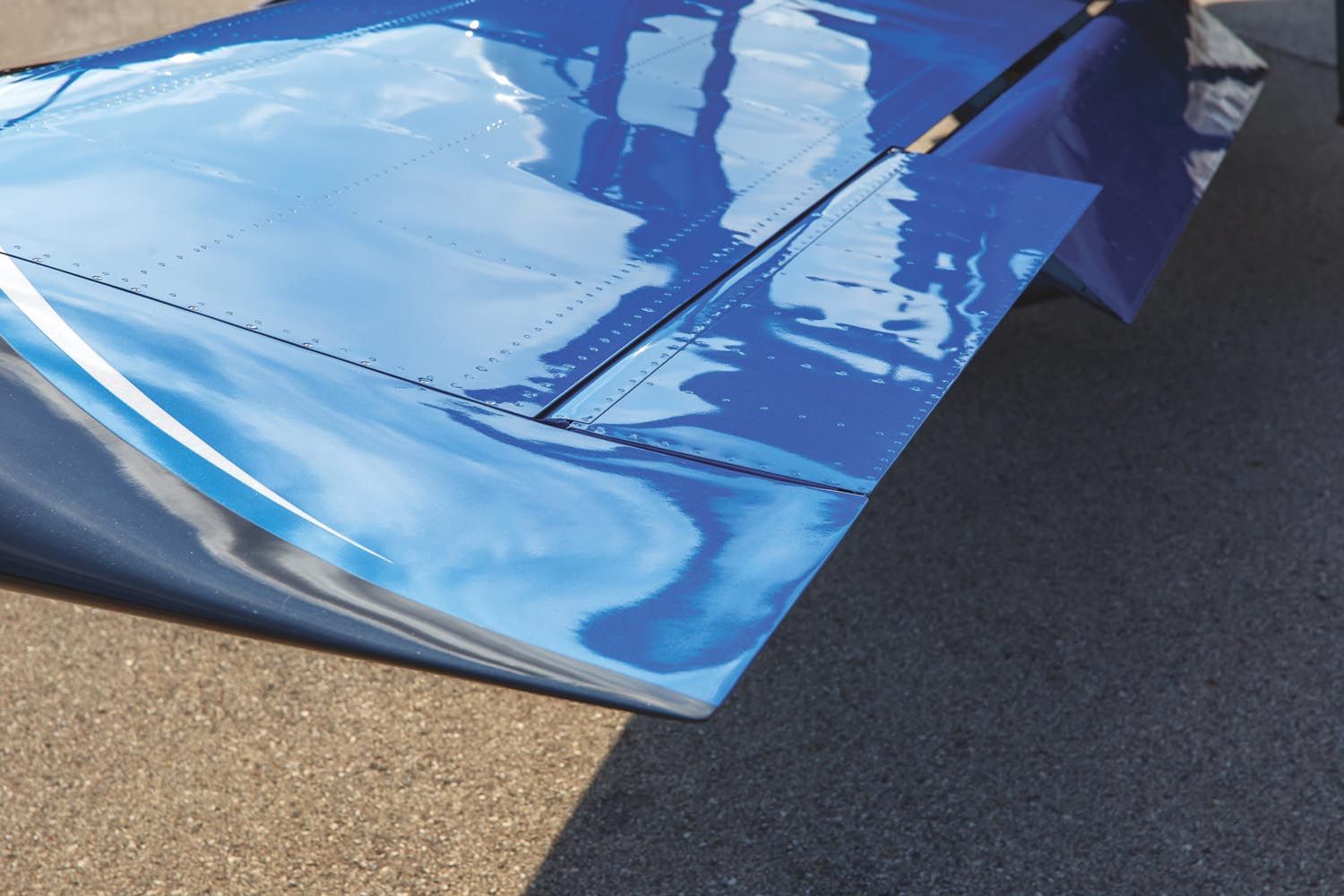
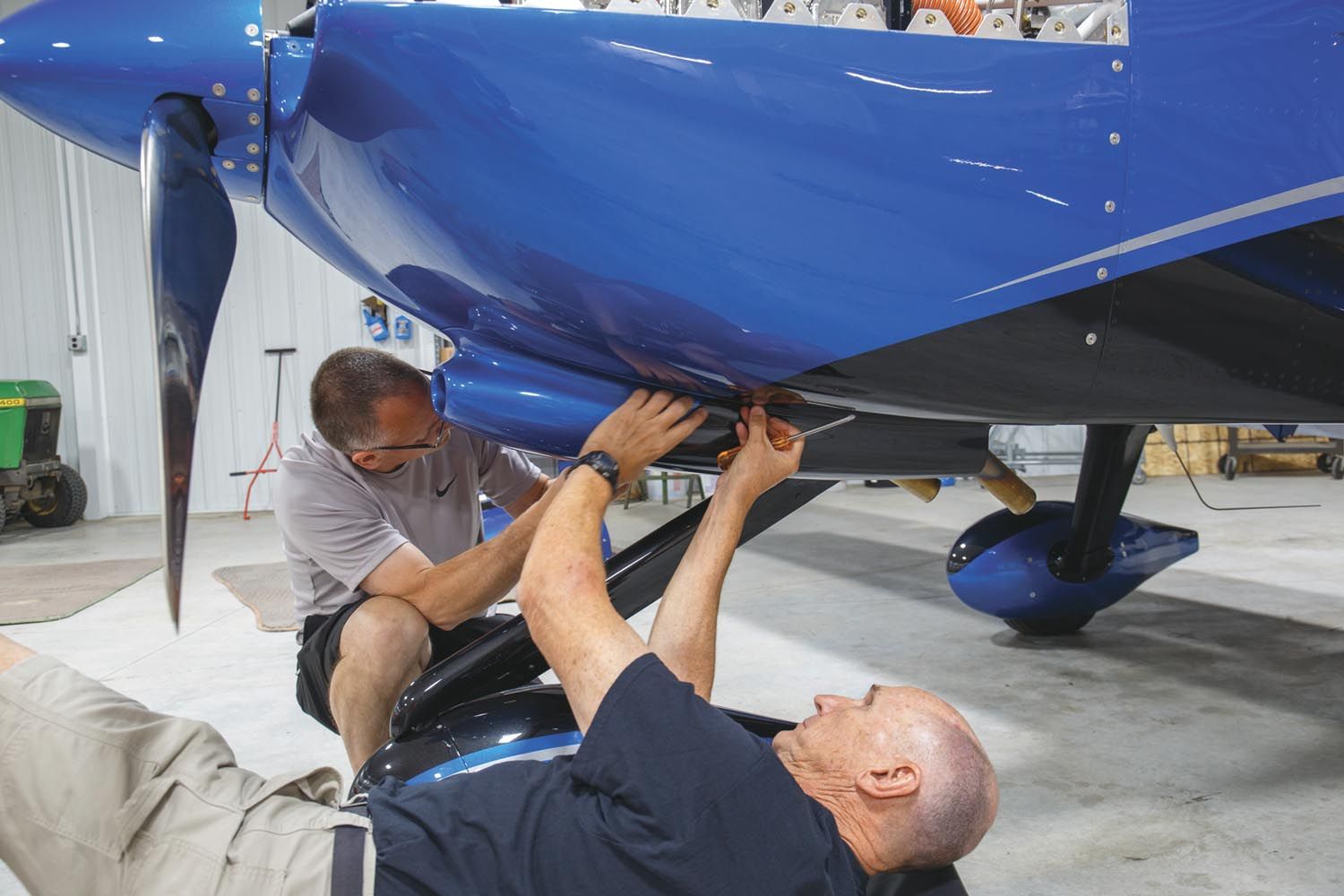
Under the Customized Cowl
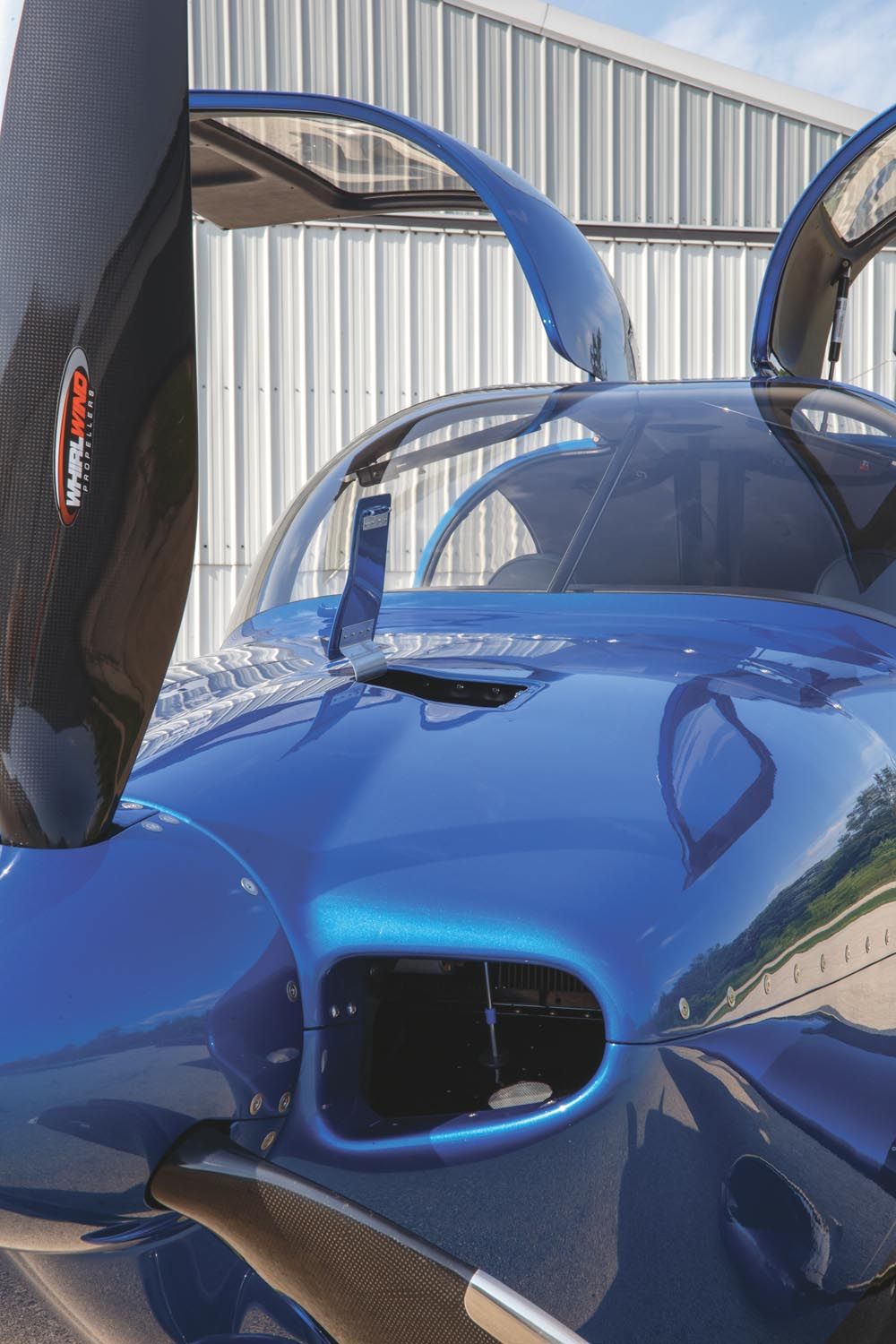
The Titan valve covers are a head fake; they adorn an Aero Sport Power IO-540-D4A5 engine, which turns a Whirl Wind propeller. “We wanted to dress the engine up with some chrome,” said Trace. The well-executed installation includes a custom alternate-air source inlet which, unlike the version shown in the plans, can be opened and closed by a cockpit control. An auxiliary battery stands by to power the essential circuits should the primary battery or circuit fail. “If the main battery or circuit fails, you typically lose your alternator. We can flip a switch on the panel to put the alternator on the auxiliary battery circuit. As long as the alternator is working, the auxiliary battery is being charged, giving us extended time.” If the alternator isn’t working, the auxiliary battery carries enough charge to get them safely down.
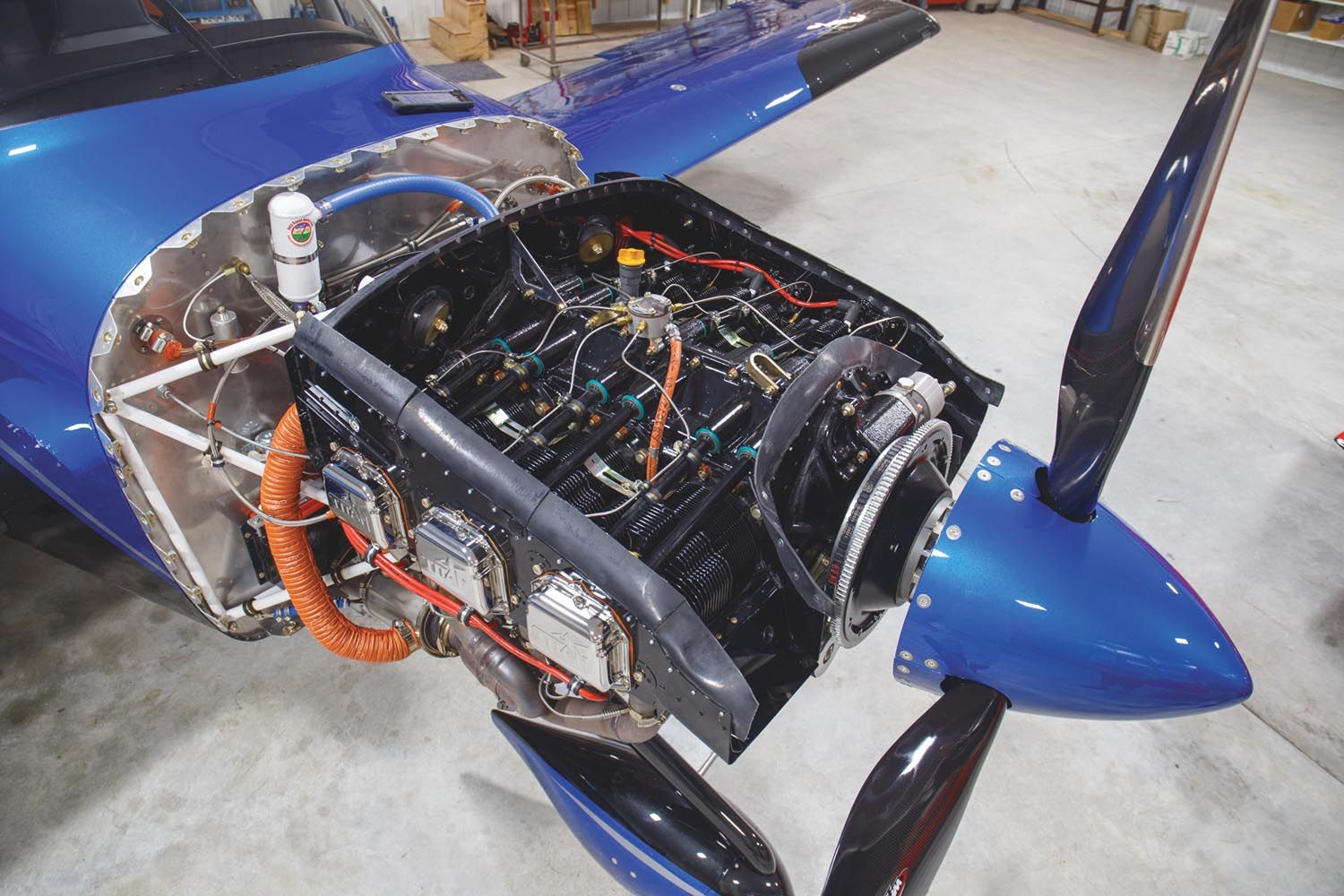
Eric and Trace both credit their Lindy to their execution of the details and the fact they did all of the work themselves. Eric said, “What’s funny is I didn’t even want to take it to AirVenture this year because of a cosmetic flaw around the windows, which appeared after it was painted and needs to be fixed. I was thinking, ‘That’s so ugly. It’s so ugly,’ because that’s all I could see. I tried to improve upon something, but it failed. But it’s fixable.” Of course, Eric pointed out the blemishes.
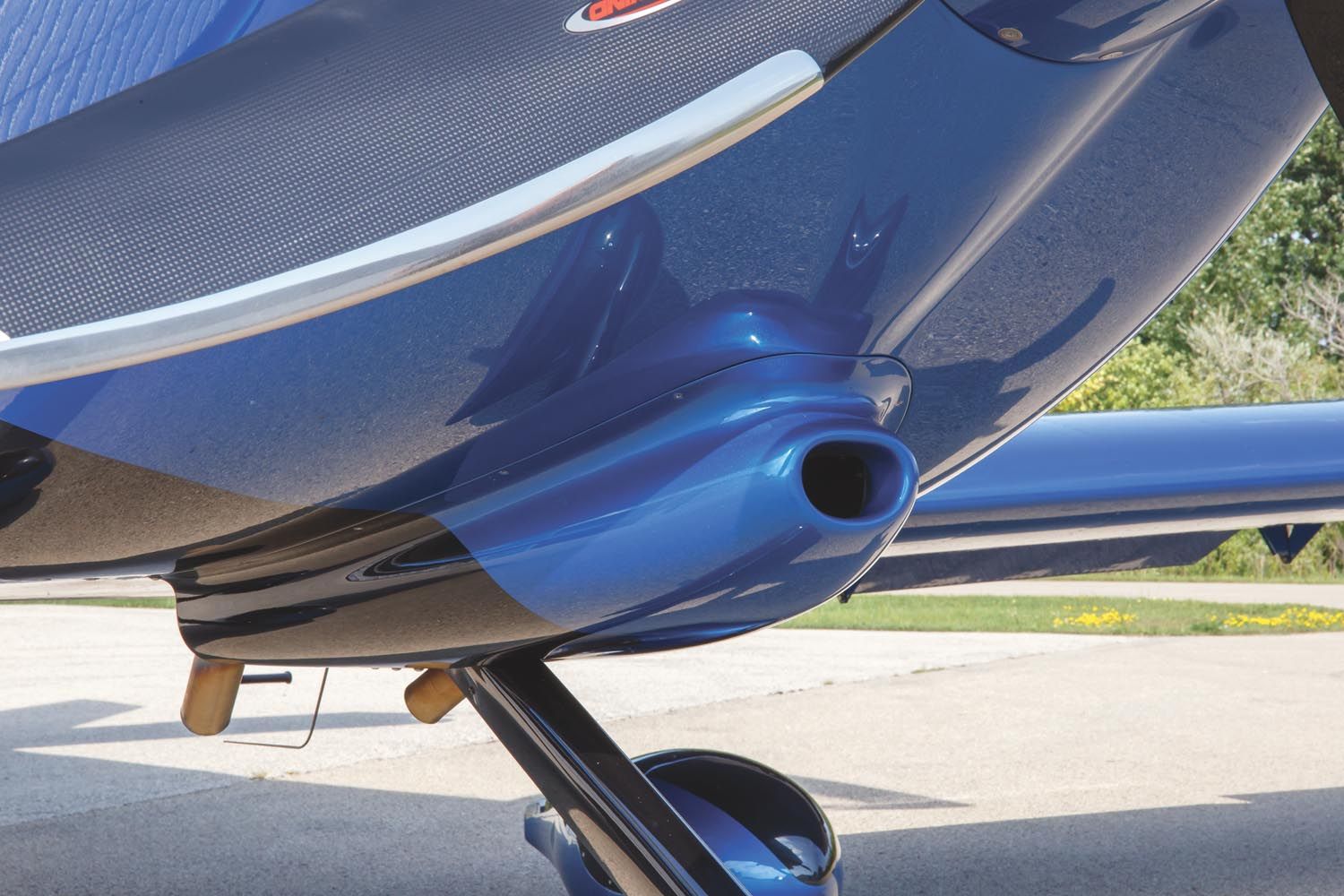
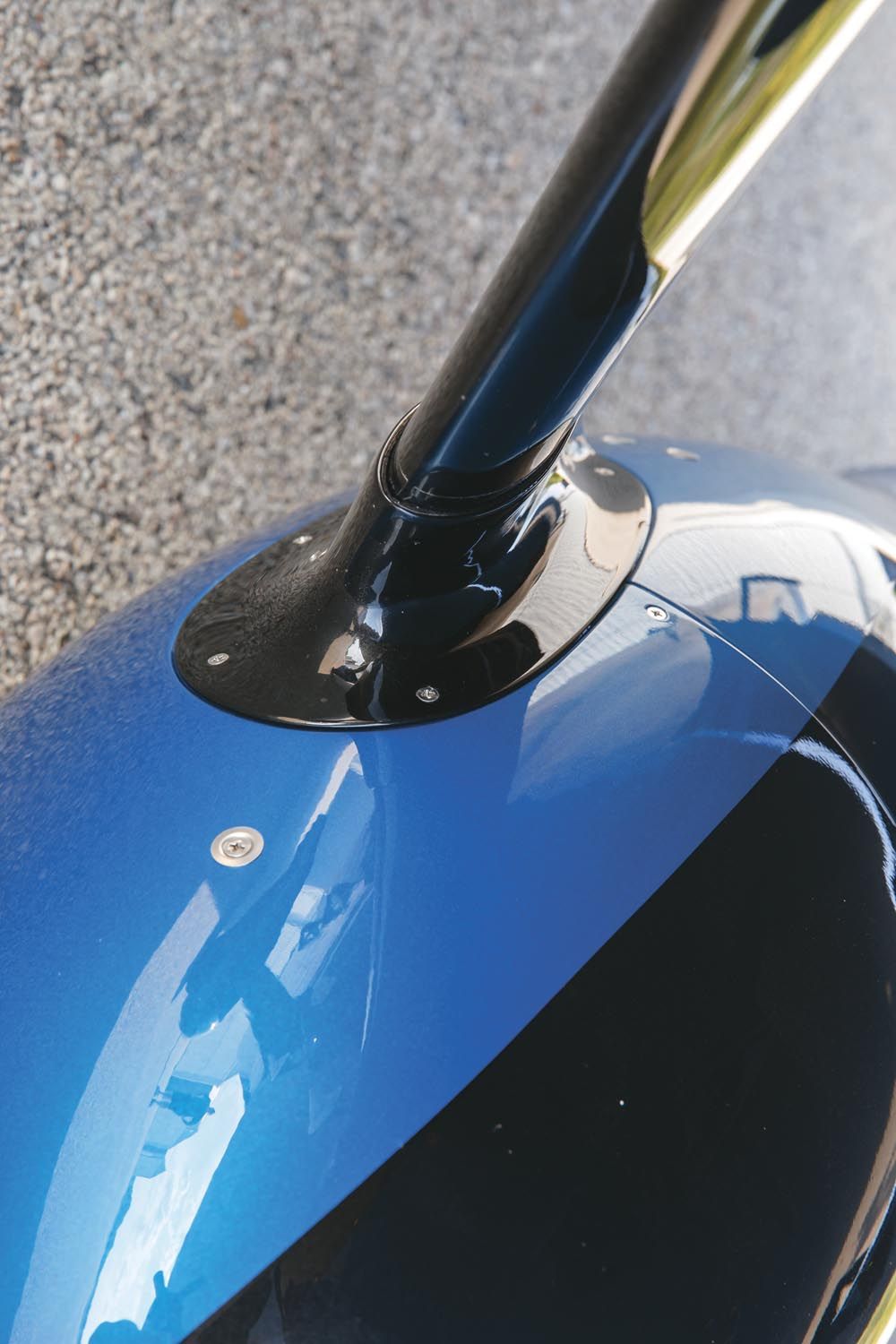
Trace said they never had to reorder a part. “If we did make a mistake, which was seldom, we found a way to correct it or we made a replacement part ourselves.” When asked his reaction to being awarded Kitbuilt Reserve Grand Champion, Trace was quick to answer: “I couldn’t believe it. We figured maybe another Outstanding Workmanship plaque, then we’d both have one with our name on it. When they finished passing out the Bronze Lindys I thought, “Well, I’m going home with my tail between my legs. We got nothing. Then they called Eric’s name for Reserve Grand Champion.”
So what’s next for the two? Eric says, “Flying. Lots of flying.” Trace added, “Yeah, I’m goin’ flying.” And with a wink in his voice he added, “I’ve got my Silver Lindy, I’m flying to Disney World.”
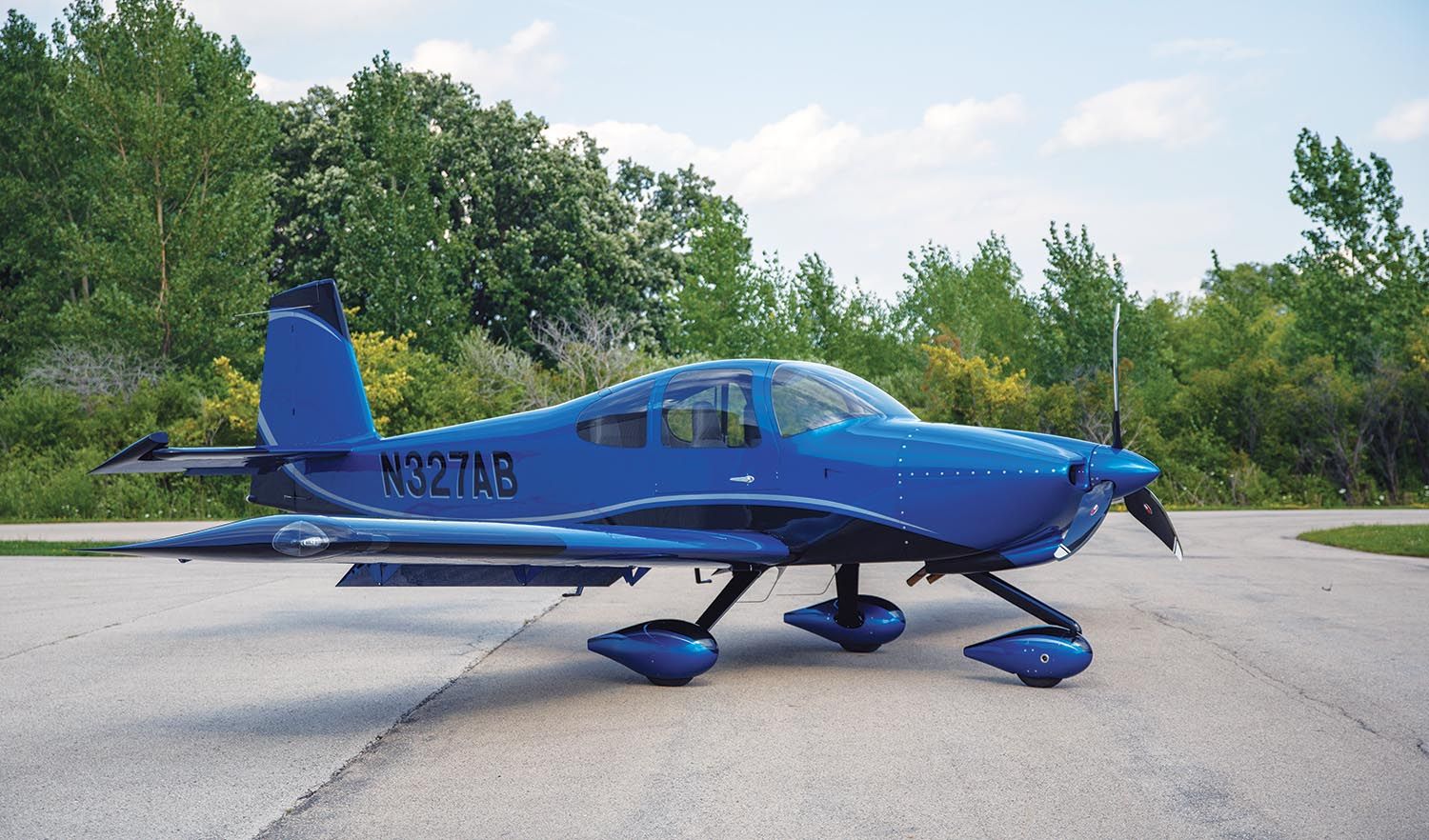