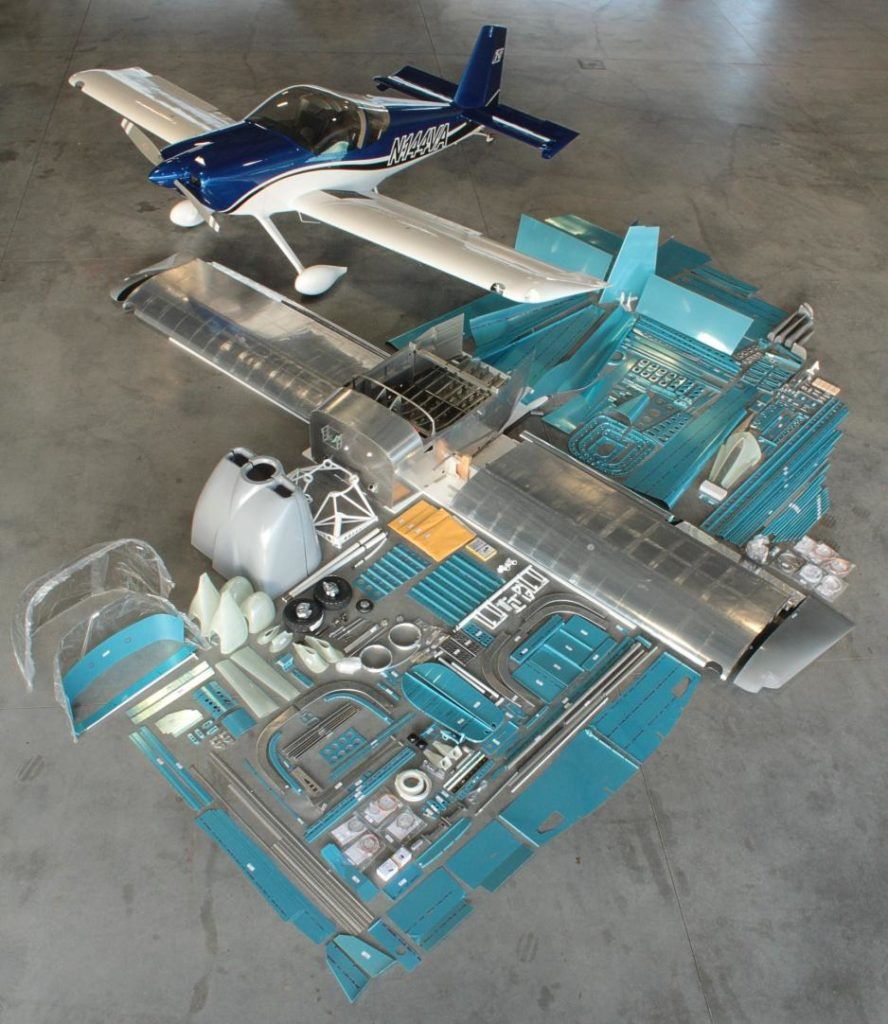
Van’s Aircraft responded to reports of cracking of dimpled parts found in recent kits here at AirVenture on Tuesday morning. The defects are the result of changes in the process for laser-cutting parts by an outside vendor. From February 2022 through June 2023, Van’s transitioned some parts from traditional punch-press manufacturing to an outside vendor that could laser-cut rivet holes. The move was intended to increase the company’s throughput and reduce the lead time and backlogs in kit deliveries. Only thinner parts were outsourced in this fashion and most, according to president and chief engineer Rian Johnson, were in low-stress and non-critical parts of the airframe. Van’s has since stopped using the laser-cut parts in this application and, to help bolster factory productivity, invested in a new, larger press-punch machine.
The root cause appears to be a change in the way the parts were cut. Originally, Van’s specified that the laser make a “pretzel” cut in the part—starting in the center, moving to the periphery and concluding back in the center. Apparently, the vendor changed the cutting path to begin in the middle, extend to the periphery of the hole, stop briefly and turn direction to follow the hole around, eventually stopping at that same point at the end of the cut. This caused a small portion of the metal to become overheated. Builders began noting these defects in parts, some worse than others, and then began to see cracking after the hole had been dimpled. (RVs have a significant percentage of flush riveting.)
In his presentation Tuesday, Johnson explained in depth the kinds of testing the factory is conducting to determine the actual impact of the defects. One revealing fact is that the most loaded part of the flush rivet is actually around the outer edge of the dimple itself. Also, the cracks found in the parts most often do not originate or end at the laser defect.
The upshot for RV builders, in this case mainly the RV-10 and RV-14 models, is that certain parts are likely to be assessed as suitable for low-stress locations but some, like tail-surface spars, will require replacement. The company has told builders to stop building with the laser-cut parts for now. Johnson urged patience to allow Van’s to finish its extensive testing, said to be in the 45- to 60-day range, before tearing into any completed pieces. He said that the company needs to determine if associated parts are impacted before finalizing its recommendations. Van’s is also readying a process for builders to receive replacement parts.