
Well built and equipped, Dan West’s RV-8 is a full-featured daily flyer with racing pretensions. There’s no bleeding edge aerodynamics going on here as the tiedown rings and antenna farm attest. That means its 240+mph TAS at altitude comes down to muscular engine power and efficient prop thrust.
Often the stories of modified Experimentals are tales of extremes. Those involved are typically well-entrenched in the aviation business and enjoy access to special parts at special prices, while at the same time harboring special drives for specialist airplanes. This is not one of those stories.
Instead, this is a look at a regular guy who’s tried something a little different: adding a supercharger to his RV-8. And as has become popular, he ran it naturally aspirated in the air races at Reno, Nevada, in 2015, then supercharged it in 2016, just ten days after fitting the blower. He also logged a little regular flying with the supercharger, but just a little until medical issues crimped his flying last year. But in the short time this boosted RV-8 has flown, it’s given us all a hint of what a simple supercharger installation can do for a regular guy.
That regular guy is Dan West, a successful concrete contractor from Sacramento, California, along with being well known in the RV and West Coast Ravens formation worlds.
Nordo, as he’s known to his friends, banged out his RV-8 in a mere 19 months, finishing in 2009. “It was a quickbuild kit, if that helps,” he says, almost apologetically. The airframe was built according to plans; power is from a Barrett Precision Engines 390 Lycoming. Both engine and airframe have worked great in the nearly 1000 hours he’s flown it, says Dan, and he’s happy with both Barrett and Van’s.
A nicely built daily flier, Dan has flown his -8 to the big meet at Arlington, Washington, where he earned an outstanding workmanship award, along with visits to AirVenture as part of a 34-ship flyover, and jaunts to the Bahamas and West Indies.
Airframe: Stock Is Good
Dan’s -8 airframe is about as stock as they come, and he says besides trying to avoid too much weight creep, he did nothing different. Other than changes to the cowling forced by the supercharger, the only airframe mod has been Bonehead composite wingtips fitted in 2015. “Down low they help a lot,” says Dan, “up high not so much; it’s better to have wider-span tips. The density altitude here [Reno] is right on the edge. If it’s cool during qualifying then they help.”

Anyone looking for a fundamental bump in engine power at low- to mid-altitudes should consider a supercharger. There are few kits available for such installations, but using Bill Beaton’s already-developed brackets and existing mechanical fuel injection, Dan and his crew made this combination work with minimum trouble.
Under the Cowling
Back when Barrett Precision Engines assembled Dan’s 390 aftermarket engine, kits were not widely available, so his engine features Lycoming parts throughout. Fueling is via Airflow Performance using an FM200 fuel servo breathing through a stock Lycoming intake/sump. According to Dan, Allen Barrett said breathing would improve only slightly if the intake was ported, so the intake was left stock. As always, if notably improved intake performance is desired, a cold air intake is the only way to go. That’s a great strategy on a normally aspirated engine, but wouldn’t be quite as good an investment on a mild engine with a supercharger such as this. Big, dumb with a blower is still a cost-effective path to power.

Dan’s Vortech V3 supercharger sits in brackets designed and built by Bill Beaton for his Harmon Rocket’s 540; it’s a good example of 360/390/540 commonality. When Beaton moved to another blower bracket, he sold these to Dan. Supercharger speed is easily adjusted via blower pulley diameter; the idler pulley is a common Dayton automotive part. The belt is a six-rib from NAPA.
In some ways, the Bendix-based mechanical fuel injection provided by the Airflow Performance hardware is simpler than electronic fuel injection. Also, many builders already have such a system on their existing core engine. If so, this old faithful in fuel delivery often offers significantly lower initial cost, if not the best long-term fuel economy. Mechanical injection also provides good power at high power levels, and Dan has found it easily adapts to the higher air and fuel flows associated with supercharging. The only change was to raise fuel pressure to overcome the boost pressure in the intake manifold. This is a necessary step with any form of supercharging.

A first-iteration installation, Dan’s blower caused its share of tacked-on plumbing and cut baffling. The brass plug in the blower housing is a fill port and dipstick for the supercharger’s self-contained lubrication fluid. No interaction with the engine’s oiling system is needed.
Going Blown
Regular readers may recall Bill Beaton’s supercharged Harmon Rocket II featured in the May 2017 issue of KITPLANES [see “Supercharging: The Turbo Alternative“]. A dedicated experimenter, Bill figures prominently in Dan West’s RV-8 story because much of Bill’s first supercharger installation was taken off his Harmon and sold to Dan, so that’s what we’re looking at now.

Blower brackets are always thick, beefy, aluminum slabs. Because triangulation is difficult, solid alignment is required to avoid thrown or damaged belts, and in high-boost applications there can be 70+ hp needed to drive the supercharger. We’d guess Dan’s drive loads are more like 25 hp, but given turbulence and G load, this is not a place to skimp on strength.
Aside from Bill running a 6-cylinder 540 Lycoming and Dan a 4-cylinder 390, the fundamental difference between the two installations is Bill uses a blow-through style and Dan a draw-through. That is, the fuel servo (throttle body, actually) is located downstream of the supercharger on Bill’s airplane and upstream of the supercharger on Dan’s.
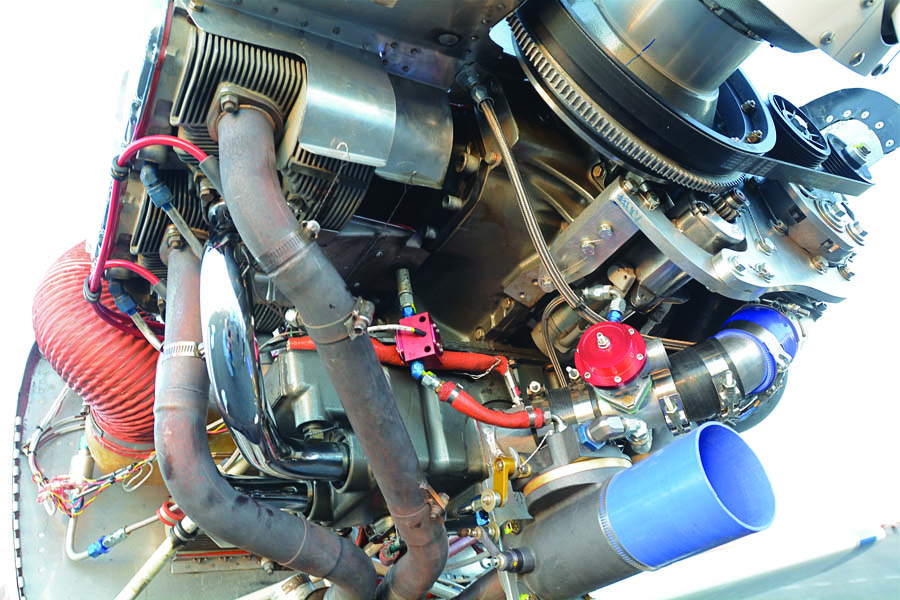
It blends in visually, but a close look shows the blower bracket extends horizontally under the engine case. Otherwise, the right side of the engine is essentially stock, a big difference from a twin-turbo layout.
The consequences of the throttle body placement are related to obstructing airflow to the supercharger and metering the fuel. In Bill’s blow-through system, the inlet side of the supercharger is unobstructed, and, in fact, may see slight ram air boost from the short, open cowling inlet and duct. Conversely, Dan’s draw-through installation means the fuel servo forms an airflow obstruction on the supercharger’s inlet side, which is, we’ll recall, naturally aspirated.
As for fuel metering, Bill Beaton’s 540 is electronically fuel injected, so he has total control over when and how much fuel is injected, although he had to tune his engine management software to accommodate the higher airflow. Dan West’s draw-through mechanical injection system still accurately meters all the air entering the engine, so fuel volume is automatically compensated for, but as previously mentioned, the fuel pressure had to be increased equally with the boost pressure in the manifold. This rise in pressure is not to increase fuel volume, but only to the match the increased pressure in the intake manifold. This is especially true with the low fuel pressures in the Bendix-based system; unmodified, in the worst case the manifold pressure could be higher than the stock fuel pressure and fuel would not flow out the nozzles.

While no bypass valve is needed with a draw-through blower, a boost relief valve is there to vent any (unlikely) excess boost. It’s the red anodized unit, which vents excess boost into the lower cowling via the open tube.
A big plus for the draw-through/mechanical fuel injection layout is sucking air through the fuel servo is how mechanical fuel injection was designed to meter fuel, so there are no gotchas.
There’s also the need to vent air from between the supercharger and the throttle with blow-through systems. This is done with a bypass valve that opens when pressure rises, typically when the throttle is closed at high engine rpm, such as descending with a fixed-pitch propeller. This is because the supercharger is still spinning quickly, yet the closed throttle traps the air between the supercharger and throttle. Minus a bypass valve, heat and pressure waves quickly form in the inlet tract. These are tough on the supercharger’s impeller, and if the throttle is quickly reopened, the heated air can cause a spike of detonation.

Hiding behind the chromed intake runner is Dan’s custom-fabricated carbon fiber blower inlet duct. This is always a tight fit on Lycomings, as evidenced by the custom oil drain back tube on cylinder #2.
Bill and Dan both opted for highly efficient centrifugal superchargers, and while both airplanes are fitted with the respected Vortech supercharger, Dan’s features a slightly different trim (impeller shape) than what Bill has ended up with. Dan is running Vortech’s V3 Si supercharger with a 3-inch pulley for a nominal maximum manifold pressure of 36 inches at 2600 rpm.
Being belt-driven, the supercharger must be mounted somewhere where a crankshaft-driven belt can reach it, and “after a lot of head scratching and looking at every corner of the engine, it ended up where it is.” Bill Beaton provided the bracket, which he had developed when first fitting his blower to his 540.

One advantage to supercharging is uncomplicated exhaust. Dan needed to do nothing to his existing 4x individual pipe Vetterman system, although he’s likely reconnected his cockpit heater by now. Seen in profile are the Sky Dynamics blower belt pulley and 2.5-inch Saber prop extension. The extension is a must to fit the blower, as are time-consuming cowling mods to fit the extension.
Next came plumbing the supercharger’s air inlet and exit. After more head scratching and “a lot of Coors Light…we got the plumbing through the servo,” says Dan. “And it worked, just like Don Rivera [of Air Flow Performance] said.” The most custom part of this was having to make a carbon fiber inlet adapter from the pipe leading up from the fuel servo to the blower’s inlet. Dan said there was no workable off-the-shelf piece, and he already had the carbon fiber in the shop, so laying up the duct was expedient.
Because the Vortech V3 uses a self-contained oiling system, Dan didn’t need to plumb oil from the engine to the blower and back again. Such blower lubrication is necessary with some earlier Vortechs and turbos, but not with the V3. Instead, the self-contained oil is changed every 7500 miles in automobiles, so this simple 4-ounce chore is probably another maintenance item during the annual condition inspection.
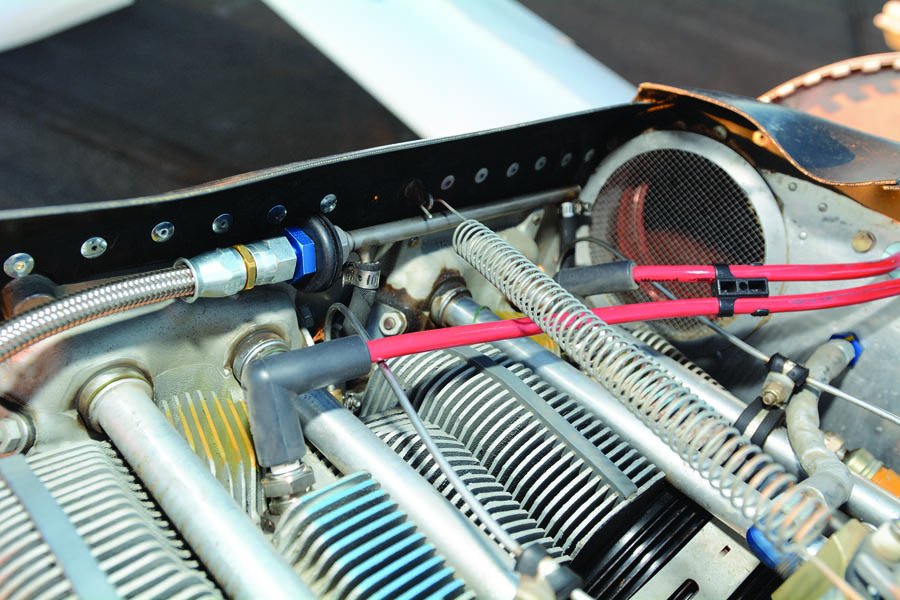
There aren’t many changes atop the cylinders, but a boost reference line communicates with the fuel injector nozzles, and the automotive spark plugs are also visible. Ignition is by P-Mags retarded an undisclosed amount in deference to the increased cylinder pressure.
Air-to-air charge coolers are out of favor at Reno due to aerodynamic drag, not to mention their immense packaging headaches, so an ADI (anti-detonation injection) system was fitted. More commonly called water injection by the horizontally opposed and automobile crowd, a simple ADI tank and a few bits of plumbing are far easier to install than an air-to-air charge cooler, and at least as effective at Reno.
Dan already had a smoke system from Smoke System Helper on his RV, so he called Marv Homsley there for a second 4-gallon tank that Dan mounted in the forward baggage well for ADI. It is hooked to the pressure side of the supercharger via a 60-gallons-per-hour pump with an electric shutoff valve in case the tank goes dry. A Snow Performance water injection valve sourced from Summit Racing does the metering, and it was plumbed using heat-sleeved stainless braided hose and is controlled by the same manual switch operating the system’s water pump solenoid.

Dan feeds his firewall-mounted 13-row Stewart Warner oil cooler with five-inch SCAT tube, good for 193 F oil temps while racing with the ADI flowing. Still, Dan is considering a dedicated cooler exit to better handle the wide range of oil cooling needs between cruising and racing.
Around the Pylons
Rushed together just 10 days before Reno, the RV was hustled through a Phase 1 test and then it was off to races. “We got real lucky on pulleys,” said Dan. “We were shooting for 35 inches at Reno,” and they landed right on the money with the blower topping out at 36 inches at Reno’s typical 7000- to 8000-foot density altitude.
Concerned that with only 19 hours on the engine since the supercharger install, the cylinder base nuts might work themselves loose, Dan kept torquing them. But they never did loosen, so that worry was discarded.
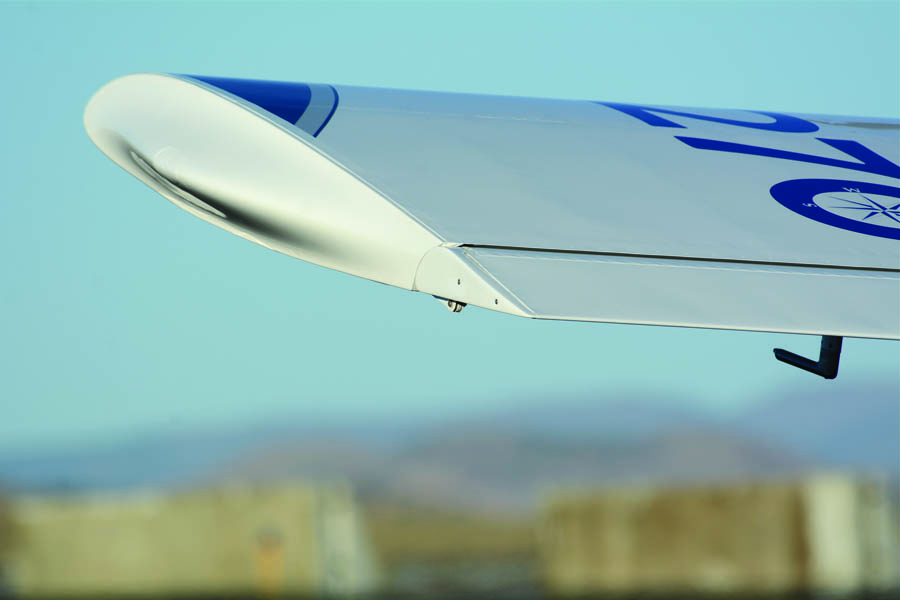
The Bonehead composite wingtips were installed for Reno 2015. Dan reports mixed results depending on density altitude; the thicker the air, the better the tips work. The unusual protruding shape pays off with less drag, but the reduction in span is telling as the air thins.
Predictably, engine temperatures ran high during practice and qualifying, so the single ADI nozzle size was increased. The final nozzle was labeled a #4 and is mounted just downstream of the throttle body.
There’s no doubt the supercharger makes the RV-8 faster. Dan qualified at a 241.9 mph while circling the pylons (40 mph slower than Bill Beaton in his 6-cylinder Rocket), making him the fastest 4-banger RV-8 qualifier, and likely one of the faster RV-8s ever. Maybe more impressively, with gravity assist Dan saw 272 mph down the chute leading onto the racecourse.

This is pretty luxurious for a race plane, but pretty sweet during cross-countries. Something of a Dynon showroom, Dan’s RV-8 cockpit offers all the flight and engine information imaginable. The sponsored installation was made by Lee Ulrich. Other crew members are Erich Scheppers (fiberglass) and Dan’s brother Dave, a jet A&P who lends an extra set of eyes. Dan’s also quick to credit his wife Diane who “owns the airplane, too.”
Trying not to run the new combination too hard, Dan initially set his race power at 2600 rpm and 36 inches. That’s barely three pounds of boost—a baby step in supercharging terms, and with the ADI flowing, this resulted in 410 F CHTs, a far cry from the 300 F he typically saw cruising lean of peak and naturally aspirated. Interestingly, EGTs were unchanged.
Getting greedy on Friday of race week, Dan changed to a smaller blower pulley, moving maximum manifold pressure to a meaningful 42 inches (six pounds of boost) and all the temperature instruments to the far right. “It got hot,” is all Dan would tell us. It must have, as the crew waited hours for the engine to cool before borescoping it. Everything looked sort of OK, but they added a second crankcase breather because a seal (not the front crankcase seal) had blown out somewhere.
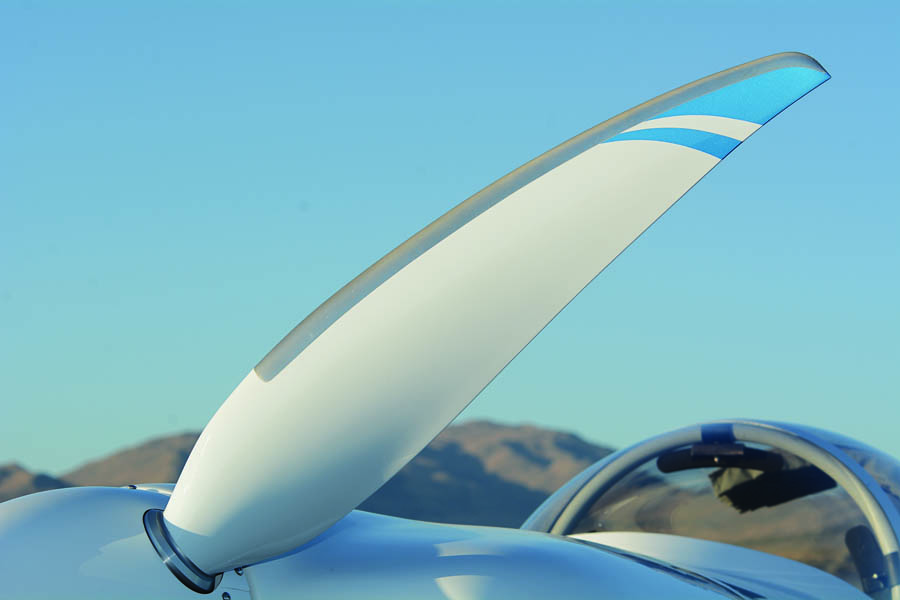
Originally, Dan ran a 200 constant speed Whirl Wind prop, but replaced it with this 74 RV blade. The newer airfoil is advertised as speedier, something Dan didn’t see, but he notes better braking which is good in formation flying when rapid changes are needed.
By Saturday morning the plane was back together, and Dan had reverted to 2500 rpm and 35 inches of manifold pressure. The plane ran well and finished the race weekend at those power settings. Dan’s final placing was finishing 6th in the Sport Bronze race at 236.579 mph.

We’re a little slow on the uptake, so it took us the better part of an afternoon to realize the “270” on Dan’s vertical stabilizer was a play on his last name. It’s a classy graphic that eases picking the bird out of the fly-in crowd.
Post Reno
Unfortunately, Dan didn’t get much flying in after Reno and was unable to thoroughly report on how the supercharged -8 does as a cross-country machine, although it’s obviously peppier at altitude. In the one trip from Sacramento to Los Angeles, Dan said the blower “makes the trip to L.A. pretty short!” Referencing the 7000 to 10,000-foot Angeles Crest Mountains ringing the north of the charmingly named “L.A. Basin,” Dan said, “You push the throttle forward and go over the mountains that are right there.” Normally it takes some shuttle climbing or a detour through the Cajon Pass to negotiate those peaks, but with the supercharger, it’s apparently possible to simply take off at the base of the mountains and climb right over them.
Of course, the fuel burn has gone up because it’s too seductive to run at the higher speeds the blower allows, plus it’s an engineering fact the engine must burn extra fuel to make the power to drive the supercharger. Dan’s take on it? “It burns a little bit more fuel, but you are getting there faster. In the real world, the fuel burn and the speed gain pretty much equal out. You’re not wishing you hadn’t put it on there.”