We had turned into the wind and braked on the runup turnout, preparing to launch on a 1-hour, 15-minute flight to my sister’s place. I felt anxious because lately it seemed as if every time my wife agreed to fly with me (over the years she has grown increasingly reluctant to fly in small airplanes), problems had cropped up. I wanted to use our airplane to fly together above the boring and frustrating highways to fun spots. At this point, my flying plans relied on the airplane being dependable.
My wife is an experienced light plane pilot (she passed the instrument pilot checkride before she stopped flying), and she knows a bad mag drop when she sees one. Unfortunately, the second I switched to the right mag during the runup, the rpm fell off with a shudder. The JPI 700 engine monitor showed only a few bars on the No. 2 cylinder EGT. I taxied back to the ramp and got out a few tools. I knew where to concentrate my efforts, but I also knew that my wife’s willingness to ever fly with me had shrunk again. All because of a bad mag spark plug.
The Mag Check
Redundancy of systems is a cornerstone of aviation safety. To this end, two independent magneto ignition systems are installed on most aircraft engines. A magneto is an electromechanical device. Dale Crane, author of the Aviation Maintenance Technician series of books for Aviation Supplies and Academics (ASA), writes, “The magneto ignition system is one of the most important systems in a reciprocating engine.” Since many of you have airplanes that are equipped with magnetos and experience “bad” mag checks, we’ll take a closer look at magneto ignition systems.

Always use an ohmmeter to check the internal resistance of spark plugs before initial installation and reinstallation. Replace spark plugs if the internal resistance is greater than 5000 ohms.
The Path of Least Resistance
High-voltage, low-amperage electrical energy is generated during magneto rotation. This energy flow is directed to the correct cylinder in the engine firing order by a simple rotor/distributor cap interface. Both Bendix and Slick magnetos depend on the insulating qualities of air inside each magneto housing to prevent the high-energy spark from misfiring by jumping to either a spark-plug contact in the distributor cap that’s adjacent to the correct contact, or to ground at the magneto case. This works well at sea level, but at altitude the insulating qualities of air are reduced in proportion to the reduction of density. Other factors that may contribute to misfiring include high air temperatures in the magneto housing, ionization of the air inside the housing as a result of arcing and a high resistance in the spark plug. Misfiring may result in burning of the magneto internal components and subsequent failure of the magneto.
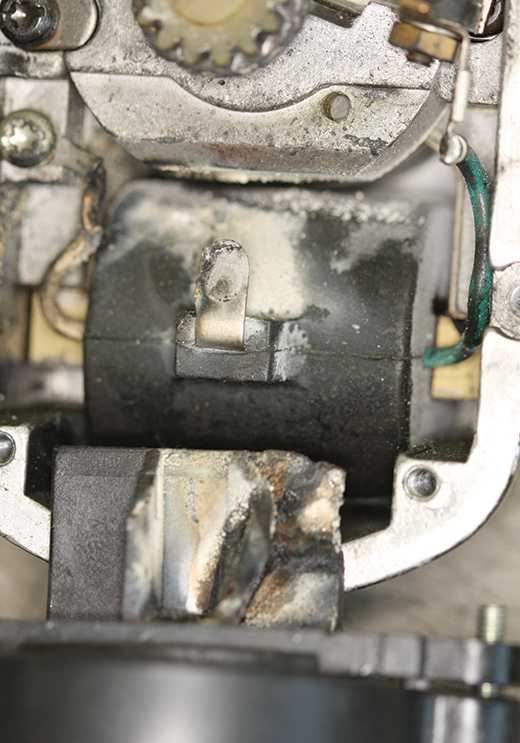
Lack of timely maintenance can result in misfiring that causes arcing within the magneto housing. Arcing burns through internal parts such as this coil.
Misfire Medicine
Manufacturers of high-powered engines designed for high-altitude operations boost the air insulation potential by piping pressurized air from the turbocharger outlet into magneto housings to restore “sea level” air-resistance values. This is called pressurizing the magneto. This solution requires the installation of a water separation device—filter or low-point check valve—between the turbocharger and magneto to prevent excess moisture from entering the magneto, because dry air insulates much better than wet air.
The most common misfire-prevention option for non-turbocharged engines is the installation of a pair of Bendix 1200 series magnetos—physically the largest magnetos available. This “medicine” is so effective that it also is installed on turbocharged aircraft in lieu of pressurizing the magneto housing.
Spark-Plug Inspections
Effective and dependable ignition-system performance requires that all the components of the system are manufactured to a standard. That seems like a no-brainer. Bendix and Slick (now owned by Champion Aerospace) magneto-overhaul manuals require checks of the go and no-go resistance values of the primary and secondary windings on coils; the specific leakage and series resistance values for capacitors require that point set spring pressures be measured to a defined value.
Not too long ago, magneto repair shops began getting more magnetos than usual that exhibited damage consistent with extensive misfiring flashover. The spark energy wasn’t making it out to the spark plugs—it was shooting to ground and arcing inside the magneto housing. The arcing, air ionization and high internal temperatures softened and burned internal parts, causing severe component damage.
Clif Orcutt at Aircraft Magneto Service (www.aircraftmagnetoservice.net/index.html) on Bainbridge Island in Washington state, in conjunction with other magneto specialists and manufacturer representatives, concluded that the baked-in internal resistors in some Champion spark plugs had exceedingly high values. All aviation spark plugs use resistors between the spark-plug lead contact and the firing electrode at the end of the plug. According to Orcutt, any spark plug with internal-resistor value greater than 5000 ohms is beyond the standard value and will be the primary cause of problems such as misfiring, hard starting and poor combustion-style magneto-check headaches.
He added that many ignition problems could be avoided when a simple electrical-resistance check between the plug lead contact and the middle electrode on the firing end is performed before the initial installation or any reinstallation of all spark plugs. Dispose of plugs that have resistance values of over 5000 ohms.
Internal and External Timing
To maximize magneto performance, two settings—internal timing and external timing—must be set correctly. Internal timing is obtained by adjusting a set of points to open at what’s known as “E” gap, which is when the potential for a hot spark is at its greatest. Point sets in Bendix and Slick magnetos are opened by either a cam follower (Bendix) or a cam (Slick). Both the follower and the cam wear, due to physical contact with rotating cams during operation. Engineers at Bendix and Slick have put a lot of effort into component design and lubrication specifications to reduce wear and compensate for the effects of wear on internal timing, but it does take place. This, plus the need to inspect for contamination and renew lubrication, is behind the mandate for 500-hour inspections.
Let’s remember that the mechanical points and coils used in magnetos are very similar to the spark ignition systems that were the standard in yesterday’s automobile engines, and that yearly tune-ups (points, plugs, condenser) were the rule on those systems. There are no solid-state electronic parts in magnetos.
External timing is also required to maximize ignition-system performance. External timing is a physical adjustment of the magneto on its mounting pad that positions the magneto “E” gap opening to the engine crankshaft rotation. Lycoming four-cylinder engines require that the magnetos be set to 25° before top dead center (BTDC).
Magneto external timing is checked at regular intervals, and the timing is adjusted as necessary by loosening the hold-down hardware slightly to permit small adjustments of the magneto on the pad. This is known as “bumping” the magneto.
As mentioned, point cams and point cam followers wear. This changes the timing of the point opening within the “E” gap range. “E” gap adjustments for internal timing may be set at any point in a specified range still within the specs. For instance, the “E” gap setting range for the Bendix S-20 series magneto is 8-14° after neutral position of the magneto. Orcutt sets the “E” gap on the S-20 to 10°.
Wear retards the spark timing, so instead of sparking the plugs at the desired 25° BTDC, the timing drifts slowly toward 26°, then 27°, etc. This retarding is the reason technicians bump magnetos to reset the external timing.
Provided the internal timing is reset at 500-hour intervals, and the point follower or cam is lubricated correctly, the “E” gap drift won’t cause a lack of spark power at the plugs.
Magneto Inspections: Impulse Couplings and 500 Hour
Both Bendix and Slick have issued service bulletins that specify maintenance intervals. These bulletins are not mandatory for Experimental airplane owners, but as Crane writes, the magneto is a vitally important part of your engine, and few glitches affect flight more than a misfiring magneto. The basic guidelines call for an external inspection (which includes checking the external timing every 100 hours), an internal inspection every 500 hours, and more extensive internal maintenance every 1000 hours. As a cost estimator, Aircraft Magneto Service does Slick 500-hour inspections for a flat rate of $250 and Bendix 500-hour inspections for a flat rate of $300. When both magnetos are known to be in good shape, ignition problems are almost always caused by spark plugs.
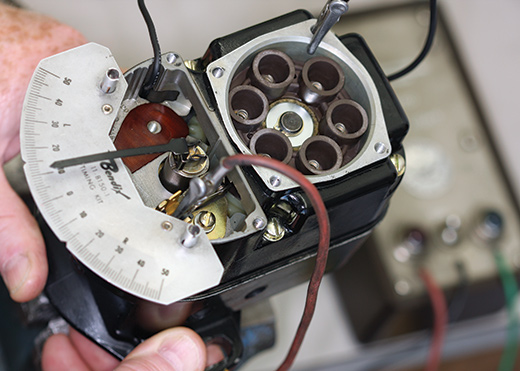
Special tools such as the degree plate and the pointer are used to set the timing (opening) of the points on this Bendix magneto. Point opening is signaled by a light and buzzing noise from the buzz box (in the background).
Timing Tools and Tricks
In 1979 I spent a few hours on a remote landing spot in Alaska, using a piece of cigarette-pack cellophane to check the timing on the Bendix 1200 magnetos on an H-391 Helo Courier.
The pilot and I were returning to Soldotna from Anchorage and were over the cold waters of Turnagain Arm when the engine shuddered a couple of times. The pilot, an old Alaska hand, immediately decided to make a precautionary landing at a nearby rough, but usable, strip. I trapped the cellophane between the points, and by slowly moving the prop in the direction of rotation (on the compression stroke of the No. 1 cylinder) was able to determine the external timing when the points opened enough to release the cellophane.
This simple test showed that the points were intact and opening at the right time. I changed a dead spark plug and we flew home, nursing mosquito-bitten skin.
The point of that story is that spark plugs cause more ignition problems than magnetos do if the magneto maintenance is kept up to date. This story also illustrates that there’s more than one way to externally time a magneto. Other timing tools include portable
timing boxes—they are usually called buzz boxes because the point opening is signaled by a buzzer and a light—such as the E50 from Eastern Electronics (www.easternelectronicsllc.com) and a crankshaft-position-indicating degree wheel (often called a coolie hat or flower pot) E25 from Eastern Electronics. One of the most inventive timing tools I’ve seen recently is the Rite-System (part number RSK-DX) from Aircraft Tool. It uses a digital inclinometer to measure crankshaft rotation and includes a solid-state buzz box. A local mechanic uses Velcro strips to secure his digital protractor to the propeller because he finds it easier to use than the degree wheel on the coolie hat. I’m going to try that one on my next annual.
If the day ever comes when you’re testing the left or right mag and the tachometer indicates a 250- to 300-rpm drop, you can be sure you have a bad plug. Years ago, before we learned the benefits of leaning mixtures aggressively while taxiing, we were taught that the drop was most likely caused by a lead clinker across the spark plug or lead fouling. We could “burn” the offending crud off the plug by running the engine up to 2000 or 2200 rpm and then leaning aggressively. In my experience that rarely works.
To locate the offending plug, look for the cylinder with the low EGT indication on your engine monitor. Then trace the spark-plug wire from the magneto that tested bad (when the magneto switch is on “L,” you are grounding the right mag and testing the left mag) to the cold cylinder, and you’ve found the bad plug.
If you don’t have an engine monitor, shut the engine down for a few minutes and un-cowl the engine as necessary to gain access to the magnetos and the top of the engine. Then start the engine and run it on the “bad” mag at 1000-1200 rpm for a minute or two. Shut down the engine, turn the mag switch to off, and then physically touch the top of each cylinder. The cylinder with the bad plug will be markedly cooler than the others. Trace the plug wire from the “bad” mag to the cold cylinder: That wire will be connected to the bad plug.
Even when the bench-style spark-plug tester indicates the plug is good, always do the simple resistance check described above before installing any spark plug. If the resistance between the contact and the firing center electrode is greater than 5000 ohms, throw the plug away or, if new, exchange it for another. Follow this simple procedure, and I’m betting your bad-mag-drop blues will fly away.
Steve Ells is what you call a gen-u-ine mechanic, a bonafide A&P with an Inspection Authorization. Former West Coast editor for AOPA Pilot and tech guy for the Cessna Pilots Association, Ells has flown and wrenched on a wide range of aircraft. He owns and wrenches (a lot!) on a classic Piper Comanche. But don’t hold that against him.