Recapping the previous (and first) installment of this build series from the July issue, remember that we had just driven to the RANS factory in Hays, Kansas, toured the facility, flown the S-21 and, over delicious pub food, made the decision between us to commit to the project. Waking up the next morning, we were filled with anticipation of what the day would bring. We had the full day to spend if needed and started by calling Michelle (Shelly) Schlitter to see if an appointment was necessary to come in and chat about purchasing the RANS S-21. No appointment necessary, she said, come on down.
We were prepared with checkbook in hand and many questions to be answered. We sat with Shelly for about 45 minutes, going through all the specifications that we wanted on the plane, and finally Mike got down to the desire to have a Lycoming engine with a constant-speed prop. That’s when the big gun was called in: Randy Schlitter, owner of RANS, came to talk to Mike about the engine choice. Randy thought it was a very doable combination. While the S-21 started out with the 100-hp Rotax 912, it was eventually fitted with a 180-hp Titan engine, though that airplane wasn’t flying during this negotiation. Clearly, Randy had plans for the S-21 to grow from the beginning.
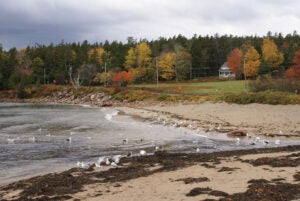
Not only that, Randy just happened to have a Lycoming IO-320 on the factory floor he wanted to show Mike. It was an engine that he had gotten 20 years prior, originally on the wing of a Piper Twin Comanche. It had been overhauled at Aero Sport Power and pickled for storage. Randy was planning to use it someday, but just never had gotten around to it, and offered it to us at a reasonable price. Mike ran the concept by me and showed me the engine, getting pretty excited about it—an engine sitting on a wooden pallet covered up and nicely stored. I wasn’t too hot on the idea—mostly due to my lack of knowledge about airplane engines—so we decided to put off this decision.
Lucky 71
We were #71 in the purchase of the RANS S-21 Outbound. Because RANS had great sales at Oshkosh that year, interest in the model had ramped up dramatically. In the realm of good problems to have, RANS did not have production capacity to keep up with the orders. More specifically, they could not build fuselage frames fast enough.
We wanted to get started, so we agreed with Shelly to accept shipment of the tail kit first, then the wing kit, followed by the remainder of the kit when available. The initial estimate of getting the tail kit at that point was the beginning of December—and remember that we were there in August. Shelly gave us her best guess regarding the fuselage, careful to stress that it was an estimate not a promise. That time frame? Spring! At that point we just wanted to get building as soon as possible, so we agreed to those shipping terms. There were no surprises with the price and it was within our budget, so Mike and I decided to pull the trigger. We settled on timing of payments for the various kit subsections and it was a go!
We had just committed to our build with more than desire. We had money in the game! We started the long trek home soon after our purchase and made it all the way to Glenwood Springs, Colorado, that night and the rest of the way home to northern Nevada the next evening.
Engine Decisions, Still
With all that driving time, we were able to discuss the concept of the used, overhauled Lycoming IO-320. Mike was able to explain to me that a “used” engine is not bad for an airplane. In fact, it’s a proven product and, with the overhaul, it was as good as new. There was a bit of skeptic inside of me still—I wanted to talk to other resources at the airpark when we got home before the final decision was made on the engine. Something about putting a used engine in a brand-new airframe just didn’t settle with me.
In any case, it wasn’t a decision we had to make right away. There were many things to take into consideration before the first box was to arrive four months down the line. Money was budgeted and within our reach, but spending had to be tracked closely, mainly due to cash flow, making sure we had enough money at the right time.
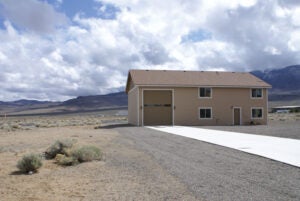
Build space was the next big consideration. We had the newly constructed 40×56-foot hangar that included a 27×12-foot workshop directly off the aircraft space, which itself measured 30×40 feet and was holding the Cessna 172. One more sliver of space, 40×17 feet, was where we’d stored our non-airplane RV. But we’d sold the motorhome to generate some cash for the S-21 purchase, and this freed up this space for storage of the boxes and staging the S-21 parts. It’s really beneficial to have a separate “warehouse” and workspace.
Even though we’d allowed for the space needed for a build during construction of the hangar, the space was still raw. Comfort was next on the list, so Mike put in an office and bathroom, insulated the walls and ran electrical and hookups for a natural-gas wall heater. (This is high desert northern Nevada, after all.) After that, of course, came the drywall. We hoped it would make a great, comfortable area for the build—one that we would want to inhabit during the build.
About Those Tools
Tools are another big consideration for the build. Mike is a person who has so many cool tools (and multiples of them), so this was not really too much of an issue. We did have to purchase hundreds of Clecoes—and then we ended up borrowing many, many more—and we also borrowed a pneumatic rivet puller and fluting pliers. Organization of those tools in a workable area was the biggest issue. Mike and I planned the hangar organization together because I wanted to be able to know where things were. Recall from the previous installment that Mike’s inherent organizational systems make total sense for him but not so much for me.
First, we separated out all the non-airplane items—camping gear, automotive, recreation, RC planes, etc.—and put them on storage racks on the edge of the main build/staging area. We also purchased four extra-tall roll-around storage racks for when we got the plane parts to organize and separate them. We also had three short roll-around carts for immediate-need items in the building space. When we were at the factory, we saw them using the concept of having the small parts stapled to a wooden board to use at the time of building that section they were working on. Both Mike and I liked that idea, so we had a wall in the workshop designated for that purpose.
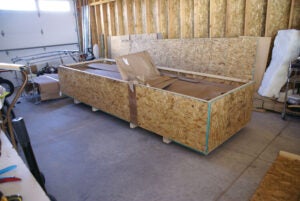
Next was the idea of a large flat table to do the work on. We had nothing of that nature, but Mike had the idea already worked out in his head! He remembered seeing plans for the EAA 1000 workbench on the Van’s Air Force website and built a worktable adapted from them (see the sidebar below). The table fit nicely in the middle of our workshop and gave us enough space to walk around the entire table. It was extremely sturdy and flat! A huge plus of this design is the shelf under the worktable, which allows for ready placement of current-need parts and supplies depending on what the project of the moment would be. We also had enough room to put a folding 6×2.5-foot table in there, providing extra “flat space” for the build manuals and for me to log the progress on the build. We were as prepared as we could be.
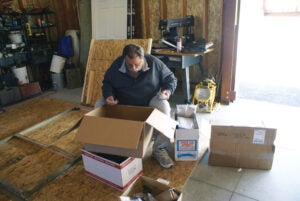
Time passed and December was coming rapidly, and we were really excited. We had many discussions regarding getting our kit and the timing and cost of getting it shipped to us in pieces. We made a decision that it would be better for us if we changed plans. Rather than wait for crates to arrive over time, we wanted to go to the factory and pick up the kit ourselves. It may not seem so, but doing it this way was actually less expensive overall, and it gave us a bit of an adventure at the same time. Shelly Schlitter estimated that we would be able to pick up the entire kit around the end of February. In the end, we felt making the trip ourselves would be better, even if it meant delaying the start of the build by a few more months. Plus, in the meantime, I had talked to enough resources about the Lycoming engine still being offered by Randy that I was finally convinced that it was an option for this plane. The engine would be part of the pickup plan in the spring, too!
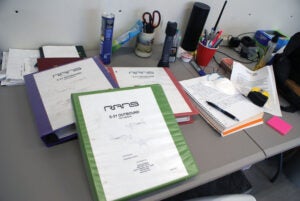
Still Organizing!
Now that we had more time before we could start work, nothing, not even a vacation to the northeast, distracted me from trying to get us even better organized. I ran the manual PDF files over to Staples to be printed out on three-hole paper and got notebooks for each of the manuals (text, parts and figures). Because a big part of my role was to be the organizer, I needed paper manuals to check off and date the steps as we built.
Mike had been poring over the manuals since we made the decision to build and was getting familiar with how he wanted to approach it. I was great at organizing the manuals, but when it came to reading them and making sense of the details of how things come together, it was pretty much Greek to me. I would read and reread and had no idea what I had read—this was going to be a challenge! The videos posted to the RANS website walking through different portions of the build proved to be a lifesaver to my comprehension of how things should come together. I tried not to get too anxious about it during the waiting period; I knew Mike had a handle on it and relied heavily on that to get us through!
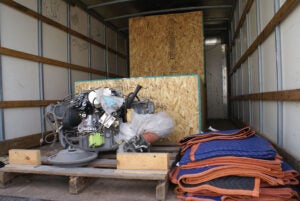
Spring was around the corner and toward the end of February, Shelly let us know that the pickup date needed to be moved back to the end of March. We agreed to be there by March 27 and made one-way airline reservations to Denver and reservations for a Budget rental truck with a 16-foot bed for the trip back. Despite all the work at home, the study and research, it seemed unreal that we actually had a date and could make plans for pickup!
Getting the two large boxes that contained the kit into our rented truck was a bit like a Tetris game. With a bit of creativity and slight modification to the height of one of the boxes, everything finally fit. With everything strapped in place and secure, we were on the road headed for home by 10 a.m. the same day. Weather was kind to us (no snow) and we were home by 7 p.m. two days later.
More Magic
Next feat of magic, one that had been long awaited, was the unload! Several of our neighbors and friends arrived ready to assist in the process. A neighbor had loaned us a forklift, and with many helping hands we unloaded the engine and two giant boxes full of plane parts and put them into the RV parking area of the hangar. On the long ride home, Mike and I discussed where we wanted to place the boxes and engine once we arrived—it was just a matter of juggling the items to get them into position so that when it came time to inventory, we would be ready to hit the ground running with little lost motion.
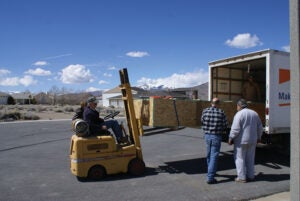
The RANS manual stresses inventory. Strongly. In the most serious terms, no less. So that is what we did. The following morning, we started the long process with the assistance of two of our neighbors. It took four people two and a half days to complete the entire inventory on the kit. While I kept an eye on the inventory and watched to see how our organization was going to work out, you would have thought it was Christmas for Mike. Like a grown-up kid, he dug through Bubble Wrap, brown paper wrapping and cardboard boxes to find treasures. It was quite the experience to witness. As Mike or one of the helpers would identify a part, I would use a pink highlighter (an old habit from my nursing days) to cross out an item done on the inventory sheet and then “pink out” the tag on the part so I knew it had been inventoried. Then I’d direct that person to the appropriate area to put the item. I organized the parts according to function: wings, tail, fuselage, firewall forward and finishing kits. Each area had a large plastic bin for the smaller parts.
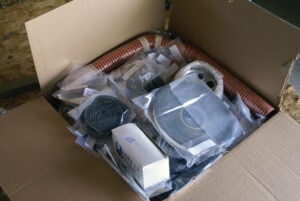
When it came to the large parts, mainly the skins, we put them back in the crate after inspection so they could be stored flat and safe from potential damage. Several times during the process, Mike would get caught up with analyzing the parts and how they were going to come together—the conceptual thinker-side of him that I previously mentioned. I knew it probably slowed us down, but I had to give him his joy. Several times, he commented on the excellent quality of the parts. “Randy didn’t skimp here,” he said often. When the entire inventory was complete, only six items were missing, four of which were on backorder and we knew we would not find. We quickly let Shelly know about the discrepancies in our inventory and the parts were shipped. There was no problem at all getting the missing parts. Huge kudos to the RANS staff for taking care of their customers!
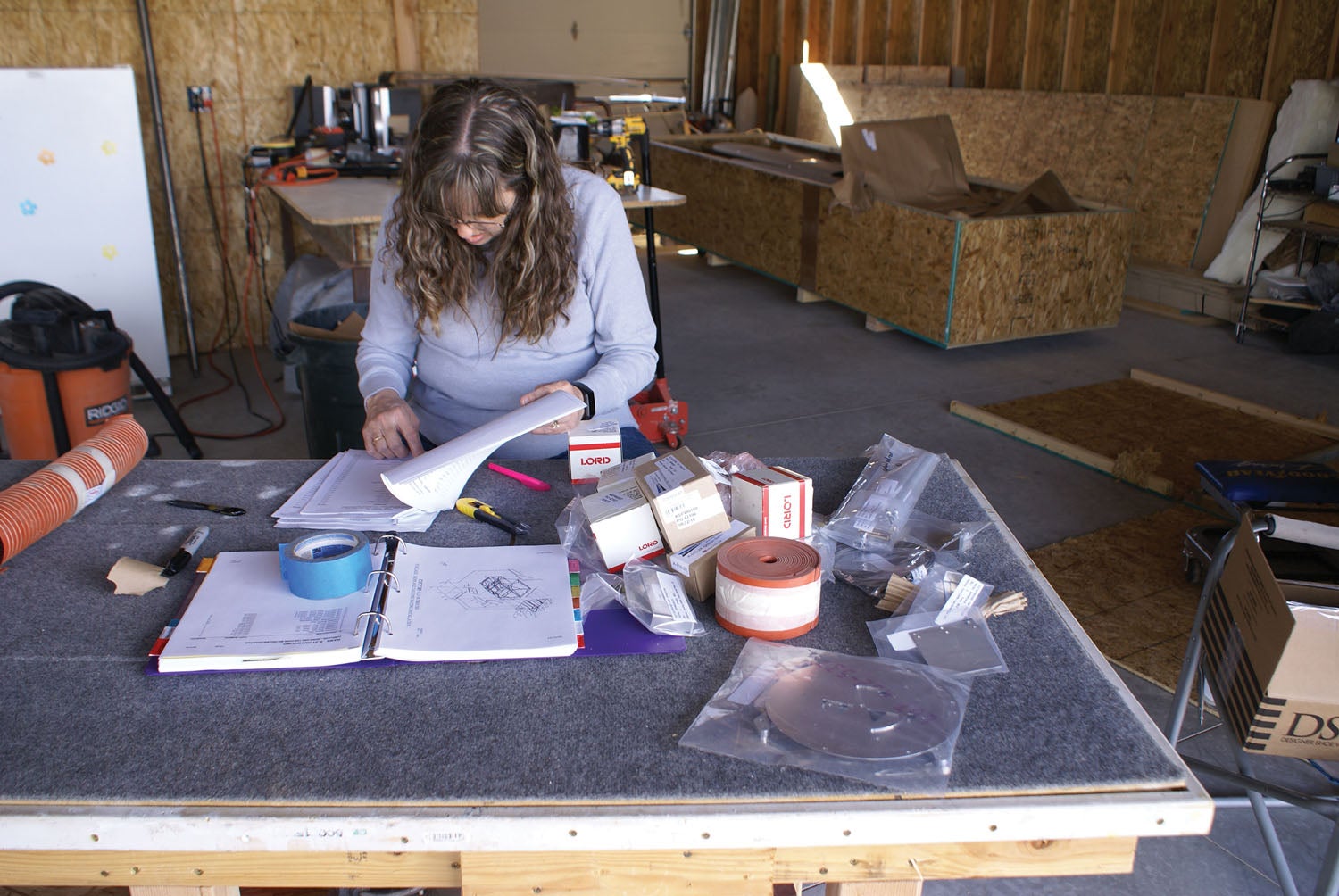
Yes, there’s still so much to do and to consider. We obviously need to get a propeller, decide on the avionics and lighting as well as the other bells and whistles that we may want. But those decisions can come later. As we concluded our inventory and refined our storage and work spaces, it dawned on me that this had already been an exciting and exhausting process. And we haven’t even begun to build. But don’t worry. We’ll start on that next month.