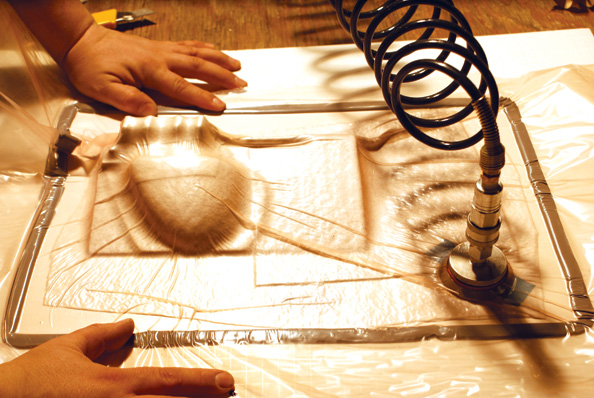
Over the past month you have had the chance to absorb the basics of vacuum bagging, so to speak, and might even have undertaken some independent research on the materials you’ll be using. Thats great. In this installment, you will learn the basic process of actually applying vacuum pressure along with how to check to make sure that you are getting the required pressure with no leaks in your bagging system.
Sealant tape is placed around the perimeter of the part with room for vacuum- bagging materials. This is a piece of a 737 aileron trimtab, used because of its extreme contours.
Preparation Is All
Let me say that again: Preparation is everything with composites in general and vacuum bagging in particular. Imagine for a minute that you are laying up your composite part in the mold. Once finished, you are ready for your bagging materials, but you still have to cut them out, place them into the mold or seal the bag. How much time do you have left before your part has cured too much to allow the benefits of applying vacuum to it?
Ah, yes. Now you see why having all the components ready to go before committing to the layup is critical. Normally, the first step in the process is to clean the surface. Even though the sealant tape is sticky, it will not adhere to a surface that has any wet resin, grease or oils.
The overlap of the beginning and the end of the sealant tape.
Place sealant tape around the perimeter of the surface to be inside the vacuum bag. This step can be both easy and difficult. It is important to leave the protective backing on the tape until you are ready to place the bagging film onto it, and then firmly place the tape in one corner of the area to be inside the bag. Roll the tape out onto the mold surface, pressing down on it to ensure a positive bond. When you reach a corner, place your finger in the corner, on top of the protective paper, and pull the tape in the new direction you want it to go. This should tear the paper and make a bend in your sealant tape. When you get back to your starting point, you will want to overlap the sealant tape ends and firmly press the upper piece of the overlap so that there is no possibility of leaks where the two ends meet. Remember, you will always want to leave enough room to place your materials into that area plus a little extra to place your vacuum port.
The overlap of the sealant tape shown from the other side. It is important to make sure that these ends are firmly pressed together to prevent leakage.
Begin cutting the vacuum bagging materials to fit the part you are working on. For this you will want to start with the materials in the order in which they go down in the bag. Fluorinated Ethylene Propylene (FEP) is first. Cut the FEP so that it extends past the resin impregnated area by an inch on all sides, but remember that you might need to add a little more to compensate for the thickness of the part. This will of course need to be compensated for on all of the materials if it is required. The next material to be cut is the peel ply, and you will want to cut this material one-half inch to an inch bigger than the FEP. This will allow any bleed out resin to be soaked into the peel ply and bleeder.
Following the peel ply is the bleeder material (if required), and it can be the same size as the peel ply or slightly larger (about a half inch). The silicone material can be cut to the same size as the bleeder so that any resin underneath it will have pressure applied to it and give a smooth finish. Next is the breather, and it is a little different. When preparing the breather, you must try and overlap the silicone by 2 inches on all sides plus a little extra where the vacuum port will be going. (As one of the last steps, you will put the vacuum port on top of the breather off to the side of the part.) The final piece to be cut is the bagging film, and it should be large enough to cover the area and the sealant tape plus 2 inches on each side. This will give you a little extra if the stack up gets a little off center.
Preparation of the vacuum bagging materials. The breather material is being cut to size.
There are just a few other items that need to be mentioned. Always ensure that your vacuum port (both pieces) is close by so that you don’t have to go looking for it. In the past I have been ready to go and forgot that I used all my vacuum ports on other projects and no ports were available-a big problem when your resin is curing! Also, try to remember to place your vacuum bagging materials in the order that they will be on your part. The first material is on the top of the stack so that you don’t have to go through all of your materials to get to the material you need.
Another thing I would recommend is to consider the shapes and contour of your part. Is your part thick or does it have square edges that could puncture the bag? Does it have a core that could be crushed under vacuum on the corners if not prepared right? We will talk about how to deal with sharp edges and how to eliminate core crush next time.
A different view of the preparation of the breather material.
Flash Breaker Tape
We have not yet talked about flash breaker tape. Its a thin Teflon heat-resistant tape that will not allow anything to stick to it on the non-adhesive side. It is used primarily in areas where any flash (excess) resin may come in contact with it, and it allows the tape to be removed without wrecking the part. Use this tape to secure the edges of the materials (FEP, peel ply, bleeder, silicone and breather) so that they cannot move while they are being stacked in place. You may also use this tape where you don’t want excess bleed out resin (flash). Be careful not to place it where it could affect the flow of resin through the material.
Trimming the FEP to size.
The FEP is an interesting material. When you place it onto your part, it will not want to form over any kind of a contour, but it will stretch a little. This will allow you to form it over small contours, but if your part has large contours, you will have to make relief cuts in your FEP to accommodate them. If you dont, you will end up with pleats that will cause problems such as bridging in your cured part. Bridging is when the materials being applied do not lay directly on the surface beneath. Here we are talking about the resin impregnated part and the FEP. The result of this bridging is a buildup of resin in the bridged area, which creates a resin-rich pocket that could one day crack or create a stress point in your part.
Make sure that the silicone caul plate material fits into position.
Pleating is a buildup of material that will fold over under pressure, and the result is an uneven pressure over the entire surface that can cause veins of excess resin that will have to be removed if possible. There is also the potential for doubling over of the FEP, which is when there is too much FEP and you have to fold it over on itself or cut it. Make sure that a single layer of FEP is tight to the impregnated surface so that there isn’t a buildup of excess resin and the resin can bleed through the appropriate holes.
Peel Ply and Bleeder
Once the FEP is placed and is as tight as possible, put down the peel ply. The peel ply is a Dacron-style fabric and will not sit down on the part like the FEP will. You must make relief cuts to get it to lay down, and you will need to be careful that there is not too much overlap in the areas cut. If the edges overlap too much, this will soak up more resin and could possibly cause some starvation. Peel ply also acts as a bleeder, so it will soak up resin until saturated.
Flash breaker tape is an important material when vacuum bagging. It holds materials in place and protects areas from excess resin.
Next, lay down your bleeder. There is nothing complicated here, as most times we use fiberglass as our breather and it tends to lay over contours easily. If you run into a problem laying down the fiberglass, cut and lay your fiberglass over the contour on a 45 angle. You may want to use flash breaker tape to secure it from moving around during the bagging process.
Caul plates are another matter. Often, if the mold is built by someone with experience, there will be alignment pins. If there aren’t any, line up the mold carefully to achieve a flawless part-and be careful not to disturb it. A silicone caul plate is easier because of its flexible nature. You can lay it down over the part and the materials with no complications. The silicone may shift during the bagging process or during the removal of the air from the bag, but taping the edges will eliminate this problem.
Use flash breaker tape wherever you think you may need it to hold your material in place, but remember not to place it where it may interfere with the flow of resin.
Take a Breather
When planning your breather material, always remember to think about where vacuum is required for even vacuum pressure. In most cases you will want to cover the entire area under the vacuum bag or within the confines of the sealant tape with breather. This is a good way to ensure that the vacuum bag will suck down evenly over the entire part.
To place and connect the vacuum port simply position the base of the port in the location that you have determined and place the bagging film (we will cover this in the next step). Using a knife, make a small slice that is the same width of the hole in the base of the vacuum port. Then place the sniffer or upper portion of the vacuum port in the hole and give it a quarter turn until you feel it lock into place. Sometimes this will not be a positive clicking feel but instead will be a firm resistance against turning it farther.
Fit the breather into place over the extreme contours of the part. You may need to make a final trim of your materials as you proceed.
Be careful that no pleats or tears are created under the two mating surfaces as these will result in vacuum leaks. If you do happen to get pleats or tears, don’t worry! They can easily be fixed. If you have pleats, simply undo the vacuum port and remove the pleats, then reconnect the two halves as before. If you end up with small rips or tears in your bagging, undo the port and smooth the film out. Place a piece of flash breaker tape over the tear and press it down firmly for good adhesion.
Well, you’ve made it to the step that can either make or break your project. From here things need to be done precisely and quickly. Depending on the vacuum bagging film that you are using, there are different ways of laying down the film, especially when the part stands off the mold surface or has many contours. There are different kinds of bagging film, and most have a certain amount of stretch that will make it easier to work with.
Start pulling the protective paper off the sealant tape as you get ready to place the bagging film.
Place one corner of the bagging film to one corner of the mold and sealant tape. Of course, before you do this, you will want to make sure that the bagging film lines up with your sealant tape area on the mold. Once the corner is down and you have pressed it firmly against your sealant tape, continue to lower one edge of the bagging film down onto the sealant tape for that edge, running your finger behind (on top of the bagging film) and pressing down onto the sealant tape. Do not continue around the corner and continue placing your film-this will cause grief when you get to the end. Instead, pull the film over your part lightly and do the same procedure on the parallel edge of the mold. Once those two edges are complete, then you can move on to one of the perpendicular edges and do the same procedure. Finally, move to the last edge and complete your vacuum bag.
Before placing the bagging film on the sealant tape, make sure that you have enough bagging to follow the contour of the part. If you dont, you will have a problem with bridging. Run your finger along the bagging film, using firm pressure for a good seal.
Once the vacuum pressure is applied to the vacuum bag and there are no leaks in it, you should see the air being pulled from the bag and the shape of the part should become partially visible. With the stretch in the bagging film, it should lay over the moderate contours of the part without much bridging. If there is mild bridging, then you can lightly press the bagging film to encourage it to go down. Be careful, as too much pressure can puncture the bag.
Check the Seal
Make sure all the edges are stuck firmly to the sealant tape under the vacuum-bagging film. Do this by running your fingers on top of the bagging film while pressing down firmly onto the sealant tape underneath. You may see air bubbles caught between the sealant tape and the vacuum bagging film, and you’ll want to work these out with your fingers by pressing the bubble out to the side of the sealant tape. If this is too difficult, listen in that area to determine whether there is any kind of hissing that would indicate a leak. If there is, you must continue to work the bubble out.
Ensure that you have the vacuum pressure you want for your project. This is good vacuum pressure at 21+ inches Hg.
The last step in your journey is to check the seal by testing the leak rate of the vacuum bag. This can be done by removing the vacuum hose from the vacuum port (once all of the air has been removed from the vacuum bag). If there is good pressure, the bag should be hard to move with your fingers.
Is it possible to run a vacuum bag with a leak? Yes, depending on how big the leak is. A good general rule is that if the bag is under pressure and you can get 19 inches Hg, then run it with that pressure. In the next article we will cover the common vacuum-bagging problems and how to efficiently troubleshoot them. Until then, keep your hands clean and your eye on the clock.
Watch critical areas for any sign of problems. In this case, make sure that the fitting does not puncture the vacuum bag.