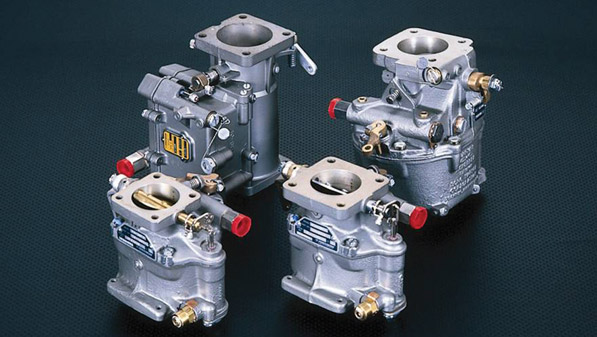
This month, we will turn our attention to the engine compartment and take a look at an all-too-common reason for propellers to stop turning in flight: carburetor ice.
In our initial flight training, we are all taught about the hazards of carb icing, and how to detect and prevent it. Virtually all trainers in the general aviation fleet have carbureted engines, and students are taught to check the carb heat during runup, and to make sure to employ carb heat during reduced-throttle operations such as descent and flying the pattern.
In spite of this training, carburetor icing is still the cause of in-flight scares and engine-failure accidents. Unfortunately, carb icing as a cause of an accident is difficult to definitively prove. By the time an investigator gets to examine the engine in the aftermath of a mishap, the ice has had more than enough time to melt, leaving no physical evidence of its presence. It is common to see NTSB accident reports that attribute accidents to loss of engine power for unknown reasons, also noting that weather conditions at the time of the accident were conducive to carburetor icing. The implications are clear.
Symptoms and Detection
Carburetor ice continues to be a problem for two primary reasons. The first is that most pilots are not as aware as they should be about the atmospheric conditions most conducive to carb ice. When we think of ice we tend to think of cold temperatures, at or below freezing. In fact, carb ice is much more likely when the ambient temperature is well above freezing (40 to 60 F) and the relative humidity is high (above 40%). In some systems, carb icing can occur at an ambient outside air temperature as high as 100 F when the humidity is between 20% and 40%. Also, pilots are trained to think about carburetor icing when operating at reduced power, as is the case for descents and flying in the pattern. They are much less aware of the potential for icing at cruise power.
Early this year, I experienced such an incident while flying on a bright, clear California morning. While the ice buildup did not cause a complete engine failure, it did cause my engine to run rough enough that I made an immediate precautionary landing (with the carb heat on full) at the nearest airport. At the time my engine started to run rough, the OAT was 65 F.
The second reason carburetor icing continues to be a problem is that the onset of icing is gradual, and the signs are subtle. To the pilot, carb icing shows up as a gradual loss of power (either rpm or manifold pressure, depending on whether the prop is fixed pitch or constant speed). Because the onset is gradual, it is easy to miss, particularly if there are other things going on such as maneuvers or power changes that tend to mask the slow degradation of engine power. When the ice builds up enough, the engine will begin to run rough, and if carburetor heat is not applied, it will eventually quit.
Applying carb heat will melt the ice out of the carburetor and restore the engine to full power, provided there is enough heat available to do the job. This is one of the reasons it is important to apply carb heat promptly if you suspect ice. If the engine quits, or if it cools off too much due to reduced power, there may not be enough heat available to clear away the carb ice.
Another symptom of a carburetor-icing situation that can get a pilot in trouble is what happens immediately after heat is applied to an iced-up carburetor. As the ice melts, the water is sucked into the engine. This will often cause the engine to run even rougher immediately after the pilot initiates carburetor heat. Some pilots respond to this increase in roughness by turning off the carb heat. This is a mistake that will allow the ice to re-form and choke the engine. If the carb heat is left on, the engine will regain power after the ice has finished melting away.
What Causes Carb Icing?
The way carburetor ice is generated is very different from the way ice accumulates on the exterior of the airframe. This difference is why carb ice tends to form at significantly higher ambient temperatures than airframe ice.
Airframe ice occurs when supercooled droplets of water hit the cold surface of the airframe and freeze. In order for airframe ice to form, the OAT must be cold enough to promote freezing of the moisture in the atmosphere. For carburetor ice, the critical temperature is not the ambient OAT, but the temperature of the air flowing through the throat of the carburetor.
The carburetors job is to mix fuel and air and feed this fuel/air mixture into the engine. Ideally, the fuel should be vaporized or in very small droplets, and well mixed with the air when it enters the cylinder. The carburetor also serves as the primary power control. The butterfly throttle valve in the carburetor throat regulates how much fuel/air mixture is admitted to the cylinders to be burned to produce power. As we will see, in addition to being a fuel/air mixer, a carburetor is also a remarkably effective refrigerator.
In the throat of the carburetor is a venturi, which is a contraction in the airflow path. The reduced cross-section of the venturi forces the air to flow faster through it, and causes the air pressure to decrease. This low pressure draws fuel into the carburetor throat through the jets, where it evaporates and mixes with the air. At partial throttle, the pressure of the flow through the carburetor drops even more as it flows through the area restricted by the throttle valve. Both of these processes reduce the temperature of the air/fuel mixture.
Adiabatic Cooling
A volume of gas under adiabatic conditions has a constant total energy. If no heat is added to the gas by an outside source, a change in velocity will cause a change in pressure, which will in turn cause a change in temperature to keep the total energy of the gas constant. In the case of the air flowing through the throat of a carburetor, the velocity increases, and both the pressure and temperature decrease. Even if no fuel were added to the airflow, this adiabatic cooling would drop the temperature in the carburetor throat below ambient.
Evaporative Cooling
When the fuel mixes with the airflow in the carburetor, it evaporates. This evaporation process is endothermic, which means that the fuel absorbs heat from the air in order to evaporate. This drops the temperature of the fuel/air mixture. The temperature drop caused by fuel evaporating can be quite large. Mixing gasoline with air at an ideal mixture ratio will cause a 40 F drop in the temperature of the air. Alcohols can produce temperature drops of hundreds of degrees. If we look at the numbers for gasoline, we can see that evaporation alone can cool incoming air at 72 F to freezing.
Mixture has some effect on this. The more fuel there is to evaporate, the more temperature drop there will be. Leaning the mixture at cruise somewhat reduces the chances of carb ice in cruise, but does not eliminate it.
When we combine adiabatic cooling and evaporative cooling, we can see that the temperature in the throat of a carburetor can drop to freezing even when the ambient OAT is quite warm. If this happens for a prolonged period of time, the metal of the carburetor body and throttle valve will get cold enough to freeze any moisture droplets that are in the incoming air, and ice will begin to form. As the ice grows, it will restrict the airflow through the carburetor throat and cause loss of power. If the restriction is severe enough, the engine will stop running.
Fuel Injection
Fuel-injected engines are less prone to induction-system icing than carbureted engines, because the fuel is not evaporated in the throat of the induction system. It is possible, however, for adiabatic cooling to cause an injected engines induction system to ice because of the pressure drop around the throttle valve.
Throttle-body injectors are halfway between carburetors and true fuel injection. The fuel is introduced near the throttle valve, but there is no venturi to cause a pressure drop. These systems can still ice up, primarily because of the evaporative cooling produced by the fuel.
Detection Instruments
There are currently two types of instrumentation available to help pilots avoid carburetor ice problems. Both of these systems help to provide a direct indication of carburetor ice potential, rather than relying on the pilot to detect a subtle change in power.
The first system is a carburetor air temperature (CAT) gauge. This is essentially a thermometer that takes the temperature of the air in the carburetor throat and provides an indication to the pilot. The CAT gauge typically indicates temperature in degrees Celsius, and has a colored (usually yellow) arc indicating the range of temperatures where icing is likely. The pilot can use the carburetor heat to keep the carb throat temperature out of the icing range.
In recent years, a second system has been developed that detects ice directly and sounds an alarm when ice forms. These systems use an LED and a photocell in the carburetor throat. The photocell detects the light from the LED. When frost or ice begins to form, it reduces the light getting to the photocell, and the alarm and warning light in the cockpit are triggered.
Both systems have their advantages and disadvantages. The primary advantage of the CAT system is that it lets the pilot prevent ice from forming in the first place. Its primary disadvantage is that the pilot must routinely check CAT to make use of the information.
The alarm has the advantage of providing a direct warning of unexpected carburetor icing. Its primary disadvantage is that it only becomes active after ice has actually started to form, so it is harder to use as a prevention aid. Either system will provide a valuable improvement in the safety of airplanes with carb-ice-prone engines.