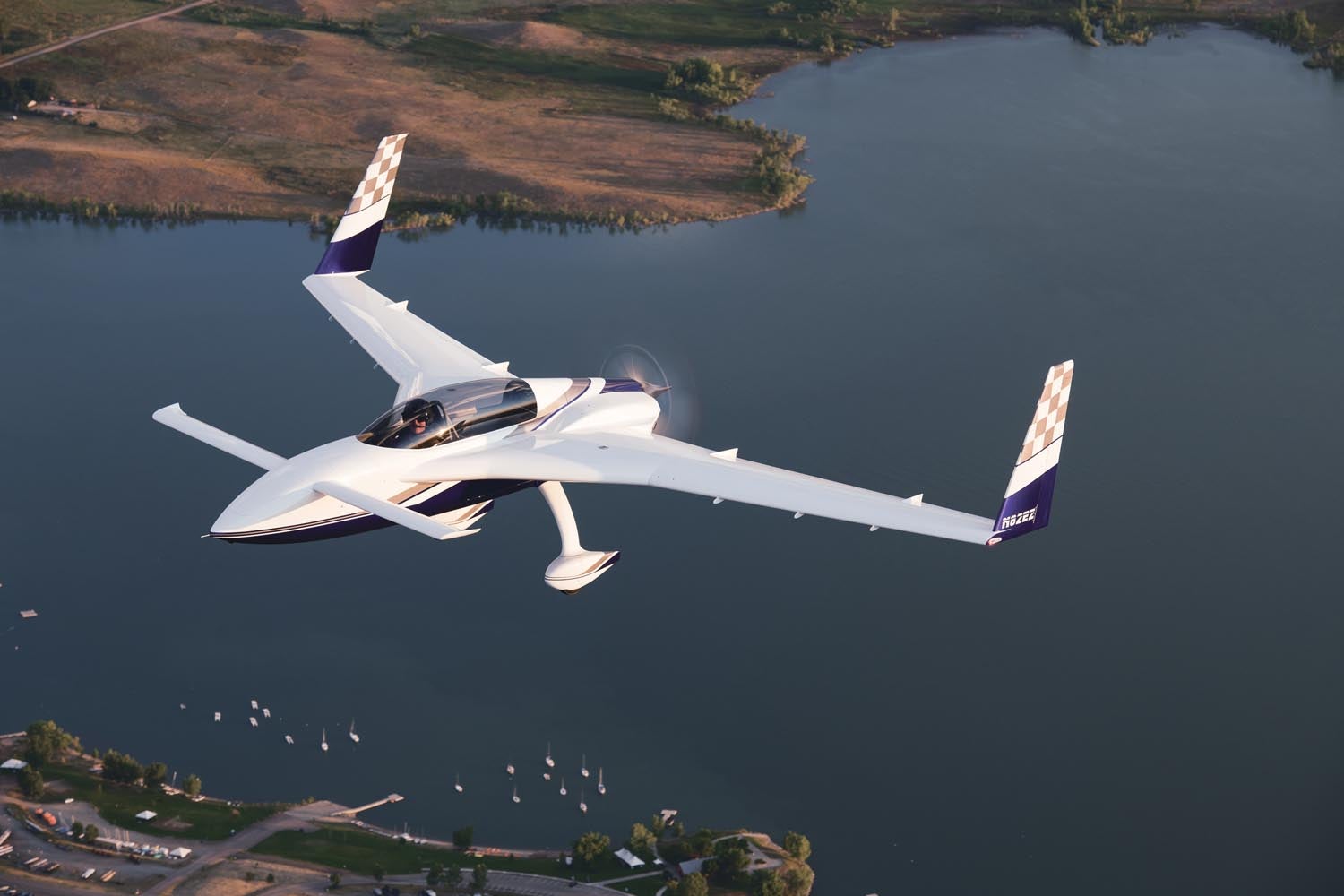
A designer must make a large number of decisions in the process of designing an airplane. These range from top-level decisions, like the overall configuration or structural materials, to detail decisions about each system and component of the airplane. The overall goal is to produce a design for a machine that works well and performs its mission effectively.
In addition to the performance of the completed machine, the designer must consider the cost of materials and components and how the parts of the airplane will be manufactured. A designer must weigh two propositions when making these decisions:
First, conventional practice is conventional because it works. And second, innovation can be the path to something better than what can be achieved with conventional practice. This is not an easy decision to make.
Every step between the Wright Flyer and modern airplanes started out as an innovation. On the other hand there have been many wrong turns and failures along the way.
The dilemma is that, while innovation can produce a better or more cost-effective design, innovating also introduces a significant amount of technical risk into the project. At the core of this problem is the newness of the innovation. It is less well-understood than the conventional approach. There is less experience and data available to guide the design, and there may be undiscovered problems or drawbacks to the new concept.
Because of this, it’s important to realize that even though it is very common to see designs advertised and praised for being innovative, innovation is not a virtue in and of itself. “Innovative” is another word for “different.” In order to be a virtue, the innovation must provide a meaningful advantage over a conventional design.
Important Questions
For any innovation, a designer should consider the following questions:
In what way will this concept make the airplane better than a conventional one?
Consider how the innovation is expected to improve the airplane. Will it improve performance in an area that is important to the user of the airplane? Will it reduce the cost of building, owning or operating the airplane?
If there is no meaningful improvement in anything important to either the manufacturer or end user of the airplane, then the innovation is not of any value and should be dropped.
If there is potential for improvement, then ask:
If the innovation works as well as it could, how much improvement does it offer at best?
Every innovation adds risk to the project and, even if it ends up reducing costs in the long run, it could significantly increase the cost of engineering it properly the first time. Because of this, the decision to use or drop an innovation comes down to a trade between the value of the improvement it can provide against the increase in risk and, potentially, cost.
The designer must determine if the overall benefit of the innovation is large enough to merit undertaking the additional effort needed to address the technical risk it adds.
It’s also important to consider all aspects of how the innovation affects the airplane. This is particularly true of major structural and aerodynamic configuration concepts.
What is the purported advantage of this concept, and even if the advantage is real, is there an offsetting penalty that reduces or eliminates the advantage?
A very common mistake is to look at the positive only and not consider the negative. One example of this is canard configurations.
When the modern canard concept first appeared, two advantages were claimed. First, that trimming the airplane with an up-load on the foreplane rather than a down-load on a tail was more efficient. And second, that the canard configuration packaged better than an aft-tail configuration, making the fuselage lighter and reducing drag.
Neither of these claims is false in and of itself, but there were offsetting negatives. A canard configuration cannot trim powerful high-lift flaps, and although the fuselage of a canard airplane is shorter than that of an aft-tail airplane, the short moment arm for the vertical fins means that the fins must be larger to provide adequate directional stability. Both of these factors offset the advantages of the configuration. While there are successful canard airplanes that work very well, the overall advantage of the canard configuration proved to be much less than an assessment based only on its positives would suggest.
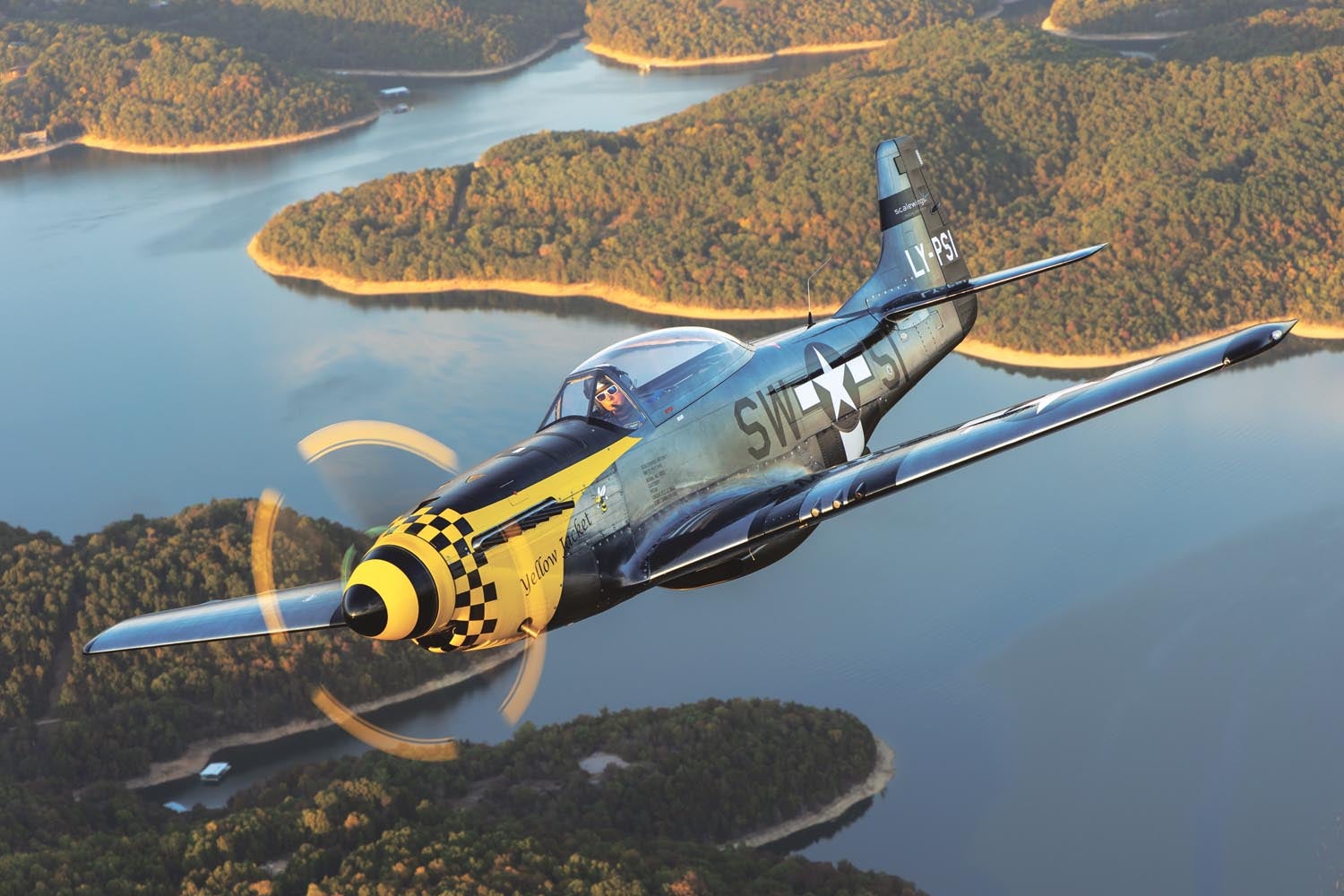
Composites followed a similar trajectory. The strength-to-weight ratio of advanced composite materials is quite a bit higher than metals and offers the potential for lighter, stiffer structures. This proved to be true in practice, but because of several detail design issues with composites, the weight savings achieved was less than one might predict by simply looking at the relative physical properties of the materials.
If, after consideration of both positives and negatives, the innovation still appears to offer a useful advantage, there is one more major question to resolve:
How big is the risk and what is the alternative if the innovation fails to deliver?
As we have already seen, the task of making an innovation work is harder than making a conventional design work. This is because there is less body of experience, data and established design practice to rely on. The amount of engineering work needed to complete a workable design is greater because the design team will have to fill in all of the unknowns along the way.
At the outset of an innovative design, it’s known up front there are some issues the designers will have to work out. Sometimes, however, things pop up that they did not anticipate. These “unknown unknowns” are the most problematic since not only must they be solved, but the methods of solving them must be invented on the fly because the designers did not anticipate them. They are also a significant part of the risk because whether they are solvable was not considered at the outset, and there is a chance that one could prove to be a showstopper.
The designer must make the best assessment of the overall technical risk inherent in making the innovation work and consider whether the advantage offered by the innovation merits taking the risk.
Finally, the designer must consider what alternatives will be available to save the project if an innovation fails to deliver. How easy it is to change to a different approach or replace an innovative design with a conventional one differs widely depending on the type of innovation.
For example, a system that is self-contained and a relatively small part of the airplane is relatively easy to replace. One example is the use of modern high-energy-density batteries to save weight on emergency or backup power systems. As Boeing learned with the battery problems on the 787, these batteries can have significant issues with catching fire when they malfunction. When this problem cropped up on the 787, Boeing had to redesign the battery system and battery containment to eliminate the fire hazard. This cost some weight, lessening the advantage of the high-performance batteries, but did not severely impact the overall program or viability of the airplane.
On the other hand, if the airplane has an unconventional overall configuration, it is extremely difficult to recover if a fundamental flaw in the concept appears during development.
Summary
Innovative design can be the path to a better design, but it brings significant risk with it.
Innovation is not a virtue in and of itself. Unconventional or innovative concepts should have advantages that directly help in areas that are valuable to the manufacturer and/or end user of the airplane.
Innovate only where it can produce significant gains, and don’t pile multiple innovations on top of each other. Every innovation brings risk, so take that risk only where it gives the most leverage.
Sometimes, a conventional low-risk design is the best approach and sometimes it is worth taking the risk to innovate. The risk/potential trade is a fundamental discriminator between concepts and one of the most important things a designer must consider.
Photos: Jonathan and Julia Apfelbaum and Zac Heald.
My respect to you, Mr. Wainfan, as you are an amazing innovator yourself. Respecting every word you said, innovation is at the center of the beating heart of aviation and that needs to continue, with all the factors and prudence you recommended.
An overarching factor is that innovation needs to be ego-project-free, a cool level head, and flying even much more, which is why I dream to see the Advanced Qualification Program (AQP), with its preparation for emergencies, to be required for all General Aviation pilots. That would be an awesome innovation based on the most conventional wisdom to stay alive.
I was amazed when I learned many fiberglass airplanes were no lighter than an equivalent aluminum design. But they do have advantages in things like shape, skin smoothness, and more. But maintenance and repair of composites, or the effects of UV light, are other factors one must consider for example. But sometimes things are not always what we first think, and sometimes the tradeoffs are not worth it.
And sometimes, older proven methods are still better than people think or realize too.
Congratulations on the excellent article.
Words like “Innovative” and “ka:bnfaiba” (in Patey accent) turn on the clientele. Sales would rather gag experienced engineers to exploit this fetish.
When composites started getting popular, many builders adopted it since it didn’t require any high level sheet metal skills, or welding talent needed in other designs. But it turned out to be very labor intensive. Especially the scratch built designs like the Rutan composites. Some may have been attracted to the canard configuration due to it’s looks, while others wanted a buildable design they could do themselves, that just happened to be a canard. Almost no one is building with composites anymore, since it drags on for so many years/decades. The word is out.
I think the author has never flown a canard. A advantage not discussed is the canard resists a stall.
It was said virtually no one is working with composites, well, how about a Cirrus. Most jets use composites In their structures.
My composite Long Ez handles turbulence better than any metal airplane I have flown.
So, I do not agree with the author