Last month we discussed some of the basics of flutter and took a look at one of the more common flutter modes: wing/aileron flutter. This month, we direct our attention further aft and look at the aeroelastics of tail surfaces.
Buffet
It is common to see any aerodynamically driven oscillation of tail surfaces described as tail flutter. In fact, there are two distinctly different types of tail oscillation. Under certain circumstances, unsteady airflow over the tail can cause unsteady or oscillating forces that prompt the tail to shake. The source of the unsteady airflow can be components of the airplane that are upstream of the tail or flow separation on the tail itself. A common source of such tail shake is the separated wake downstream of the wing as it begins to stall, particularly on low-wing airplanes.
Tail shaking caused by unsteady airflow is called buffet. It is not a result of aeroelastic instability of the tail, and is not true flutter. Buffeting is undesirable if it is a steady-state situation in a normal flight mode such as climb or cruise. Buffet that generates a clearly felt aerodynamic warning to the pilot of an incipient stall is a good thing. While buffet itself is not tail flutter because it arises purely from the effect of unsteady airflow, it can sometimes set off flutter by exciting an unstable aeroelastic mode of the tail.
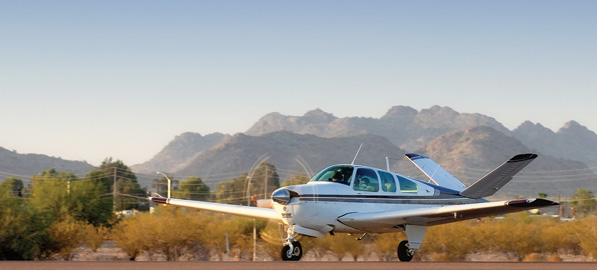
V-tail designs such as this Bonanza are especially sensitive to aft movement of the control surface CG, so much so that improper repainting could cause catastrophic failure.
Flutter
Flutter is caused by the changes in shape of the structure as it oscillates. Unlike buffet, the incident airflow is steady. The forces driving the oscillation are a direct result of the mode shape of the oscillation itself. It involves the interaction between two structural modes and the airstream. For the wing, the primary structural modes of concern are wing bending, wing torsion (twisting) and the rotation of control surfaces around their hinges. All of these modes are important for tail surfaces, but because the tail is mounted on the end of the tail cone, bending and torsion of the fuselage also come into play. While tails can exhibit flutter modes that look similar to wing bending/torsion flutter or wing/aileron flutter, modes involving either bending or twisting of the fuselage are also important.
Fuselage Torsion Modes
Fin/rudder: On most airplanes, the vertical fin and rudder are mounted so that the centroid of area of the fin and rudder are significantly above the centerline of the fuselage. Hence, the center of effort of any side force generated by the fin or by rudder deflection is offset significantly upward from the elastic axis of the fuselage, and any aerodynamic force generated by the fin and rudder cause the fuselage to twist. There is a flutter mode in which the natural torsional oscillation frequency of the fuselage couples with the natural frequency of the rudder rotation about the hinge line. As the fuselage twists, it causes the fin to roll about its root. The lateral acceleration of the fin causes the rudder to lag, generating side force that drives the roll. As the torsional stiffness of the fuselage arrests the roll and starts to drive it the other way, the rudder overshoots and lags again, and the cycle repeats.
Anti-symmetric elevator mode: Engineers understanding of flutter as a coupling between structural oscillation modes began in WW-I with an investigation into violent oscillations of the tail and aft fuselage of the British Handley Page O/400 bomber. On the O/400, the left and right elevators were independently connected to the cockpit control column by cables and were not directly interconnected at the tail. This setup provided control redundancy in the event of a cable failure, but the left-to-right elevator connection was soft, because the only things keeping them in formation were the control cables that stretched all the way up to the cockpit. This interconnect acted like a soft spring and allowed the elevators to flap independently when the fuselage twisted.
The elevators on the O/400 were not mass balanced, which is not surprising, as flutter was not understood at the time. The flutter mode that arose happened when the elevators lagged the fuselage twisting. They acted much like the rudder described in the example above. One elevator went up and the other down when the fuselage twisted, generating a rolling moment that drove the oscillation.
The solution was to connect the left and right elevators with a stiff torque tube. With this tube in place, the inertial forces trying to drive one elevator up and the other down resisted each other, and the net motion of the elevators in response to fuselage torsion was eliminated.
V-tails: On a V-tail airplane, the situation is similar to that of the elevators of the HP O/400 described above. The ruddervators of a V-tail must move symmetrically for pitch control and anti-symmetrically (one up and one down) for yaw control. Accordingly, the control surface of a V-tail are essentially independent, because the only constraint keeping them from moving relative to each other is the pilots hands and feet on the controls in the cockpit. The surfaces must move independently to control both pitch and yaw, so the option of a strong interconnect like that used on elevators is not available.
Although stiffening the fuselage torsionally during the design phase can help reduce the chance of fuselage torsion-related flutter modes, the primary defense against flutter for both rudders and V-tails is proper mass balancing.
Because the chord of the control surfaces on a tail is much longer than that of a typical aileron, the amount of mass balance required to protect against flutter is larger. Tail surfaces are also sensitive to mass behind the hinge line and the position of the center of gravity of the control surface. This sensitivity was illustrated by a series of flutter incidents on early V-tail Bonanzas, which experienced tail flutter at airspeeds well below the published Vne (redline) speed of the airframe. In several of these incidents, the airplanes landed safely because the pilots reacted by slowing down and applying control pressure, stopping the flutter. Once they were on the ground, it was discovered that the flutter had done extensive damage to both the tails and aft-fuselage structures. These incidents are in NTSB safety recommendation A-93-42, which describes the damage to one airplane thus: The entire empennage was loose, and the fuselage, particularly the right side forward of the stabilizers, was buckled from top to bottom and torn.
The cause of these flutter incidents was found to be changes in the mass properties of the ruddervators caused by repainting of the control surfaces. On some airplanes, the new paint was applied in thicker, heavier coats than the factory paint, and on at least one, the tail had been painted with the control surfaces still mounted on the airplane. This trailing-edge-down position caused some paint to run toward the trailing edge. The aeroelastic stability of the tails was so sensitive to aft movement of the CG of the control surfaces that improper repainting could cause a highly destructive, potentially catastrophic flutter.
Mass Balance
The purpose of mass balance is to move the CG of the control surface to the hinge line so that the control surface does not rotate when a motion of the structure the control surface is attached to moves the hinge line. For the mass balance to work, it must move with the control surface when the hinge moves. On an aileron, which is typically on the outer panel of the wing, placing the mass balance at the tip or the midpoint of the aileron usually works. For a tail surface, we need to take into account the way the tail itself is moving in response to fuselage twisting.
As the fuselage twists, the tail surface flaps around the elastic axis of the fuselage. If the mass balance is near the root of the tails surface, it will not be accelerated by the motion of the tail, and will be ineffective. In order to be effective against flutter modes involving fuselage torsion, mass balances should be at or near the outboard tip of the control surface.
Barnaby Wainfan is a principal aerodynamics engineer for Northrop Grummans Advanced Design organization. A private pilot with single engine and glider ratings, Barnaby has been involved in the design of unconventional airplanes including canards, joined wings, flying wings and some too strange to fall into any known category.