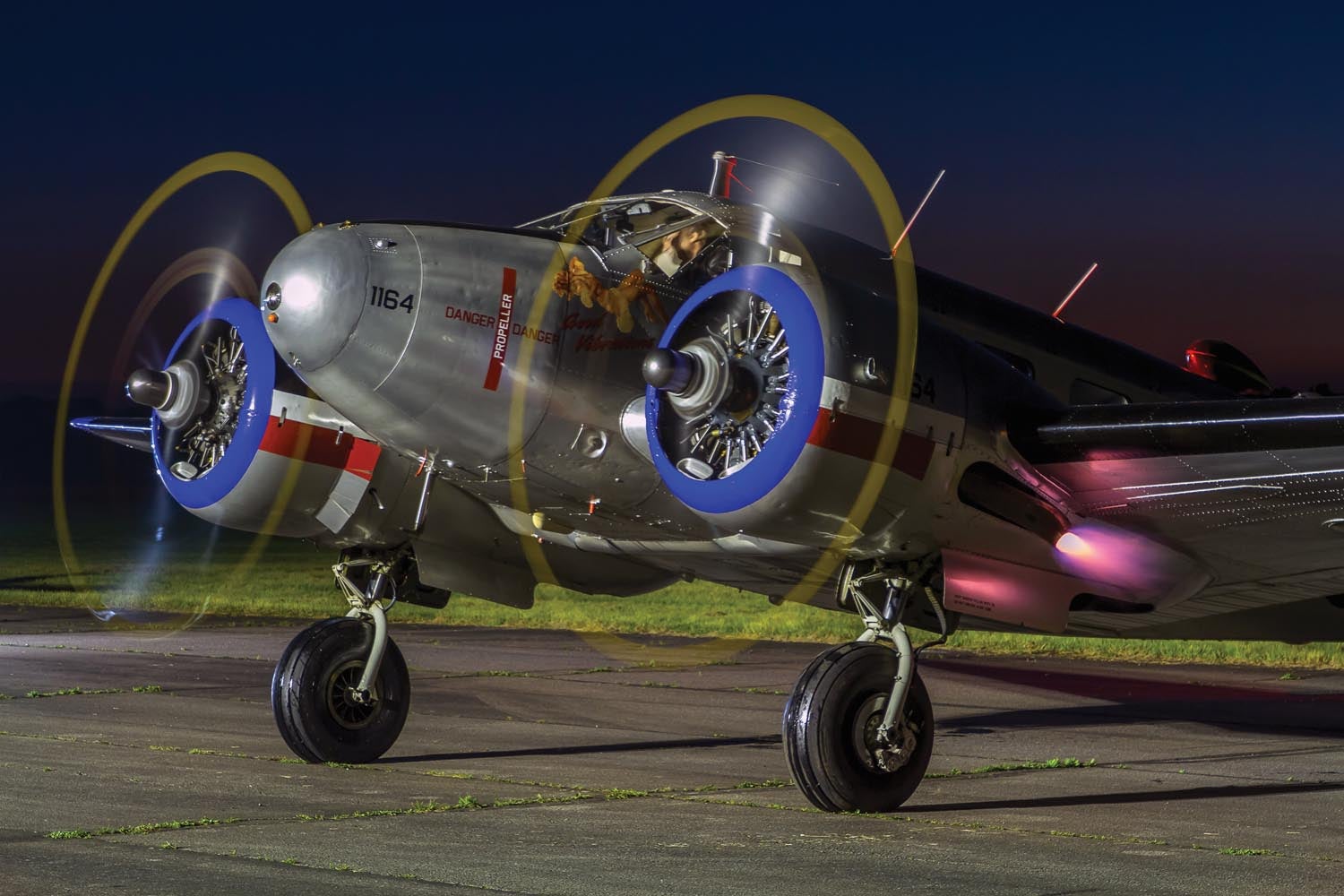
The cooling system is a major component of the airplane. It has a large impact on the performance and reliability of the machine. The engine and accessories must be properly cooled to survive and function, and the airflow required to do that cooling can account for a surprisingly large portion of the drag of the airplane.
An airplane engine is a heat engine. It converts the heat generated by combustion of the fuel into useful work in the form of power delivered to the propeller shaft. This power turns the propeller and generates the thrust that drives the aircraft forward in flight.
All of the heat generated by burning the fuel is eventually transferred from the airplane to the air in one form or another.
Some of the energy goes to generating power to turn the propeller. That energy is transferred to the air by the propeller while generating thrust. The air absorbs the energy the burning fuel imparts to the propeller through the drag of the airplane and the increased air velocity in the propeller slipstream.
Not all of the heat generated by the fuel burning is converted to power that drives the propeller. An aircraft internal-combustion piston engine typically has a thermal efficiency of between 25% and 35%. This means that only between ¼ and 1/3 of the heat energy generated by the combustion of the fuel in the cylinders ends up generating the useful work that turns the crankshaft and propels the airplane. The remaining 2/3 to ¾ of the heat generated by the combustion of the fuel is rejected as waste heat by the engine.
Heat Transfer Paths
To keep things acceptably cool, “leftover” heat generated by the burning fuel must be transferred directly to the air the airplane is flying through. There are several heat-transfer paths that do this.
Some of the heat leaves the engine via the exhaust. For example, the recommended maximum allowable exhaust gas temperature for a Lycoming aircraft engine is 1450° F.
Induction air enters the engine at the ambient outside air temperature (OAT). It is compressed in the cylinders and heated by the combustion of the fuel. The heating of the gas in the cylinder increases its pressure and it is this pressure acting on the piston that generates power.
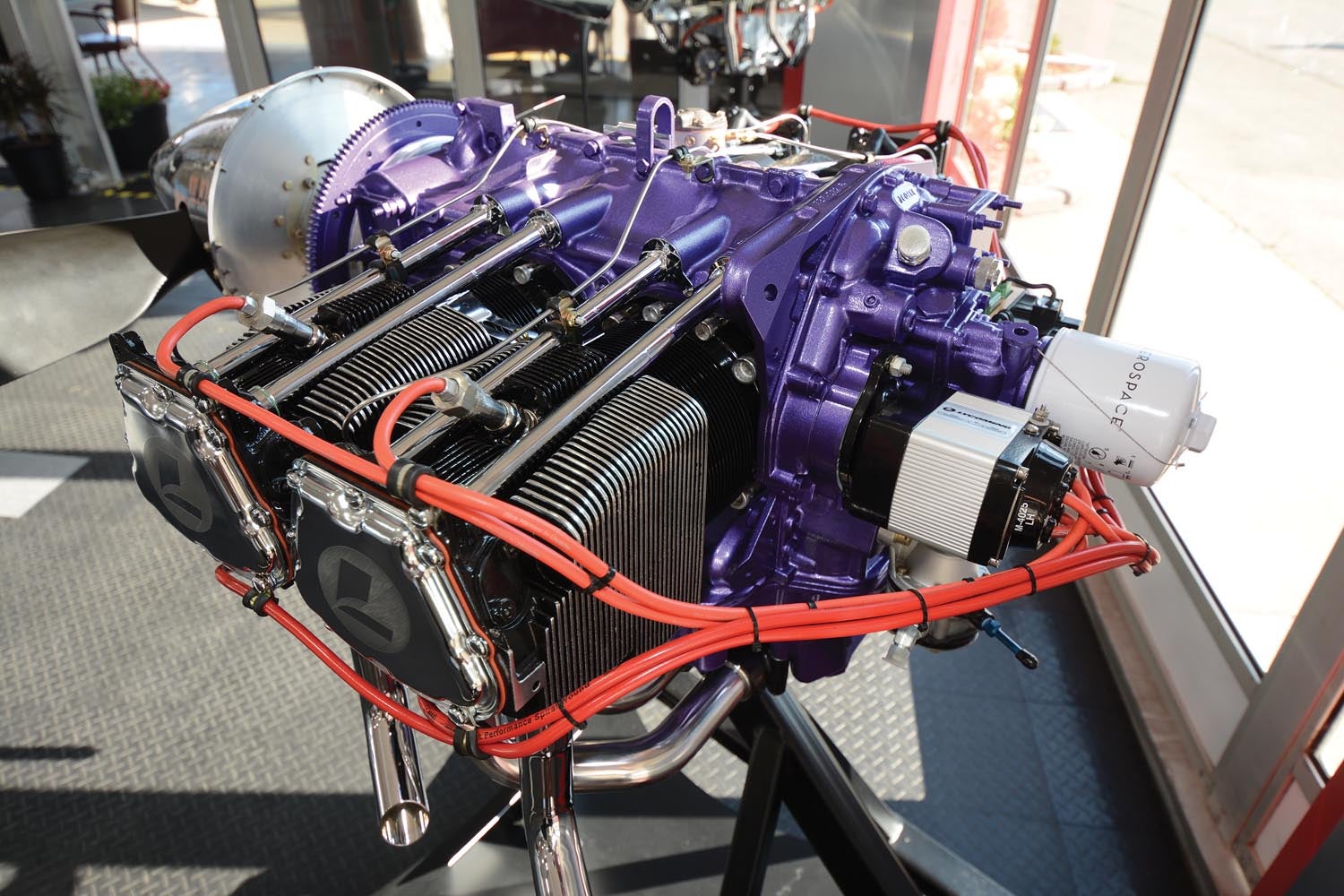
As the piston moves in the power stroke, the volume of the working chamber of the cylinder increases and the temperature of the charge inside it drops. A perfect engine would expand the hot gas so much that its temperature would drop to ambient before being exhausted from the engine. In the real world, the gas temperature in the cylinder drops from a peak of up to 3000° F to an exhaust temperature of 1200 to 1450° F. This hot gas flows out of the exhaust, taking with it a significant portion of the heat that was not converted to useful work.
In a perfect engine, the heat carried away by the exhaust gas would be the only waste heat rejected by the engine. To achieve this ideal, the cylinders, pistons, valves and any other components that come in contact with the hot gas in the cylinder would have to be able to withstand being at the full combustion temperature of the burning fuel/air mixture.
In reality, the engine needs to reject more heat in order to survive. One remarkable thing about piston engines is that the temperature of the burning fuel/air charge inside the cylinders is higher than the melting point of the materials the engine is made of. Cast iron melts at about 2200° F and aluminum has a melting point of about 1200° F. The peak temperature of the combustion gasses can get as high as 2500 to 3000° F.
Even these melting points do not tell the full story. Metals soften and lose strength as their temperature increases. At temperatures far below their melting point they lose a large percentage of their yield strength.
Metals also expand as their temperature increases, so the clearances between moving parts (like pistons and cylinder walls) decrease as the engine gets hotter.
All of this means that the engine must be kept much cooler than even the average temperature of the burning fuel/air mixture in order to survive. For example, the never-exceed cylinder heat temperature (CHT) for a Lycoming O-320 is 500° F and it’s recommended that the steady-state CHT be kept at or below 435° F to preserve the long life of the engine.
Intermittent Combustion
Fortunately for the viability of piston engines, the combustion of fuel in the cylinders is intermittent. A four-stroke engine only has hot gas in a cylinder for a quarter of the time and a two-stroke engine has hot gas in the cylinder for half the time.
During this hot period, the parts of the engine absorb heat from the hot gas. The temperature of the metal rises as it absorbs the heat. The metal parts have sufficient heat capacity that the temperature does not rise to a critical temperature in a single cycle.
After the combustion is finished and the hot gas is exhausted from the cylinder, the cylinders reject heat by conducting it through the walls to a fluid that will absorb the heat and carry it away. On an air-cooled engine, like those used in most general aviation aircraft, that fluid is the air itself. The fins on the cylinders absorb heat and then conduct that heat into the cooling air flowing over them. The fins are also there to increase the surface area of the metal that the cooling air flows over to absorb heat.
On a liquid-cooled engine, the heat is transferred from the metal of the engine into a liquid coolant, and the coolant then flows through a radiator that transfers the heat to the air.
In both cases, the excess heat is eventually transferred to the air and carried away from the airplane.
The metal parts of the engine never get to a steady-state temperature close to the combustion temperature of the fuel/air charge.
Intermittent combustion is the reason piston engines were feasible much earlier than gas turbines. Unlike the interior of the cylinders of a piston engine, which only experience full combustion temperature intermittently and have time to cool between cycles, the turbine blades in the hot section of a gas turbine are continuously immersed in the hot gas coming from the combustion of the fuel. They get much hotter than the components of a piston engine. The performance of a turbine engine is determined in large by the maximum turbine inlet temperature that the hot section blades can sustain. Because of this, a significant portion of the history of performance improvements in gas turbine engines is a history of the development of ever better high-temperature materials for the turbine blades.
Keeping an airplane’s engine and its accessories cool requires cooling air to be taken on board the airplane and used to absorb waste heat, then directed overboard to carry that heat away from the airplane.
Next month we will start a look at the cooling airflows themselves.
The engine is actually partly cooled by the oil absorbing heat which is then transferred to the air flow by the oil cooler, an oil to air heat exchanger or radiator. So all heat is ultimately transferred to the air but a significant portion is transferred to the oil as an intermediate fluid and then on to the air.