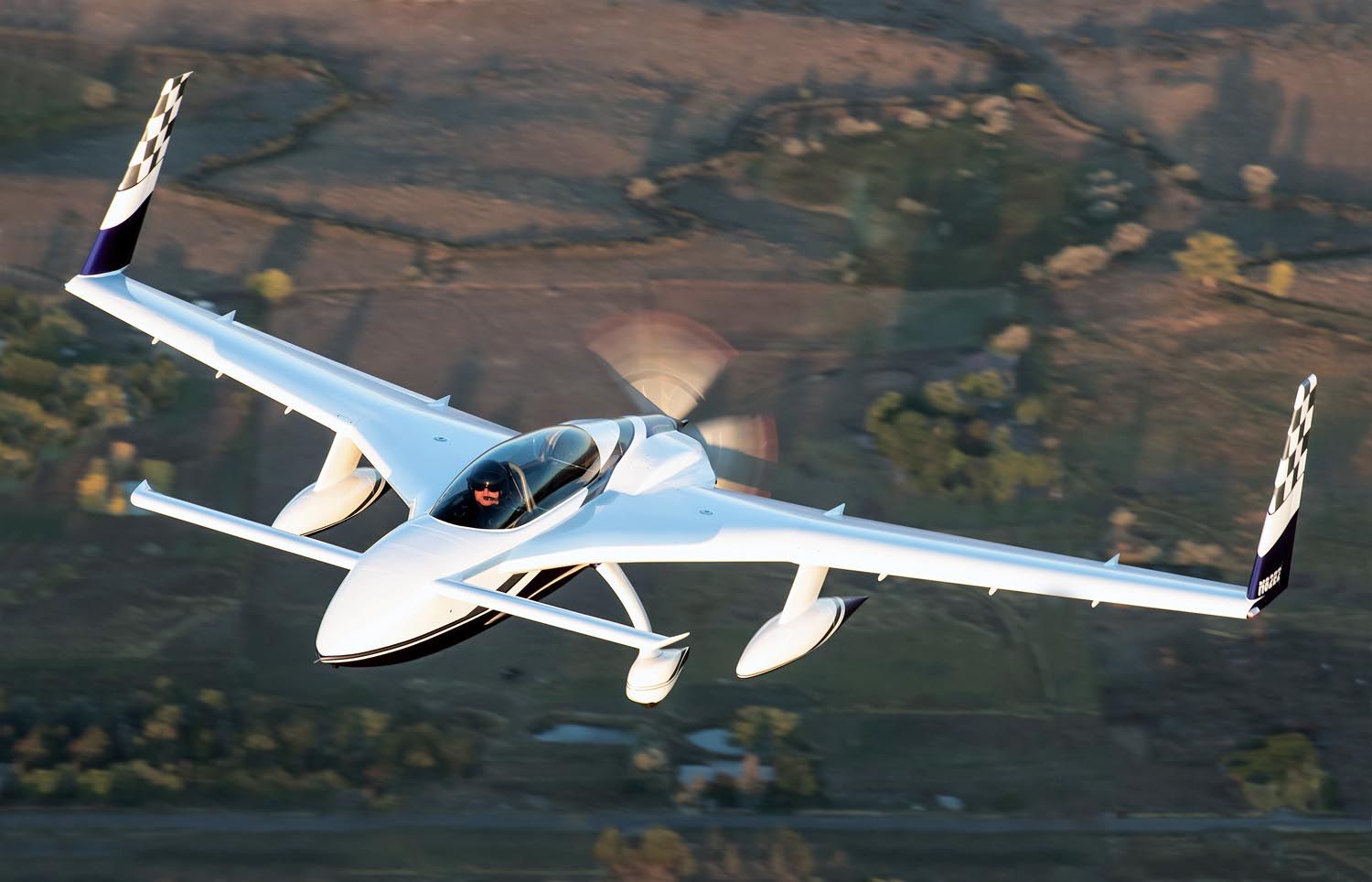
We often treat the propeller as a uniform “actuator disc” and the slipstream as a uniform stream tube of accelerated and swirling air. While this simplification is valid for many types of analysis, a propeller is composed of discrete blades. Each blade generates force and also sheds an individual aerodynamic wake downstream.
The discrete nature of the propeller blades has several effects on the propeller, the engine and the airframe.
Blade Loads
The loads on the propeller blades are not constant in flight. There are several conditions that change the aerodynamic environment of a blade as a function of its angular position along the orbit of the propeller. This variation produces a cyclic change in the force generated on the blade.
Angle of Attack
As we saw in last month’s Wind Tunnel about P-factor, the lift on the blade can vary as it goes around its orbit, even if the propeller is rotating at a constant rpm. There can be several causes for this variation in blade lift.
The first is the effect of the angle of attack of the airplane on the angle of attack and airspeed the blades encounter over a full rotation of the propeller.
A positive airplane angle of attack tilts the prop axis relative to the wind. Individual propeller blades encounter different conditions at different points in the propeller rotation. An up-going blade has a lower blade AOA and airspeed than if the shaft were parallel to the wind. A down-going blade has a higher blade AOA and airspeed. This causes the lift of each blade to vary cyclically within a period of one cycle per revolution.
Wake Impingement
If the wake of any part of the airframe impinges on the propeller, it affects the forces on the blades. This is particularly true on pusher configurations because the propeller is some combination of the wing, tail or engine support structure.
The frequency of the perturbations to the forces on a blade depends on how the blade passes behind an airframe component. For example, if the engine is pylon-mounted, as is the case on the Lake Amphibian, each blade passes through the wake of the pylon once per revolution. If the engine is in line with a wing, like on the Rutan canard designs such as the Long-EZ or on an airplane with wing-mounted pusher engines like the Piaggio Avanti or Beech Starship, each blade passes through the wing wake twice per revolution.
Upwash and Downwash
A lifting wing deflects the airstream. There is an upwash ahead of the wing and a downwash behind it.
On a multi-engined airplane with wing-mounted engines and tractor propellers, the props are immersed in the upwash ahead of the wing. This means that the propeller axis of rotation is tilted upward relative to the local airflow at the plane of the prop, even if the propeller shafts are physically aligned with the direction of flight. The blades will encounter the same variation of local angle of attack and airspeed around the prop orbit as we saw in our discussion of the effect of airplane angle of attack.
The downwash behind a lifting wing changes the angle of attack of the parts of the airplane behind the wing. On a pusher configuration, wing downwash affects the inclination of the oncoming airstream relative to the propeller axis of rotation. This produces the same type of once-per-revolution variation of blade forces as we saw as a result of airplane angle of attack.
Effects of Blade Force Variations
The aerodynamic effects we have just discussed produce cyclic variations of the loads on each propeller blade. The characteristic frequencies of the variations in blade load are multiples of the propeller rate of rotation.
Resonance and Blade Fatigue
The cyclic changes in blade thrust can excite flapping oscillations of the blade. This can be a significant problem if the natural frequency of a flapping mode of the blade is at or near the same frequency as the excitation caused by the fluctuation of the aerodynamic loads on the blade.
If the two frequencies couple, the blade will experience a resonance. The cyclic aero load will excite the structural flapping mode of the blade, causing the flexing of the blade to grow and the transient forces on the blade to increase far above the initial magnitude of the aerodynamic load. This can cause fatigue failure of the blades and is a particular problem for metal propellers or props with metallic shanks holding on wooden or composite blades.
It’s important that the propeller blades be stiff enough so that their natural frequencies are well separated (usually higher frequency) from at least one-per-revolution and two-per-revolution blade-passing frequencies. Certified propellers are tested extensively to ensure that they do not suffer from resonance issues within their normal operating range. There have been problems in the past with Experimental props with metal blades that were not so extensively tested, and at least two early attempts at variable-pitch props for homebuilts had to be withdrawn from the market after a series of in-flight blade failures.

Cyclic Loadings From the Prop
In addition to affecting the blades themselves, the cyclic variations of blade loading are transmitted into the propeller hub, the prop shaft and eventually the airframe via the engine and engine mount. This creates structure-borne vibration in the airframe and also cyclic loads that can fatigue mounting bolts and other structural components.
The frequency of these vibrations is different than that experienced by a single blade because it also depends on the number of blades. In essence, the characteristic frequency is multiplied by the number of blades. If, for example, a single blade experiences a one-per-revolution variation of load, a two-blade prop will put a two-per-revolution force variation into its hub and a three-blade prop will generate a three-per-revolution excitation.
The number of blades also affects the amplitude of the vibration caused by blade-force variations.
The amplitude of the propeller-induced vibration is a function of the loading of the individual blades. The cyclic loading on each blade is proportional to the nominal or average load the blade is carrying.
To the first order, the thrust generated by the propeller is divided equally between the blades. Increasing the number of blades reduces the load carried by each individual blade and therefore reduces the amplitude of the cyclic variation of load on each blade.
The result of these phenomena is that as the blade count increases, the frequency of the propeller-induced vibrations increases and its amplitude decreases. With more blades, the propeller will generate higher-frequency, lower-amplitude vibration.
The lower amplitude and higher frequency of the prop-induced vibrations are one reason to use a prop with more blades. In general, using fewer blades and more diameter is more efficient until the blade tip Mach number becomes the limiting factor on diameter, but the reduction in vibration amplitude with more blades is often worth the slight reduction in efficiency. Also, higher-frequency vibrations are less objectionable to people, so both effects make the propeller seem “smoother” to the occupants of the airplane.