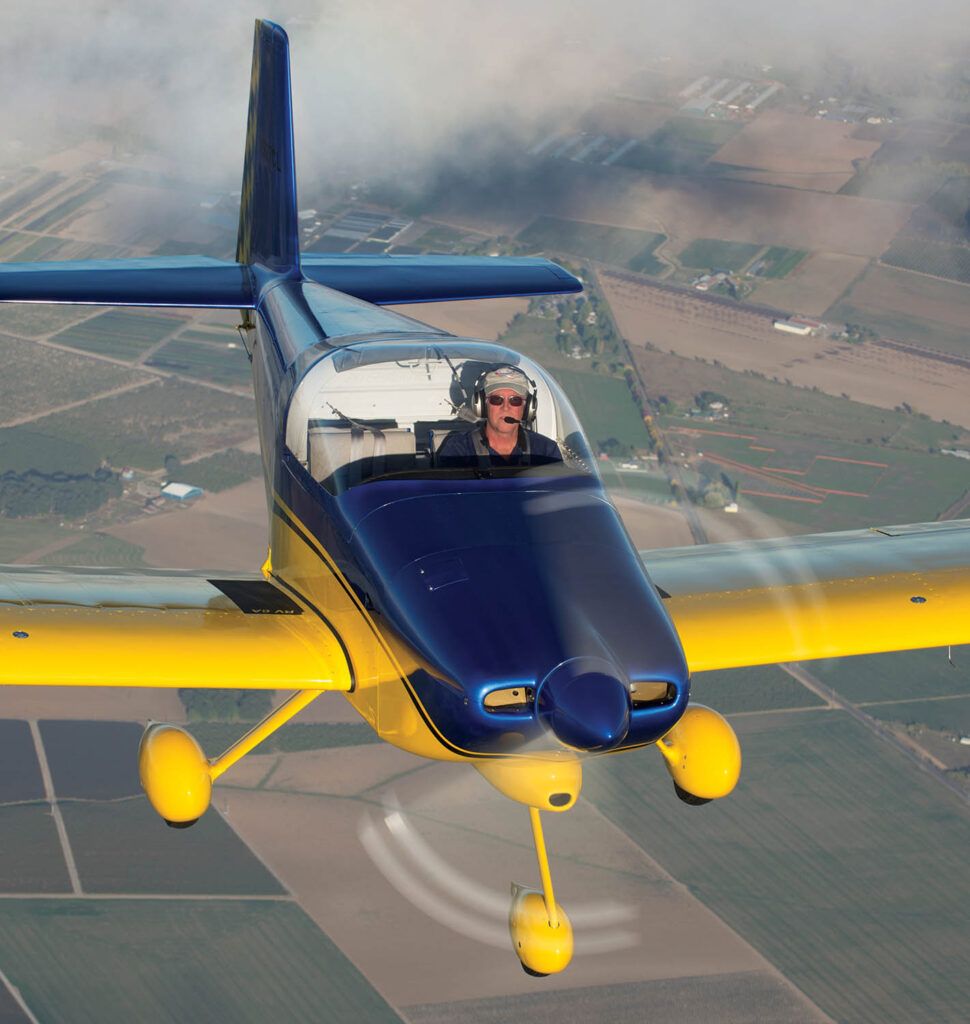
In preliminary design and for performance calculations, we treat the engine, propeller and airframe as separate entities. The only engine effect we typically consider in preliminary performance analyses is cooling drag. We neglect the propeller’s effect on the drag of the airframe and treat the prop as a pure thrust producer. Any effect the propeller might have on drag is kept as a small reduction in propeller efficiency.
For jet aircraft, the question of what is thrust and what is drag can get quite complex since the flow though the engines affects the airflow on the airframe significantly, particularly for aircraft with buried engines like fighters and some other military jets. Thrust-drag accounting is a major effort in and of itself on these airplanes and is far beyond the scope of what we need to consider for simple propeller-driven airplanes.
That said, although we can treat the performance effects of the propeller airflow very simply in most cases, the effect of the prop wash on the aerodynamics of the airplane in flight is not trivial. In a recent message, a colleague commented that “Installing a prop is like attaching a tornado to the airframe.”
Slipstream
In order to produce thrust, a propeller accelerates a column of air backward. The air in this column downstream of the prop is called the slipstream. In the slipstream, the air is moving faster than the free stream, and it is also rotating in the direction of the rotation of the propeller. The streamlines in the slipstream are spiral in form as the air flows downstream.
Both the added velocity and the spiraling swirl in the slipstream can affect the aerodynamic behavior of the airplane. The slower the airplane is flying, the greater both the slipstream velocity and swirl for a given horsepower to the propeller. Accordingly, slipstream effects are at their highest at low airspeed and high power.
Stall Characteristics
On most tractor airplanes, some portion of the wing is immersed in the propeller slipstream. For a single, the root of the wing is in the prop wash, while for a twin it is the portions of the wing behind the engines. The slipstream has two effects, both of which tend to delay the stall. First, the propeller turns the oncoming air and directs it aft more parallel to the prop shaft than the free stream. This reduces the angle of attack of the wing behind the prop. Second, the increased velocity in the slipstream increases the lift the immersed portion of the wing is generating.
Because it delays the stall of the blown portion of the wing, the slipstream changes where the wing stalls power-on. Particularly for a single-engine airplane, the point of initial stall on the wing will shift outboard of the propeller slipstream. A wing that had a benign root-first stall power-off may well stall farther outboard and tend to roll off during a power-on stall.
The combination of the delay in the stall and the shift in stall characteristics is what makes departure stalls more abrupt and dynamic than power-off stalls. The airplane stalls at a slower airspeed and at a more nose-up attitude, making the stall break more dramatic than with power off, and the lateral shift of the initial stall increases the chances the airplane will depart laterally into an incipient spin.
Lift
The propeller-induced velocity in the slipstream increases the airspeed of the portion of the wing and flaps it blows over. The lift generated by the wing and flaps is proportional to airspeed squared, so at low airspeed and high power the lift increase due to the additional slipstream velocity can be quite large. For STOL takeoffs, the combination of high power and powerful flaps can generate a lot of lift and reduce liftoff speed and takeoff roll significantly.
There are two concerns with using this additional propeller-induced lift on takeoff. First is that while the flaps generate a lot of extra lift in the prop wash, they also generate a lot of drag. The airplane must have enough excess thrust to climb after lifting off on prop wash-augmented lift.
The second concern is that if the prop wash goes away, so does the excess lift. This can lead to a very unsafe condition shortly after takeoff. The airplane is dependent on the extra lift from the propeller slipstream to keep flying. An abrupt throttle cut or engine failure will leave the airplane stalled in a nose-high attitude at an airspeed significantly below its power-off stall speed. It will require a significant loss of altitude to accelerate to a high enough airspeed to establish stable un-stalled flight.
Pitching Moment
As the slipstream flows aft, it flows first over the wing and then over the tail of the airplane.
As it flows over the wing and (sometimes) flaps, the slipstream is deflected downward. As we have just seen, this generates some additional lift, but it also generates some nose-down pitching moment.
Downstream of wing and flap, the down-deflected slipstream impinges on the tail. The tail sees both higher airspeed and a more negative angle of attack as a result. These two effects induce an additional down load on the tail and cause a nose-up moment as a result. The slipstream-induced nose-up moment of the tail is usually larger than the nose-down moment induced on the wing and flaps, so adding power at low airspeed will tend to cause the airplane to pitch nose up.
On airplanes with high-mounted engines like amphibians and some pusher ultralights, this slipstream-induced down load on the tail can help compensate for the nose-down effect of the high thrust line. If the tail is placed directly aft of the propeller so it is blown by the prop wash, then the slipstream-induced down load on the tail will generate a nose-up moment that helps compensate for the nose-down moment produced by the high thrust line.

Tail Power for Takeoff Rotation
Prop wash over the tail significantly increases elevator power at low airspeed. This helps with lifting the nosewheel off the runway to rotate for takeoff. It helps the pilot make a smooth takeoff if the elevators can lift the nose gear at well below the stall speed. The pilot can initiate a gentle rotation, starting somewhat before liftoff speed, and get a smooth, progressive transition from rolling to flying.
T-tail configurations that get the tail out of the slipstream sometimes have poor takeoff characteristics because the elevators can’t rotate the airplane until it’s going faster. Full up is often required to rotate. Once rotation starts, the pilot will have to react by reducing elevator deflection to prevent over-rotation or hop-off. Several T-tailed certified airplanes suffered from this problem, and at least one type started out with a conventional low-mounted horizontal tail, was converted to a T-tail in a later (supposedly improved) model and then converted back to a low-mounted tail again in a still later revision. The final low-tail version of the airplane is still in production.
Next month we will turn our attention to the lateral/direction effects of the propeller slipstream.
On the gyro form it is stated that keeping the h stab (no elevators) in the prop slipstream reduces the tendency to nose over in high power/low airspeed conditions.
Does the gyro behave as a weight shift control aircraft?
Hi, John. You might take a look at these older Wind Tunnel columns.
https://www.kitplanes.com/wind-tunnel-67/
https://www.kitplanes.com/wind-tunnel-68/
https://www.kitplanes.com/wind-tunnel-69/
https://www.kitplanes.com/wind-tunnel-70/
https://www.kitplanes.com/wind-tunnel-71/