Among the many effects of the supply chain problems in the summer of 2022, aviation discovered that it was having a difficult time functioning without a simple commodity—the oil filter. Lycoming and Continental engines everywhere needed spin-on, disposable oil filters to keep flying, and the supply was extremely limited. KITPLANES® research found that Champion had effectively stopped production—though it is now ramping back up—while Tempest was going at their normal production rate and trying mightily to increase it to meet demand. But Tempest simply couldn’t double its production overnight, so suppliers’ shelves emptied as aircraft owners quickly bought up every filter they could find. Remember the toilet paper shortages in the early days of COVID? Yeah, it was sort of like that.

Homebuilders searched their favorite forums to see if anyone had an extra filter on the shelf when it came time for an oil change, and as a hopeful sign of civility, many filters changed hands so that pilots could continue to fly. Some oil-change intervals might have been fudged—but for personal Part 91 operations, nothing says that you can’t go an extra 10 hours if you choose to do so. Not so lucky were flight school and rental-fleet operators, many of whom discovered that they had to find filters—at any cost—or stop operating some (or all) of their aircraft when inspections and oil changes came due. Lack of a $40 oil filter turned into much lost revenue.
Fortunately, there is—and has been for many years—an option to spin-on disposable filters. And no, I am not talking about going back to the simple oil screens that engine manufacturers used for over half a century before disposables came along. The original screens (I had a couple on my early airplanes) were comparatively very coarse, which meant they needed to be cleaned and the oil changed every 25 hours, according to Lycoming. Spin-on filters allowed intervals to be stretched to 50 hours—a welcome cost savings for aircraft owners, both certified and Experimental. Spin-on filters had, of course, been used in automobiles for a century—but took a little longer to make their way into aviation. Now, of course, they are pretty much the de facto standard. But an alternative is the permanent, cleanable filter that attaches to the same adapter as a disposable, spin-on filter.
Pioneered in general aviation by Challenger Aviation, the permanent filter has economic advantages in the long run (it will pay for itself after a certain number of oil changes) and reduces waste. And based on testing performed by K&P, which manufactures the filters for Challenger, it appears to provide better filtration and higher oil flow rates—both of which should be better for your engine.

How Good?
There are two parameters used to measure the “quality” of oil filters—particle size (how fine the filter is) and flow rate. Intuitively, it is obvious that the smaller you make the holes in the filter media, the smaller components it’ll catch and the cleaner your oil will be. Media is rated by hole size, in microns. The smaller the number, the better the filtration. However, there is a point of diminishing returns because the smaller the hole size, the harder it is to force enough oil flow through the filter element. This is obvious if you reduce the hole size to zero—in this case, nothing is going to go through!
K&P discusses this in detail on their website, citing that paper filters, which they had tested, range from 48 microns to 300 microns. (Bear in mind the source of this information, which is likely to not be impartial.) The variability is simply because no two paper filters are ever going to be alike—even when they come off the same manufacturing line. So paper media is rated on averages. But stainless-steel cloth is manufactured with a uniform process producing uniform results. The K&P media is rated at 35 microns, for instance. Tempest states on their website that their paper filters are rated at 40 microns—which is quite good. Challenger told us that their filters are manufactured to their specifications (by K&P) with a screen rating of 22 microns. In all cases, K&P’s testing showed significant increase in flow rates over paper filters.

The real question, of course, is “what is good enough?” The answer to this simple question is elusive. Lycoming has no specifications that identify a maximum micron size or flow rate, leaving us to assume that any filter you can buy is sufficient. One maintenance manual we found for a popular Lycoming clone specified a filter size of 20 microns—and none of the existing filter manufacturers claim to be that good. In truth, we have heard of essentially no engine failures or early overhauls due purely to the fact that the filter wasn’t taking care of fine enough materials. Sure, there are engines that were making metal that required early overhaul—but that would have been true regardless of the filter being used.
There probably isn’t enough data to prove that the permanent filter will provide longer time between overhauls or lower the risk of oil-related engine failures (an astronomically small number unless you count “lack of oil” incidents). Or that it’s any worse than a spin-on. But if you believe that oil filtration is a good thing—and that better filtration is a better thing—then it is hard to argue that the permanent filters, if they do indeed provide equivalent filtering to our well-known paper filters, aren’t a reasonable solution to our current supply issues.
In truth, this is really just a top-line discussion of filter ratings and capabilities. The subject could be considered a gator-infested swamp, but we’re willing to ford into the marsh—that’s why we’re working on a more in-depth look at what the ratings mean, how filters are tested and what this may (or may not) mean for your actual airplane engine. Look for that in a near-future issue.

Filter Features
Back to the nuts and bolts. Oil filters are not just a can with filter media inside. There are certain features, which are important, especially for an expensive motor that is keeping you in the air! Yes, you need a good filter media, one that has a good flow rate, and also a small filtration size. But what happens if the filter media gets clogged? You still need oil going to the engine’s vital parts, so any acceptable filter needs to have a built-in bypass valve to let oil continue to flow. Yes, many oil filter adapters on engines have their own bypass valves—but some of us like a belt-and-suspenders approach, and all good filters have a bypass anyway. It’s important to know that you don’t want to lower the bypass pressure of course—otherwise, the valve stays open and you get no filtration at all.

the X-shaped O-ring lightly with clean
oil before installation.
Another feature you may or may not find in an oil filter is an anti-drainback valve. This is usually a rubber flapper that keeps oil in the filter after the engine stops so that when the engine is restarted, the filter is already full and you get immediate pressure. The need for this valve is hotly debated by many mechanics, builders and pilots, but the fact that some filters have them and others don’t begs the question of whether or not they are essential. In general, Lycoming engines with straight-back oil filters don’t use the anti-drainback valve, while those with an angle adapter do. The permanent filters we have looked at do not have them, and we know many owners using the permanent filters on angle adapters with no problem. We found no hard evidence on their need one way or another.

Other features of aviation oil filters are external, including a large (usually 1-inch) hex nut on the end to help you torque them without a strap wrench, and holes with which to safety wire the filter to the engine. Aircraft oil filters are safety wired because they have always been safety wired—or so it seems. This is another thing hotly debated on homebuilder forums, and this author falls on the side of, “If there is a hole why not safety wire it? And if there isn’t a hole, there is one on the engine—so why not have or make a provision on the filter?” The Challenger aviation filters have both the nut and the safety wire holes. The K&P filters marketed to the automotive and motorcycle world generally do not have either—but it is very easy to add holes in the top-most cooling fin, and these units come with a special “cup wrench” that mates to a 3/8-inch socket drive to make installation easy. Just don’t lose the cup, or you’ll be using a strap wrench.
One additional feature on the K&P-manufactured filter elements is a small high-strength magnet designed to pick up ferrous chunks from the oil. Magnetic drain plugs have been a thing for years—this is just a variation on the theme and probably not a bad idea, especially if you have reason to believe your engine might be shedding bits of steel or iron.

Permanents
The only permanent filter intended specifically for aviation use is the one designed and marketed by Challenger. Challenger does not currently sell direct to consumers, but rather through a dealer network, probably the largest dealer being Aircraft Spruce. Because of the shortage of disposable filters in 2022, Challenger told us that they were having a difficult time keeping up with demand, but were doing what they could to increase their output.
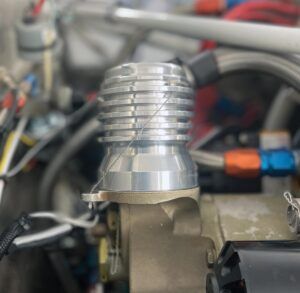
In the same way that many home-builders have used automotive filters on their Lycomings for years, many homebuilders have been purchasing the K&P-branded filters from various sources. The fact that K&P makes the Challenger filters has been used by many to assert equivalency, but as noted a little ways back, the filter element in the Challengers has a finer grid than the stock K&P product, which partly explains the price difference. It also should be noted that there have been a number of reports from homebuilders who had their orders canceled when K&P found out that the filters were going to be used on aircraft. Some manufacturers are funny that way—which is why, when you go to AutoZone to buy a Denso alternator, you must weave the story that it is for your beloved ’98 Suzuki Samurai and not your homebuilt airplane.
When it comes to commerce, some builders will seek out the cheapest solution and some will decide it’s more important to support two aviation companies (Challenger and the distributor/retailer) for what amounts to a difference equivalent to 20 gallons of avgas. That said, if you want the K&P, you’ll need the S15, which is a 48108 equivalent right off the shelf. To replace a 48110, you’ll also need a ¾-16 nipple for about $8.
Installation Matters

Installing the permanent filters is simple: Spin off the old filter and spin on the new one. Torque to the spec that comes with the filter, using the hex nut on the end or the cup tool, and safety wire. If you need to add the safety wire holes, it’s simple to drill a #50 hole in the outermost cooling fin. We drilled four in ours, just to give us various clockings. Note that the permanent filters come with an X-shaped O-ring. The K&P units we received came with a spare—we have read reports of folks using them up to 10 times, and also those who replace them every other oil change. Do what you feel comfortable with.
So what do the engine manufacturers and/or the FAA say about the permanent oil filters? Let’s start with the FAA. They have issued an STC for the Challenger filter, so they can be installed on virtually any aircraft with a Lycoming or Continental engine. Not that we need an STC in the Experimental world, of course. But clearly Challenger has proven to the FAA that their filters do the job up to acceptable standards.

As for the engine manufacturers, they are pretty much silent on the topic—as they are on any filter choices. We could find no reference in the Lycoming documentation regarding minimum specifications for oil filters. Continental documentation is also very sparse, with only one reference we found in the IO-370 manual that specified a filter with “20 micron filtering,” which is problematic, since we couldn’t find any filters in the industry that meets this spec. The truth seems to be that just as the disposable filters do a good job at filtering oil, the experience of many builders is that the permanents are doing just as well.
In a discussion with Linda Rocco, president of Challenger, we asked about the length of time between oil changes. Lycoming for years recommended a 25-hour oil change/screen cleaning with the old screens—but with a full-flow disposable, that could be stretched to 50 (what most owners use these days). Rocco said that while they can’t speak for Lycoming, their position is that pilots should use whatever interval they have been using with disposables when they switch to the Challenger.
Given that the K&P filters are specified at 35 microns, and the paper filters are rated at 40, it is probably safe to assume that staying with the 50-hour number is probably OK—but everyone should decide for themselves.

Just More Bling?
There is no doubt that the reusable filters look great on an engine—smaller, finned, billet-machined…they just scream “hot-rodding,” and that is hard to resist. But at the same time, they appear to be a very good filtration system that takes you out of the dependence of disposable filter availability. Do they really make oil changes quicker and easier? Well, that depends on if you always go to the effort to cut open and evaluate your disposable filters. We all should, but many don’t. Very few people cut open their car’s oil filter to examine the contents, which is why the disposables are quick and easy to use. If you are just spinning it off and throwing it in the trash, then the reusable filter is going to add to your oil change time because you pull it off, clean it and reinstall—and that takes a little time.

Does the reusable make less mess? Partly that depends on how much mess you make with your disposable, and that depends on your engine configuration. And now you need a container in which to rinse and wash the filter element—just like we grumbled about in the bad old days of oil screens. Six of one, half a dozen of the other—it’s up to everyone to decide what makes the most sense. We’re putting them on our “fleet”—and will report back on the results—but to come up with meaningful results, that might take a couple of years. Weigh the pros and cons for yourself—this is, after all, Experimental aviation!
Great idea and nice article but one thing is missing. How is it cleaned? Part of our oil change process involves opening the paper filter to examine the filter material for debris. What’s the recommended process for cleaning the filter and how can the contents be examined?
Actually quite simple! The filter element fits easily in a disposable food container from the dollar store – rinse it in some stood dead solvent or shoot brake cleaner into the core to knock off anything that collects on the outside (the inlet side of the filter). Examine for any bits in the container. Nothing hides, like it sometimes does in a paper filter.
The $350 is initially difficult to justify. But in the K&P tech info, they noted a 20 psi drop across a paper filter vs 1 psi with their metal mesh filter, in the high performance engine they tested. [ not necessarily an aircraft engine ]. This resulted in a 5 HP net gain with the reduced load on the oil pump.
In my GO-300 I’m seeing the low end ‘green’ of 30-35 psi at cruise power. I wonder if changing to the K&P would increase the oil pressure and the oil flow rate and improved cooling of the valves ?. It certainly would reduce the load on the oil pump and the accessory gears.
So, it may be a wise investment. ?
Jim, I would think that having less of a pressure drop and reduced load on the oil pump using the K&P would translate to a lower indicated oil pressure .
Martin,
Most oil pressure sensors are some distance down the main oil gallery, downstream of the oil filter, so any reduction in oil pressure loss through the filter will show as a higher reading on the gauge..
The C172R is had flown has the pressure sensor at the front of the engine, and the low oil pressure switch at the rear.
The Continental in the C175 I fly now has the pressure sensor 1/2 way along the main oil gallery , after oiling 1/2 the main bearings. [ no low pressure switch, but the temp sensor is at the inlet to the oil cooler , next to the prop gearbox. ].
I’ve tried these filters in my aircraft, they filter VERY good and flow good (when clean).
The problem I had with it; and the reason I stopped using it; is that they are hard to clean and validate that it is truly clean. The small particles they catch are the same color as the screen itself; very hard to discern when it is completely clean.
I’d rather toss a paper filter than inspect it and pick the tiny particles out of the screen that invariable get stuck in it and reduce the ability of the filter to do its work like when it was new.
Brian, Paul,
Would an ultrasonic cleaner with the appropriate solvent be able to remove/dislodge all the small particles caught in the screen wires ?
I would consider using this part, even with the $345 cost , since filters are hard to find [ why ?], and I’d like the increase in oil pressure, and lube flow for cooling.
I don’t want to discount Brian’s experience, but my own is that I haven’t had any issues cleaning the filter as I described above, and the filters haven’t hidden anything. Generally, I find some small black carrion particles in a filter – if I find metal, I really take my time because engines shouldn’t be making metal….
Thanks Paul,
I’ll consider buying one.
Paul, where can you source the nipple you refer to? “To replace a 48110, you’ll also need a ¾-16 nipple for about $8.”
Thanks!
It looks like the price has gone up considerably since we bought some, but we found that at: https://usaoilfilters.com/product/threaded-fitting-3-4×16-x-3-4×16/
USAOilfilters.com appears to be the online sales arm of K&P.
Great video on how to clean: https://youtu.be/YvsFN3PMRGE
I’ll reach out tomorrow to see if FAA is considering extending TBO once using this contraption.