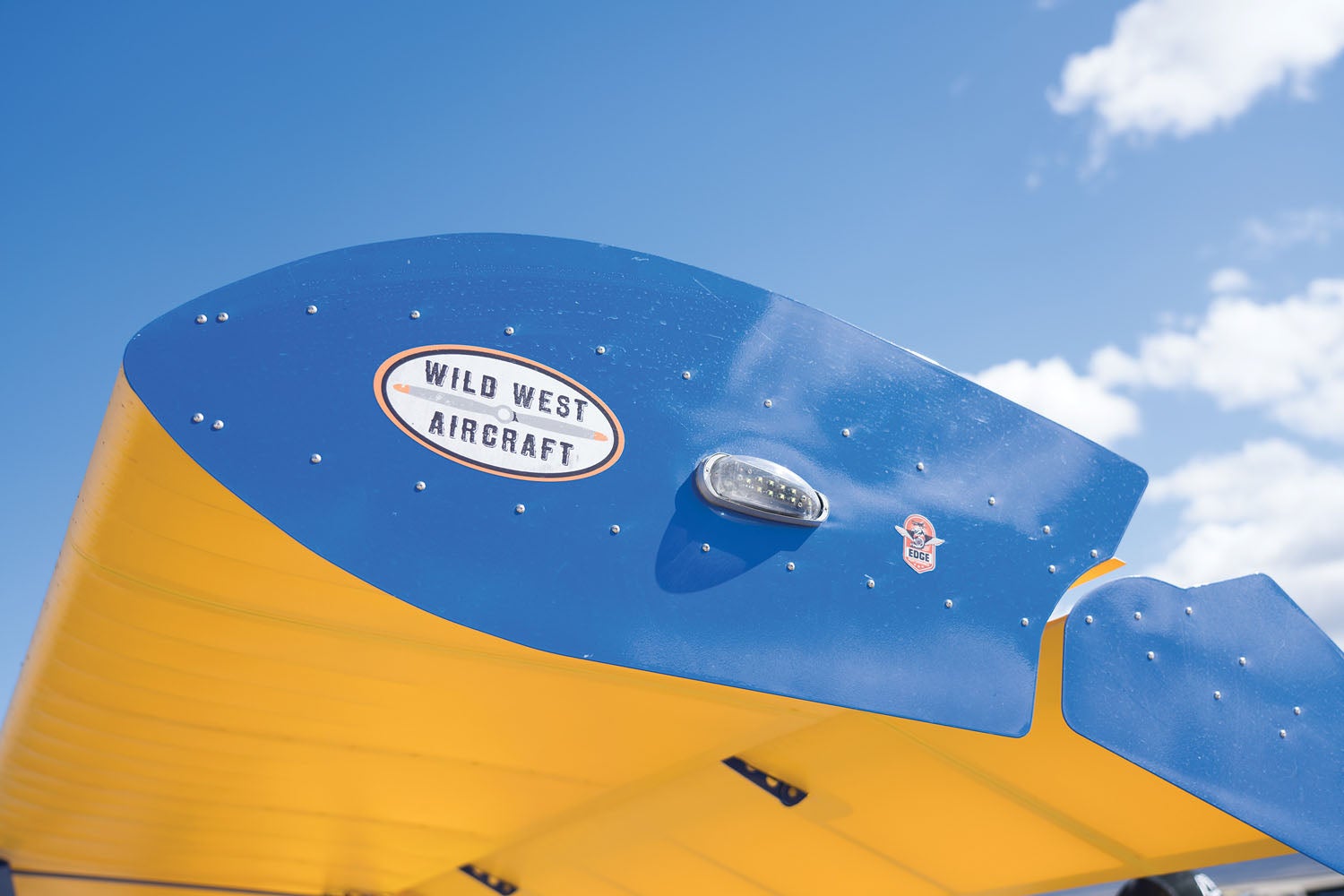
A wing produces a pressure difference between its upper and lower surface. The pressure on top of the wing is lower than the pressure on bottom.
At the wingtip, the wing disappears to the air, removing the barrier between the two pressure zones.
Just inboard of the tip the wing deflects the air downward, while outboard of the tip the air is driven upward by the pressure difference between the top and bottom of the wing. The combination of the downwash behind the wing itself and the upward flow just outboard of the tip causes the air to wrap up into a vortex that sheds aft of the tip of the wing.
Last month we saw how tip planform and shaping can affect formation of the tip vortex and the effective span of the wing. This month we’ll look at two types of wingtip aerodynamic devices that go a step beyond a planar tip and seek to directly manipulate the cross-flow at the tip to alter the formation of the tip vortex.
Manipulating the Tip Flow
There are two types of wingtip aerodynamic devices that go a step beyond a planar tip and seek to directly manipulate the cross-flow at the tip to alter the formation of the tip vortex. These devices function as barriers to the cross-flow near the wingtip or manipulate the cross-flow in the vortex itself in order to weaken the vortex and/or recover energy from the swirling flow.
Both types add wetted area to the airplane, and hence increase parasite drag at the same time as their influence on wingtip airflow reduces induced drag. The trade between parasite drag due to wetted area and reduction in induced drag is a function of the flight condition of the airplane and will determine whether it is appropriate to incorporate a tip device.
The two classes of tip devices are end plates and winglets.
End Plates
An end plate is a thin flat plate mounted at or near the tip of the wing, perpendicular to the wing surface and parallel to the airflow. It acts as a fence that opposes the spanwise flow near the tip of the wing.
The end plate restricts the cross-flow near the wingtip, and this also weakens the tip vortex.
The overall effect of the end plate is to maintain the pressure differential between the upper and lower surface of the wing farther outboard on the wing. The end plate traps some additional high pressure on the lower surface of the wing near the tip and reduces the ability of the high pressure from the bottom of the wing to bleed into the low-pressure zone on the upper surface.
The end plate increases the amount of lift the wing generates at a given angle of attack and reduces the induced drag of the wing.
Typical end plates are relatively short. They are more like fences near the tip than large surfaces and rarely protrude more than about 1/4 of the cord above or below the surface of the wing.
Because of this, the forces on the end plate are relatively small and the plate itself can be a thin flat plate rather than a more substantial structure.
The end plate does affect the loads on the wing in a way that may be significant structurally. By trapping more high pressure under the tip of the wing and low pressure on the top of the wing, the end plate increases the lift of the wing near the tip. This in turn increases the bending moment on the wing by shifting the centroid of the wingspan loading outboard.
Another effect of end plates is to increase the effectiveness of the ailerons since the end plate helps maintain the pressure differential across the deflected aileron.
End Plates also add some wetted area and therefore produce some parasite drag. The trade between the increase in parasite drag and the reduced induced drag is fundamental to the decision of whether to incorporate end plates.
Winglets
A winglet is a wing-like device that extends vertically or nearly vertically up from the tip of the wing. The winglet operates in the cross-flow generated by the tip vortex.
Unlike an end plate, which is flat, a winglet has an airfoil cross section and may also incorporate twist to optimize its aerodynamic effectiveness.
In the tip vortex region above the wing, the air is flowing both inward and aft. The inward component of the flow generates an angle of attack on the winglet. The winglet generates lift as a result. This lift acts normal to the incident airflow and is inclined forward due to the inward cross-flow. The forward inclination of the lift vector generates a thrust force on the winglet.
In effect, the winglet acts like a turning vane or a sail that deflects the inward flow from the tip vortex aft, and this aftward deflection causes a forward reaction force on the winglet.
As is the case with end plates, the induced drag reduction provided by the winglet must be traded off against the parasite drag due to increased wetted area and the increased weight of structure required by the forces on the winglet.
The winglet can have a large beneficial effect on the induced drag of the airplane, but the forces on it can be quite high. In normal flight there is an inward force on the winglet as a result of the lift it is generating to turn the cross-flow from the vortex. Winglet loads can get even higher if the airplane is side slipped as would be the case in a lateral gust encounter or a crosswind landing.
The winglet structure and the structure of the wing it is attached to must be strong enough to withstand these loads. The weight of the additional structure required can be quite significant and must be factored into the trade-off to determine if adding the winglet gives an overall performance improvement.
A winglet configuration should also be traded against a wingspan extension. It’s possible to increase the span of the wing by extending the tip. For the same wetted area and weight increase needed to implement a winglet, we could build a longer-span wing, which would also have lower induced drag than the initial wing design.
There is still considerable difference of opinion as to whether a configuration with a winglet is superior to an optimized planar wing of greater span. I believe the answer depends on the details of the airplane’s mission and the outside constraints imposed on the design.
It’s clear that if the wingspan is constrained by other considerations such as hangar size, a configuration with a winglet can have can have superior performance to a span-constrained planar wing.
We can get some idea of the relative merit of winglet configurations and optimized planar wings by looking at commercial jet transports. Winglets have appeared as retrofits for a variety of commercial transports and are also incorporated on new production airplanes that are derivatives of aircraft originally created with planar wings. There’s no doubt that the winglet provides a useful benefit.
In the Experimental aircraft world we find an example of a special case for the winglet. On the Long-EZ and similar Rutan style canards, the winglets do double duty as the vertical stabilizers. In this application adding winglets does not increase wetted area because the winglet replaces a vertical fin of similar size. This allows the configuration to take advantage of the induced drag reduction provided by the winglet without incurring an offsetting parasite drag penalty.
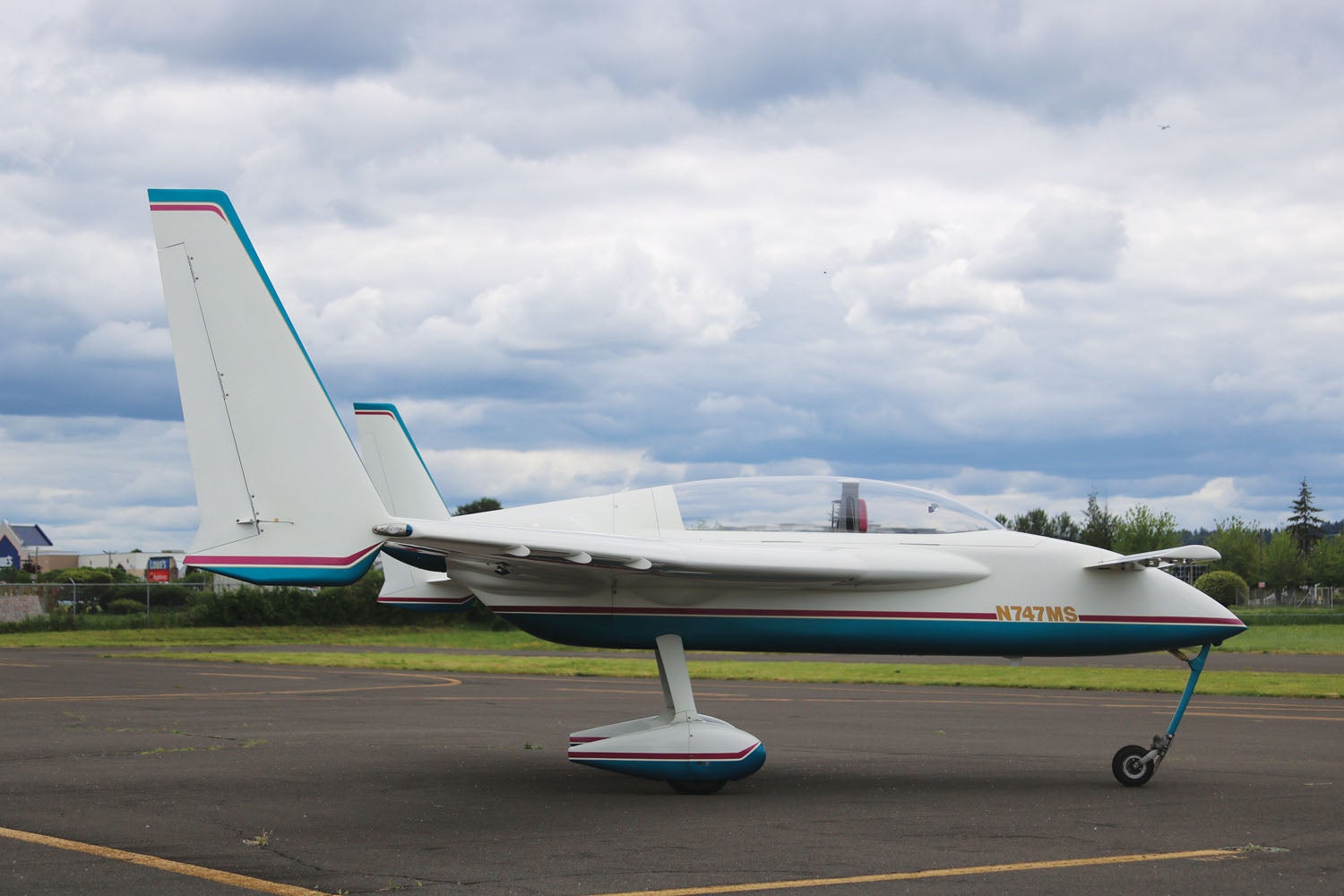
I was hoping for a bit more useful information regarding GA aircraft and the benefits that may be provided in the different speed ranges. As an example, to put things in perspective, you can’t compare end plates to winglets, where do droops tips fit in the discussion? Our aircraft type has seen many mods, end plates, extended wings and drooped tips or a combination of extensions and tips. As I understand the basics: Drooped tips really help in the slow speed high angle of attack realm. End plates can do the same, but don’t have the drag at lower angles of attack for cruise. Winglets on the other hand are more for cruise efficiency reducing or channeling the spanwise flow from the swept wing. Then last month you’d mentioned the scalloped tips . . . perhaps something on how they may compare.?
winglets improve cruise efficiency by converting some of the tip vortices into thrust, as well as reducing overall induced drag. But I agree that few places discuss wingtip devices in anything approaching adequate. Everyone likes to just skip over it quickly, probably because most people actually don’t understand how they work themselves beyond, “I read it in a book, and that’s how it said they work.”. Few people I’ve met can actually explain the aerodynamics of such devices, and thus most people reading their work have even less understanding of how they actually work. A good discussion would address all the most common types with a simple description of the aerodynamics of each, followed by a pros/cons discussion of each, ending with a discussion of when/why a person might consider using that type, or not.
This is counterintuitive, the added area of an end plate is quite small, so one would expect quite a minor effect on parasitic drag. But, the rearrangement of load distribution, taking the distribution even further from the ideal elliptical distribution would seem to be significant, and is expected to increase rather than decrease induced drag.
Having worked driving Hi-Lift trucks at an airport , I know that there is not much room between the wings of aeroplanes parked on adjacent bays. Increasing the wingspans on A320s and 737s would reduce this even further. However using upturned winglets, helps reduce the effect of wing tip vortices without significant increase in wingspan. So the aeroplanes can continue to use the existing standard size bays at all the worlds airports. A380s and 777s could not fit into standard size bays from the outset. They would either take up two existing bays , or special bays were built to accommodate them. These bays were large enough to fit extended wingspan without needing the tips to be turned up. Turned up winglets are a compromise between reducing the effect of wingtip vortices and fitting into existing airport bays .