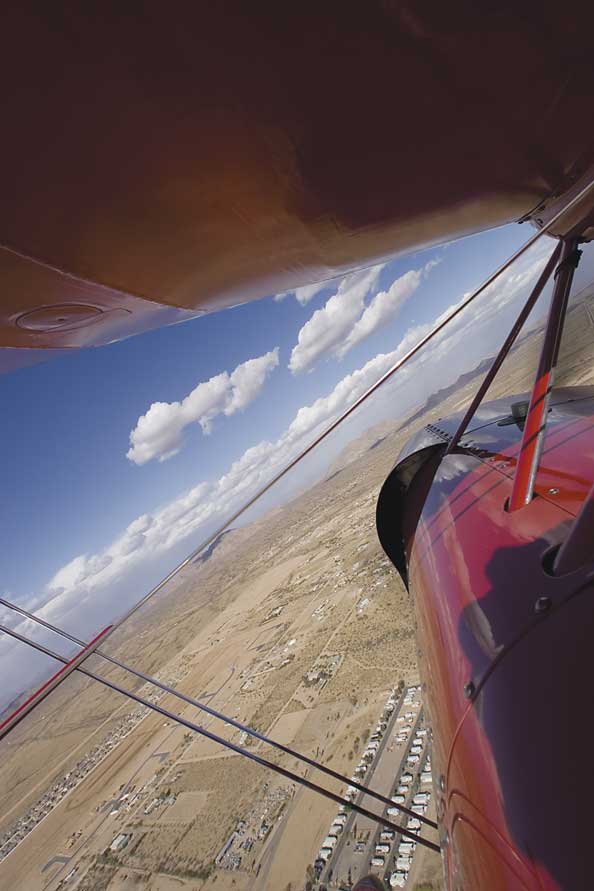
In recent months, this column has been addressing flutter. This month, we turn our discussion to flutter that is different in nature than the classical flutter cases that have been discussed before. The types of flutter already covered all arise when two of the fundamental twisting or bending modes of the airplane structure couple in frequency, and are driven by aerodynamic forces arising from the distortion of the structure. It is possible, however, for other combinations of factors to lead to aerodynamically driven oscillations.
Stall Flutter
Classical wing bending/torsion flutter and aileron flutter happen in a flight regime where the airflow is fully attached and the aerodynamic forces vary linearly with angle of attack or control deflection. Sometimes, however, airflow separation or stall can be a major contributor to a flutter mode known as stall flutter.
The elastic axis of a surface is the axis about which it twists. For a wing or tail, this means that a lift force ahead of the elastic axis causes the surface to twist leading edge up, and a lift act of the elastic axis causes it to twist leading edge down. Typically, wings and tails are designed so that the aerodynamic center of the flying surface is near, or slightly aft, of its elastic axis so that changing lift does not cause the surface to twist.
If the elastic axis of a surface is aft of the aerodynamic center, the system will be unstable. Increasing angle of attack increases lift, which in turn causes the surface to twist, increasing angle of attack and lift more. The twist is opposed by the torsional stiffness of the surface and its supports. Four variables control what happens in this situation: the torsional stiffness of the surface, its ultimate strength, the product of the area of the surface, and the distance between the aerodynamic center and the elastic axis. There are three possible outcomes given these variables.
If the surface is stiff enough and strong enough, the structure will be able to resist the twisting caused by the aerodynamic load without failing. Increasing angle of attack will cause the surface to twist leading edge up some, but the surface will come to a steady-state shape without failing.
If the surface lacks sufficient torsional stiffness, it will be divergent. The aerodynamic twisting moment caused by the lift ahead of the elastic axis will cause the surface to twist sufficiently to generate more lift than the structure can resist, and the twist will increase without bound until the structure fails. The possibility of this sort of structural divergence is the primary issue that prevented the widespread adoption of forward-swept wings. Although forward sweep can have significant aerodynamic advantages for airplanes flying at high subsonic Mach numbers and might be very useful for making slower airplanes balance properly, it is difficult to design a forward-swept wing that is not structurally divergent at a reasonable weight. It is possible to do so using modern structural analysis techniques and composite materials, as was proven by the Grumman X-29 research airplane.
The third case arises when the structure is strong enough to withstand large twist angles without failing, but it is torsionally soft enough so that the aerodynamic forces can cause a lot of twist. In such cases, what sometimes happens is stall flutter, the mechanics of which are illustrated in Figure 1.
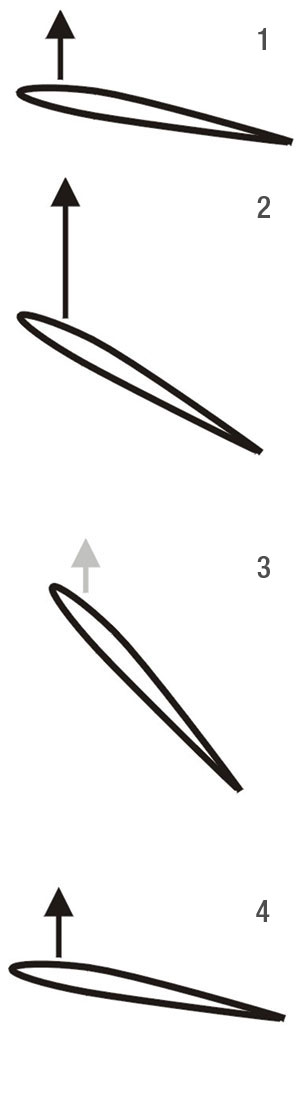
Figure 1.
1.Lift acts forward of the elastic axis of the surface.
2.Surface twists, increasing the angle of attack. This causes lift to increase, making the surface twist more.
3.Surface reaches stall angle of attack. Lift is greatly diminished.
4.Torsional stiffness of surface causes it to spring back to original shape after stall. Lift is devolved again, and the cycle repeats.
The Cycle
The stall flutter cycle starts with a perturbation (either a gust or an angle of attack) that causes the surface to lift (1). The lift acts ahead of the elastic axis, causing the surface to twist to a higher angle of attack, increasing lift (2). The surface continues to twist until it reaches a high enough angle of attack to stall (3). When the stall causes the aerodynamic moment twisting of the surface to disappear, the structure, which is twisted like a torsion spring, twists back to its original, unloaded position (4). This reduces angle of attack enough for the airflow to reattach, generating sufficient lift to start twisting the surface again, and the cycle repeats.
As with all flutters, the severity of stall flutter can vary from an annoying limit-cycle buzz to a rapidly diverging oscillation that will cause structural failure. One example of a relatively common large-amplitude limit-cycle stall flutter oscillation is the behavior of some road signs in a strong wind. If the sign post is of the open U-channel variety commonly used for smaller signs like speed limit and no parking signs, the signpost is strong, but soft in torsion. In a strong wind coming edge-on or nearly edge-on to the sign, it will exhibit a limit-cycle stall flutter of surprisingly large amplitude.
On airplanes, stall flutter of primary flying surfaces rarely happens, because if the surface is torsionally flexible enough to stall flutter, it will be unacceptable for many other reasons and will never fly. Stall flutter does show up on other airplane components, however.
Landing-gear doors are relatively susceptible to stall flutter. Like the road sign mentioned above, a landing-gear door is relatively thin, and hence torsionally flexible, and is flying nearly edge-on to the airflow. The position of the doors elastic axis is primarily determined by where the actuating linkage that controls the door position attaches to the door. If the linkage attaches well aft on the door, then the elastic axis may be far enough aft to allow the door to twist in a direction to increase lift when it is loaded aerodynamically.
In recent years there have been two incidents I know of where airplanes on first flight encountered stall flutter of landing-gear doors. In one case, the flutter was violent enough to fatigue off the fasteners holding the door to its hinges, and the door departed from the airplane. Fortunately, the failure of the door did not cause any collateral damage or render the airplane unflyable, and it landed safely. In the second instance, the door was not damaged, but the vibration caused by the doors motion was pronounced enough that the flight crew wisely elected to keep airspeed low, cut the flight short and return to base immediately. This reaction was exactly correct and should be taken as a lesson for all of us contemplating flight test of new homebuilt or kit airplanes. If an unexpected vibration or buffet begins, treat it as a serious safety of flight issue, keep it slow, and get on the ground as soon as safely possible.
Another airplane component that sometimes exhibits stall flutter is a streamlined bracing wire like that used to brace the wings and tails of aerobatic biplanes. Because the wire is solid, its elastic axis is at 50% of its chord. It is streamlined, so its aerodynamic center is at 25% chord. Accordingly, the necessary condition for potential stall flutter (aerodynamic center ahead of elastic axis) exists. If the wire is relatively short, the combination of its natural stiffness and the tension on the wire make it stiff enough so that it does not oscillate. If the wire is longer, as is the case for wing-bracing wires on single-bay biplanes, the center of the wire may be able to twist enough to initiate stall flutter. The cure for this is to attach the multiple wires together with a tube or dowel called a bayonet. The bayonet constrains the center of the wires so they do not twist, preventing stall flutter.
Avoiding Stall Flutter
Unlike classical flutter, mass balancing of surfaces does not help prevent stall flutter and may actually exacerbate it by increasing the torsional inertia of the surface. There are only three variables that affect stall flutter: the relative position of the elastic axis and the aerodynamic center, the torsional stiffness of the surface and the area of the surface. The key to preventing stall flutter is to keep the surface from twisting under aerodynamic load. The way to do this is to keep the elastic axis near the aerodynamic center, and particularly in cases where this is not possible, to ensure that the surface has sufficient torsional stiffness to resist twisting under aerodynamic load.
Barnaby Wainfan is a principal aerodynamics engineer for Northrop Grummans Advanced Design organization. A private pilot with single engine and glider ratings, Barnaby has been involved in the design of unconventional airplanes including canards, joined wings, flying wings and some too strange to fall into any known category.