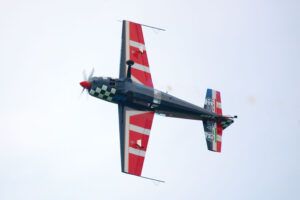
Last month we looked at roll control schemes for airplanes where high lift or other requirements do not leave enough room on the wing’s trailing edge for conventional ailerons. Airplanes like that are a special case, and most airplanes use ailerons as their primary roll control. Accordingly, let’s take a closer look at options for the design of the ailerons themselves.
Ailerons are flap-like surfaces mounted on the wing trailing edge. They are deflected differentially to roll the airplane. Typically, one aileron deflects down and the other up in response to a roll input to the stick.
The up-going aileron decreases the camber of the wing on that side and reduces its lift, while the down-going aileron increases the camber of the other wing and increases its lift. This difference in lift between the two wings generates the rolling moment the pilot uses to control the airplane.
Size Matters
The first aileron design decision is how big to make them. As we have discussed in the past, the ailerons are typically sized to meet a time-to-bank or a roll-rate command requirement. The more rapid the roll response needed, the larger and more effective the ailerons need to be.
The requirements vary widely depending on the mission of the airplane. For example, a cruising airplane meeting the minimum requirements of FAR Part 23 is required to do a bank-to-bank reversal from 30° one way to 30° the other in 4 seconds at landing conditions. This 60° roll only requires an average roll rate of 15° per second.
At the other end of the spectrum, some unlimited aerobatic airplanes are capable of rolling up to 400° per second, which is over 25 times as fast as the roll rate of the minimally compliant Part 23 airplane. Clearly, the aileron size and design for the two types will be significantly different.
There are a wide variety of types of ailerons. Their design is a balance between roll control power, control forces, mechanical complexity and aerodynamic drag.
Hinge Moment
One of the primary concerns in the design of the ailerons is the amount of force or moment required to deflect them. The larger the aileron and faster the airplane flies, the more force is needed to move the aileron.
This became a major concern in the era before the advent of power controls and hydraulically actuated flight control systems as the size and performance of airplanes increased over time. By WW-II, airplanes still had mechanical control systems actuated only by the pilot’s muscles, but fighters were exceeding 400 mph and bombers (the B-17 and B-29, for example) had grown to be quite large.
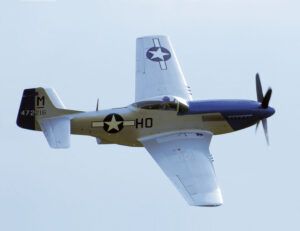
Fighters needed the ability to roll quickly in combat at high speed, so it was vital to keep the aileron hinge moments down to a level where the pilot’s strength could still command a large aileron deflection. Bomber pilots needed to be able to control their much larger airplanes and fly formation, again on muscle power alone.
Once the size of the ailerons and the speed of the airplane are set, the geometry of the ailerons and their hinges control hinge moment.
The chord of the aileron is a primary factor. For a given area, an aileron can have a range of span and chord. The longer the span, the shorter the chord. For a simple “plain-flap” surface of constant area, the hinge moment required to deflect it is a linear function of the chord. The longer the chord, the higher the moment. Accordingly, a short-span, long-chord aileron will require more force to actuate than a long-span short-chord aileron.
Once the aileron span and chord are finalized, the next parameter the designer has to work with to adjust hinge moments is the position of the hinge line on the chord of the aileron itself. Simple plain ailerons have their hinges at their leading edges, right at the junction between the back of the aileron cove and the front of the aileron.
There are several aileron design concepts where the hinges are set back from the aileron leading edge so the aileron pivots about an axis that is aft of its leading edge. Moving the hinge axis aft places it closer to the centroid of the aerodynamic pressure that develops on the aileron when it deflects. This reduction in the moment arm between the aerodynamic force on the aileron and the hinge axis reduces the hinge moment and hence the force required to deflect the aileron.
Offsetting the hinge also exposes the nose of the aileron to the airflow when it is deflected. The designer can use this to shape the nose of the aileron to further adjust hinge moment.
There are several specific types of offset-hinge ailerons and their nose shaping is quite different. We will look at these in more detail next month.
Aerodynamic Drag and Gap Flow
In addition to providing adequate roll control power and keeping hinge moments under control, the designer must address the aerodynamic effects of the aileron installation when the ailerons are in the neutral position in cruise.
The two primary sources of aerodynamic effect on the wing from undeflected ailerons are the flow around and through the gaps at the hinge and ends of the aileron, and the effect of exposed hinges and linkages on drag.
Flow through gaps can increase drag, decrease aileron effectiveness and reduce the lift of the wing. Ideally, the ailerons should disappear aerodynamically when they are not deflected. For minimum aerodynamic effect in cruise, the ailerons should have very small, well-sealed gaps and no exposed hinges, control arms or linkages. It’s possible to get very close, and some fast cross-country airplanes have aileron systems that approach the ideal in this respect.
The trade-off a designer faces is that almost all of the design concepts that help reduce aileron hinge moments lead to either open gaps, exposed aileron hinges or actuation components, or both. The proper design choice hinges on the relative importance of roll control performance and roll rate versus drag in level flight.
Cost, Weight and Complexity
The aileron design concepts that help reduce hinge moments are, in general, heavier and more complex than simpler designs. The hinges and hinge supports needed to implement an offset hinge are heavier and add additional load to the wing structure. They are also likely to be more complex and more expensive or time-intensive to make compared to simple hinges. The structure of the aileron itself will also be more complicated and might require more precision to manufacture. As with every decision in design, the right choice depends on the trade between extra cost, weight and complexity, and the need for the improvement in performance or flying qualities that the more complex design provides.
This is not always a straightforward choice, and designers and manufacturers sometimes change their minds mid-project, or even after the airplane is in production. At least one common certified light airplane was first introduced with a complex, aerodynamically-balanced aileron system and then, after several years of production, modified to incorporate much simpler (and presumably lower-cost) ailerons.
Next month we will look at several common aileron designs in more detail.