Until the advent of fully powered control systems shortly after WW-II, airplanes had manual flight control systems. The control surfaces were linked to the cockpit controls by mechanical linkages, and all of the force to deflect the controls was provided by the pilot’s muscles acting on the stick and rudder pedals. As airplanes got larger, so did the control surfaces.
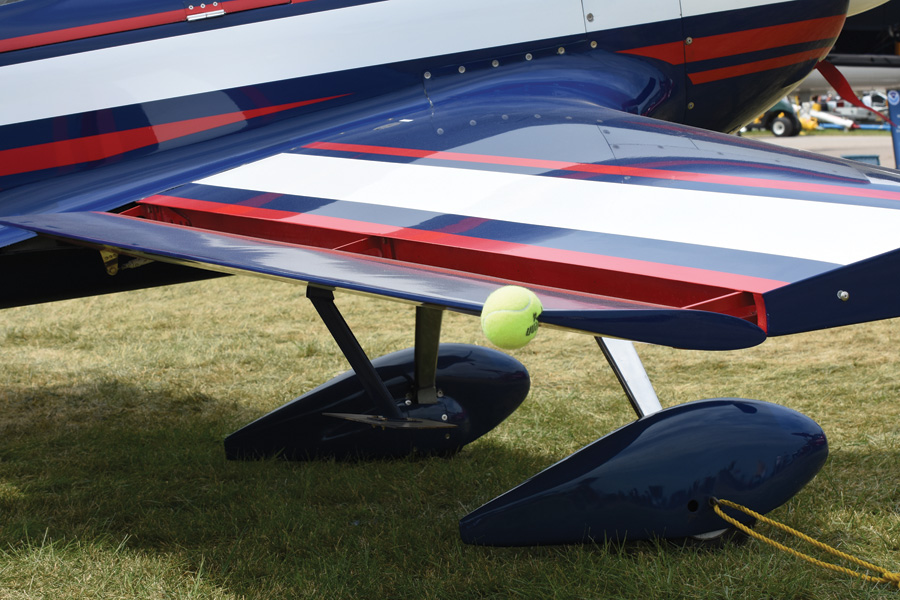
The aileron of this Giles 200 shows the set-back hinge axis and an intermediate nose shape. Note how far the aileron hinges are cantilevered aft of the wingspar.
The combination of larger control surfaces and greater aerodynamic loads resulting from higher flight speeds presented designers with a problem: The moments required to deflect the controls got so large that a single pilot was not strong enough to move a simple flap-type control enough to fly the airplane. In order to solve this problem, it was necessary to learn how to shape and hinge control surfaces so that the hinge moments needed to deflect them remained within the capacity of an average human pilot.
In today’s world, large and high-speed airplanes use fully powered control systems, so the problem is solved with brute hydraulic or electrical force. General aviation airplanes, however, still use mechanical controls, and some of the aerodynamic balancing concepts originally developed for WW-II military airplanes can be quite useful to tailor the flying qualities of the airplanes private pilots build and fly.
The simplest form of aerodynamic balance is the offset hinge line. Instead of being placed at the leading edge of the moveable surface, the hinge axis is moved aft. When the control surface is deflected, the force acting on the portion of the control surface ahead of the hinge line will produce a moment that is opposite to that produced by the force acting behind the hinge line. By adjusting the position of the hinge line, the designer can control the restoring tendency of the surface. The position of the hinge line will also affect the floating tendency. As the hinge line moves aft, both the floating tendency and the restoring tendency decrease. In addition, the moments that oppose the control deflection when it is moved become smaller, and the surface has less tendency to rotate parallel to the airstream as angle of attack changes. In most cases, both of these effects are desirable, provided they are not so extreme that control surface instability results.
Offset hinges disappeared almost entirely from the scene with the advent of powered controls on large airplanes. In recent years, they have reappeared on the ailerons of aerobatic airplanes.
Disadvantages
Offset hinge line balancing does have some disadvantages that must be addressed. The first is that the hinge system becomes more complex. The hinges must be cantilevered back from the fixed portion of the flying surface, and the hinges themselves and the structure they are anchored to must be strong enough to withstand the moment caused by this aft cantilever.
The second disadvantage is that, in order to work properly, the control surface nose must be able to move up and down relative to the fixed surface the control is attached to. This necessitates some gap at the control surface leading edge and means that gap sealing is not possible. There will be some aerodynamic penalty for this.
One characteristic of the offset hinge line type of balance is that it can introduce significant nonlinearity into the control-surface hinge moments. The hinge moments on a plain flap control surface change smoothly as the surface deflection changes. If the hinge line is offset, the moments may change suddenly at some deflection, or the rate of increase of moment with increasing deflection may change over the control surface’s range of deflection.
This nonlinearity is not always undesirable. On an aerobatic airplane, it can be used to tailor the aileron forces so that the initial stick force for the first few degrees of deflection is heavy enough to allow precise control and for the airplane not to feel “twitchy,” while at the same time keeping the force required to make a large aileron movement for rapid rolls light enough to allow the pilot to maneuver aggressively.
If done wrong, however, the nonlinearity in stick force can become a problem if it causes the pilot to feel control forces which do not vary smoothly with changes in control position and flight condition of the airplane. Such nonlinearity can make the airplane difficult to control or unpleasant to fly. Sudden changes in stick force or stick force reversal that cause the control to try to deflect itself are never good.
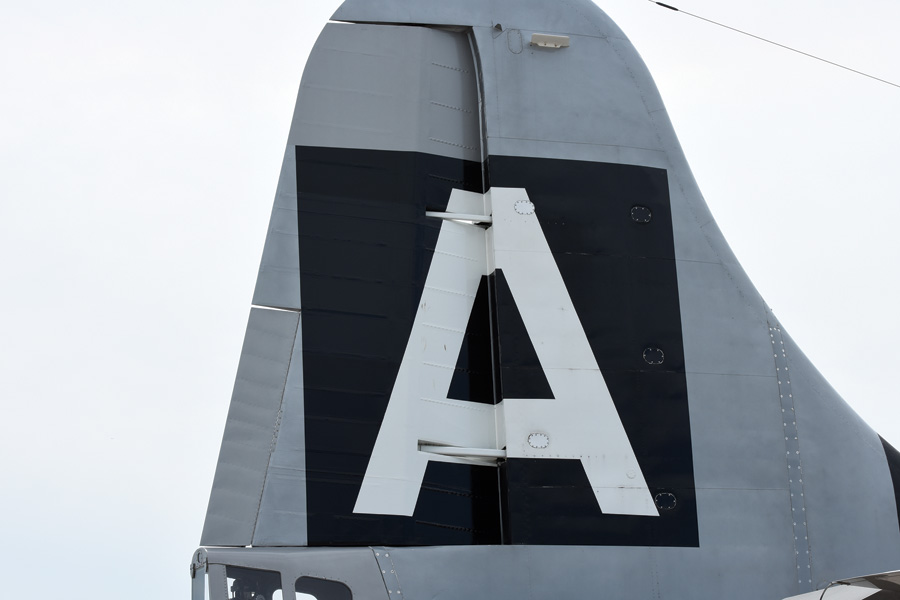
The B-29 rudder has a sharp nose shape and an offset hinge. The large amount of offset was needed so this very large surface could be moved by the legs of a single pilot, with no power assist. The included angle of the rudder leading edge is chosen so the sharp leading edge of the rudder does not unport at maximum rudder deflection.
The nonlinearity arises from the fact that the nose of the control surface is shielded by the fixed surface ahead of it when the angle of deflection is small. As the deflection increases, the nose of the control surface moves out into the free stream and new aerodynamic forces start to be generated by the increased airspeed over the nose.
If the control surface nose is rounded, the air flowing over the curve of the nose will produce a low pressure area, and this lift will produce a moment which tends to increase the control surface deflection. This moment is opposed by the moment produced by the lift on the portion of the surface aft of the hinge line. The lift on the aft portion of the surface changes relatively linearly with changing deflection, but the lift on the nose of the surface can change suddenly both when the nose first protrudes into the airflow and at higher deflections when the nose of the surface stalls.
Over the years, designers have developed a number of control surface nose shapes that are used on balanced controls.
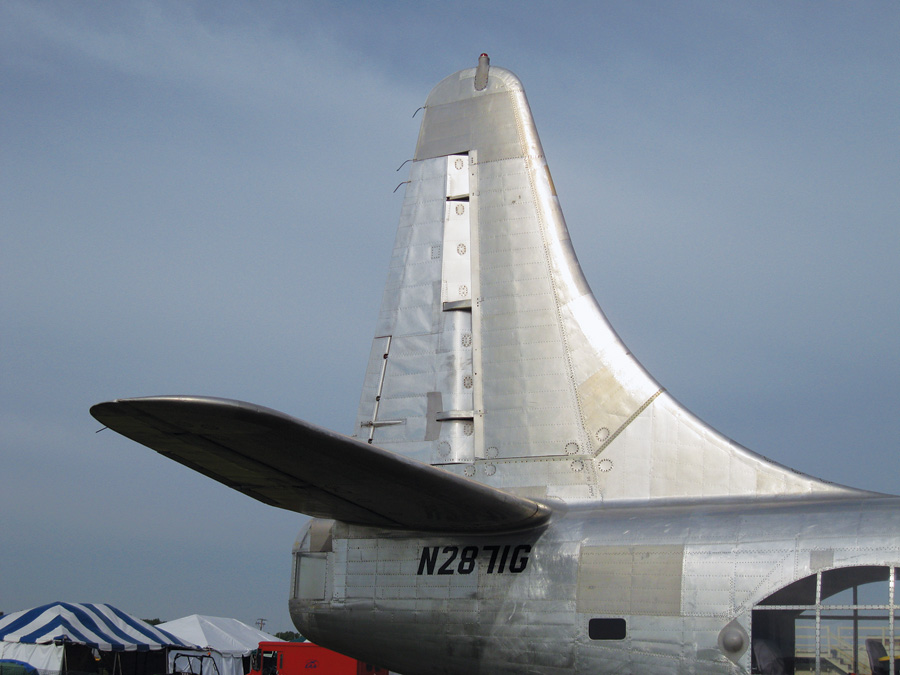
The rudder of the Consolidated PB4Y-2 Privateer (Naval patrol version of the B-24 Liberator) has a mix of nose shapes. The lower half has a more rounded shape, while the upper portion is sharp edged. The combination of the two allowed the rudder hinge moment to be tailored by varying the span of the sharp and rounded segments of the leading edge.
Blunt Nose Balance
Blunt nose balance gives the largest reduction of restoring tendency and hence the largest reduction in stick force. Unfortunately it also produces the most nonlinear variation of hinge moment with control deflection.
As the nose of the control surface moves out from behind the back of the fixed surface, the air begins to flow over the highly curved leading edge of the surface. This produces a low-pressure area on the nose of the control surface, which develops as the deflection increases. This lift on the control surface leading edge helps reduce the surface’s hinge moment, but it varies greatly as the deflection changes. In the region of small deflections, the nose of the surface is shielded behind the fixed portion of the wing or elevator and there is very little nose lift. When the nose of the surface unports or comes out from behind the fixed surface, the nose lift will begin to develop. This will be felt by the pilot as a reduction in the stick force required to deflect the surface. A fully blunt nosed surface unports at very low deflections, so the nonlinearity is felt almost immediately as the surface deflects.
At some larger deflection the nose of the control surface will stall. This will cause an abrupt change in both the hinge moment and effectiveness of the control surface. Stall of offset-hinge control surfaces is dangerous, and can lead to loss of control of the airplane. The deflection of the surface should be limited to prevent this stall from happening, even with the controls against the stops.
Sharp Nose Balance
The second type of balance nose shape is the sharp nose balance. A good example of this type of balance is the rudder of the WW-II B-29 bomber. The sharp nose balance provides less balancing effect than the blunt nose balance, but has the advantage that its variation of hinge moment with deflection is quite linear over the range of deflections available before the nose unports. This range of deflections is determined by the wedge angle of the balance nose.
The disadvantage of the sharp nose balance is that the control surface will stall abruptly when the nose of the surface does emerge from behind the back of the fixed surface. A surface employing a sharp nose balance should be limited in deflection so that the nose will never unport and cause the surface to stall.
Intermediate Nose Balance
The third type of nose shape is a compromise between the blunt nose and the fully sharpened nose. As one might expect, its characteristics are somewhere between the characteristics of the two other shapes. The compromise nose provides more hinge moment relief than the sharp nose, but less than the full blunt nose. It has more linear hinge moment characteristics than the full blunt nose and is less prone to sudden stalling than the sharp nose surface. As a result, this compromise nose shape is a good choice for control surfaces using offset hinge line balance.
All of these nose shapes have been successfully used on flying airplanes to alleviate hinge moment and floating tendency. Which is the best choice depends on three factors:
- How much hinge moment alleviation is required.
- How much hinge moment nonlinearity with deflection can be tolerated, and
- How much control power is required.
The fully blunt shape provides more hinge moment relief than the other two shapes, but has the most nonlinear hinge moment characteristics.
The sharp nose provides the most linear variation of hinge moment, but reduces hinge moments less than the blunt shaped nose. The sharp nose also has the lowest total control power for a given control surface area due to its sharp stall when the nose unports.
The intermediate nose shape offers a compromise between these two sets of characteristics.
Barnaby Wainfan is a principal aerodynamics engineer for Northrop Grumman’s Advanced Design organization. A private pilot with single engine and glider ratings, Barnaby has been involved in the design of unconventional airplanes including canards, joined wings, flying wings and some too strange to fall into any known category.