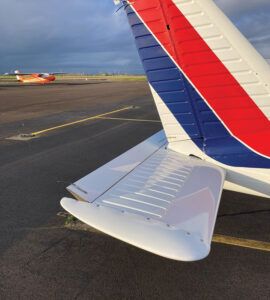
A conventional horizontal tail has a fixed horizontal stabilizer with an elevator hinged to it to provide pitch control. The “fixed” portion of the tail may have adjustable incidence for trim, but the pilot’s primary pitch control is via deflecting the elevator.
On an all-moving tail the whole tail pivots about a spanwise axis. Rotation of the tail about this axis changes the incidence of the tail to provide both trim and pitch control. All-moving tails are common on high-speed aircraft and light fighters; they provide more consistent control at high Mach numbers because of the way shock waves form on the tail when it is deflected. On a conventional tail, shocks forming at the elevator hinge line can severely degrade the control power of the elevators when flying near the speed of sound.
All-moving tails are less common on general aviation airplanes, but they are used on some types, notably the Piper line of single-engine airplanes and the Thorp T-18. Although general aviation airplanes fly too slowly for the high Mach characteristics of an all-moving tail to be relevant, there are still advantages to the concept that sometimes prove valuable for slower airplanes.
The biggest advantage of an all-moving tail is control power. Since the pilot’s stick input rotates the whole tail instead of just an elevator, it can generate more pitching moment for a given tail area than a conventional tail with elevators.
For airplanes where the tail is sized by control power rather than stability, this allows the all-moving tail to be smaller than a conventional tail.
Typically, this shows up on airplanes with large CG travel and airplanes that have high-lift systems that produce large nose-down pitching moments. For such airplanes the tail size is frequently determined by the pitch control power needed to trim the airplane at forward CG with the flaps down or to lift the nosewheel to rotate for takeoff.
When the tail is sized by a control power requirement like this, rather than a stability requirement, the extra control power of an all-moving tail can allow the tail to be smaller than it would need to be with a conventional elevator configuration.
Let’s take a look at the design considerations for an all-moving tail.
Stick Stability
It’s essential that the pivot axis on an all-moving tail be placed such that when the tail deflects, the moments produced about the hinge line tend to oppose the deflection and drive the tail back to its neutral position. Accordingly, the pivot axis must be ahead of the aerodynamic center (AC) of the tail.
If the axis is behind the tail AC, the tail will be divergent. It will produce moments that tend to increase deflection and will go hard over if the stick is released. This is very dangerous and should be strictly avoided.

(Photo: Paul Dye)
Airplane Stability Stick-Free
On an airplane with manual controls, the pitch-control surfaces (elevators or all-moving) float in the oncoming airstream unless the pilot holds the stick in a fixed position. This is called the “stick free” condition. Because the pitch-control surface is floating, it can move when the angle of attack changes to align with the airflow. The aerodynamic load on the surface remains essentially constant so it makes little or no contribution to the stability of the airplane.
On a conventional tail, the fixed portion of the tail continues to stabilize the airplane stick-free, even though some stabilization is lost due to floating of the elevators.
The loss of stabilization stick-free can be a major issue for an all-moving tail. With the pivot ahead of the tail AC, and no other mechanism to adjust hinge moment or float, the whole tail will float with the wind stick-free, effectively eliminating the stabilizing influence of the tail.
All-Moving Tail Design to Improve Stick-Free Stability
The key to regaining the stabilizing influence of the tail stick-free is to reduce or eliminate tail float. A simple way to get some improvement is to use centering springs to hold the tail in a specific position so the airplane is never truly stick-free. This has been tried occasionally with limited success. It is difficult to get acceptable flying qualities this way. By the time the springs are strong enough to have a large favorable effect on stability, they are also strong enough to make the pilot’s stick force to move the tail against the spring force objectionably high.
The aerodynamic and mechanical solution has two parts: The first is to place the pivot axis for the tail at, or very slightly ahead of, the AC of the tail. This minimizes the aerodynamic hinge moment driving the tail float. Unfortunately, it also makes the stick forces too light, so the airplane will be unacceptably sensitive in pitch.
To solve this, we add an anti-servo tab to the trailing edge of the tail. This is a tab, usually covering most of the span of the trailing edge), that is geared to “lead” the deflection of the tail itself relative to the fuselage. For example, if the tail is deflected trailing-edge-up by the pilot, the tab will deflect trailing-edge-up relative to the tail.
The tab produces a hinge moment that opposes the deflection of the tail. This fights float and is also used to tailor pitch stick forces by tuning the ratio of tab deflection to tail deflection. The anti-servo-tab linkage can also be designed to make the neutral position of the tab adjustable by the pilot, so the tab also acts as a classical trim tab. This is the system used by most general aviation airplanes with all-moving tails.
Tail Structure and Stiffness
One significant design concern for an all-moving tail is the structure that carries loads through the fuselage. This might be either a cylindrical spindle/tail spar or a tail structural spar box. In either case, it must be relatively short fore and aft to allow the tail to pivot. This structure must carry all of the loads on the tail, both in bending and torsion. It’s especially important that it be stiff enough in torsion to prevent the tail from fluttering.
The structural challenges of the carry-through mean that an all-moving tail will usually be heavier than a conventional tail of the same size.
Root Gap Aero
Because the all-moving tail must be free to pivot to control the airplane, there will be some gaps between the roots of the tail panels and the sides of the fuselage. Air leaking through these gaps will cause drag and reduce the effectiveness of the tail at stabilizing and controlling the airplane. It’s important to keep these gaps as small as possible and seal them as much as practical without impeding the free motion of the tail.
All-moving tails can be a good design choice in the special case where the need for high pitch control power outweighs the issues of more complex design, heavier structure and tricky root-gap aerodynamics. In most cases, a conventional tail will be simpler and lighter, but occasionally the all-moving tail wins out in the design trade-off.
And an aircraft with a full flying tail or variable incidence horizontal can go supersonic as proved by Chuck Yeager and Jack Ridley in the X1.
Although that is a very small advantage for a Cherokee.
Very good description of how/why it works.
Thanks
If you consider the Piper’s stabilator to be an “all-moving tail”, then the Mooney’s pivoting tail section is even more so.
The Piper’s elevator is not “considered” all-moving, it IS all moving. Any stick input for pitch moves the entire thing.
A Mooney uses a traditional elevator and rudder. Every part of the Mooney’s tail does not move with every input on the stick.
May I point out that the Cessna 177 line also has the stabilator . It is quite powerful, thus causing some problems for newby pilots in the landing flare. This problem was partially mitigated with the stab mods providing smoother ir over the stab at higher angles of attack. .
Thanks for the lesson. I was wondering about this just last Monday while driving to work. Does anyone know the safety record of moving tails vs traditional on GA airplanes? Is it really worth the additional design complexity on slower planes?