Opening a properly shaped slot between the lower and upper surface of the wing near the leading edge can greatly increase the angle of attack at stall.
The portion of the wing forward of the slot acts like a vane that starts turning the air ahead of the main portion of the wing. This assistance from the forward portion of the slot allows the air to turn more of a corner and therefore allows the wing to fly at a higher angle of attack without stalling.
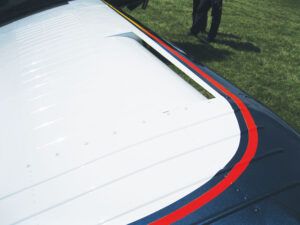
Airflow enters the slot from the lower surface at high pressure and is injected tangential to the upper surface by the slot. This sheet of air coming through the slot pulls the airflow around the corner at the leading edge and adds energy to the boundary layer on the upper surface, delaying flow separation.
This slot effect can be implemented one of two ways. Leading edge slots are “fixed,” and the slot is actually cut through the basic airfoil.
If the slots are properly placed and contoured, then at cruise angle of attack there is very little pressure differential across the slot and therefore very little flow through the slot. If so, the drag penalty can be quite small. A few airplanes have also been built with doors to close the slots in cruise.
Fixed slots are occasionally used over the full span of the wing, but they are more commonly used to protect the outer panels of a wing to improve stall characteristics. Several airplanes have fixed slots on the outer portions of their wings, covering the area ahead of the ailerons. The slots help tame the stall by keeping the outer panels flying and the ailerons effective as the stall begins. Fixed slots often appear on wings that have a combination of taper twist and airfoil that would normally cause the wing to stall first from the wingtip, causing unstable roll damping and a tendency to spin out of a stall. One example of such an airplane is the Globe Swift.
Another application for fixed leading-edge slots is on an all-moving tail. An example of this is the Cessna Cardinal. The stabilator of the Cardinal did not have enough maximum lift in the downward direction to trim the pitching moment caused by the very large flaps when the airplane was at its most forward center of gravity. The lower surface of the tail would stall causing an un-commanded pitch down. Cessna test pilots discovered this in flight test. The stall of the tail caused a loss of control that took a lot of altitude to recover from. The airplane could not go into service with this characteristic, so Cessna had to find a fix. Rather than increase the size of the tail to solve the problem Cessna engineers incorporated a leading-edge slot into the existing sized tail to increase its maximum lift (or in this case downforce) enough to trim the airplane in all configurations and at all center of gravity locations.
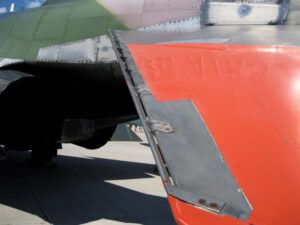
Some versions of the F-4 Phantom also had fixed slots on both the wings and tail.
The fixed slot has the advantage of being a fixed-geometry feature with no moving parts. Properly designed it can have a very low, but not zero, drag penalty in cruise if it is incorporated into the base airflow correctly.
The fixed slot has the same issue as vortex generators in that it will trip the boundary layer, and no laminar flow can be expected on wings with fixed leading-edge slots.
Slats
A slat is a portion of the leading edge that moves down and forward when it is deployed, opening a slot behind it and increasing the camber of the leading edge. When it is extended, it acts as a vane that combines the aerodynamic effects of a leading-edge droop and a slot.
The combination of increased camber and the effect of the slot on the flow over the upper surface of the wing make the leading-edge slot a very powerful device that delays the stall more than either a droop or a slot acting alone.
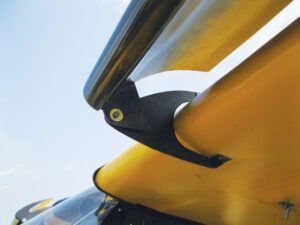
Slats are usually used in applications where the high-lift capability of the wing is most important. Accordingly, they appear at opposite ends of the speed scale. In the general aviation world, slats are commonly used on STOL airplanes such as the Helio Courier or Valdez STOL competitors that need to fly extremely slowly to take off and land in minimum distance.
Slats are also used on jet airliners and transports. These fast jets need to have a high wing loading to get the high-speed cruise efficiency they need to fly their missions. In order to slow down enough to take off and land safely on reasonably sized runways, jet transports need to generate a lot of lift per square foot of wing. Leading-edge slats are a critical component of the high-lift system that allows jet wings to reach a high enough CLmax to take off and land safely.
Slats are powerful aerodynamic devices but are also mechanically complex. They need to be mounted on tracks or multi-bar hinge mechanisms to deploy properly. The slat itself is a long slender structure. When it is extended, the air loads on it are large. The structure of the slat must be strong and stiff enough to carry these loads without distorting or failing.
When it is retracted, the slat becomes the leading edge of the cruise wing. The slat must hold its shape under cruise and maneuvering air loads and not gap open and allow air to leak through the wing. A properly designed slat that retracts cleanly and fits tightly when closed has a very small drag penalty and does not change the shape of the base airfoil. It’s important to have good seals that the slat can bed down on to keep air from flowing through the small gap between the retracted slat and the rest of the wing.
Actuation
The slats on airliners and other high-speed or heavy airplanes are typically extended and retracted by hydraulic or electric actuators. These extend the slats and hold them out, and also retract them and hold them closed in cruise. One notable aerodynamic characteristic of slats is that, above a certain angle of attack, the net aerodynamic force on the slat itself tends to pull it forward relative to the rest of the wing because of the lowered air pressure around the leading edge and the relatively higher pressure in the slot behind the slat vane. If the slat is actuated, the actuators must be sized to both push and pull so that the slats are properly extended when deployed and held tightly closed against suck-open forces when retracted.
The forces on the slat can be used to deploy them automatically. If the tracks or linkages are designed properly, the aerodynamic forces on the slat will hold it closed at low angles of attack in cruise and pull the slats open when the angle of attack rises above a specific level. Done right, this allows the slats to open and close automatically without actuators and without any actions from the pilot. Aerodynamically actuated automatic slats were first invented at Handley Page in Great Britain around 1919 and are commonly used on general aviation STOL airplanes to this day.
Barnaby, I enjoyed your article on slots and slats. It is informative and easy to read.
Barnaby,
Great article. Can you approximate or suggest how to determine the improvement that a fixed slot the full length of the wing might provide? I built a Zenith CH750 with fixed slots the full length of the wing span and am curious what per cent improvement of wing loading the fixed slot configuration might be? Thanks in advance for any suggestions you might have.