Maintaining attached flow is a primary concern for the designer of any airplane. To minimize drag and maximize lift, maintaining fully attached flow is desirable. The exterior shape of the airplane is created to promote flow attachment, but sometimes separation occurs anyway.
Stall is caused by flow separation. Eventually, if the angle of attack is high enough, the flow over the top of the wing will separate, and the wing will lose lift. In addition to proper shaping of the wing and fuselage, there are several add-on devices that can be used to delay or eliminate flow separation.
Enter the Vortex Generator
The most popular of the options are vortex generators, which are small devices used to help reattach separated flow. Installed in groups, they can help eliminate separation and solve a variety of aerodynamic problems. There are several types of VGs, but the most common is the vane type. These are small, low-aspect-ratio blades that are mounted perpendicular to the skin of the airplane. Each vortex generator is mounted so that it has an angle of attack relative to the oncoming flow, which causes it to act like a wing. It develops lift normal to the oncoming flow and sheds a vortex off of its free tip. The tip vortex of a VG stays close to the surface of the airplane as it moves aft.
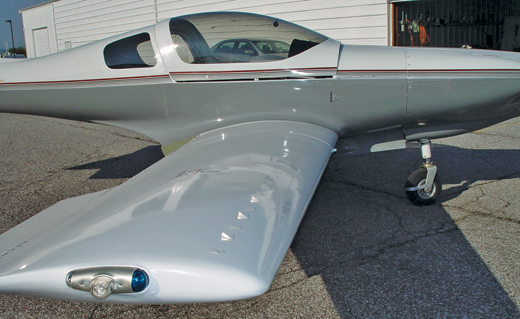
The vortex shed by the VG tends to move air that is near the airplane skin up, away from the skin, while at the same time moving air from the outer flow down, closer to the skin. This mixing of air gives the VG its beneficial effect on flow separation.
When separation is imminent, the air in the boundary layer, right near the skin, is out of energy. It is moving slowly and will soon stop and reverse direction, causing separation. The air in the outer flow, however, is moving fast and has high kinetic energy. The vortex created by the VG moves some of this fast-moving, high-energy air down into the tired boundary layer and moves some of the tired air away from the surface. The net effect is to increase the speed of the air in the boundary layer and delay or prevent separation of the flow.
To work properly, the VG must be able to affect the air outside the boundary layer, and to do this it must be placed slightly upstream of the point where the flow would separate without the VG. If separation is allowed to occur upstream of the VG, it will be submerged in the separated flow and will be unable to reach clean outer-flow air to mix into the boundary layer.
VGs for the Kit World
For many years, VGs were primarily found on large transports and military aircraft. But over the last 10 years, vortex generators have moved into the general aviation world, and retrofittable VG kits have been developed to improve the characteristics of light airplanes. These kits first appeared to tame the low-speed behavior of some production twins, including the Beech Baron and some of the more popular Cessna twins. More recently, VG kits intended to reduce the stall speed and improve STOL performance of single-engine airplanes have appeared.
The vortex generator kits generally address two areas:
1) Clmax improvement: Stall is caused by separation of the airflow over a wing. Reducing separation and delaying the stall to a higher angle of attack will increase the maximum lift coefficient (Clmax) and reduce stall speed. Properly placed VGs on the upper surface of the wing can achieve this.
Two configurations have met with success. The first uses a full-span row of VGs to increase the maximum lift of the entire wing, reducing stall speed. The VGs delay the stall of the whole wing, thus increasing Clmax and reducing stall speed. Full-span VGs increase the maximum lift of the wing, but they do not have a large effect on where on the span the stall first appears when the wing finally does stall. Accordingly, full-span VGs will reduce stall speed but may not have any beneficial effect on lateral stability at the stall.
If the primary goal of a VG installation is to improve lateral stability and aileron control at stall, rather than to reduce overall stall speed, then the proper approach is to install the VGs on only the outer portion of the wing. This will delay the stall of the tips, giving the airplane a gentle, root-first stall.
2) Control-power improvement: Another place where VGs can provide a useful fix is where we need to increase the control power of an airplane, particularly rudder power on multi-engine airplanes. If, for example, an airplane is retrofitted with more powerful engines than those for which it was originally designed, the extra power may be more than the rudder can trim to keep the airplane straight in the event of engine failure. This causes minimum control speed (Vmc) to rise. To bring Vmc back down, more rudder power is needed. Retrofitting the airplane with a larger rudder is often impractical or prohibitively expensive, so there is a large motivation to improve the control power of the existing rudder.
The effectiveness of a control surface is limited by how far the surface can be deflected before the flow separates at the hinge line. Deflecting the surface farther than this will cause a large drag increase, but it will not increase the amount of lift the surface is generating.
As we have already discussed, placing VGs upstream of the separation point can re-energize the boundary layer and delay separation. Adding a row of VGs just upstream of the rudder hinge line increases the amount the rudder can be deflected before the flow separates. The lift of the rudder at higher deflections is also increased. Vortex generators ahead of the rudder hinge are a feature of several of the VG kits currently marketed to tame production light twins. They also can be found on the Beech Starship, Boeing 727 and on many other production airplanes.
VG Drag
The aerodynamic fix provided by VGs does not come entirely free: The VGs are in the airstream all the time, and they do produce some drag. How much depends on the configuration of the airplane and the size and placement of the VGs. If VGs are added to a very clean wing, particularly one that would have laminar flow without the VGs, the drag penalty can be significant. On many airplanes, the improvement in the quality of the airflow downstream of the VGs is sufficient to offset, or nearly offset, the drag of the devices themselves.
VG Geometry
There are two common ways of installing vane-type VGs. All VGs should be mounted so that they have an angle of attack relative to the local airflow of between 15° and 20°, but they may be mounted so that all of the VGs are parallel to each other, or in pairs with equal-and-opposite angles of attack.
The first approach, with all of the VGs parallel, is called a “corotating” installation because all of the generators shed vortices that are rotating in the same sense. The paired equal-and-opposite-angle installation is called a counterrotating installation because each pair of generators sheds a pair of vortices that rotate in opposite directions.
Both types of installation are used. The Voyager and most other canard airplanes that need VGs use a row of counterrotating pairs of generators. The vortex generators on the fin of the Boeing 727 and on the canard of the Starship are corotating.
For many years, counterrotating VG installations were more widely used and better understood than corotating installations. Corotating VG installations are somewhat lower drag than counterrotating configurations, and they have become more common in recent years. The appropriate configuration depends on the details of the geometry and airflow over the surface they are being used on.
VG Size
To effectively mix outer-flow air into the boundary layer, VGs must stick out above the edge of the boundary layer, but only a little, to minimize drag. A recommended height for a first try is about 1.2 times the local boundary-layer thickness. Boundary-layer thickness is difficult to determine accurately, but it is usually on the order of 1% to 2% of the distance from the leading edge.
VG Shape and Placement
Typical VGs are either triangular or trapezoidal, with swept leading edges and vertical trailing edges. To work at all, VGs must be installed upstream of the point of flow separation. Before installing VGs, determine where the separation you want to eliminate starts. The VG row should be a short distance upstream of this point.
For corotating VGs, the root chord of the VG should be on the order of four times the VG height, and the distance between VGs in a row should be five to six VG heights.
For counterrotating VGs, the root chord of the VG should be about 2.5 times the generator height. The distance between the centers of the two generators in a counterrotating pair should be about the same as the root chord of one VG. The counterrotating pairs should be spaced about 10 VG heights apart.
Making a vortex generator installation work requires some experimentation with VG size, number and spacing. If an initial VG installation provides the desired effect, try reducing the size and/or number of generators to reduce drag. If more effectiveness is needed, increase the size or number of VGs.