Last month, as we began our look at biplanes, we saw that the biplane configuration came into being and remained predominant for what were, at the time, sound technical reasons. When the biplane faded from preeminence, it was also for good reason.
Biplane Disadvantages
Why then did the biplane fall out of favor, to be replaced in large part by the cantilevered monoplane? The major disadvantage of biplanes is high parasite drag. This arises from several sources. The first is the combination of bracing wires, and interplane and cabane struts, which support the wings. These external-to-the-wing structural bracing elements give the biplane the lightness and rigidity that made biplanes desirable early on. These features are also the aerodynamic Achilles heel of the biplane configuration because of their drag at high speed.
Two other related factors add somewhat to the parasite drag of typical biplanes. First, biplanes tend to have somewhat lower maximum lift coefficients than monoplanes because they are rigged so that one wing (usually the upper wing on a positive-stagger configuration) stalls before the other. This makes the stall characteristics safe, but costs maximum lift. The second is that most biplanes do not have effective flaps or other high-lift devices. Accordingly, biplanes tend to have low wing loadings when compared to monoplanes. If we look at the biplane fighter wing loadings shown in Table 1, we see numbers that we now consider typical of light airplanes rather than fighters.
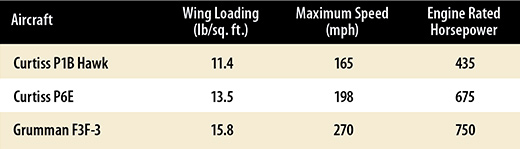
Table 1: Characteristics of Biplane Fighters
Low wing loading implies large wing area and accordingly large wetted area. Since the wetted area of the fuselage and tail does not change with wing configuration, the typical biplane will have more parasite drag than a monoplane partially because of its lower wing loading and higher wetted area.
Biplane Design Evolution
Designers were aware of the drag of the bracing relatively early. As airplanes evolved, the design of biplanes was improved to reduce bracing drag. At first, many airplanes were multiple-bay biplanes. They had more than one set of interplane struts, and each bay between sets of interplanes was braced by sets of diagonal wires. These wires had a cylindrical cross-section at first. The combination of multiple struts and lots of cylindrical wire was extremely draggy. For very early airplanes, where everything including the pilot and the engine were out in the breeze, this was acceptable, primarily because these airplanes were so slow.
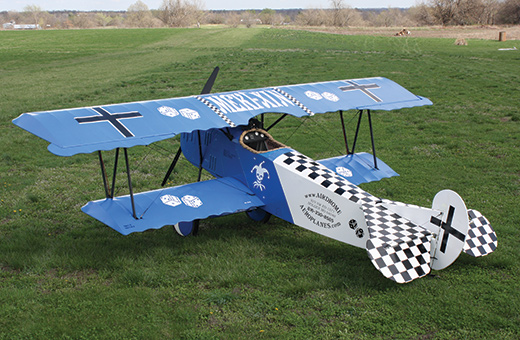
The Fokker D-VII (replica shown here) had cantilevered wings and respectable performance. The N struts were the result of official insistence that the airplane have them.
As time progressed, the rest of the airplane became cleaner. Fuselages were covered, engines were cowled, and eventually fairings were added to landing gear. As the parasite drag of the rest of the airplane dropped, the drag of the bracing of the biplane wing cellule became a larger and larger portion of the airplane’s total drag.
Designers responded by modifying the design of the bracing to reduce drag. Streamlined bracing wire replaced cylindrical cross-section wire. This reduced the drag of the bracing wire by as much as 75%. Struts were given faired cross sections, and the number of struts was reduced. Later biplanes were almost all single-bay, with only one set of interplane struts on each side, and one set of bracing wires in each bay. On a few airplanes, the cabane struts were eliminated by attaching both wings directly to the fuselage. This was also a design feature of the later cabin biplanes such as the Waco series and the Beech Staggerwing. This approach to reducing biplane drag is a mixed blessing because eliminating the cabanes leads to configurations with smaller-than-desirable gaps between the wings, or deeper-than-optimum fuselages.
Another feature that appeared to reduce the drag of the wing bracing was the combining of the three elements of the early “N” interplane strut into a single, cleaner “I” strut, which flared out at its ends to pick up both spars on each wing. This was more common on civilian airplanes and racers than on fighters.
After all of the biplane drag-reduction features just described had been developed, the designers had gone about as far as they could go to reduce the drag of the wing bracing. At the same time, engines were getting more powerful, and airplanes were getting cleaner aerodynamically overall. Airplanes were flying faster, and the bracing became an ever-larger percentage of the total drag.
To illustrate how this evolution could affect the designers’ thinking, I have done some calculations on three American biplane fighters: the Curtiss P1B Hawk, the Curtiss P6E (the final evolution of the Hawk) and the Grumman F3F-3, which was the last biplane fighter to see service in the United States.
The results are shown in Table 2. (Antique airplane buffs, please note: These are relatively rough calculations, based on data from Jane’s American Fighting Aircraft of the 20th Century. Even if they are off slightly, they are accurate enough to illustrate the important points about biplane drag.)
These results can give us some insight into how airplane design evolved, and why designers finally decided to switch to monoplanes.
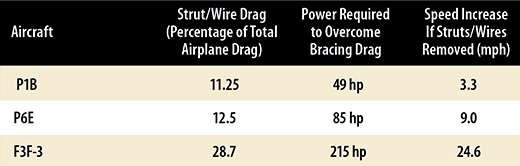
Table 2: Effects of Wing-Bracing Drag
First, let’s consider a designer looking at the P1B Hawk airplane. Since the rest of the airplane was aerodynamically dirty, the drag of the wing bracing was not a dominant factor in the overall drag. When the radical aerodynamicist shouted down the structures man and suggested that the airplane should be a monoplane, the chief engineer asked, “If we make this airplane a monoplane, and don’t change the landing speed, how much faster would it go?” When the answer was 3.5 mph, there was little incentive to try a new, high-risk design. Increasing power 10% would get the same result, and there were other, less radical aerodynamic refinements that would reduce the drag of the airplane the same amount without affecting the structural design of the wings. The decision was made to stick with the biplane and concentrate on detail cleanup and increased engine output. Given the starting point, and the knowledge available at the time, it was a sound engineering decision.
The airplane that resulted from this type of thinking was the P6E Hawk. The fixed landing gear was faired, and the overall shape of the fuselage improved. Engine power increased. Top speed went up from 165 mph to 198 mph, a much larger performance increase than would have been achieved by simply making a monoplane out of the P1B. At this point, the aerodynamicist probably spoke up again and said, “Now those struts and wires are costing us more, and we could be going 9 mph faster with a monoplane.” He still lost the debate because 9 mph was still not a big enough performance boost to be worth the effort and technical risk of an all-new structural and aerodynamic configuration. After all, they had just increased the top speed of the Hawk by 33 mph without doing anything radical.
Over time the trend continued. The rest of the airplane was cleaned up further. The cockpit was enclosed with a clean canopy, and the landing gear became retractable. Cooling systems improved. Eventually, the airplane had evolved to the point where the drag of the struts and wires was a large percentage of the parasite drag of the airplane, because the excess parasite drag of the other components of the airplane had been substantially reduced. The airplane was flying faster, significantly increasing the power required to overcome any additional parasite drag. As we can see from Table 2, the F3F-3 was using over 200 hp just to push the wing bracing through the air. The rest of the airplane was by then about as clean as it could easily be made. When the inevitable request for improved performance came, the monoplane-advocating aerodynamicist finally had a winning case. Switching to a monoplane finally offered a performance increase large enough to be worthwhile, (almost 25 mph), and most of the other options for aerodynamic improvement had been exhausted. The only way to significantly reduce the overall drag of the airplane was to get rid of the struts and wires bracing the biplane wings.
Grumman actually started the design of the F4F Wildcat as a biplane, and then changed over to a monoplane configuration when the engineers realized that the time had come when the drag of biplane wing bracing had become unacceptable.
Technology for the Monoplane
While designers were improving biplanes, the overall state of aeronautical technology was also improving. Several technologies helped sway the balance between biplane and monoplane.
Thick Airfoils
One of the primary reasons for the use of biplanes early on was that early airfoils were all very thin—so thin, in fact, that all wings, biplane or monoplane, needed external bracing to handle flight loads. By the time WW-I ended, designers such as Fokker and Junkers had produced thick-wing airplanes with cantilevered wings that had quite good performance. The Fokker D-VII biplane actually had cantilevered wings. The N struts were added at official insistence, and there were no bracing wires. The Fokker D-VII monoplane had a fully cantilevered wing.
By 1933, NACA Report No. 460, describing the NACA four-digit series of airfoils, some of which are still in use today, had been published. The advent of airfoils that were reasonably thick was important for the rise of the monoplane. Thicker airfoils allowed monoplanes to have cantilevered wings, and to get rid of the drag of the struts and wires bracing the biplanes’ wings.
High-Lift Devices
The maximum lift coefficient advantage of an un-flapped monoplane over a biplane is not large enough to make a large difference in wetted area. As we have already seen, as airplanes got faster, reducing parasite drag became more and more important. One way to do this is to make the wing smaller, reducing the wetted area and parasite drag.
In order to increase wing loading while keeping the stall and landing speeds down, it is necessary to increase maximum lift coefficient. By the early 1930s, several types of high-lift devices, including flaps and leading-edge slats, had been developed that almost doubled the maximum lift available from a wing. Designers could use flaps to allow wing loading to rise while maintaining an acceptable stall speed. The Grumman F4F Wildcat had a wing loading of 28.5 pounds per square foot as compared with the 15.8 of the biplane F3F-3. The ability to pack a lot of wing area into a relatively compact configuration to keep wing loading and stall speed down was a major advantage of biplanes. The advent of high-lift devices made higher wing loadings possible, and higher speeds made higher wing loadings desirable. Thus, a feature that was an advantage for biplanes initially became a disadvantage as performance and technology improved.
Better Engines and Variable-Pitch Props
One advantage of biplanes was that the combination of low wing loading and low induced drag allowed them to have acceptable climb performance with low-powered, heavy engines. As engines improved, the power-to-weight ratio of airplanes also improved. Variable-pitch propellers allowed the engine to deliver its full power efficiently at both climb and cruise airspeeds. Because of the large reserve of power available, climb performance became less critical. Thus, improvements in propulsion reduced the importance of the second major biplane advantage.
Improved Knowledge of Structures
In the early years of aviation, the air loads on wings were poorly understood, and aeroelastic phenomena such as flutter and wing divergence were entirely unknown. The inherent rigidity and strength of the box-girder biplane structure helped ensure that airplanes were strong enough and stiff enough to fly safely. Also, the truss structure was well understood and relatively easy to analyze, while a cantilevered, multi-spar structure was still somewhat of a mystery.
Many early monoplanes ran into some form of structural trouble. The Fokker D-VIII had a series of wing failures caused by the wings twisting under load, and transferring lift outboard until the wing broke. Flutter problems were common on early cantilevered monoplanes. These problems naturally caused designers to look upon the cantilevered monoplane as a high-risk configuration. As structural knowledge advanced and people learned enough about the mechanism of flutter to design flutter-resistant wings, the technical risk associated with cantilevered wings was reduced to a manageable level.
We have seen that the biplane appeared for good technical reasons, and then faded away, again for good technical reasons as the state of technology and mission requirements changed. The biplane lives on in some specialized applications such as crop-dusting, aerobatic flying and for sport aircraft where top speed is of secondary importance.
Barnaby Wainfan is a principal aerodynamics engineer for Northrop Grumman’s Advanced Design organization. A private pilot with single engine and glider ratings, Barnaby has been involved in the design of unconventional airplanes including canards, joined wings, flying wings and some too strange to fall into any known category.