Much of the performance of an airplane is determined by major configuration features such as the shape of the fuselage, the span and airfoil of the wing, etc. Sometimes, however, relatively small details can have a large impact on drag and performance. Some areas of the airplane are very sensitive to detail, and small changes can have large effects. One such area is the wingroot, where the wing joins the fuselage.
Induced Drag and Span Loading
One of the two major components of an airplanes drag is induced drag or drag due to lift. This is the drag caused by the generation of lift by the wing. Induced drag is proportional to the lift squared, and inversely proportional to the effective wingspan squared. Its importance varies, depending on the phase of flight. In general, the slower the airplane is flying, the greater the importance of induced drag.
At high speed, particularly at low altitude, the majority of the airplanes drag is parasite drag, and induced drag is relatively unimportant. The opposite is true during climb. For a piston-engine airplane flying at the airspeed for best rate of climb, three-quarters of the total drag is induced drag. When the airplane is cruising at its best lift-to-drag ratio (L/D), half of the drag is induced drag. In reality, general aviation airplanes cruise at airspeeds faster than that for best L/D, so the induced drag in cruise is less than half of the total drag.
For minimum induced drag for a given wingspan, the ideal lift distribution is elliptical. In other words, if we plotted the local lift as a function of span, the plot would look like a half ellipse, with the lift being greatest at the root. Most real-world wings have span loadings that vary a bit from elliptical, but they are a reasonably good approximation.
Large deviations from an elliptical span loading will cause significant increases in induced drag. This is particularly true if the lift near the center of the wing is compromised. If the lift near the center is reduced enough, the wing starts to act aerodynamically like two shorter wings flying in formation. Induced drag is inversely proportional to span squared, so this effect can be large.
Configuration Effects
There are two common ways that wingroot configuration can increase the drag of the airplane significantly. The first is if the wingroot junction is poorly designed and causes the flow to separate near the root. A poorly designed junction can cause a large increase in drag, particularly in climb and economy cruise where the lift coefficient is high. In general, junctions on the upper surface of the wing are more critical than lower-surface junctions. The airflow over the upper surface of the wing is much more sensitive to interference, which might cause premature separation or stall.
Because the airflow over the upper surface of the wing is so sensitive, careful attention should be paid to the design of the wing-to-fuselage junction area, particularly on a low-wing airplane. Even in a situation where larger separation is not expected, some filleting is still a good idea. Air flowing in a corner between two surfaces is slowed down by skin friction with both surfaces, which causes the boundary layer to thicken and generate more drag. It may also produce early separation. Radiusing the corner with a fillet accomplishes two things. First, the wetted area in the area of the corner is reduced. Second, the air will not have to rub against both surfaces forming the corner, and will produce less skin friction drag. Fillets are particularly effective in areas where surfaces meet at angles significantly less than 90.
One common example of this situation is at the wingroot of a low-wing airplane with a rounded fuselage cross-section and/or dihedral in the wing. The addition of the fillet will clean up the flow in the corner area and reduce the drag of the airplane. Proper design of the fuselage can minimize the interference drag caused by the wingroot junction and reduce the size of the root fairing required. A high-wing configuration with some dihedral is an example of a low-interference-drag design. The upper surface of the wing is uninterrupted, and the lower surface joins the fuselage at a large angle, thus minimizing the undesirable corner effects on the airflow.
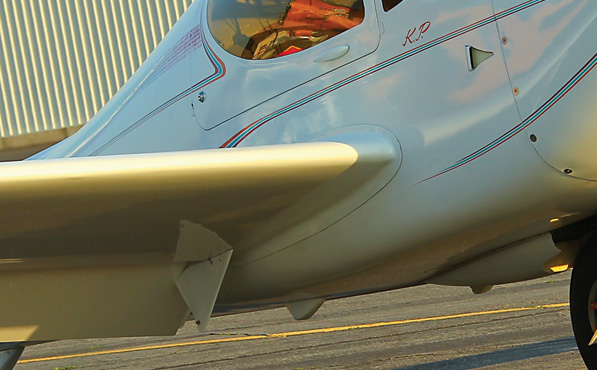
Wingroot Gaps
If the wingroot is not sealed where it meets the fuselage, the result can be dramatic. Air leaking through the gap makes the wingroot act like a second wingtip and drastically reduces the effective span of the wing. This effect was first noted in WW-I, when designers tried cutting away the root of the upper wing of biplane fighters to give the pilot better visibility up and forward. While the increased visibility was highly desirable in combat, the performance penalty proved to be prohibitive.
In the modern world, it is not uncommon for a builder or restorer to decide to make an early test flight without installing the seals or fairings at the wingroots. This usually leads to an unpleasant surprise when the airplane suffers from an extremely degraded ability to climb.
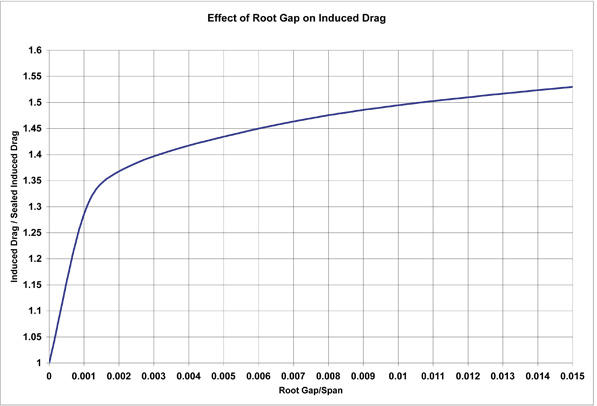
Figure 1 shows the theoretical effect of a single gap in the center of a rectangular wing. It illustrates the induced drag of the wing with the gap open divided by the induced drag of the wing without the gap as a function of the ratio of the root-gap span to the wingspan.
Note how quickly the drag rises with the gap size. A gap that is one tenth of a percent of the span increases the induced drag 28%. That is equivalent to a quarter-inch gap on a 25-foot span airplane. Remember that the plot is for a single gap, but a real-world airplane has two wingroots.
The effect of the two gaps is made worse by the fact that they are separated by the span of the fuselage, so they are cutting the wing into three segments rather than two. Accordingly, for a given wingroot gap, using twice the gap of a single junction when reading the plot in Figure 1 will give a slightly optimistic first-order idea of how much induced drag penalty the gap will produce.
For our 25-foot span airplane, having a quarter-inch gap at each root is roughly equivalent to a half-inch single gap, and we can expect a 35% increase in induced drag. At best rate of climb airspeed, the represents an increase of 26% in the total drag of the airplane. Because climb is a function of excess power rather than total drag, a given percentage increase in drag will reduce the rate of climb by a larger percentage than the percentage increase in drag.
For our example, the two quarter-inch wingroot gaps will likely reduce the best rate of climb by somewhere between 30% and 40%. It may be even worse than that, however, because the analysis just presented does not take into account the parasite drag penalty of the air flowing through the gap, or the flow separation it may cause.
The important thing to remember is that a relatively small air leak near the root of a wing can have a startlingly large detrimental effect on the climb performance of the airplane.