Last month, I talked about the various types of airparks available for those so inclined as well as the specific airpark, AZ82, that my wife and I have chosen for our second home. In this issue, I’ll dive a little deeper into airpark/hangar construction considerations and, specifically, hangar door selection.
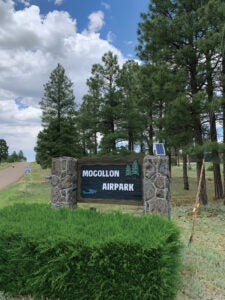
My first hangar experience was a simple municipal T-hangar. This particular hangar was constructed of steel I-beams and industrial corrugated sheeting. It had a heavy-duty two-piece sliding door that overlapped to one side. Other than two electrical outlets and an overhead light, these kinds of hangars have very few accoutrements or creature comforts. Depending upon the size of the mechanical occupant(s) and local restrictions, lessees often cram in a desk, worktable, small fridge and a tool cart. Others look like a “hoarder’s paradise.” Some municipalities are friendly to the construction of Experimental aircraft, others not so much. “Heavy” work like welding and painting are usually prohibited by the associated fire departments who commonly perform routine inspections.
I built the major components of my RV-10 at my home shop and then used a flatbed trailer to take them to the paint shop at my local airport, a few blocks away. I then did the final assembly at the airport hangar. I still rent that hangar and plan to continue to do so into the foreseeable future. I have been told that my $220 monthly lease payment would be considered a bargain in most parts of the country. Nevertheless, as I have since found, a municipal hangar has a hard time holding a candle to a custom purpose-built private airpark hangar, especially for builders of Experimental aircraft.
The Other Half
Most airpark communities require something more aesthetically pleasing than a municipal hangar, typically with construction that mirrors the residences themselves. Some homeowner associations—often heavy handedly—lay out specific requirements concerning size limits, setback, materials, colors, sidewalls and roofing. This can be both a blessing and a curse. Obviously, if you go to the effort and expense to build a hangar/home to luxury-home standards, you don’t want to see an erector-set hangar built next door. The vitally important thing for all prospective buyers is to thoroughly familiarize themselves with the local requirements before purchasing—and then again before designing, a third time before building and then a fourth time before being called in for a grilling by the architectural committee. (Own that T-shirt.)
Hangar design and construction may appear simple compared to a home, but there are unique aspects that must be handled properly, especially the physics involved with hangar doors. It is strongly suggested to use the services of a draftsman/architect who has experience with such things, even better if the experience includes properties on your airpark of choice.
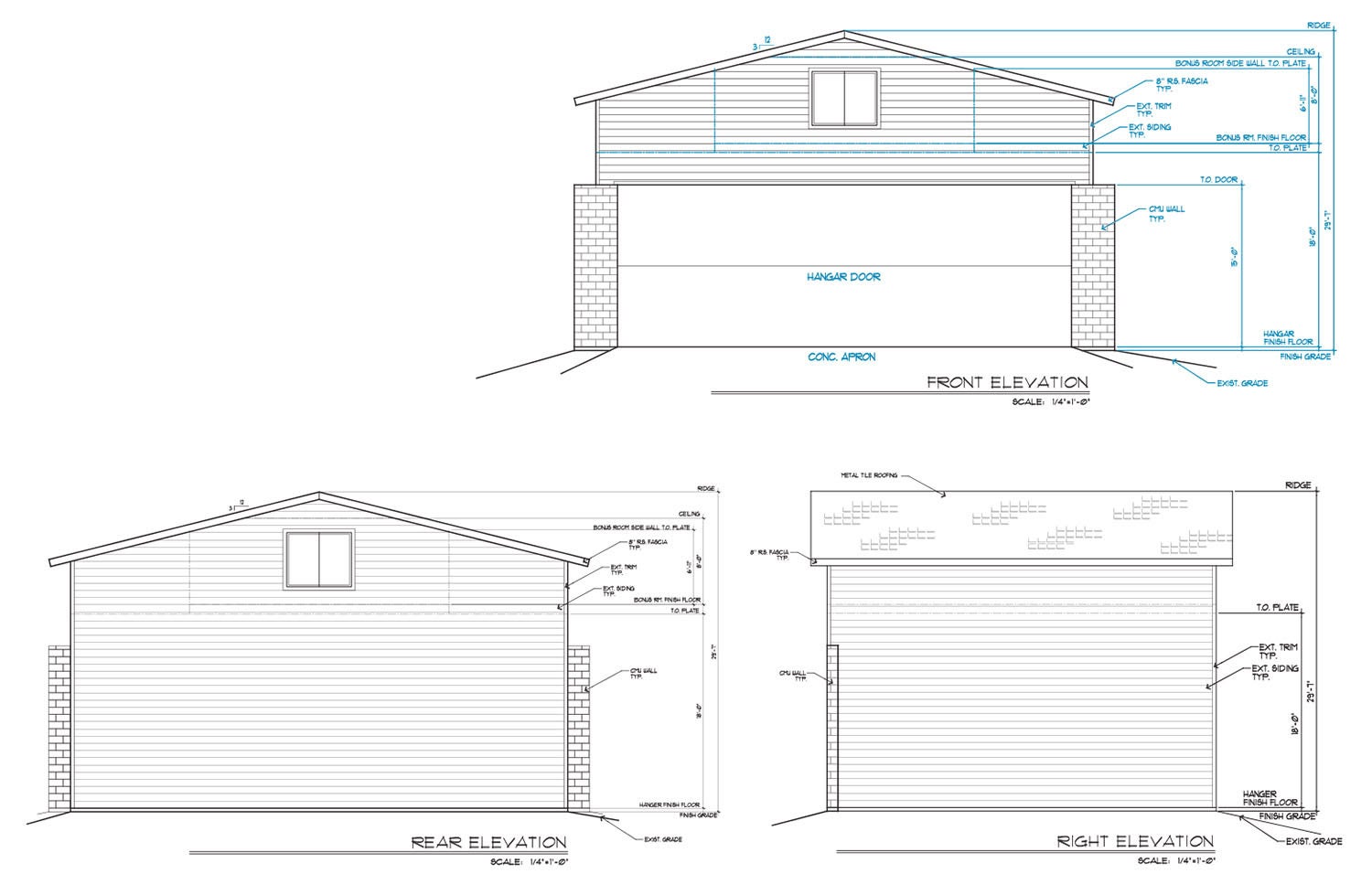
Now, the List
We were fortunate enough to find a person who had drawn dozens of such designs, including several in our community, and were very pleased with his counsel and results. Just like designing your dream airplane, there are several advantages to designing your own hangar. For folks who are considering building an aircraft in the hangar, or even just performing routine maintenance, there are several things that are key to making the experience more rewarding and pleasant. Here is a partial list that is far from complete.
- Bigger is better. Build as much square footage as allowed to fit on your property and within your budget. Who knows, some day you may want a motorglider.
- Plan for exceptional lighting throughout the space.
- Good power. You can never have too many outlets around. They are cheap to build in but can be expensive to add later. Adding 220-volt AC can be handy for welding or a large compressor. Do this while you’re building since adding this capability later is a pain.
- Water. Have hose spigots inside and outside of the hangar. Sinks, especially deep shop/laundry type tubs, are extremely handy and useful. Toilets are also useful depending upon how close the hangar is to the home, especially if you want the women in your life to hang out and participate in the hangar—or when you’re over 60.
- Heating and air conditioning. This can really vary by need and local climate. Some builders go full heat and air-conditioning, but, like a certain preacher’s doghouse, that can also be overkill. A hangar is still a hangar. Portable devices are often sufficient for all but the coldest of climates. An inexpensive parabolic heater from the aviation aisle at Walmart works great for me. Ventilation is a must. We put in a conventional garage door on the perpendicular wall to the hangar door and together they not only make for lots of open access, but nice flow-through ventilation as well.
- Storage. Worktables, shelves and cabinets can be designed in from the start or added easily after the hangar has been “lived in” for a period of time to get a feel for where things would work best and to allow time for the budget to recover. Sometimes that kind of stuff just evolves naturally over time.
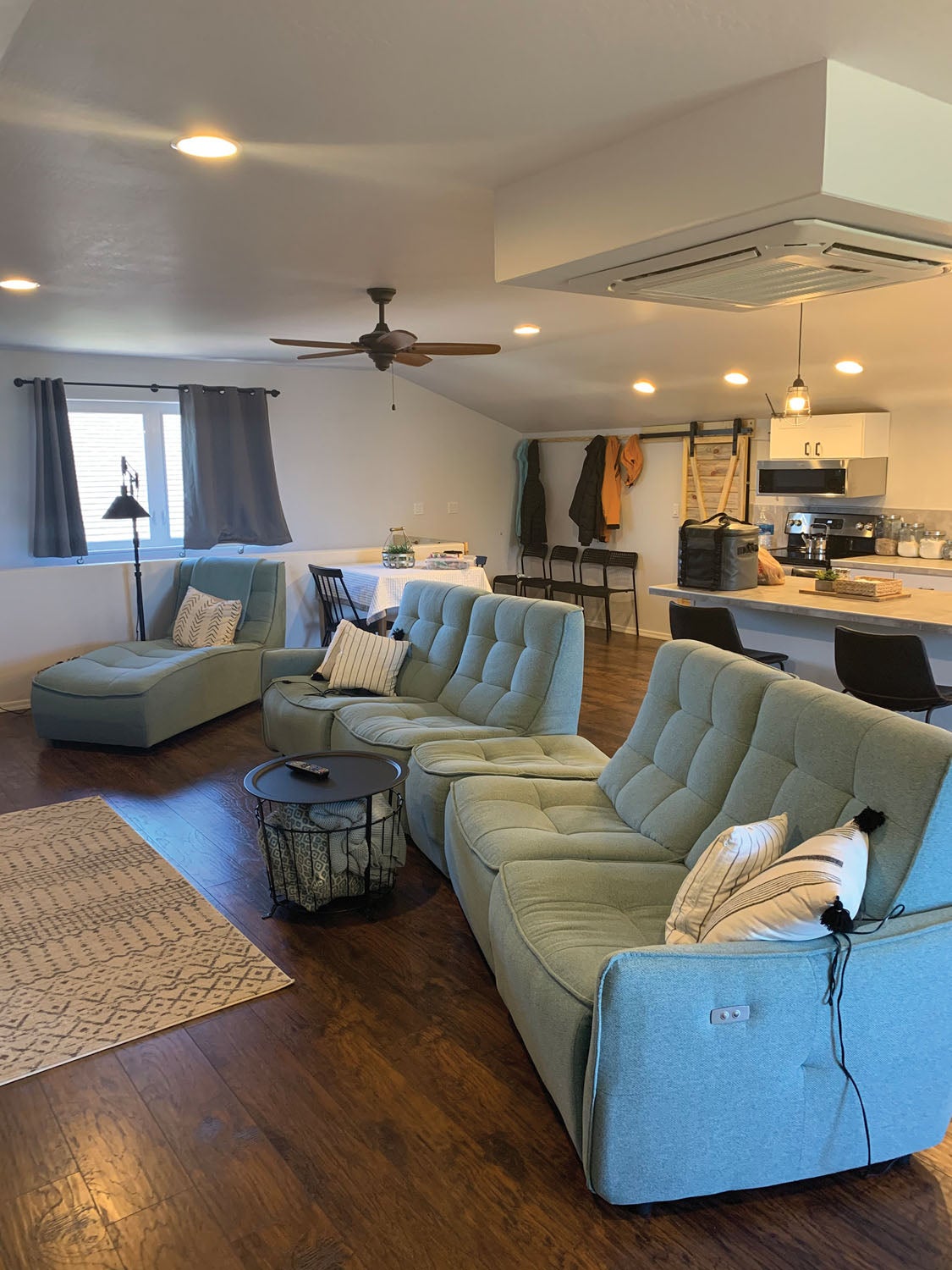
Snow Season Is the Reason
Our airpark lies at approximately 6600 feet elevation. That is deep into snow country, even in Arizona. One design aspect of a roofline pitched for snow is that the geometry creates a space above the hangar ceiling. Some folks just leave it as an attic, which is a waste, in my opinion. Some make a storage area with stairway access. One feature popular at our airpark and others is to make the space above the hangar into a small livable area, like a spare bedroom or studio apartment.
As I mentioned last issue, our hangar lot is separately situated a short walk from our residence lot. We decided to fully dress out the hangarminium or “H-mini,” as the family calls it, with a kitchenette, bathroom and living area. It is efficiently heated and cooled with a ductless split HVAC system. With four kids, all married, we make five couples, so our long-term plan is to build the main cabin with four bedrooms and use the H-mini for the fifth during all-hands family events and gatherings. We are still anxious to build the main cabin, but unfortunately, the covidity blues came out of the blue and set that timetable back a bit. (Actually, a couple of hundred thousand bits). Nevertheless, in the meantime, the whole family has thoroughly enjoyed the H-mini as a mountain getaway. My daughter, an author, isolated herself up there to finish her third novel. (Search “Haelo” on Amazon).
Shut the Front Door
One massive difference between a hangar and a home, or even a garage, is the need for a proper hangar door. Like E/A-B kits, hangar doors come in several options. Also like the kit market, a handful of companies dominate.
One of the first choices that must be made is what type of door best suits your airpark needs. Sliding-panel doors are well suited to clusters of hangars, like municipal airport hangars, where the doors can overlap the adjoining hangar(s). That type generally doesn’t work as efficiently at private airpark hangars that are overwhelmingly solitary. The three primary types of hangar doors for airpark hangars are bifold, single panel (usually hydraulic) or manual accordion style. Each has its advantages and disadvantages. (Doesn’t everything in aviation?) Our airpark has examples of all three.
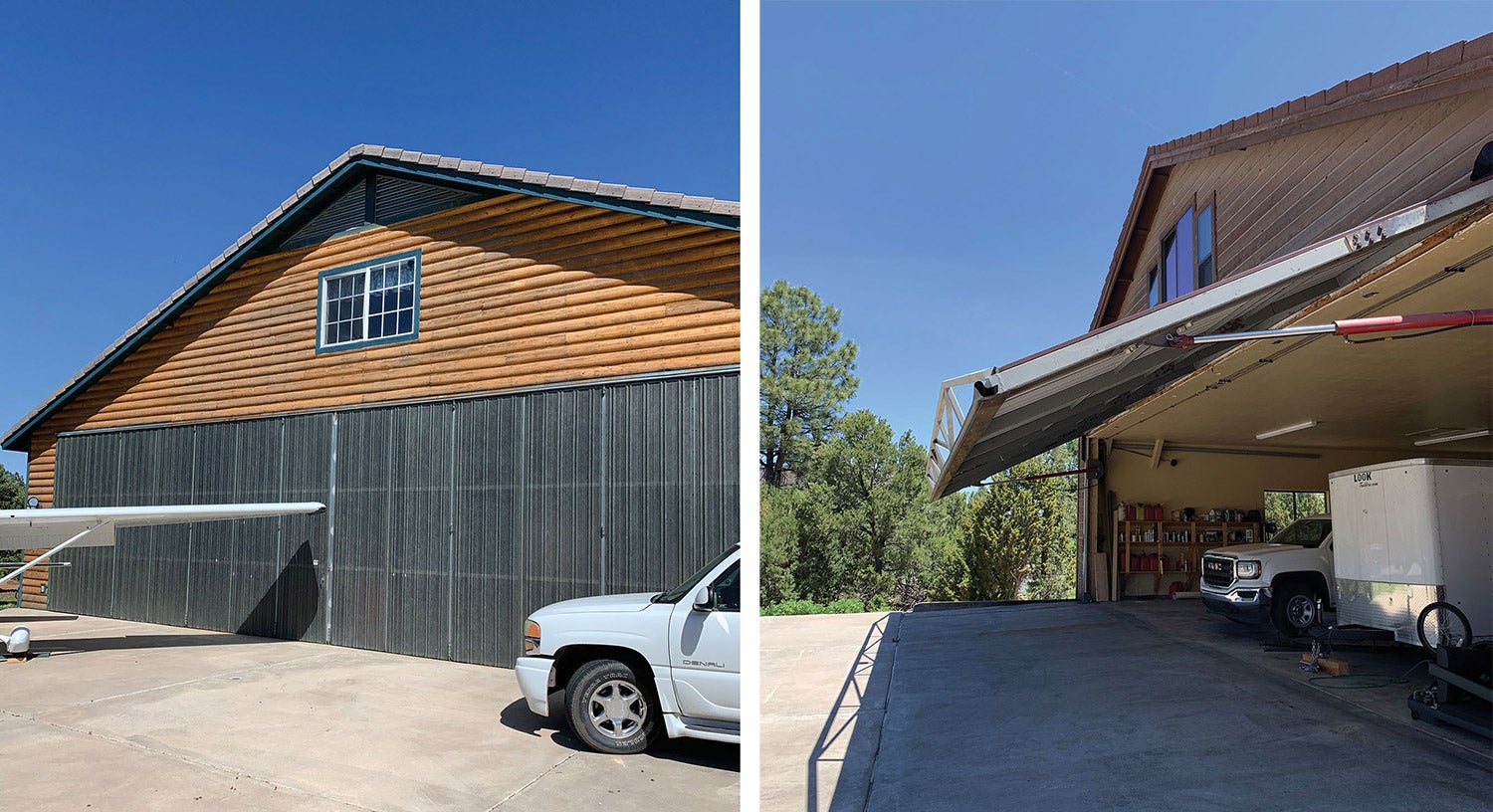
One consideration was that I wanted my wife to be comfortable operating the hangar door by herself. For us, that ruled out a manual door. That brought the decision down to either a bifold or a single-panel hydraulic door. One of the best places to conveniently research hangar doors is at major airshows like AirVenture. The major players are always there with displays and usually, show specials for the plucking.
As previously mentioned, our airpark is in snow country. I was concerned about heavy snow blocking the base of a single panel door, especially after watching a future neighbor have to dig his out before being able to open the door. The same geometry also applies to parking an aircraft or other vehicles close to the outside of the door. A bi-fold door pulls mostly up rather than swinging out, which is a clear advantage in those situations. I also found that the single-panel doors with their impressive hydraulic-arm systems were generally more expensive than bifold doors. One clear advantage of the single-panel design is that an open door makes for twice the shade/rain cover.
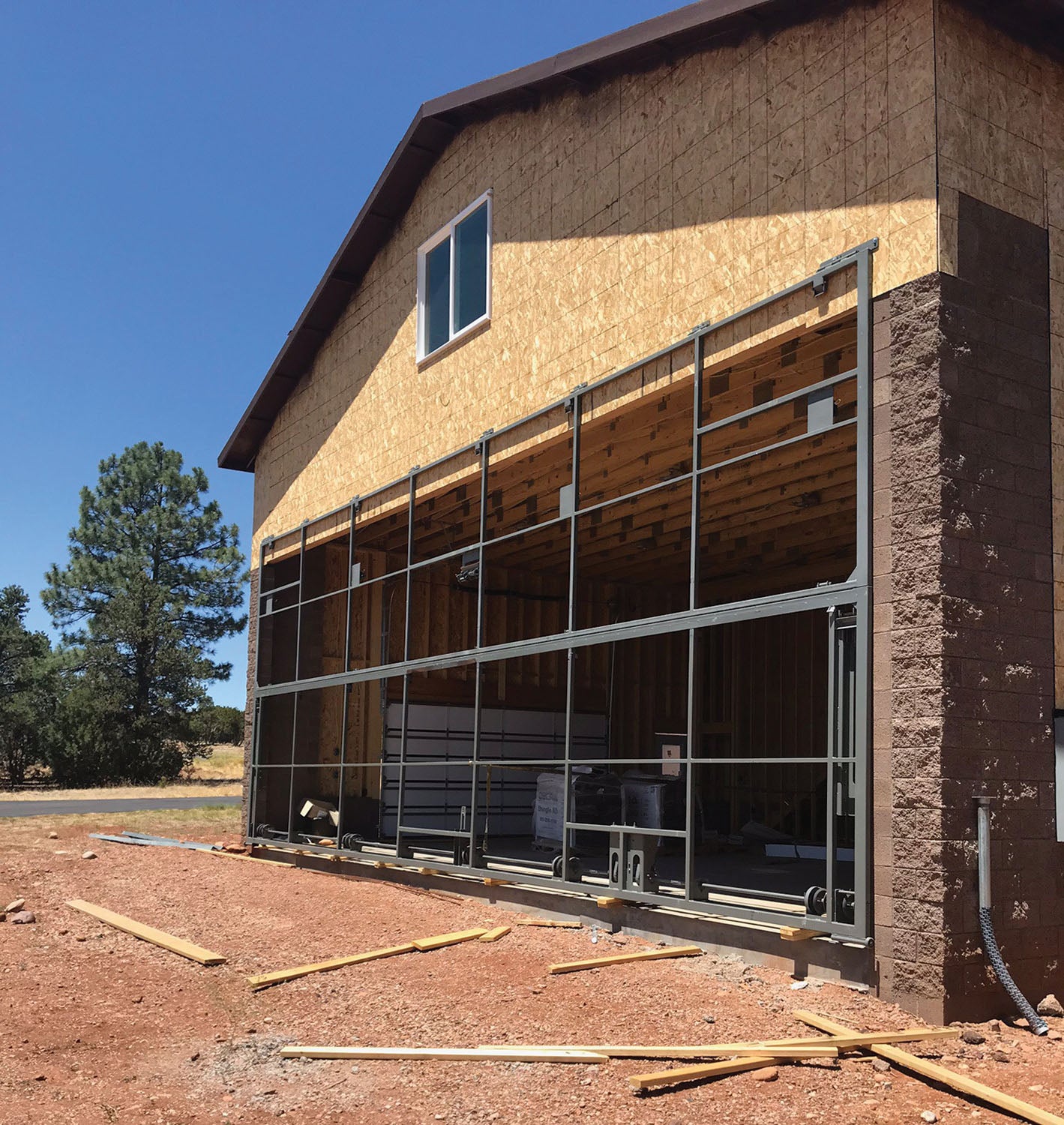
Having chosen the bifold door, the next choice was cable or strap actuation. I really liked a cable version made by a company in Canada called Diamond. I liked the easy access to the motor, the clever winding spools and the integrated insulation panels.
Our other option was the Schweiss bifold door, which touts its unique strap system over cables. I liked Schweiss’ strong industry leadership position, many of its design features and the fact that there were several Schweiss doors already in use at our community. Plus, my builder was familiar with them.
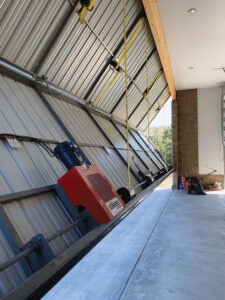
In the end, door for door, the Diamond was less expensive. However, where the rubber met the road (literally) was shipping. Shipping a hangar door from Canada to rural Arizona came up to the level of ghastly expensive—almost half the cost of the door itself. Shipping a door from Minnesota to Arizona can’t be cheap, either, but it just so happened that the OSH show special for Schweiss that year was a substantial shipping credit. That sealed the deal on the Schweiss.
Door quotes are based upon rough design dimensions. When you order, you send a copy of your hangar plans and they custom design the door to your exact dimensions. They also send an impressive copy of engineering calculations with the equally impressive documentation packet.
My first impression upon seeing the door delivered by flatbed truck was that I was actually quite unimpressed. It looked just like a couple of simple welded steel frames rather than an expensive door, which is exactly what it is. What they build and sell is the skeleton. What makes it function as a door is whatever covering you or your builder attach to the skeleton frame to close it up and seal it in. Insulation is optional. When you get the package all opened up is when you see and appreciate the high-quality materials and workmanship.
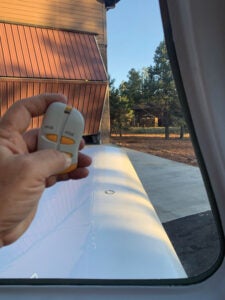
So, could the average schmo install the door on his own? You certainly could as I’m sure many have. The instructions are complete. However, the door is very big, awkward and heavy, and portends damage, disaster and even death if mishandled during installation. It takes several worker bees and a heavy-duty forklift to get it stood up into initial position and hold it there until the retainer bolts can get installed. In my opinion, it pays to use a pro, preferably one who is well insured. The manufacturers have recommendations for installers in just about any area.
Airpark living has always been a dream of mine, so going to the effort of carefully designing and artfully executing a custom hangar has been worth the time, effort and money. I feel fortunate and blessed to be able to fulfill that dream. Much like the infamous “RV grin” that comes from first flight of an aircraft you assembled yourself, that grin returns broadly the first time you taxi up to your airpark hangar and press “open” on the remote control in the cockpit.
The RV grin is NOT “infamous”. Consult your dictionary, or talk to your editor.
ML
The editor says a little tongue in cheek is allowed.
I am in the process of closing on a vacation getaway at an airport community. A back to basics with two turf runways. Multiple taxiways to taxi up to ones idea of paradise. There are a few … very few requirements for living space and hangar. Mostly wooded lots and when the sun goes down…a million stars come out.
Welcome to paradise. My idea of it anyway.
Doran Jaffas
KY91
Where is KY91? Airnav doesn’t know where you are.
Rick
Try Y91.
Lake City, Michigan
I am based at Y70, Ionia, Michigan
There will be a lot of commuting back and forth between the two. Y91 is less than 1 hour Tailwind W8 flight time from Mackinac Island. Bois Blanc Island over by Mackinac Island as well. Go the other direction and you have Beaver Island. From Beaver Island it’s a quick hop over the lake to the Upper Peninsula which is absolutely gorgeous.
I have been living in an airpark in Australia for 8 years and enjoy it very much. Most residents have nice homes and good size hangars on half an acre situated in a lovely part of the country, with great climate and easy driving to cities.
There are a few residents who don’t fly but live here to enjoy the spacious relaxed lifestyle. We all know one another and most of us, including wives, are good friends, often flying together or getting together for a coffee and social events.
Importantly, with a great range of aircraft and skills, there is always advice or help at hand if needed.
The convenience factor of living at an airpark and having your aircraft right beside the house simply cannot be overstated. I usually fly 3 or 4 times a week, whenever I feel like it. Sometimes early morning, sometimes just before sunset. Some flights are 15 minutes while others a few hours if I drop in on other local airstrips for a coffee and a chat. If not flying I will usually be in the hangar doing something on the aircraft, or some other tasks like fixing the mowers. It is a pleasant place to spend time.
On several occasions when taxiing out for a flight and seeing neighbours I have stopped so they could jump in and we have a lovely chat while flying around the neighbourhood. It is a great joy to share time and experiences with friends.
A well organised and run airpark with good people is a wonderful thing for a pilot. .